Electrical systems in barns
Learn how an electrical system can start a fire, applicable regulations, design and component considerations and barn electrical maintenance practices. This technical information is for Ontario producers.
ISSN 1198-712X, Published July 2021
Introduction
No one wants to experience a barn fire. In the past five years, there have been 42 human injuries and one human death related to barn fires reported by the Office of the Fire Marshal and Emergency Management (OFMEM).
When the origin of the fire is determined, approximately 40% of barn fires are caused by electrical system faults — the largest single cause of barn fires. Improvements in barn electrical system design, component choice and maintenance practices can help to drive down the number and cost of barn fires in Ontario.
This fact sheet provides information on:
- how an electrical system can start a fire
- which regulations apply to a barn's electrical system
- design and component considerations
- barn electrical maintenance practices
The operator is responsible for understanding these electrical safety requirements as well as other governing regulations on the farm.
Reducing the risk of barn electrical fires by following regular electrical inspections and maintenance by a licensed electrical contractor can result in reduced annual electrical system maintenance costs and insurance premiums.
Barn fire trends
Barn fires are devastating to the farmer due to the loss of livestock, crops, buildings, equipment and income. In 2019, the OFMEM reported 172 barn fires with estimated losses of over $47.3 million for buildings and equipment.
While the number of barn fires occurring per year has been decreasing in recent years (Figure 1), the average estimated dollar loss per barn fire has been increasing (Figure 2).
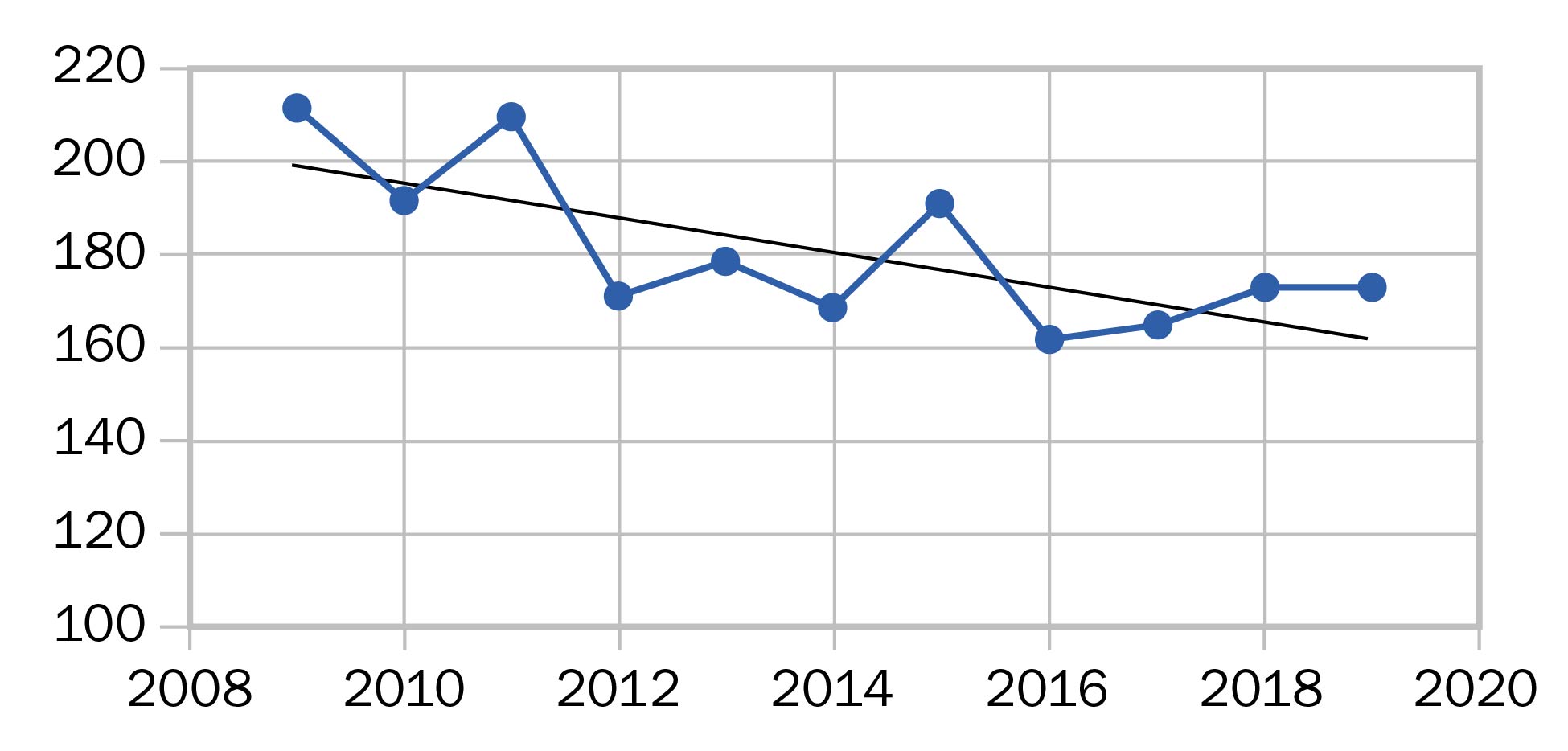
Source: Ontario Fire Marshal and Emergency Management Data, 2021
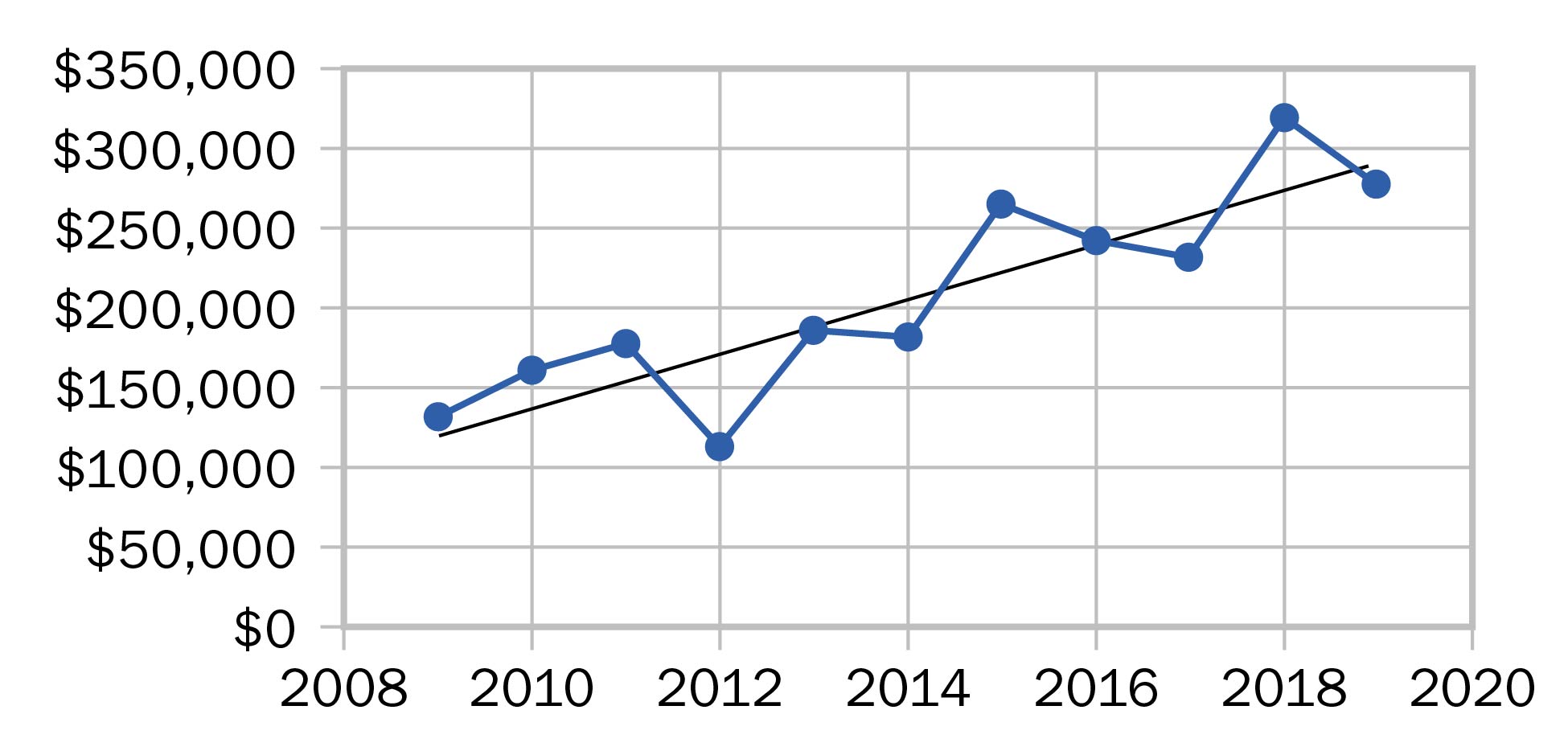
Source: Ontario Fire Marshal and Emergency Management Data, 2021
Considering the significant personal and financial costs that can result from a barn fire, paying attention to the electrical system in the barn is an important activity that should be conducted at every farm in Ontario.
Effect of barn environment on electrical systems
The barn environment is harsh on electrical system components, especially in livestock and poultry operations. Livestock barn environments contain high humidity levels and elevated concentrations of corrosive gases such as hydrogen sulfide and ammonia. The combination of humidity and corrosive gas cause the copper in the barn electrical system to corrode at a much faster rate than the electrical system in the home. Rodent concentrations within the barn can cause damage to the electrical system and increase the risk of a barn fire.
