Total mixed ration use in the ewe flock
Learn about the benefits of feeding a total mixed ration (TMR) to ewes. This technical information is for commercial sheep producers in Ontario.
ISSN 1198-712X, published June 2014.
Introduction
Total mixed rations (TMR)
The result of combining all ration components in one mix is known as a complete ration or TMR. By definition, a TMR contains weighed amounts of all diet ingredients, mixed thoroughly enough to prevent separation or sorting. It is usually a blend of forages, commodities and supplements formulated to specific nutrient requirements and offered free-choice. The purpose of feeding TMR is to ensure that each mouthful of feed consumed by the ewe is complete and nutritionally balanced.
Advantages of TMR
- use of a wide variety of feedstuffs, commodities
- no sorting of feeds, ration nutritionally balanced, steady state rumen conditions
- no separate feeding of vitamins, minerals, additives or grain
- improved production per unit concentrate
- reduced digestive upsets (acidosis, off-feed, laminitis)
Disadvantages of TMR
- cost of equipment
- ration balance point and grouping strategies required
- special attention required for ration formulation, feed analyses and silage moisture
- limited ability to handle dry hay
There are many combinations of feed distribution options. As you move from the traditional (forage plus grain) to TMR group feeding, there is an increase in efficiency of feeding. Pail feeding of ewes requires a large amount of labour. Many producers move into TMR feeding systems without considering that labour in the form of time is still required to move feeds to the mixer, individually add forages so that they can be weighed, and wait for mixing time and delivery of the TMR to the bunk. As a result, time spent feeding sheep may not be reduced unless the system is well planned.
The mixer is the heart of the TMR system. Before deciding which TMR system to purchase, compare the pro's and con's of each. Producing and delivering total mixed rations will require equipment and management changes on most farms. This Factsheet provides information on the type of equipment required and how to choose the correct equipment for your operation. A variety of mixers is available to fit specific flock requirements. Some of the design features of the most common TMR mixers are described here.
Total mixed ration equipment
Storage systems
Forages are the largest volume ingredient in the TMR and are usually grown and stored on the farm. Commonly, forages will either be stored in an upright silo, a horizontal silo or bales. The type and location of the silos will affect the location of the feed centre and the type of mixing and conveying equipment used.
For best results, two forage structures should be available to allow flexibility in controlling forage use in TMR. Small farms with limited forage storage are not easily adapted to mixing a good TMR.
Mixers
A variety of mixers are available today to fit specific needs. The type of mixer selected will depend on individual needs.
Tumble mixers
Tumble or drum mixers are the simplest of all TMR mixers. There are a number of different drum designs and attachments on the circumference of the drum lift that tumble the ration to mix it. Tumble mixers generally have less wear and lower power requirements than auger mixers of the same capacity. Dry hay must be chopped to a 2.5-7.5-cm (1-3-in.) cut if it is to be mixed in a tumble mixer. Tumble mixers are attractive because of their low cost and compact design. However it is more difficult to get a good mix with this type of mixer because there is less end-to-end mixing, and they generally have a lower feed capacity.
Some tumble mixer designs incorporate a centre auger that circulates the feed. The auger moves the feed to the front of the mixer where it either is remixed in the tumbling action or delivered to the unloading port. It is easier to obtain a more uniform mix in a tumble mixer with a centre auger. This type of tumble mixer also has more capacity than one without an auger but also requires more space. All tumble mixers must be operating during loading.
Design
- simple, compact design resembles a cement mixer
- different design and mode of lifting and tumbling are based on interior design
- in some mixers, centre auger moves feed to front to remix or unload
Loading and unloading
- can be loaded and unloaded from different ports depending on design
- operates when loading
Power and wear
- requires less power
- wears down less than auger mixers of same capacity
Capacity and mix quality
- mix capacity is lower (65%-70%)
- high-quality mix is more difficult to achieve
- mixer is difficult to empty completely and collects more residue (may contaminate subsequent batches and cause corrosion)
- scale is less accurate (some feed suspended in air while drum is rotating)
- chopped hay, 1-2.5 cm (½-1 in.), must be added to mixer
Chain mixers
Some TMR mixers use a drag chain to mix the ration. It is possible to load this type of mixer with a front-end loader. Use chopped dry hay and be sure to pour in the critical ingredients evenly from side-to-side in the mixer, or they may not be distributed evenly.
Design
- drag chain mixes ration (similar to apron chain on a manure spreader)
- in some mixers, cross auger used to improve mix quality
Loading and unloading
- can be loaded with front-end loader
- can be filled before mixing
Capacity and mix quality
- ingredients must be distributed side to side to ensure equal distribution
- mix capacity is 70%-80% of struck capacity (some suggest 85%; quality will suffer if overloaded)
- hay must be chopped 1.2-2.5 cm (1/5 to 1 in.) prior to incorporation
Reel or beater mixer
The reel or beater mixer includes a set of counter-rotating augers and a reel similar to a combine reel. Feed is lifted and tumbled by the reel, moving it to the augers, which also provide an aggressive mixing action. Knife sections on the auger flights cut or tear long dry hay into 8-10-cm (3-4-in.) pieces and incorporate it into the ration. This mixer is probably the best type to use for mixing byproducts. Take care in introducing ingredients to get good end-to-end mixing within the unit.
