Manure handling options for robotic milking barns
Learn about manure systems in robotic dairy barns. This technical information is for Ontario dairy farmers.
ISSN 1198-712X, Published May 2016
Introduction
It is important to maintain clean and dry cow alleys in a milking barn. Cows will drag manure from dirty alleys onto their free-stall bed, which can result in unhealthy udders and feet.
This Factsheet discusses the products available for manure handling in robotic milking barns at the time of printing. The ministry does not recommend or endorse any specific product.
Robotic milking barns
Free-stall barns where cows are milked robotically require different cleaning strategies than barns where the cows are milked in a parlour. Since the free-stall area of a robotic barn is never free from cows, cleaning with a tractor or skid steer is not recommended. The layout of many robotic barns makes it difficult to clean the barn using traditional alley scrapers, because barn layouts make use of large open areas in front of the robotic milkers (Figure 1) and often have larger cross-overs than in parlour barns. As a result of these layouts, many robotic milking barns have slatted floors for better manure removal.
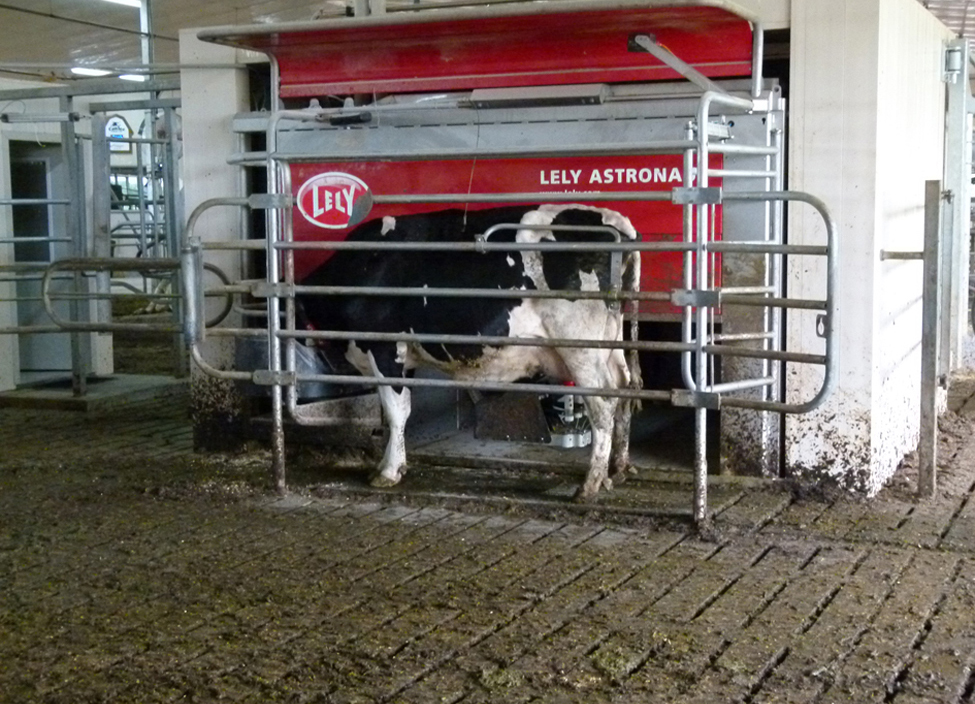
Slatted-floor manure systems
Slatted-floor barns originally were designed with narrow alleyways that concentrated cow traffic to push the manure through the slats. As interest in cow comfort increased and lying times in stalls lengthened, reduced cow movement in the alleys resulted in a greater build-up of manure in the alleyways. The most effective way to deal with this manure build-up is to use some form of scraper to push the manure down through the slats.
Automatic alley scrapers
Automatic alley scrapers with a cable or a shuttle drive are the most popular. These scrapers do not have to be as rugged as regular alley scrapers since they do not drag manure down the barn alley, but rather push the manure through the slats.