Corrosion
Corrosion can cause two different fire ignition risks:
- Localized heat generation — As the surface of the copper wire or terminal in contact with the corrosive gas corrodes, the cross-section of the remaining copper becomes smaller. Electrical current travelling through the reduced copper cross-section responds by generating heat at that location. If sufficient deterioration of the copper occurs, the heat generated can reach the auto-ignition temperature of the surrounding materials. Once this temperature is reached, the surrounding material can spontaneously ignite (Figures 3 and 4).
- Arcing — Arcing can occur when corrosion has created a small gap between, for example, two terminals in an electrical system component. Stressed brass and copper can also crack when exposed to ammonia. In both of these cases, sparking occurs when an applied electrical current tries to jump across the gap. These sparks can ignite a fire in the surrounding materials
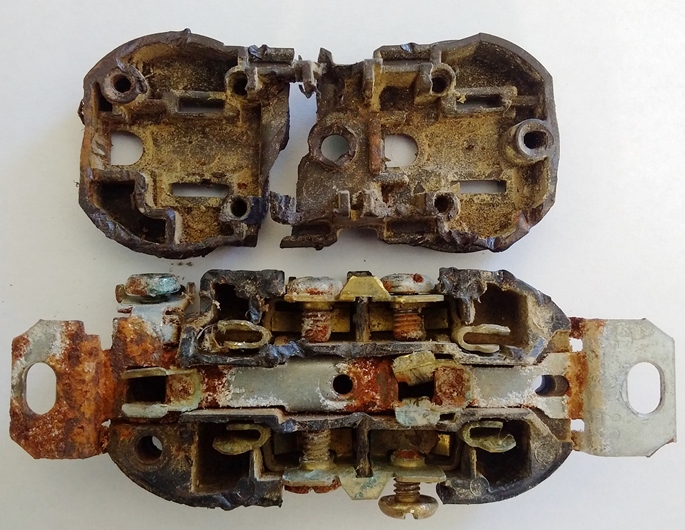
Source: Heartland Farm Mutual, Waterloo, Ontario.
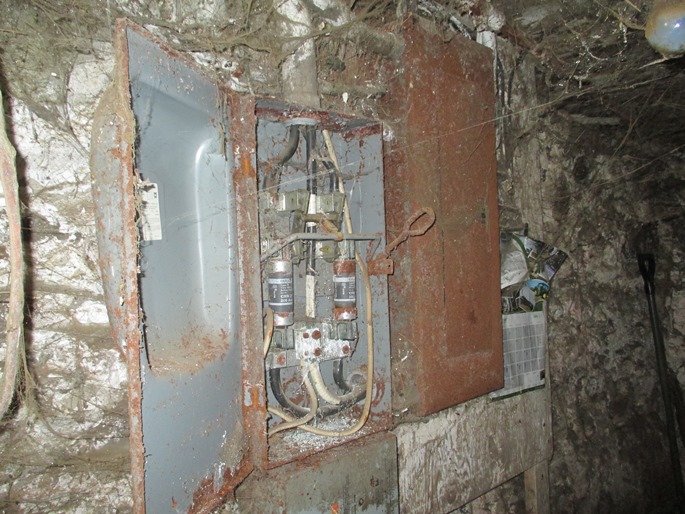
Source: Heartland Farm Mutual, Waterloo, Ontario.
Rodent damage
Rodents like to chew on the insulation coating on electrical cables in order to control the length of their continuously growing teeth. Arcing occurs when enough insulation is removed to expose two adjacent copper wires inside the cable (Figure 5). The arcing can ignite a fire in the adjacent materials.
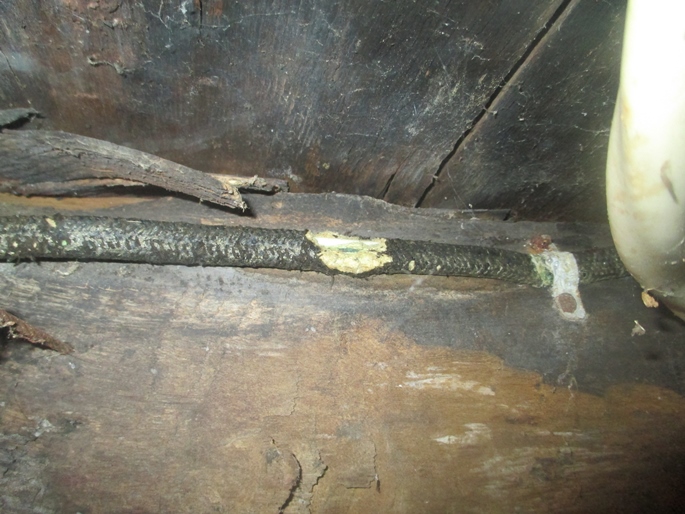
Source: Heartland Farm Mutual, Waterloo, Ontario.
