Hog target weight calculator
Learn how to accurately determine the weight of a hog. This technical information is for commercial swine producers in Ontario.
ISSN 1198-712X, published June 2011
Introduction
Once the job of raising a hog is done, whether a profit is made may depend on the final step: marketing. While the cost of production is a key component of the profitability of any operation, maximizing revenue is as important to profit as reducing the cost of production.
The carcass weight targeted by a hog grading grid primarily determines when hogs are marketed. A variety of factors, from pig variation to space requirements to holidays, influence shipping practices that result in a less-than-perfect fit with the grading grid's target range. Some of these factors can be controlled or managed in order to maximize financial returns.
Sort loss
Revenue is lost when carcasses miss the grading grid's targets for lean yield or weight. While the value of this loss isn't itemized on the settlement statement, it can be estimated by tallying the numbers of carcasses on the statement that didn't fit into the target and calculating the resulting revenue missed. Even if the average weight and average lean yield of a group appear to hit the target, many carcasses may, in fact, lie outside it. While an average weight for a pen may seem adequate for shipping, it's important to remember that carcasses are graded and priced individually.
To minimize this source of lost revenue, pay careful attention to the grading grid being targeted and know the shipping weight necessary to achieve the best possible fit with the targeted carcass weight and lean yield. Understand the growth characteristics of the pigs and the dressing percentage (DP) at the packing plant, by routinely reviewing shipping weights and the resulting settlement statement. Knowing how shipping weight affects carcass weight and lean yield will help pork producers effectively adjust their shipping strategy. Obviously, getting the shipping weight right is a fundamental starting point. There is always variation in a herd, but here is where it can be managed, at least to some extent. Grading grids use a sharp cut-off, not a gradual one, and hitting the next higher weight class could mean a loss of 10-14 points (using the Ontario Grid as an example), resulting in lost revenue.
Start with an accurate weigh scale. Accurately weighing pigs prior to shipping can result in greater returns than possibly any other manual effort in pork production. A survey of 34 pork producers in Kansas showed that the estimated return from one employee spending 2 hours per week weighing market hogs ranged from US$41.53 to US$190.38 per hour, depending on the sort loss to begin with². Using automatic sorters is another way to accurately weigh hogs.
The second tool for quickly determining the required shipping weight depending on the target carcass weight and DP is the Hog Target Weight Calculator (Figure 1). The target weight calculator can be used to see what carcass weight is likely to result from shipping hogs at a given live weight, or to see what effect a change in DP (which may result from extended transport times) might have on carcass weight.
Carcass quality can also be affected by handling decisions; shipping time is not the time to take chances with the investment already made in a finished animal.
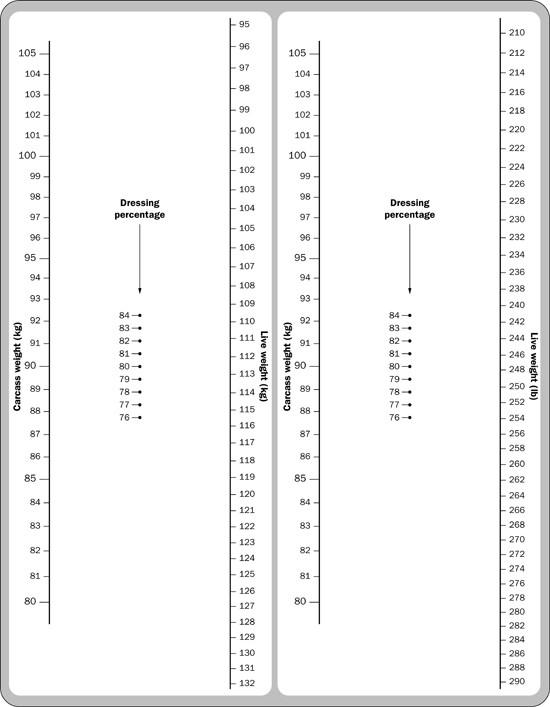
The target weight calculator
The target weight calculator diagrammatically relates carcass weight, carcass DP and live weight. The calculator can determine a shipping weight given a target carcass weight and an estimate of DP (or vice versa). Figure 1 shows the Hog Target Weight Calculator with shipping weight provided in kilograms and pounds.