Challenges with automatic alley scrapers
Automatic alley scrapers are effective in pushing manure through slats, but they still involve cables or shuttle arms that have to be maintained as well as corner wheels or other drive mechanisms that have to be installed outside the cow area so as not to be a hazard to cow traffic, adding to the size of the barn. A disadvantage of automatic alley scrapers is that they cannot remove manure from cross-overs and holding areas.
Robotic slat cleaners
Robotic slat cleaners address the disadvantages of automatic alley scrapers. They do not require cables or drive wheels and can deal with cross-overs and any large open areas adjacent to robotic milking units. They can be programmed to scrape the areas in the barn where manure builds up the most, such as next to the free-stall curb, more frequently than other areas of the barn. This keeps the slats and, consequently, the cows cleaner.
Robotic slat cleaners are not intrusive. They do their job quietly and have little effect on cow behaviour. In fact, the only time cows become concerned is when the robotic slat cleaner is not moving. If a robotic slat cleaner encounters a cow lying in the alley or some other obstacle, it will either try to go around or try several times to push it out of the way. If the cow or obstacle still will not move, the robotic cleaner will shut down and wait for the producer to take action.
Types of robotic slat cleaners
At the time of printing (June 2016), there are two types of robotic slat cleaners currently used, the JOZ-tech, also distributed as the DeLaval RS250, and the Lely Discovery. Basic parameters for both types are shown in Table 1.
Parameter | JOZ-tech | Lely Discovery |
---|---|---|
Length | 129.5 cm (51 in.) | 127 cm (50 in) |
Width | 71.9 cm (28.3 in.) | 88.1 cm (34.7 in.) |
Height | 59.9 cm (23.6 in.) | 54.6 cm (21.5 in.) |
Scraper width | variable | 88.1 cm (34.7 in.) |
Weight | 408 kg (900 lb) | 272 kg (600 lb) |
Driving speed | 13 fpm | 35-60 fpm |
Tank capacity | 79.5 L (21 USG) | 30.3 L (8 USG) |
JOZ-tech (DeLaval RS250) - The JOZ-tech robotic slat cleaner (Figure 2) navigates using a series of transponders installed in the floor. Using a remote-control device, the operator moves the robotic slat cleaner around the barn to lay out its initial route. An antenna on the unit picks up the signal from each transponder it passes over, which sends the scraper unit a command to either turn or continue in a straight line.
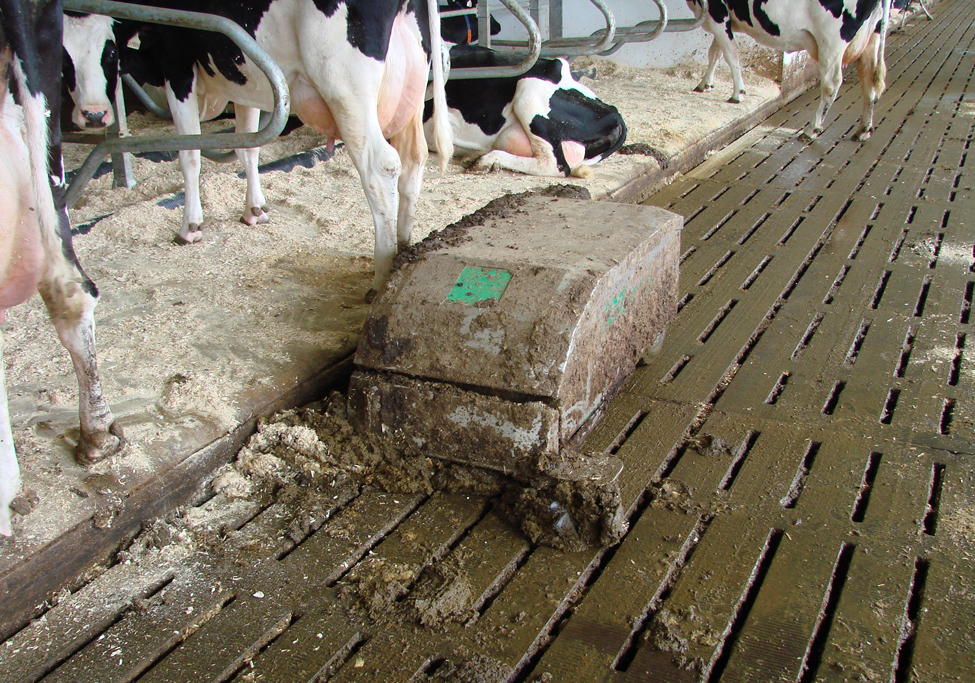
The unit has three wheels. The single front wheel is a drive and steering wheel about 30.5 cm (12 in.) in diameter and 20.3 cm (8 in.) wide, filled with foam. Sensors in the wings of the scraper blade keep the unit tracking along the stall curbs and walls. The two rear wheels count revolutions to track distance travelled.