Humidity and pressure washing
Humid environments can also accelerate corrosion in barn electrical systems. Unless specifically addressed, the components in barn electrical systems are not designed to withstand the pressure and water flow associated with pressure washing of barn interiors and equipment. Water entering an electrical component (plug, receptacle, light fixture, light switch, etc.) can create short circuits, accelerate corrosion and cause other damage.
Regulatory environment
The Electrical Safety Authority (ESA) is mandated by the Government of Ontario to enhance public electrical safety in the province. It is both a safety regulator and advocate. ESA has responsibilities under the Electricity Act, 1998, and the Safety and Consumer Statutes Administration Act, 1996.
ESA's primary activities are identifying and targeting leading causes of electrical safety risk: monitoring and enforcing regulations; promoting awareness, education and training, and collaborating with stakeholders to improve the state of electrical safety in Ontario.
ESA recognizes the additional environmental risks impacting electrical systems installed in barns and provides guidance on acceptable electrical system installations in the following documents:
- 2015 Ontario Electrical Safety Code (OESC)
- ESA Bulletin 22-3-* Electrical Equipment in Confinement Barns
Ensuring a barn's electrical system complies with regulatory requirements is a good starting point to minimize the risk of barn fires caused by electrical system faults. A licensed electrical contractor is familiar with all the specific requirements of these regulations.
Barn electrical system design and components
When designing, modifying or updating a barn's electrical system:
- It's the law that if you are hiring someone to do electrical work in Ontario, it must be a licensed electrical contractor. An ESA permit is required as it creates a permanent record of the electrical work that has been done and it triggers a review process by ESA. This is an added safeguard for the owner. When the work is complete, ask the licenced electrical contractor for the Certificate of Inspection to confirm the work was conducted in compliance with the OESC. Verify or find a licensed electrical contractor online.
- The OESC and ESA Bulletin 22-3-* require that non-essential electrical equipment and electrical service distribution panels must be installed in locations separated from the livestock housing area of the barn. Install this equipment in a separate room which is supplied with clean, dry, temperature-controlled air. This will reduce the exposure of the electrical system components to the corrosive gases and moisture present in the livestock areas of the barn.
- The OESC designates the type of wiring that must be used in barn electrical systems. For example, Non-Metallic Wet (NMW) or Non-Metallic Wet Underground (NMWU) cable must be used in livestock housing areas of barns. These designations indicate the cable insulation and outer coating is specifically designed for wet (NMW) or wet/underground (NMWU) conditions. Only copper cable is acceptable within the barn.
- The OESC does not permit the installation of non-armoured cables behind walls, floors or ceiling panels unless installed in conduit (Figure 6). Concealed cables that are not mechanically protected are susceptible to rodent damage and cannot be inspected for condition.
- The use of common receptacles, plugs and extension cords, in the livestock housing area of the barn have a heightened risk of starting a barn fire (Figure 7). The copper terminals in these components are continuously exposed to the wet, corrosive barn environment and can deteriorate quickly. The ESA Bulletin 22-3-* requires that equipment and lighting in this area of the barn must be hardwired wherever possible directly into sealed junction boxes (Figure 8). Where it isn't practical, wet-rated plug and receptacle connections such as those in Figure 9 must be used. This bulletin also dictates the use of anti-oxidizing paste on all wire connections to provide additional protection to the exposed copper.
- Choose electrical system components which are specifically designed to operate in the barn environment. The OESC requires that the electrical system components used in the barn must be specifically designed to withstand the barn's corrosive and wet environment. There are different grades of electrical components available for different operating environments.

Source: Heartland Farm Mutual, Waterloo, Ontario.
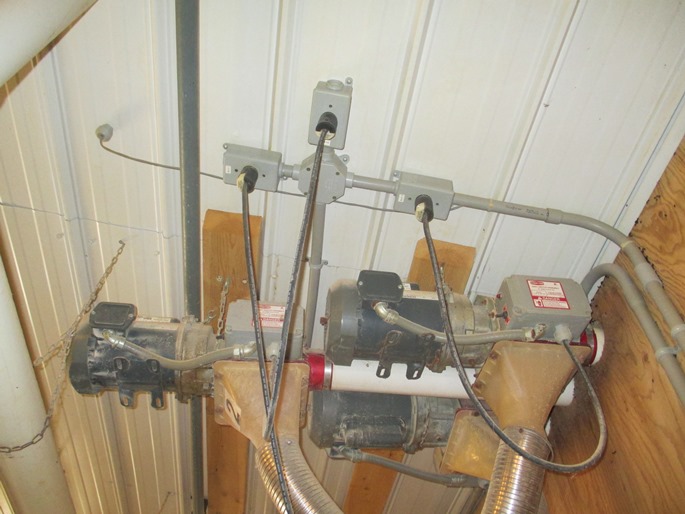
Source: Heartland Farm Mutual, Waterloo, Ontario.
