Poly tanks for farms: tank inspection
Learn about three common inspection techniques used to evaluate the integrity of polyethylene tanks. This technical information is for Ontario producers.
ISSN 1198-712X, Published January 2023
Introduction
Polyethylene tanks, called poly tanks, are often used on farms (Figure 1) and by commercial application businesses to efficiently store and transport water and other liquids such as pesticides and fertilizers. However, poly tanks have a limited lifespan. They degrade quicker when misused, neglected or used beyond their design specifications. The goal is to replace the tank before it ruptures. The hard part is knowing how to assess the structural integrity of the tank to determine when replacement is necessary. This fact sheet explains three common inspection techniques used to evaluate the tank integrity.
Poly tanks are popular for several reasons:
- They are available from many suppliers and retailers.
- They cost less than tanks made from other materials.
- They are compatible with many liquid products used by farmers, commercial applicators and commercial businesses.
- They are relatively lightweight and easy to handle.
- They are resistant to corrosion (they won't rust).
- They are fairly resistant to impact.
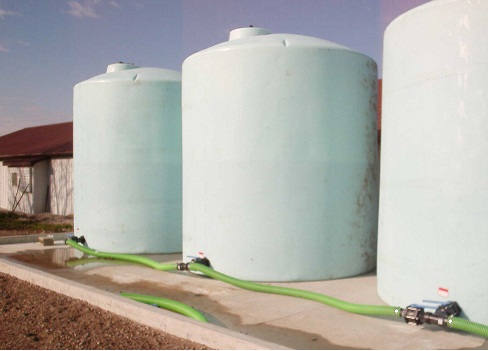
Poly tanks also have an often overlooked downside that can result in significant economic and environmental costs. When a poly tank is exposed to sunlight, ultraviolet (UV) radiation from the sun degrades the polyethylene. It changes from a tough, resilient material to a hard, brittle material (Figure 2), making the tank more prone to leakage or rupturing.
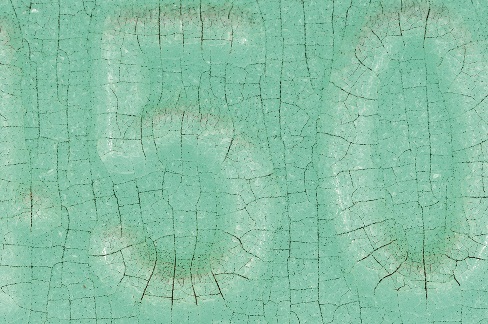
Before one can properly inspect and evaluate a poly tank, a basic understanding of how the tanks are manufactured, which materials are used, the manufacturing process and manufacturer markings is essential.
Tank material construction
Poly tanks are built using highly durable, chemical-resistant resins made to contain today's pesticides and fertilizers. They are built to the specifications of the manufacturer, not according to a national standard. The resins used in the manufacture of poly tanks are either high-density linear polyethylene (HDLPE) or high-density cross-linked polyethylene (XLPE). Both materials work well for the storage and transport of most pesticides and fertilizers, but XLPE is more chemical resistant and durable (and generally more expensive) than HDLPE. Contact the chemical manufacturer to determine if an HDLPE tank will work for the products stored and/or transported on the operation.
Poly tanks are manufactured using a process known as rotational moulding. A powdered polymer compound, with an UV protection package, is poured into a two-piece mould. The amount of UV protection varies by tank type and manufacturer. The mould is clamped shut and heated in a hot oven. During the heating process, the mould is tumbled in two directions. As the powdered polymer melts, the tumbling causes it to coat the inside of the mould. Once complete, the mould is moved into a cooling chamber where the temperature is slowly decreased. The completed tank is then removed from the mould.
This process creates/moulds poly tanks as a single piece. A visible external seam — known as the parting line — gives the impression that two pieces are joined together. The parting line results from the manufacturing process and represents the juncture of the two pieces of the mould, not the tank itself.
Specific gravity rating
A tank's specific gravity rating is a measure of its ability to hold materials. The specific gravity of a substance is the ratio of its density to the density of water (Table 1).
Manufacturers design tanks with specific gravity ratings of 1.0 to 1.9 or more. Tanks with higher specific gravity ratings can withstand greater hydrostatic stresses caused by stored liquids.
Understanding the significance of specific gravity to poly tank evaluation begins with the weight of water: 1 kg/L (8.334 lb/U.S. gal). The specific gravity of water is 1.0, and the specific gravity of all other substances is relative to the density of water. For example, a poly tank with a specific gravity of 1.0 is designed to hold the weight of water or any other liquid that weighs a maximum of 1 kg/L (8.334 lb/U.S. gal).
