Gravity manure transfer systems for dairy barns
Learn about a non-mechanical way to transfer manure from the barn to long or short-term storage. This technical information is for Ontario livestock producers.
ISSN 1198-712X, Published May 2004
Introduction
Gravity flow is a non-mechanical way to transfer manure from the barn to long or short-term storage. This system has become popular because it is simple, less expensive than mechanical transfer systems and works just as well when properly installed and managed.
A number of dairy farmers in Ontario have installed gravity flow manure transfer systems (Figure 1). They are installed in new barns or used to replace worn out stackers and manure pumps. This fact sheet discusses the experiences of these farmers, the management and physical factors that are required to make the system work and questions to ask when considering installing such a system.
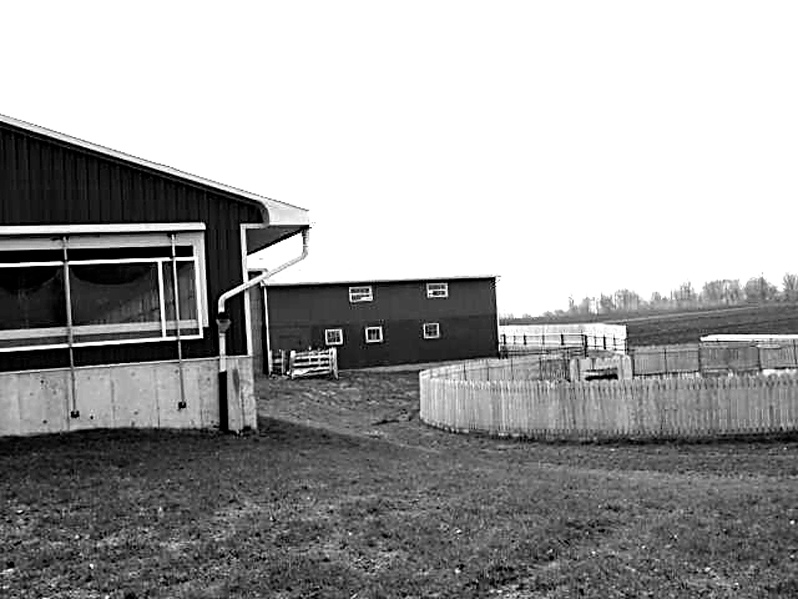
Basic requirements
The most important requirement is the consistency of the manure, not the slope from barn to storage. Gravity manure transfer systems require manure that will flow under its own weight. The manure must have a high moisture content with a limited amount of coarse bedding or long hay. These systems do not work when sand is used for bedding.
Experience indicates the manure needs to stay as a liquid in the storage, that is, there must be enough liquid in the stored manure so it can be mixed, pumped and transported to the field as liquid manure. In fact, manure that flows slowly when it leaves the barn becomes more liquid during storage, as long as the storage is made to hold the liquid fraction of the manure as well as precipitation (rain or snow).
Gravity transfer systems
Many Ontario dairy farmers have installed gravity manure transfer systems. Most were either ready to replace worn-out equipment (stacker, etc.), or were planning new manure storage for economic, labour or environmental reasons. Installing new transfer systems, whether hydraulic, air-type pumps or new stackers are always expensive. Gravity transfer is considerably less expensive, but will it work for you?
The following questions outline conditions that are necessary for gravity manure transfer:
- Are you feeding a Total Mixed Ration (TMR)?
- Do you feed little or no dry hay?
- Do you have a well-fed high-producing dairy herd? Cattle on abundant, top-quality feed tend to produce wetter, sloppier manure.
- Are your cows on mattresses or rubber mats to reduce bedding?
- Do you chop your bedding?
- Do you use bedding keepers or gutter grates to reduce the bedding in the gutter?
- Do you have to add a lot of bedding in the gutter to help move manure up the stacker?
- Are you having trouble containing the manure in the storage area?
- Does the pile slump, not pile at all, or try to ooze out of the storage when the frost comes out in the spring?