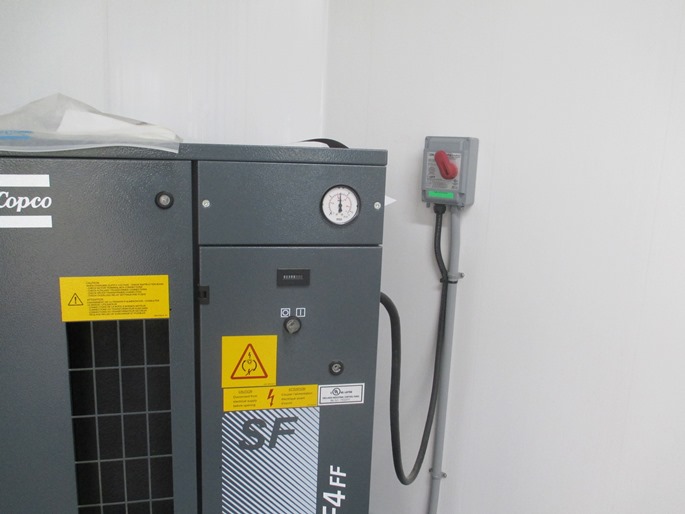
Source: Heartland Farm Mutual, Waterloo, Ontario
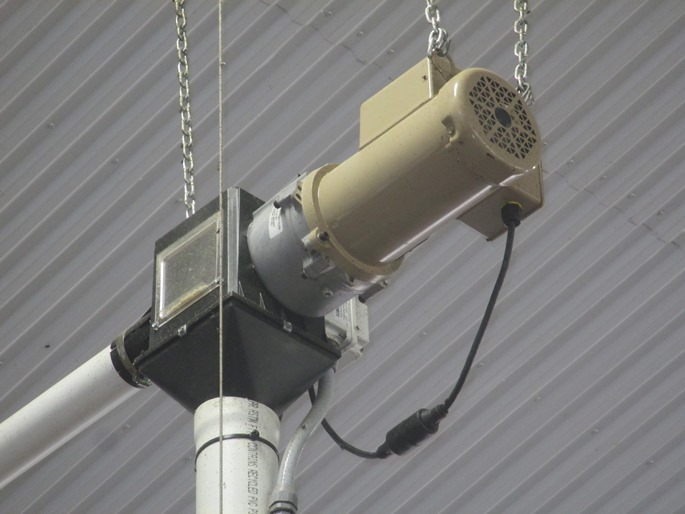
Source: Heartland Farm Mutual, Waterloo, Ontario.
The ability of electrical panels, junction boxes or disconnect switches to withstand dusty, wet and corrosive environments is indicated by their National Electric Manufacturers Association (NEMA) rating (Type 1 to Type 13) (Table 1). NEMA 1 and NEMA 2 are not appropriate for barn environments. The minimum rating for these components operating in a barn environment is a NEMA 3. Use components with a NEMA 4X rating in the livestock housing areas of the barn to withstand the wet and corrosive environment.
Rating | Details |
---|---|
NEMA 3 |
|
NEMA 3X |
|
NEMA 4 |
|
NEMA 4X |
|
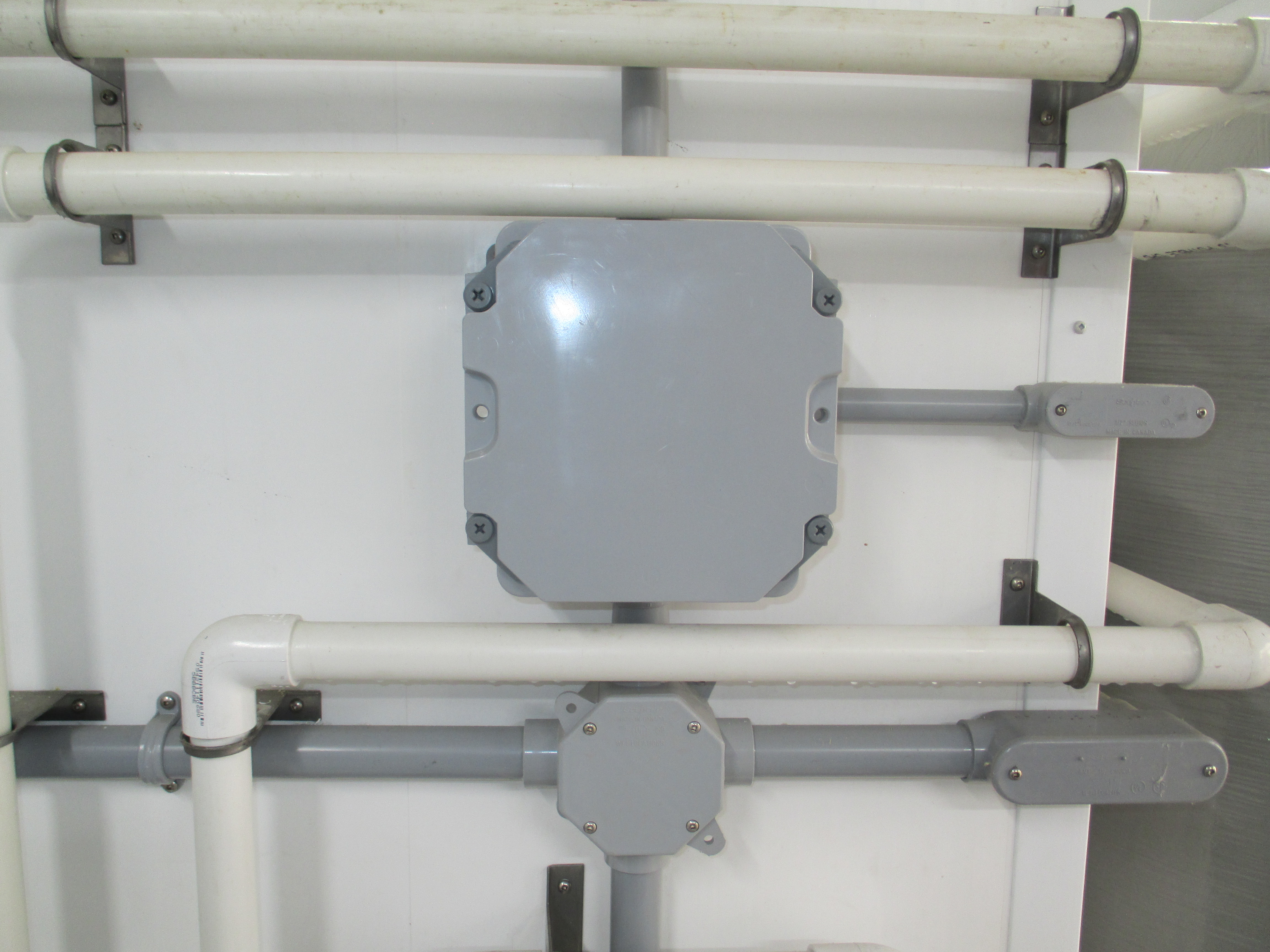
Source: Heartland Farm Mutual, Waterloo, Ontario
Electrical system wiring and components designed to withstand the barn environment are more expensive than, for example, electrical wiring and switches designed to operate in residential houses. This can increase the cost of barn electrical system materials.
Using the right grade of electrical components, as specified in the Ontario Electrical Safety Code, can help to reduce the risk of a barn fire and maintain regulatory compliance for your operation. Considering the overall cost resulting from a barn fire it is not worth the risk to use the wrong electrical system components.
Best management practices
The OESC and ESA Bulletin 22-3-* establish minimum requirements for electrical safety. To further reduce risk, best management practices that go beyond regulatory requirements are identified. Consideration should be given to the following best practices:
- Replace unprotected recessed wiring to minimize electrical safety risk. When replacement of the recessed wiring is not possible, install an arc fault circuit interrupter (AFCI) in the electrical supply panel to provide extra protection to these electrical circuits. An AFCI is a type of circuit breaker that is able to detect the condition of dangerous levels of electrical arcing within the circuit it protects. In comparison, conventional circuit breakers detect overload and short circuit conditions within an electrical circuit but not the presence of arcing. Arc faults are a leading cause of fires.
- Electric motors used in barns should have a totally enclosed frame to protect against dust, water and corrosive gases entering the motor. Look for the designation Totally Enclosed Fan Cooled (TEFC), Totally Enclosed Non-Ventilated (TENV) or Totally Enclosed Air Over (TEAO) on the motor nameplate. Use electric motors with designation Totally Enclosed Wash Down (TEWD) when the motor will be subject to high pressure wash downs.
- Electric box heaters installed in livestock barns are a specific area of concern. Many of these heaters are supplied with a plug already attached to the power supply cable. Heater installation using the supplied plug is not recommended due to the risk of corrosion on the plug and receptacle initiating a barn fire (Figure 11). In these cases, remove the plug and hardwire the heater power supply cable into a junction box with an appropriate NEMA rating for the installation location within the barn. If a plug and receptacle is required for maintenance purposes, use a wet-rated plug and receptacle set.