Specific gravity | Density of liquid stored |
---|---|
1.0 | 1 kg/L (8.3 lb/U.S. gal) |
1.5 | 1.5 kg/L (12.5 lb/U.S. gal) |
1.9 | 1.9 kg/L (15.8 lb/U.S. gal) |
In general, the weight of liquid fertilizers ranges from 1.20–1.44 kg/L (10–12 lb/U.S. gal). Specifically, 10-34-0 liquid fertilizer weighs 1.4 kg/L (11.67 lb/U.S. gal), while 28-0-0 liquid fertilizer weighs 1.2 kg/L (10.7 lb/U.S. gal).
At a minimum, only store liquid fertilizers in poly tanks that have a specific gravity rating of 1.5 or more. Always purchase tanks with a specific gravity rating at least one increment higher than required.
When inspecting existing tanks, the specific gravity rating tag may no longer be attached. It is not possible to figure out the specific gravity of a tank based on its appearance. Ask the dealer for the specific gravity rating of the tank in question, review the manufacturer's catalogue and/or examine the tank specification sheet. Sometimes, the specific gravity rating is part of the product code. Other manufacturers will stamp the information on the side or top of the tank. Consider these variations when purchasing used tanks.
Wall thickness
Tanks must account for the internal forces required to hold the specific gravity of any given product. Wall thickness is a major factor in the ultimate strength of a tank.
Tank wall thickness and overall design are the two most important factors in determining a tank's specific gravity rating. When purchasing a poly tank, consider the specific gravity of the heaviest liquid that will be stored and select tanks with that specific gravity rating or higher.
The manufacturers of poly tanks determine the location of critical stress points in the tank and strengthen those areas during the moulding process.
Extreme temperatures
Extreme temperatures usually do not impact high-quality polyethylene tanks. Quality tanks are designed to withstand expansion and contraction caused by extreme hot and cold. Results of tanks tested to −40°C demonstrate that freezing does not damage poly tanks. Constant, sustained temperatures above 37°C may weaken the tanks. Poly tanks are damaged if the temperature of a stored product exceeds 48°C.
UV degradation
Plastics deteriorate when exposed to sunlight. One way to increase the service life of the tank is to shelter or protect it from direct sunlight by placing the tank inside a building. If the poly tank will be exposed to the sun, select only those that have UV protection. Tank manufacturers can add stabilizers to the plastic resin during tank formation to increase the tank's resistance to ultraviolet radiation. For example, a poly tank with a UV 8 rating will have twice the resistance to ultraviolet light as a poly tank with a UV 4 rating.
Impact resistance
While poly tanks can withstand moderate impacts, it is important to protect them from high impact events. Where appropriate, protect poly tanks from vehicle collisions with bollards, guardrails or other physical barriers.
Manufacturer warranty
Manufacturers usually guarantee their tanks to last 3–5 years from the date of manufacture, not the date of purchase. Most tanks have 3-year warranties, but longer warranties are provided on more durable tanks such as those with a 1.9 specific gravity rating. The date of manufacture is sometimes imprinted on the tank as part of the serial number. If the manufactured date of a failed tank cannot be clearly determined, have the manufacturer look up the serial number.
Most warranties cover the tank if it is used according to the manufacturer's specifications and if the failure occurs during the warranty period. Coverage is for workmanship and materials only. Under these terms, a defective tank is repaired (if possible) or replaced at no cost to the original owner.
Warranties do not cover the replacement cost of lost product or environmental clean-up due to a release or spill, nor do they cover tank failure where the material stored had a specific gravity higher than the tank's rating. Read the manufacturer's warranty to find out what is and is not covered. Create a file marked "Poly Tanks" for all shipping papers, warranties and delivery tickets. While the tank is new and clean, record serial numbers and part numbers that are stamped on or into the plastic or written on a decal, and file them for future reference. This information is often required to file a warranty claim with the manufacturer.
Poly tank attachments and venting
Some methods of connecting attachments to poly tanks can decrease the tank life. A system completely plumbed with stainless steel or solid plastic pipe is very rigid, causing excessive stress on the tank valve and plug area of the tank wall (Figure 3). Flexible plumbing connections (such as hoses) are preferred to rigid pipe as they do not cause extra stress on the tank, thus reducing the potential for cracks to develop. Keep all plumbing as short, lightweight and flexible as possible.