- Are you using organic bedding (not sand)?
- Can you construct a tank or pit 3-3.7 m (10–12 ft) deep without encountering a water table or bedrock problem? (See Table 1 for requirements in Nutrient Management Act, 2002 (NMA), O. Reg. 267/03, as amended.)
- Do you have natural slope between the barn and the storage site? A natural slope of 1.5–1.8 m (5–6 ft) from the barn to the storage site is ideal since this permits the storage to be built partly below and partly above grade. Some contractors recommend a minimum of 0.3 m (1 ft) elevation difference for every 3 m (10 ft) of horizontal travel.
Nutrient | Type of floor | Unlined storage | Lined storage |
---|---|---|---|
Liquid Manure |
Reinforced concrete |
1 m 10% clay or 0.5 m (1.6 ft) HSS1 or equivalent |
0.5 m (1.6 ft) native undisturbed material or compacted granular soil |
Liquid Manure |
Unreinforced concrete |
1 m 15% clay or 1 m HSS or equivalent | 1.0 m undisturbed soil or compacted granular material |
Other liquid agricultural source materials | Earthen storage |
Contaminated liquid2 Max. depth Max. capacity |
Nutrient storage3 2.0 m HSS or equivalent |
1 HSS = Hydraulically Secure Soil. Must test to a depth of 1.5 m below bottom for concrete or steel structure and 2.5 m for earthen storage
2 For storage of contaminated water (runoff, wash water, etc.)
3 For storage of liquid manure
1 m = 3.3. ft
If you have some slope and if the manure contains enough liquid (as determined by answering "yes" to the previous questions), then you can consider a gravity manure transfer system.
The amount of slope is important in determining what type of gravity system you choose. There are two distinct types: the minimum grade continuous-flow system and the steep grade, flush system.