Using the calculator, producers can determine the target shipping weights for their hogs, based on their current grid, or the potential shipping weight, based on the target weight range of a new grid. They can also estimate the carcass weight resulting from shipping hogs at a given live weight, or determine what effect a change in DP might have on carcass weight.
Using the calculator
- Find the target carcass weight (from your grid) on the left axis.
- Estimate your DP (from records, or use 80%).
- Use a ruler to read across from the target carcass weight, through the DP, to find the target live weight.
- Reverse the procedure to determine carcass weight based on a given live weight.
Example: Consider the current Ontario Grading Grid. The Index is the maximum of 114 over the weight range of 80-94.9 kg; this example uses 80-95 kg. Assuming a DP of 80%, we can read from 95 kg (carcass weight, left side) through the 80% point to arrive at a target live weight of about 118.8 kg on the right side. Similarly, a carcass weight of 80 gives 100 kg (Figure 2). In this example for the Ontario grid, the target live weight range is 100-118.8 kg. The live weight target range of 100-118.8 kg found in this example is quite wide compared to some grids where the maximum index occupies a single weight class range of 10 kg, or even 5 kg, compared to the current Ontario Grading Grid's 15 kg. In these cases, it is very important to know, and to ship at, the optimum live weight to hit the target carcass weight.
Use the calculators in Figure 1 to repeat the exercise, using your own grid. Be aware of the factors that can influence carcass weight and DP. Note how a change in DP changes the target live weight for a given target carcass weight.

Lower target carcass weight | kg |
---|---|
Upper target carcass weight | kg |
Dressing percentage | % |
Lower target shipping weight | kg |
Upper target shipping weight | kg |
Influencing factors
Target carcass weight:
- is determined by your grading grid
- depends on dressing percentage and live weight
- requires producers to know their grid and targets, and to weigh their pigs
Dressing percentage:
- transit time
- slaughter time (know your schedule)
- feed withdrawal/gut fill
- diet composition
Marginal feed cost and marginal return
After pigs have reached the minimum weight demanded by the grading grid, consider whether it is profitable to continue to feed to higher weights. This is particularly important when feed cost is high, and even more so if market prices are also low. It also assumes that the main driver is not the need to free up the facilities for incoming animals.
To make an informed decision, producers will need good information on the feed conversion ratio (FCR) of the herd over the relevant weight range (in addition to the change in lean yield discussed earlier). This is important, since conversion normally declines as animals get larger and can really only be estimated with any accuracy by measuring it in the barn. This information allows producers to make incremental calculations of the added cost of feed (the marginal feed cost) and the added value of the carcass (the marginal return), and determine the point where profit peaks.
Light pigs
Deciding when to move light pigs remaining at the end of a batch is particularly relevant to all-in/all-out systems. Is it worthwhile keeping these pigs, or moving them to a separate facility for finishing? Moving them helps with efforts to reduce disease transmission to newcomers if the space is needed for incoming pigs. Nevertheless, are the economics valid?
Good record-keeping will provide the answer here, as elsewhere - are these pigs "tail-enders" because they got a slow start, or because they are poor performers and trying to get them to finish weight is throwing more feed away? They may cost more than they are worth, especially if they tie up space. The best strategy may be to arrange to ship on two separate grids to accommodate another degree of variation in the herd.
Conclusions
The information required for making good marketing decisions and the advice and tools for interpreting the information are all available. Putting it all together is worth the effort. Providing carcasses that fit into the highest possible index score on the relevant grading grid is the goal. Shipping weight is under the producer's control, as is lean yield, to some extent, if the producer understands the factors determining it. The producer can also control pork quality - as affected by handling and transport — and pre-shipping feeding strategies. The potential impact of managing these factors on revenue is very great.
References
- de Lange, K. 1997. Monitor shipping strategies . . . and make more money. PigPens. University of Guelph.
- Keeler, G.L., Tokach, M.D., Goodband, R.D., Nelssen, J.L., and M.R. Langemeir. 1994. Assisting Swine Producers to Maximize Marketing Returns. J. of Extension. 32(1).
This factsheet was written by Jaydee Smith - Swine Production Systems Program Lead, Ontario Ministry of Agriculture, Food and Rural Affairs.