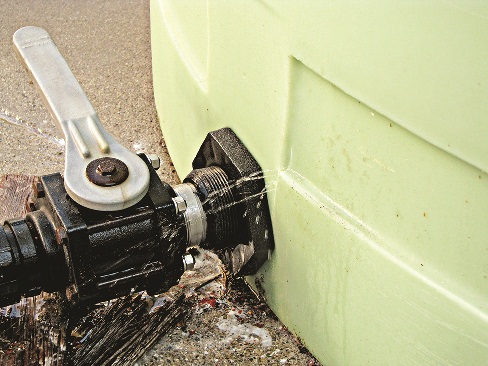
The most common valves used on poly tank systems are stainless steel or poly ball valves, and there are two options for their placement:
- One option is to use flexible hose between the fittings and the ball valve. This is especially important if the ball valve is heavy, because placing the valve some distance from the poly tank keeps its weight from pulling down on the plastic. The one problem with this approach is the inability to stop a leak if the flexible hose fails.
- Another option is to attach a lightweight ball valve as close to the tank as possible (Figure 4), followed by a flexible hose, allowing the flexible hose to pulsate as the fluid is pumped from the tank. The valve allows the tank to be shut off in the event of hose or pump failure.
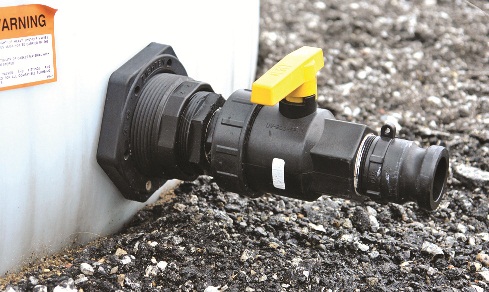
Vertical storage tank site inspection
Whether a tank is a few years old or 20 years old, the only way to be sure it is structurally sound is to perform inspections before filling and again at the end of the storage period. The inspection, prior to filling, provides reassurance that the tank can safely store or transport the fertilizer or pesticide required. Inspect the tank after use to determine if a new tank is required before the next filling (if the tank is defective or unserviceable, there is time to consider a replacement). Make sure that the base under a vertical tank remains solid. Animals can burrow underneath, causing the base to become uneven. Keep a written record of each inspection for liability or warranty concerns.
Threaded poly fittings sometimes develop leaks when left dry for extended periods of time, so be sure to check them before use. Some of the older poly tanks are plumbed with black iron fittings versus poly fittings, and after years of use the iron starts to deteriorate from the inside out. Inspect these fittings and consider replacing them with newer poly fittings.
Before conducting an inspection of the poly tank, it is important to know the difference between crazing within the tank wall (cracks that extend through the tank wall) and surface scratches.
Crazing is the appearance of very fine cracks within the tank wall, usually appearing as a network of fine lines that cannot be felt with a fingernail. The tank will still hold liquids, but its structural integrity is significantly reduced. Crazing occurs in both high-density and cross-linked poly tanks; it is a sign of serious deterioration within the plastic, which leads to cracks and fractures.
Cracking causes no displaced material; very abrupt lines may run parallel or cross at right angles to each other. UV cracking has a dry rot or alligator-skin look in advanced stages; a fingernail may catch on the cracks. It is common for the poly material around the crack to appear whiter than the surrounding polymer.
Most scratches displace minute amounts of polymer but remain superficial. Scratches are open to the surface. Displaced material is evident on the tank's surface. A fingernail would catch on the scratch.
It is difficult to visually determine a good tank from a bad tank. Three inspection techniques are used for inspecting poly tank integrity:
- writing on the tank with water-soluble ink
- candling the tank with light
- hitting the tank with a baseball bat
These techniques can pinpoint weakened walls and stressed areas around the fittings.
Marking the tank with a water soluble marker
Crazing may signal UV damage. UV crazing, which is very difficult to see, forms in areas where the tank gets maximum sunlight exposure; the lines become more visible when the tank is "coloured" with a water-soluble marker. Rub the marker over several 6-in.-×-6-in. sections on the sides of the tank exposed to sun, on its top and around fittings. Quickly rub off the ink with a dry cloth or paper towel. The ink left behind will penetrate the surface of the tank and reveal any crazing present (Figures 5 and 6).