With both systems the excavation is 3–3.7 m (10–12 ft) below grade in places. This can be extremely dangerous for workers who are shaping the trench bottom and setting pipes in places. Common sense and construction codes require using portable “shoring” or other methods to support the banks until the pipes are placed, aligned, sealed watertight and ready for backfilling. Hire an excavation contractor equipped to meet these important safety requirements.
Minimum grade, continuous-flow system
In this system, manure drops from an in-barn stable cleaner, tractor scraper or continuous-flow gutters into a vertical drop pipe (Figure 2). As manure is added, the head of manure in the drop pipe causes it to flow down through a transition elbow into the horizontal outlet pipe and eventually out to the storage (Figure 3).
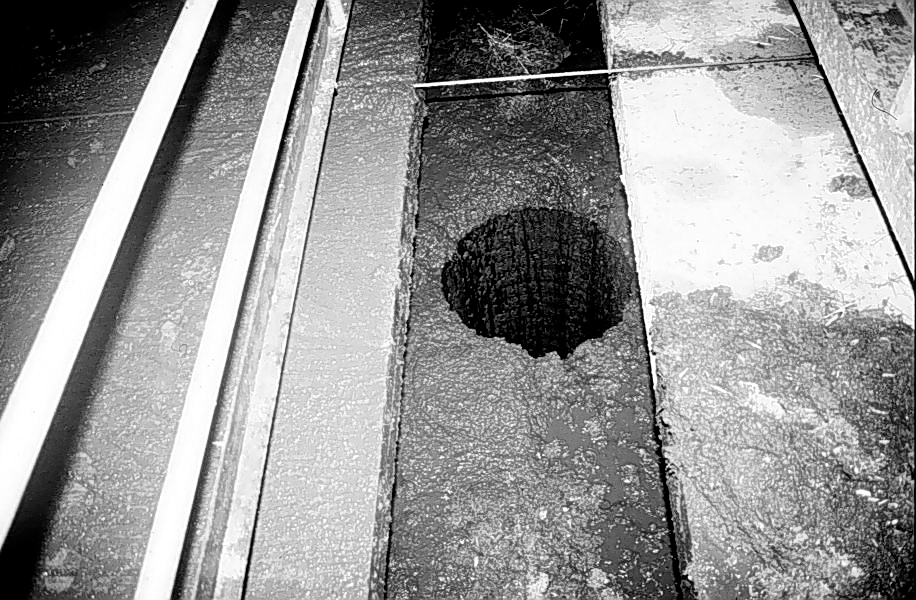
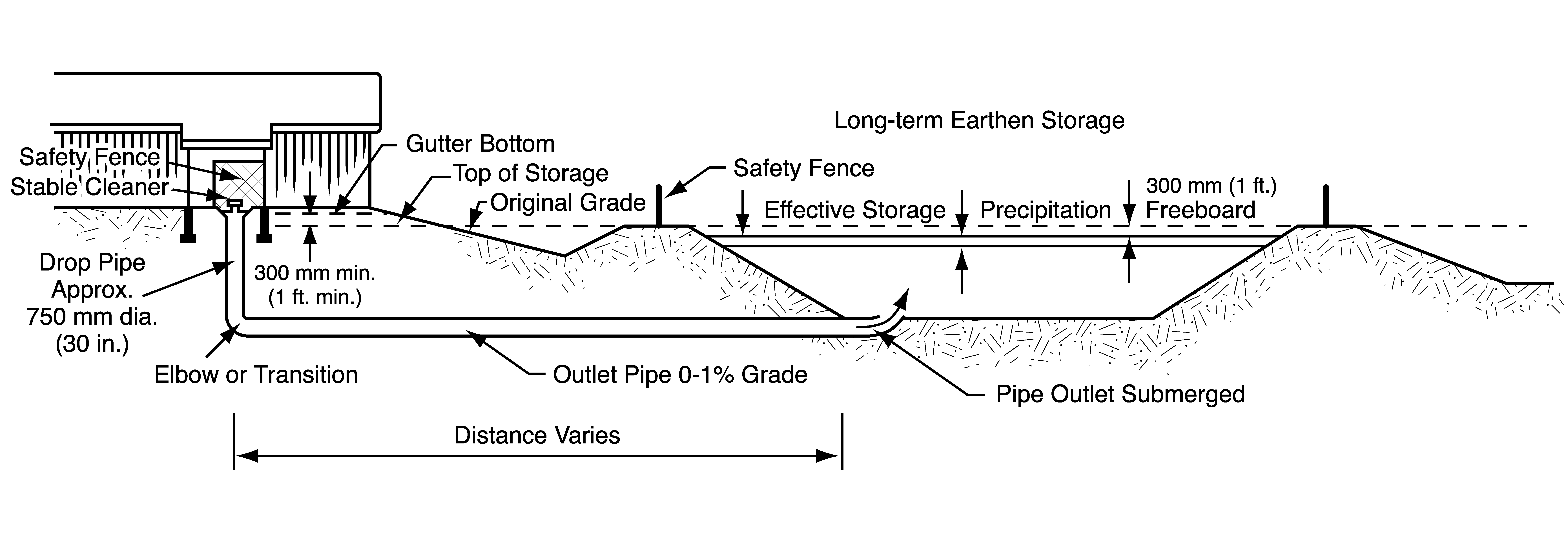
Mixing
Normally mixing the manure with stable cleaner paddles or tractor blade is sufficient. With continuous-flow, avoid excessive mixing. The liquid and solid manure fractions should flow as a mass. Some farmers have added a paddle wheel connected under the transmission of the stable cleaner and extending down into the drop pipe. This paddle wheel rotates slowly during the operation of the stable cleaner and seems to provide just the right amount of mixing.
Outlet pipe slope
To encourage manure to flow as a mass without separation of liquids and solids, install the outlet pipe with little or no slope, 0%–1% recommended. A slight back slope is also acceptable.
Size of drop pipe and outlet pipe
Outlet pipe diameters generally range from 60–90 cm (24–36 in.), with 76 cm (30 in.) being most common and the recommended size for both vertical and horizontal pipes.