If the JOZ-tech becomes stopped or disoriented for some reason, an operator can steer it to the next transponder using the remote control and the unit can adjust its route from that point.
The JOZ-tech uses a deep-cycle marine battery that must be charged for a continuous 6 hr each night, plus for 30 min. several times throughout the day, as it navigates its route, giving it a total of 16 hr of cleaning time per day.
Lely Discovery - The Lely Discovery (Figure 3) navigates by a combination of gyroscope, ultrasound device and wheel revolutions. The gyroscope is used to maintain orientation, ultrasound is used to determine the distance away from walls and curbs, and to keep the unit tracking along stall curbs, and the wheel revolution count is used to track distance.
Using a remote-control device, the operator moves the unit around the barn to lay out its initial route. A series of "bump" points are programmed into the route to tell the unit to change direction. In this way, the robotic slat cleaner can be programmed to do alleys multiple times along the curb and to return to the charging station as needed.
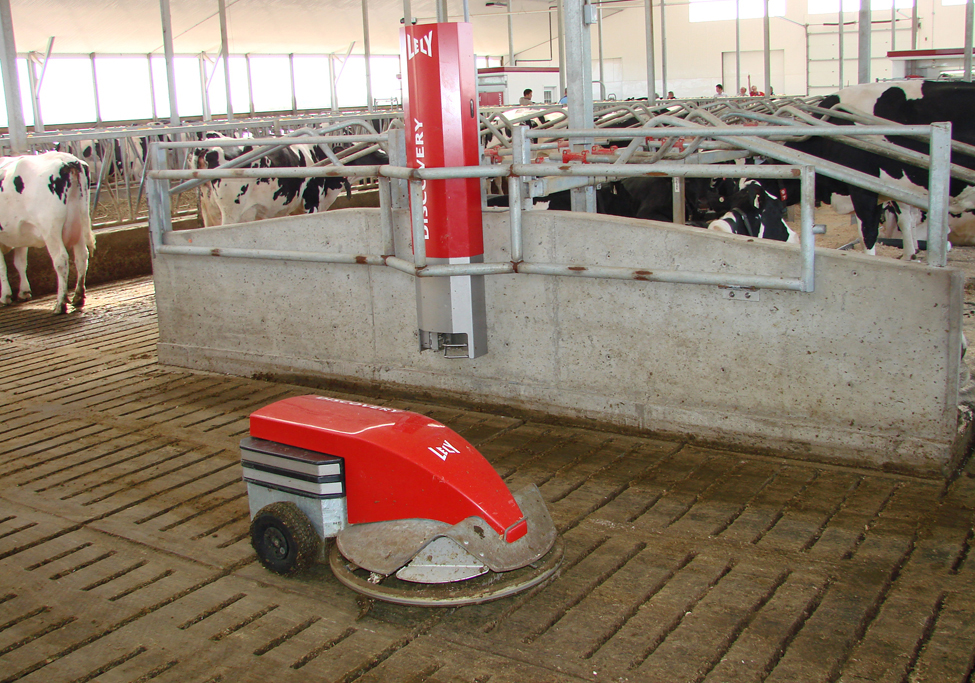
Powered by two separate electric motors driving two gel-filled wheels, the unit turns by varying the rpm of each individual wheel.
If a Discovery loses its position in a barn, an operator uses the remote control to direct it to a "bump" point to continue its route.