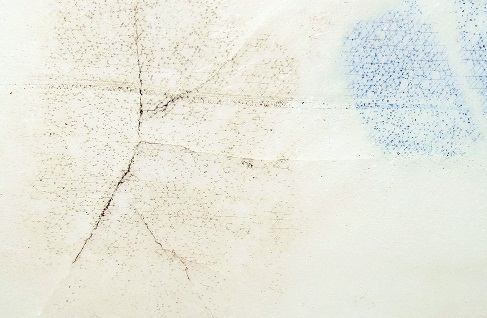
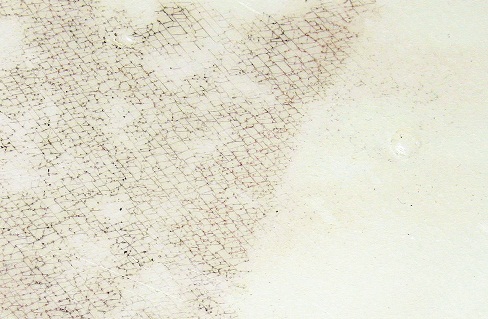
Crazing is one of the first signs of deterioration, so check tanks with crazing often. Consider using crazed tanks for water only. If the ink reveals cracking or spider webbing, where the lines go in all directions, classic UV radiation damage is indicated. Advanced deterioration to the plastic presents a checkered or "dry rot" appearance, indicating loss of elasticity. Replace a tank showing these symptoms.
The appearance of parallel lines signals early UV damage and the need for continual inspections. Replace tanks with parallel lines in the plastic around fittings immediately or use the tanks to store water only.
Candling: visual inspection with a light
Candling consists of placing a bright, cool light source inside a poly tank (Figure 7) while conducting a visual inspection from the outside (do not use a hot lamp, as it could melt the tank).
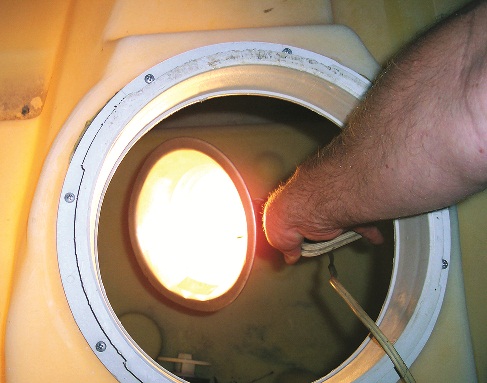
Repeat this procedure with the light on the outside of the tank (Figure 8) and someone looking through the fill neck or man way. Do not enter the tank. A camera, camcorder or other optical device may be helpful in detecting defects.
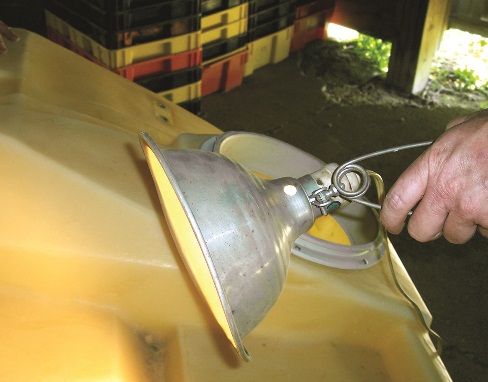
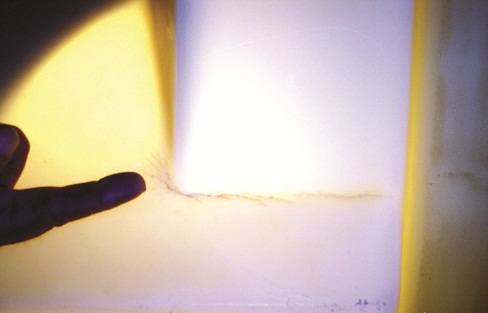
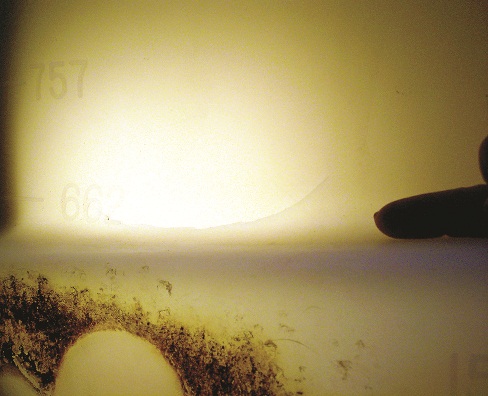
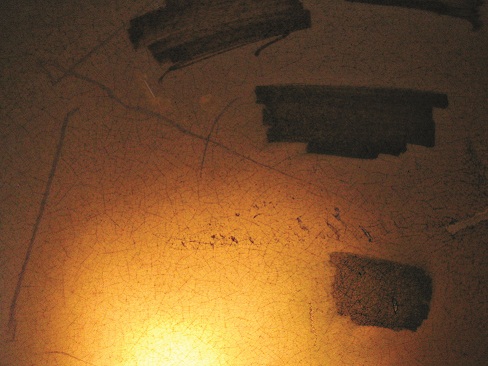
Hitting an empty tank with a baseball bat
An empty tank showing UV cracking can be further evaluated by striking it with a baseball bat. Some people are afraid to hit their empty tank with a bat, fearing that the bat might break the tank. Do not hesitate to perform this test, because if the tank ruptures in this situation, it should not be in service. Cracking an empty tank with a bat is a better option than risking the rupture of a tank filled with fertilizer or pesticide.