Transition from drop pipe to outlet pipe
The transition part from the vertical to the horizontal pipe is one of the most important design considerations. Since the surface elevation of the manure in the drop pipe and in the storage tends to equalize, usually within a few minutes, the drop pipe need not be larger than the outlet pipe. A drop pipe the same size as the outlet pipe allows a smoother transition elbow, improving the flow from drop pipe to outlet pipe. Two 45-degree elbows work better as a transition than a single 90-degree elbow.
Therefore, in “minimum grade, continuous-flow” gravity manure systems, the best recommendation is a uniform 76 cm (30 in.) diameter for the drop pipe, transition elbow and outlet pipe. Exceptions are where two or more stable cleaners, or a wide gutter under slatted floors, discharge into one outlet pipe. The drop pipe in these cases must have a larger opening, which dictates either a larger drop pipe or a tapered hopper at it's top.
The Protocols under the NMA specify gasketed PVC pipe certified to CSA B 182.2 and conforming to ASTM D3034 with only specifically designed fittings allowed. No rough sawn holes sealed with concrete are permitted in the pipe.
If flow problems are possible, consider installing a 7.6 cm (3 in.) diameter pipe along side the large pipe to flush extra liquid from the storage back through the gravity system.
Steep grade, flush system
In this system, manure is held in a holding tank that is considerable higher than the storage. When the holding tank is full, a valve is opened to flush manure through the outlet pipe into the main storage (Figure 4). The bottom of the holding tank should be at, or above, the elevation of the top of the main storage.
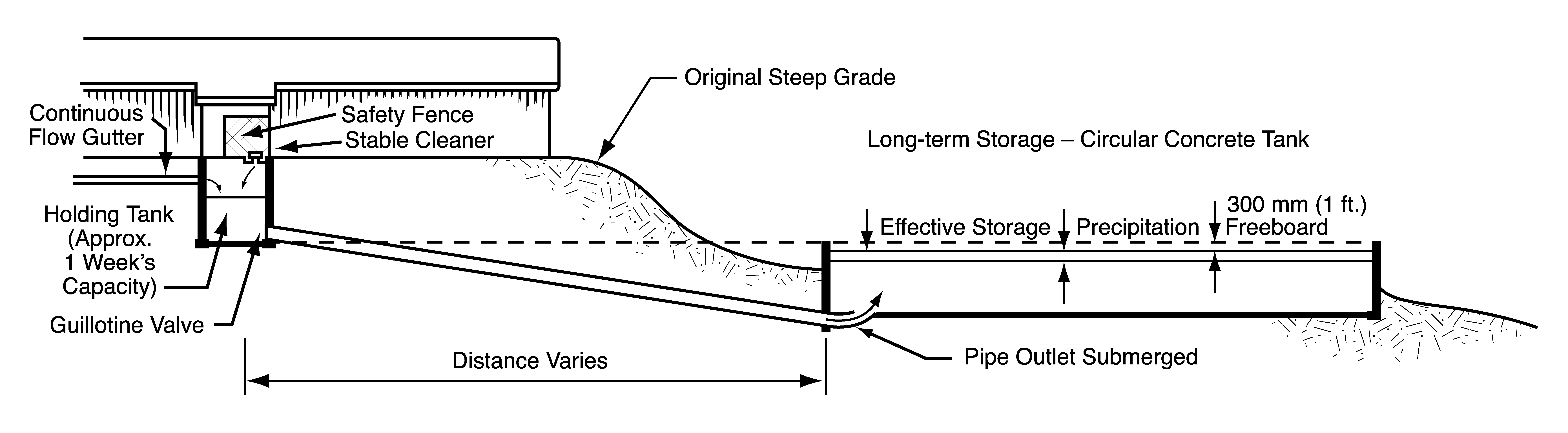
Holding tank, valve and outlet pipe
For practical reasons size the holding tank to hold about 1 week’s manure production. Make it 2.4–3 m (8–10 ft) deep to provide enough head to initiate the flush action through the outlet pipe when the valve is opened. A quick-opening, guillotine-type valve is best. The valve needs to be strong enough to withstand the pressure of the liquid manure. It should slide freely in its guides, fit tightly to prevent leakage and have a good linkage to the opening device. Use a heavy steel plate with steel “L” or “V-type” guides and a hydraulically operated opening device (Figure 5).