The unit can function 40% of the time and has to charge for 60% of the time.
Challenges with robotic slat cleaners
Dry manure stuck on slats can be difficult for robotic slat cleaners to remove. Hot, dry weather and summer cooling fans in barns can dry out the manure on the slats. When this happens, it can be more difficult to push manure down through the slats, and the tires may spin on the dry manure, causing the robotic slat cleaner to lose its position, as the revolution count on the wheels no longer represents distance travelled.
To address challenge, both units have a water spray system. Water tanks can be refilled during or after charging, and water spray applied to the floor to soften dry manure. The JOZ-tech system has both front and rear spray nozzles, and the Lely Discovery system has nozzles spraying just in front of the scraper blade.
Solid-floor manure systems
Not all robotic milking barns have slatted floors. Some producers use sand bedding for cow comfort, and other producers have installed robotic milkers in existing barns with solid floors. Still others have built new barns with solid floors. Sand bedding is not compatible with slatted floors, and solid floors require a manure-removal system other than tractors or skid steers. The two best alternatives for collecting manure from solid-floor barns are automatic alley scrapers and flush systems. With either system, the layout will have to be modified to eliminate large open areas that neither the alley scrapers nor the flush system can reach.
To keep the cows clean, dry and comfortable, structure alley floors so all liquid can drain off. It is recommended that the alley floor have at least 1% of slope, end-to-end, so the liquids will drain to the transfer point. The alleys should also slope about 0.4% to the centre to allow liquids to drain away from the stall curbs. Some producers want to have flat floors, but this usually results in ponds of water that collect between scrapings, as a floor can never be poured perfectly flat, and the liquid has nowhere to go. Other producers argue that the floors can dry out too much and become slippery. This seldom happens but does occasionally occur on outside alleys on windy, dry summer days. Some producers run a polyethylene pipe drilled with small holes along the outside wall that they use to wet the area for a period of time before scraping the alley.
Automatic alley scrapers
Automatic alley scrapers are used to collect manure from the alley floor and remove it to a transfer system either at the end of the barn or in the middle, depending on the barn length. They usually have one blade per alley and travel back and forth at timed intervals. The scrapers work in pairs, so while a scraper is cleaning one alley, the other is on the return part of its cycle. In a simple system, both alleys must be the same length. Blades fold back or raise on the return stroke, so manure is only moved in one direction. Scrapers can be chain drive, cable drive or rope drive with a special polyester rope.
Mechanical alley scrapers have the advantage of providing automatic mechanized rapid removal of manure. Frequent cleaning results in less manure being dragged into the stalls and, therefore, cleaner cows. During cold weather the scrapers have to run more often to prevent manure from freezing to the alley floors. Over time, alley scrapers will cause wear to the alley floors, making them slippery. Though these systems can be used with sand, the sand will increase the wear on the equipment and on the floor.
Tube scraper system
The tube scraper system (Figure 4) was pioneered by Mason-Dixon Farms in Gettysburg, PA. It was developed to minimize the "wave" of manure that travels in front of an alley scraper, especially in long barns, to keep cows' feet cleaner and drier.