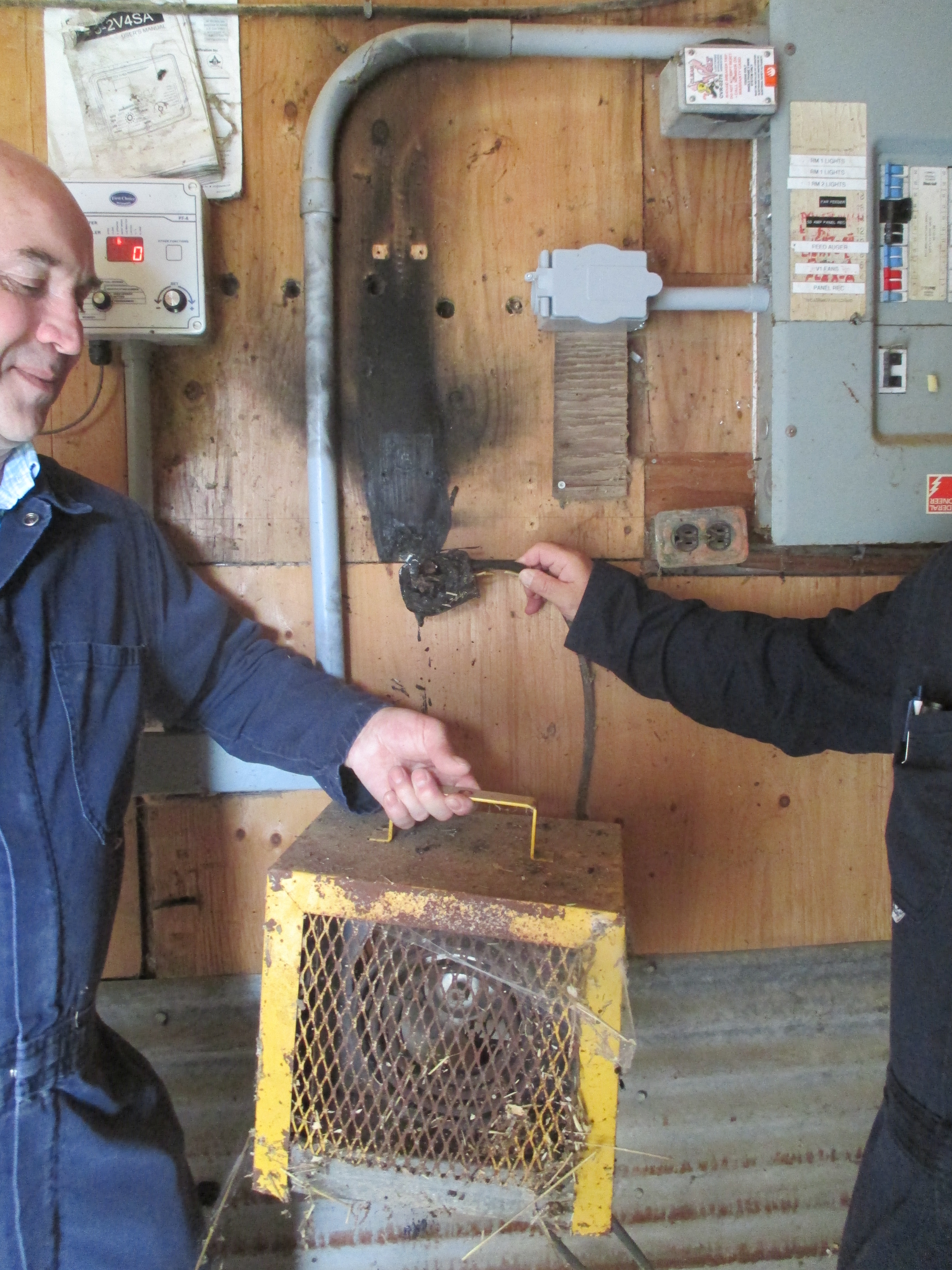
Source: Heartland Farm Mutual, Waterloo, Ontario
Additional barn activities
Some types of livestock barns are routinely washed several times during the year (for example, broiler chickens, weaner pigs, etc.) and the electrical equipment will be exposed to high pressure washers. To reduce risk of damage to electrical equipment:
- Minimize the amount of electrical components present in the pressure wash area.
- Ensure electrical components within the pressure wash area are rated to withstand high pressure wash down.
- Provide additional protection to the electrical system by covering the electrical components with plastic sheets prior to the pressure wash down.
There will be times when temporary activities will occur within the barn that require electricity supply through extension cords. In these cases:
- Ensure the extension cords are in good shape and contain wet rated plugs and receptacles.
- Extension cords should only be used on a temporary basis as they are not safe for long term use.
- Route the extension cord carefully to avoid the possibility of cable damage or immersion in water.
- Where possible, remove combustible materials from the area of the activity.
Over-voltage is a condition where an electrical system receives short duration spikes of voltage, which are significantly higher than normal. This condition can damage electrical equipment. If there has been a history of inconsistent electrical power quality in the past, consider the following:
- Contact the local hydro utility if any electrical power quality issues are noted.
- A licensed electrical contractor can measure the quality of the electrical power being supplied to the barn and Install protective devices (for example, an over-voltage protection device) when needed.
The Ontario Ministry of Agriculture, Food and Rural Affairs Publication 837, Reducing the Risk of Fire on Your Farm, provides additional information on best practices to reduce barn fire risk.