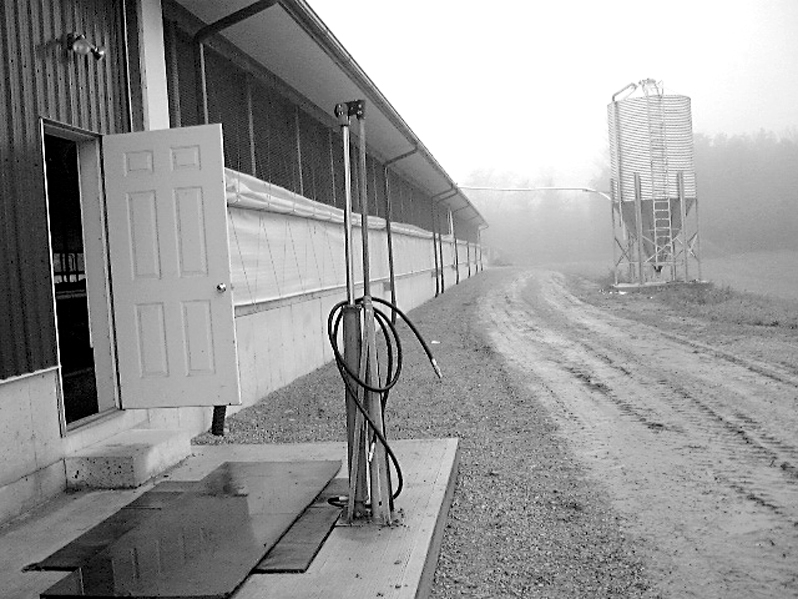
The outlet pipe can be smaller than that for the continuous flow system. Use either 40–76 cm (16–30 in.) outlet pipes; 60 cm (24 in.) is a good compromise. The 40 cm (16 in.) pipe is only suitable for very liquid manure with no feed or bedding clumps. Connect the outlet pipe to the holding tank via the guillotine valve located at the tank floor.
At the other end, the outlet pipe is connected into the long-term storage below, or at least halfway under, the storage floor. This ensures that the outlet is submerged as quickly as possible after emptying, thus reducing risk of freezing problems. Also the submerged end of the pipe becomes an effective gas trap preventing gases entering the barn from the storage. The connection to the long-term storage must use a flexible watertight gasket or membrane to serve as an anti-seepage collar.
The horizontal pipe does not need to extend to the centre of the storage. If the manure is liquid enough to flow to storage, it will flow in the storage as well. It is possible to have the outlet pipe enter at the top of the main storage, but only if you are sure the pipe will drain completely and quickly after each flush. There is also a high risk of build-up of frozen manure at the outlet pipe with top entry. The crust that forms on the manure storage may make it more difficult to push the manure out.
General recommendations
Type of housing systems
These gravity manure transfer systems work very well for tie-stall dairy barns with stable cleaners or continuous-flow gutters under totally slatted heifer barns. They work equally well in transferring manure from continuous-flow gutters under the alleys in free-stall barns or from scrapped alleys in free-stall barns. With continuous-flow gutters in the barn, more total grade from the floor level of the barn to the main storage is needed.
Manure from cold free-stall systems will be a problem if manure freezes on the floor and is scraped in large chunks to the drop pipe or holding tank. Add washwater from the milking centre to the vertical drop pipe so it mixes with the manure. Do not use gravity flow systems when sand is used for bedding. Sand-laden manure does not flow well by gravity.
Bedding
Use as little bedding as possible while still providing cow comfort. Most farmers learn quickly what can and cannot be done because unplugging the transfer pipe is an unpleasant task. Box stall manure can be added slowly to a large flow of liquid manure but the preference is to handle it as “solid” manure and move it into a separate storage. Gravity flow systems do not work when sand is used as a bedding material.