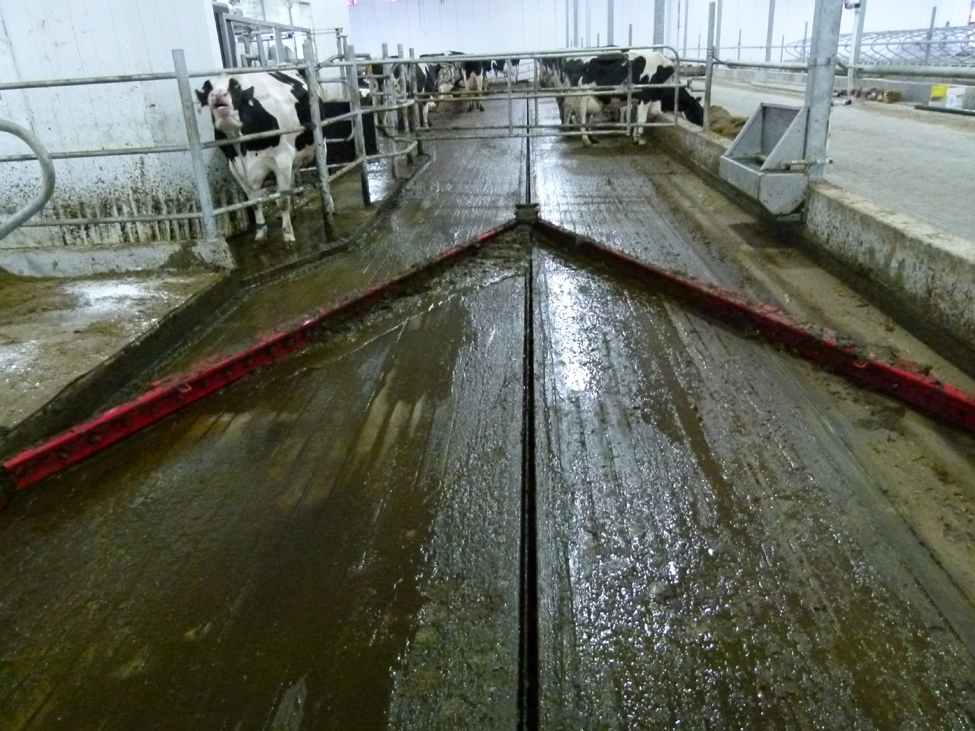
This system consists of a round or rectangular tube approximately 45.7 cm in diameter or 45.7 × 45.7 cm (18 in. diameter or 18 × 18 in.) installed beneath the alley floor (Figure 5). There is a 5-cm (2-in.) slot connecting the tube to the scrape alley. A V-shaped alley scraper blade pulls the manure to the centre of the alley, where it drops through the slot. There is a "paddle" in the tube attached to the scraper blade that moves the manure through the tube towards the transfer trench.
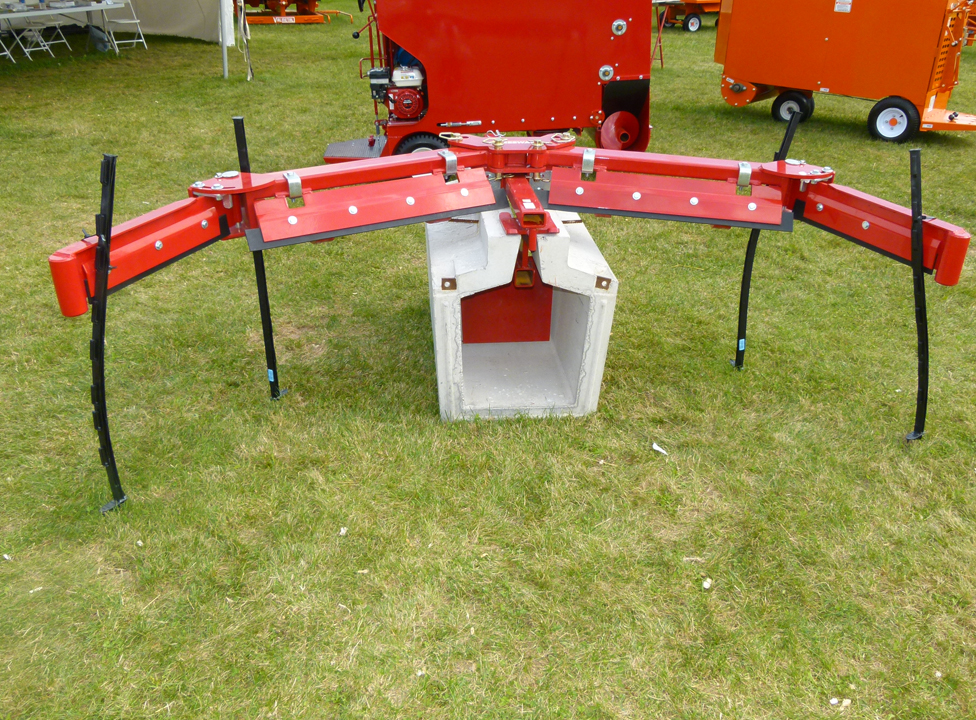
Hydraulic alley scrapers
Another type of alley scraper is driven by a hydraulic motor. A shuttle arm moves the scraper forward in a series of steps. An advantage of this system is that it can operate single scrapers, with different lengths of alleys, with a single drive unit. Cows are able to step over the slow-moving scraper blade. A disadvantage is that the scraper blade is an obstacle on the alley floor. In new installations, the shuttle arm can be recessed into the floor. Other disadvantages are manure freezing in the winter or drying in the summer on the shuttle arm, causing the scraper to skip.