Barn electrical system maintenance
Barn electrical systems are not maintenance-free systems. The effects of the barn environment as well as continuously changing barn activities imply the condition and loading of the electrical system is continuously changing as well. The electrical system requires regular attention.
Conduct a barn fire safety audit at least four times each year to identify and correct any factors that increase the risk of a barn fire. Look for the following:
- Is there any visible evidence of damage, heat, arcing or excessive corrosion on the electrical system and surrounding materials? Hire a licensed electrical contractor immediately to correct any issues found.
- Are there any extension cords or temporary electrical equipment in place (Figure 12)? Remove these items from the barn if not being used for a short-term, monitored activity.
- Is there excessive flammable material being stored in close proximity to electrical system components (Figure 13)? If so, relocate the material to a safer location.
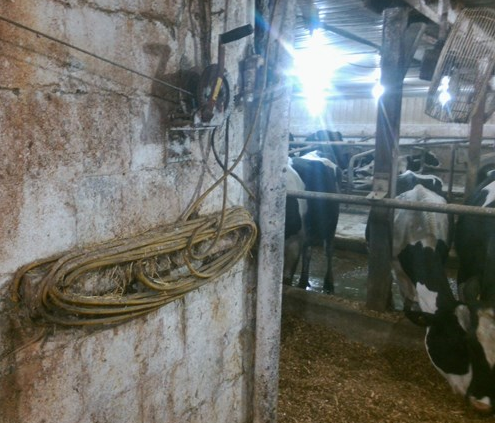
Source: Heartland Farm Mutual, Waterloo, Ontario.

Source: Heartland Farm Mutual, Waterloo, Ontario.
The barn electrical system, when under load, should be fully inspected by a licenced electrical contractor on an annual basis. A thermal scan of electrical system components using an infrared thermal scanner is very useful to identify hot spots which indicate the effects of corrosion (Figure 14). Many insurance companies provide this as a free service.
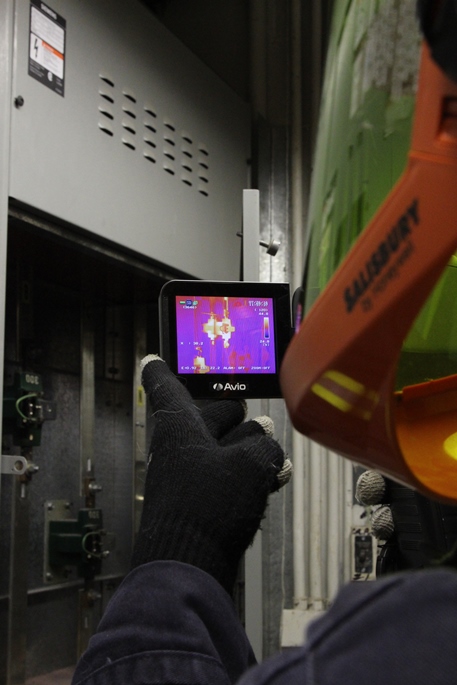
Source: Heartland Farm Mutual, Waterloo, Ontario.
Summary
Barn electrical system faults are a significant cause of barn fires each year. Focus on improving the electrical systems to ensure they are able to withstand the dusty, wet and corrosive environment within the barn. This will reduce the risk of a fire occurring. The Ontario Electrical Safety Code provides details on the required minimum system design practices and component choices to withstand the environmental challenges. Remember that barn electrical systems are not maintenance-free. Regular monitoring and a prompt response to issues found will keep the system in good shape. Hire only a licensed electrical contractor to do electrical work.
Disclaimer
The information contained in this factsheet is not authoritative. It is derived from the 2015 Ontario Electrical Safety Code and Electrical Safety Authority Bulletin 22-3-* Electrical Equipment in Confinement Barns and is for information purposes only. Efforts have been made to make this factsheet as accurate as possible. In the event of a conflict, inconsistency or error, the requirements set out in the referenced legislation takes precedence. Do not rely on this fact sheet as a substitute for specialized legal or professional advice in connection with any particular matter. Although the fact sheet has been carefully written, the authors and the government of Ontario do not accept any legal responsibility for the contents of this fact sheet, including direct or indirect liability, arising from its use. Retain the services of a licenced electrical contractor to address any concerns with your barn's electrical system. This document does not intend to provide assurance of compliance with electrical safety regulations in Ontario. To receive assistance with compliance with electrical safety requirements or additional information on electrical safety, contact the Electrical Safety Authority.
This fact sheet was written by John Van de Vegte, P.Eng., OMAFRA, Dan Ward, P.Eng., OMAFRA and Steve Beadle, P.Eng., OMAFRA. It was reviewed by the Office of the Fire Marshal and Emergency Management, the Electrical Safety Authority and Heartland Farm Mutual.