In tie-stall barns with conventional stable cleaners, keep bedding out of the gutter. With big enough stalls, bedding keepers and chopped straw or shavings, most of the bedding can be kept in the stalls where it belongs.
Many farmers add considerable bedding to the gutter in order to keep the cows’ tails clean. Properly-sized stalls help, but the use of tail ties is a more suitable option. They prevent tails from lying in the gutter while allowing the cattle freedom to switch. They also have an automatic breakaway device in case a cow gets loose. Gutter grates offer another but more expensive way to keep tails clean (Figure 6).
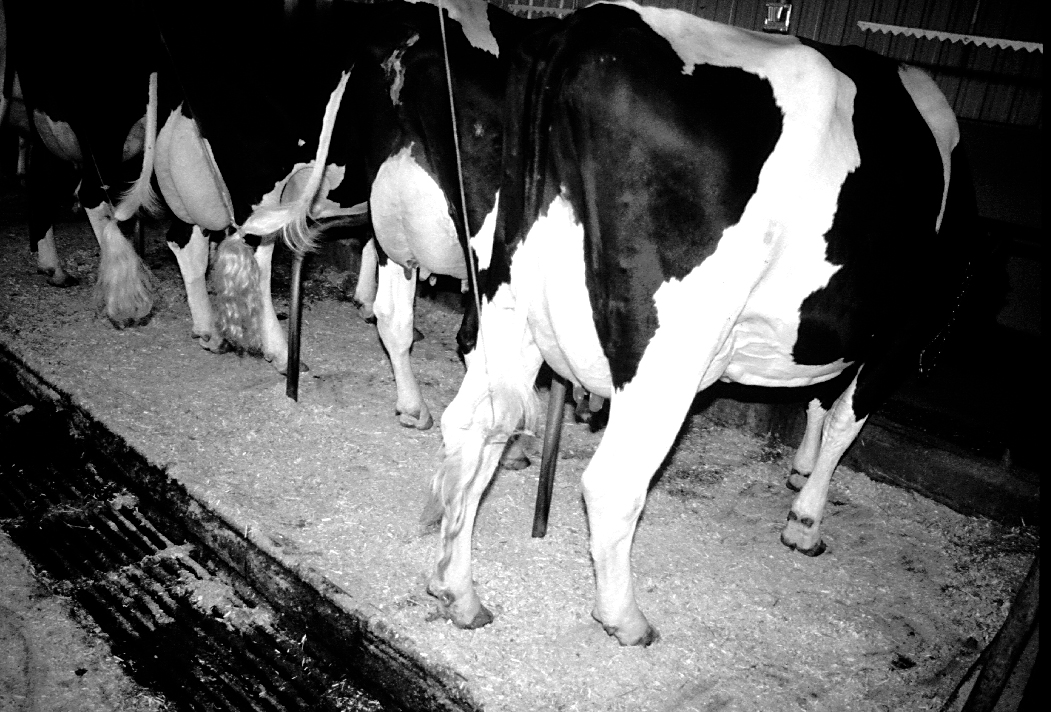
Barns with continuous-flow gutters
Continuous flow gutters require a level floor and a 10–15 cm (4–6 in.) lip at the exit to maintain a liquid base. Managing continuous-flow gutters is similar to the requirements to make manure flow in the gravity flow transfer system. If it flows in the gutter, there should be no problem with the transfer system itself. The type of feed seems to be very important, especially with heifers and dry cows. Heifer and dry cow manure is quite dry and does not move well through a gravity flow transfer system unless additional water is added.
Adding extra water
Extra water helps. Many farmers dispose of their milking centre washwater through their liquid manure systems. Usually the washwater is pumped directly from the milking centre, overhead through the barn and into the drop pipe or holding tank.