Flush manure system
A flush manure system (Figure 6) uses a large volume of water to clean the alleys. Flush systems can be used to clean holding areas and cow traffic alleys.
Flush systems require a large volume of water to clean properly. Most systems use some form of solid-liquid separation, then recycle the separated liquids for the flush water. The cleaner the flush water is, the better the job it will do in cleaning the floors. If there is too much manure left in the flush water, a scum will build up on the floors over time, making them quite slippery.
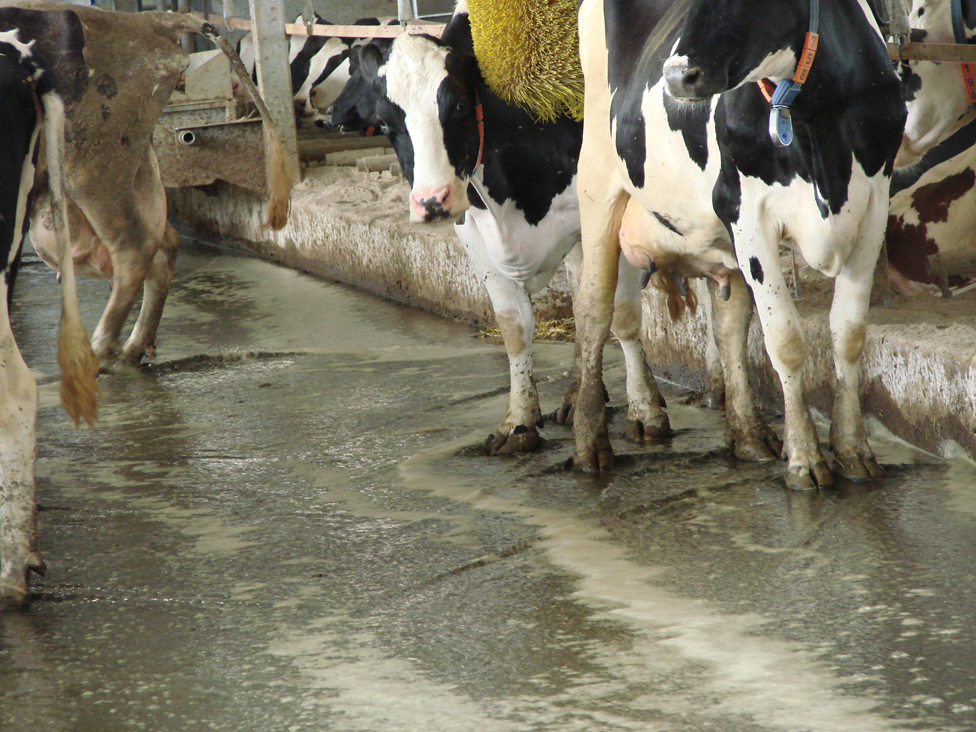
Flush manure systems must have alley slopes of between 1.5%-4% to flush properly. The alleys should be flat or slightly crowned in the centre to force the water to the curbs where most of the manure is, or they can be grooved in a "tractor tire" pattern to force the water to the curbs. Typically, 454 L/day (120 gal/day) per 455 kg (1,000 lb) of cow is needed for adequate flushing. Flush with at least 1,340 L/m (90 gal/ft) of alley width. All flush water should be released in 10-20 seconds. Determine the actual flush-water volumes and the frequency of flushing best suited to individual barns by trial and error.