A good tank has the flexibility to bend outward as it is filled and inward as it is emptied. Tanks that are brittle (for example, if they show excessive or advanced cracking) have lost the ability to flex under pressure and to rebound when impacted. Test the brittleness of an empty tank with a solid swing of a baseball bat where the signs of cracking were discovered during the water-soluble ink inspection. Hit the tank along the sides and top (Figures 12 and 13) where they receive the most sunlight, then check the tank for signs of breakage. It is impossible to crack a good tank using this method, because the polymer is strong and resilient; if the tank cracks or breaks open when hit by a bat, a potential spill has been averted.
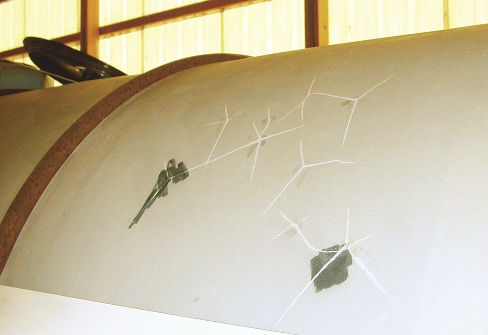
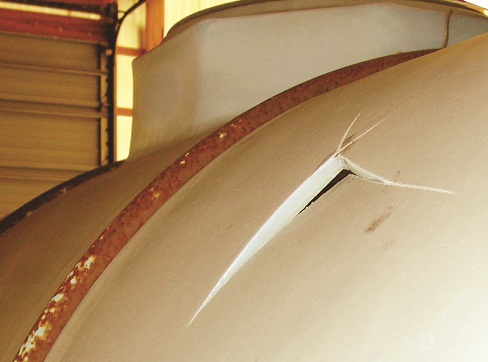
Repair of poly tanks
Most poly tanks with crazing or cracks, and those made from cross-linked polyethylene, cannot be repaired. Repair of polyethylene tanks is not recommended. Manufacturers sell kits for repairing small surface scratches or pin holes in high-density linear polyethylene tanks. Few adhesives or caulking materials adhere to polyethylene, and other means such as plastic welding are best left to professionals. Even if a tank is repaired, there is no guarantee that the repair will hold once the tank is filled. Use a repaired tank for water only and replace damaged tanks.
Environmental risk
If a poly tank fails, what are the risks to the farmer and the environment? There are monetary costs associated with the lost fertilizer, clean-up activities and fines if environmental charges are laid. Damage to the environment will depend on the location where the spill occurred and if fertilizer enters a watercourse resulting in fish kill. In 2008, in Ontario, a spill from a poly tank used to transport liquid fertilizer led to the release of fertilizer into a watercourse and resulted in fish kill. The farmer was charged under the Ontario Water Resources Act, 1990, with impairing the quality of the water contrary to Section 30(1) of this Act.
Best management practices suggest that if liquid fertilizer is stored on the farm:
- Select the appropriate tank (specific gravity).
- Inspect the tank regularly prior to use.
- Monitor the tank on a regular basis during use.
- Construct secondary containment around the tank(s) sufficient to contain 110% of the volume of the largest tank.
Summary
This fact sheet discusses many of the reasons poly tanks are commonly used to transport and store liquid fertilizer products. It also provides details for extending their service life, and preventive maintenance checks that will help prevent leaks and spills.
Take additional care when poly tanks are transported, or exposed to the sun or vehicular traffic. When managed appropriately, poly tanks can provide an affordable and convenient method for storing liquids on the farm.
This fact sheet was written and updated by Dan Ward, P. Eng., poultry and other livestock housing and equipment, OMAFRA.