Long-term storage
In most liquid manure systems storage needs to be at least 3–3.6 m (10–12 ft) deep. Agitation equipment tends to work better at this depth and the storage collects less precipitation. With a minimum grade, continuous-flow system, strive to have the top of the storage wall 0.3–0.6 m (1–2 ft) below the bottom of the deepest gutter in the barn. This provides a minimum of 0.3 cm (1 ft) head to make manure flow when the storage is full. To prevent a disastrous overflow, make sure the storage is sized for the longest manure production period, plus precipitation, plus 0.3 cm (1 ft) of freeboard.
Outlet pipes up to 30 m (100 ft) long should not cause any difficulty. Since the velocity of material moving through the pipe is very low, so also is the friction loss. As indicated before, experience is limited to liquid manure storages.
Safety
Like many farm systems, there are some dangerous places that need special protection. Build a fence around the main liquid manure storage to exclude small children and livestock. At the drop pipe opening, place a large grill of welded reinforcing bars with 13 cm (8 in.) square openings directly over the drop pipe. Alternatively, fence off the drop pipe or holding tank from the rest of the building with tight fencing such as corncrib wire (Figure 7). The gate to this area should have a lock or a latch that cannot be opened by small children.
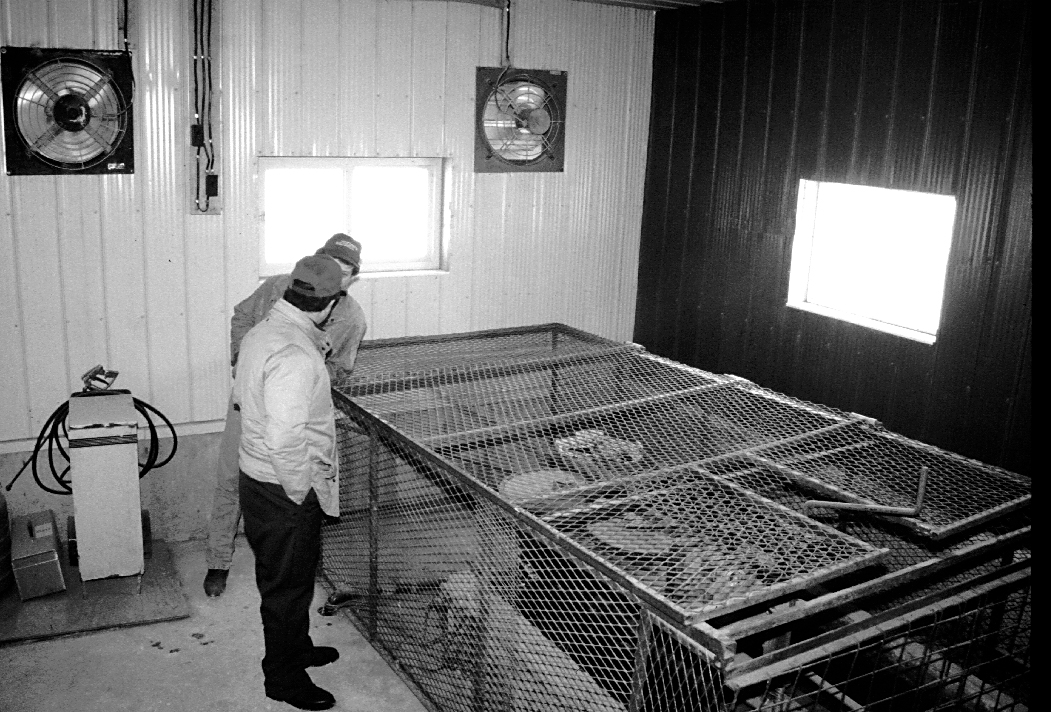
Remember the potential hazards of a deep excavation and the possibility of a cave-in during construction, as mentioned previously.
Conclusion
Dairy farmers have constructed many variations of the gravity flow transfer systems shown. Some installed systems have outlet pipe slopes and diameters different from those recommended here. All of the systems seem to work quite satisfactorily. Each farmer has adapted unique management practices to suit individual systems.