Flushing has an advantage if sand is used for bedding. The sand-laden manure can be flushed into a settling lane, and the sand can be removed. The purity of the sand will vary depending on the parameters of the settling lane.
Feed stalls
Feed stalls (Figure 7) are not common but serve a number of purposes. The stall dividers prevent cows from disturbing each other during eating. The raised platform keeps cows from being disturbed by alley scrapers and protects them from the "wave" of manure resulting from scrapers or flush manure systems. The platform is not cleaned directly but remains reasonably clean as it is short enough that any manure lands off the platform.
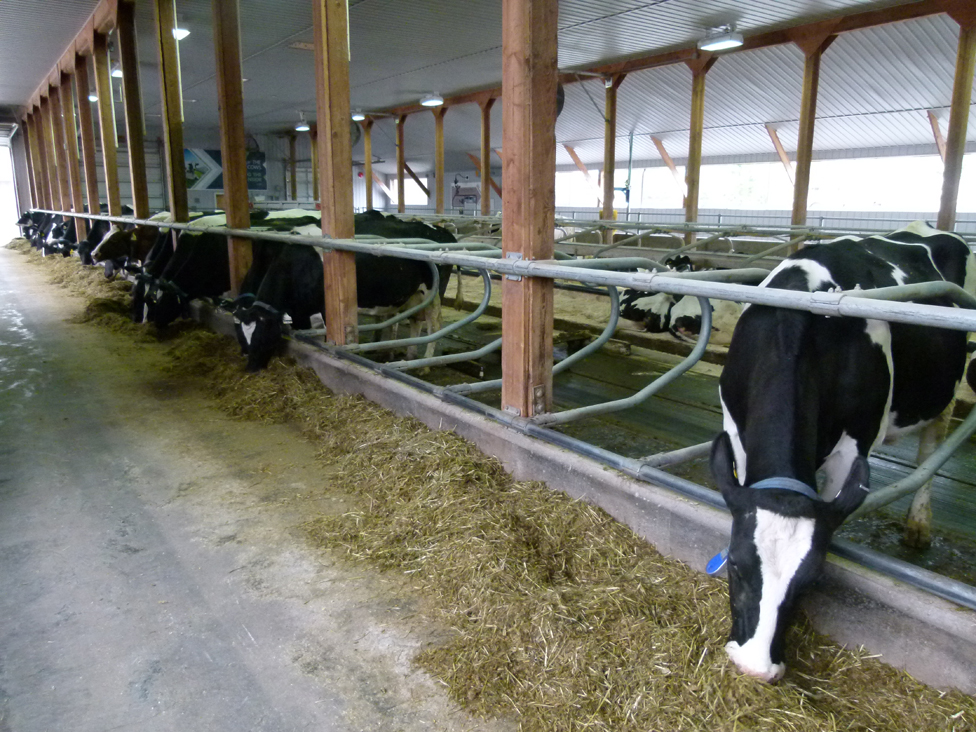
Summary
The design of the robotic milking barn and the material used for bedding will determine the best option for removing manure. A slatted floor system works well for layouts with large holding areas and wide cross-overs. Alley scrapers and flush systems can be used when sand or organic material are used for bedding. A tube scraper system is a modified alley scraper, resulting in cleaner floors and cleaner feet.
Resources
House, H.K. 2012. The Use of Robotic Slat Cleaners to Clean Slatted-Floor Dairy Barns. Joint Meeting. NABEC-CSBE 12-018. Orillia, ON.
House, H.K. 2010. Sand-Laden Manure Handling and Storage. Factsheet. Ontario Ministry of Agriculture, Food and Rural Affairs. Guelph, ON.
Lang, B., H.K. House, N.G. Anderson and J. Rodenburg. 2012. Free-Stall Housing Manual. Ontario Ministry of Agriculture, Food and Rural Affairs. Guelph, ON.
This factsheet was written by H. House, P. Eng., Dairy and Beef Housing and Equipment Engineer, OMAFRA, Clinton (retired).