Design
- mixer uses reel or beaters (similar to combine reel)
- reel lifts feed to the counter augers, which provide mixing
- knife sections on auger flights cut long hay particles
Loading and unloading
- can be loaded with front-end loaded
- can be filled before mixing
Capacity and mix quality
- ingredients must be introduced carefully to get good end-to-end mixing
- mixing is more aggressive than tumble action alone
- wear in auger flights may result in increased mixing time
- mixer is well suited to mixing wet byproducts
- small amounts of hay can be added
- mix capacity is 70%-80% (some suggest 85%; quality will suffer if overloaded)
Auger mixer
Horizontal auger mixers use three to four augers to churn the feed in a hopper. One or two of the augers are counter-rotating to move feed opposite to an adjacent auger that provides the mixing action. Knife sections attached to the auger flights provide the ability to cut or tear long hay into 8-10-cm (3-4-in.) pieces and incorporate it into the ration. Auger mixers generally provide a more aggressive mix than the tumble mixer. As the auger flights wear, it may become necessary to increase the mixing time to obtain a uniform mix.
Auger mixers are filled before the mixing is started. If the batch is mixed too long, the power requirement increases dramatically. Auger mixers are the most common mobile type of TMR mixer.
Design
- 3 or 4 horizontal augers churn feed in hopper to move it along the auger flights
- augers are counter-rotating to move feed opposite to an adjacent auger for mixing
- knife sections on auger flights allow for limited incorporation of dry hay
- this is the most common mixer in use across species
Loading and unloading
- should be filled before mixing is started
- can be filled with a front-end loader
Capacity and mix quality
- mixing is more aggressive than tumble mixers
- wear in auger flights may increase mixing time
- over-mixing increases power requirements due to packing of small feed particles
- mix capacity is 90%-95%
- small amounts of hay can be added
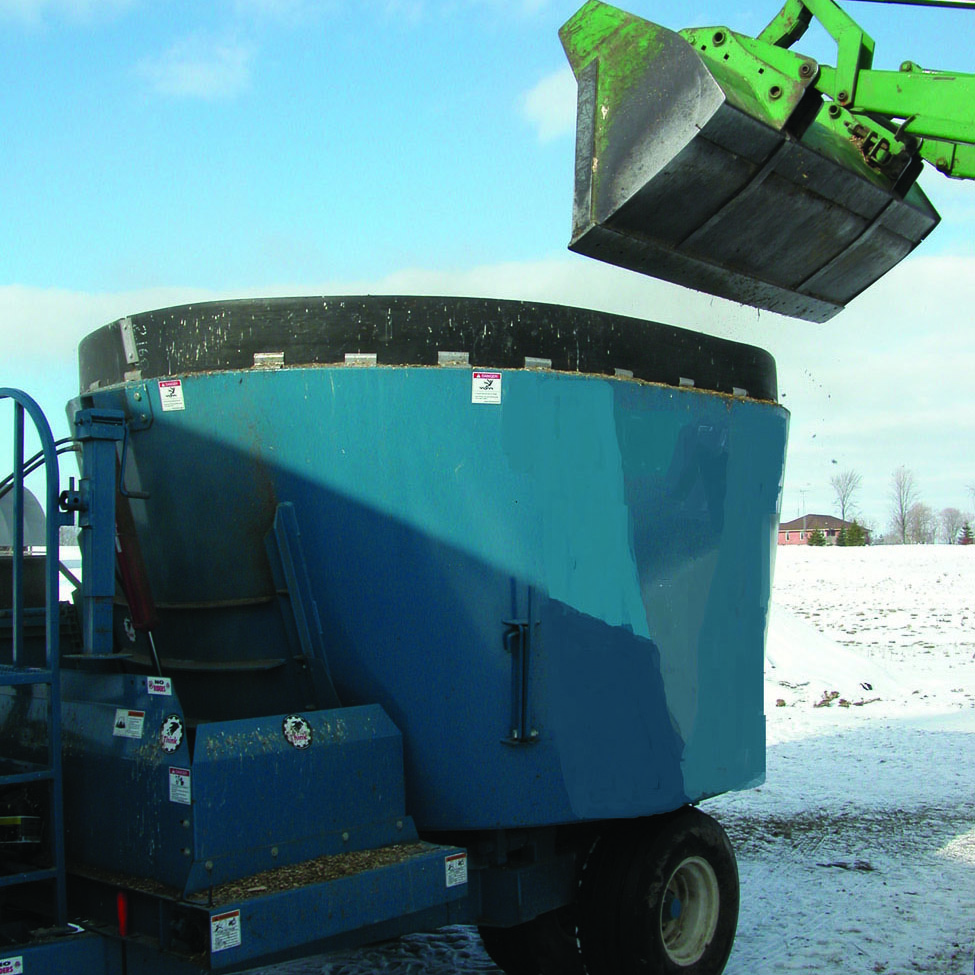
Vertical (round bale) mixers
The newest class of TMR mixer is the vertical mixer, which is capable of processing whole large bales of hay or baleage and incorporating large amounts of dry hay (Figure 1). It is the style generally recommended to sheep producers because of its flexibility to accommodate a transition from round bale hay or silage right through bulk silages and commodities.
Design
- mixer resembles giant kitchen blender
- vertical axle screw of diminishing screw diameter cuts and mixes
- bolt-on, replaceable, serrated blades are attached to vertical screw
- design features fewer wear points, fewer moving parts, no chains or sprockets
- options include stationary, truck mounted or pull type
Loading and unloading
- comes in many configurations of chain discharge elevator
- may require less power than other mixers
Capacity and mix quality (vertical mixers)
- mixer processes large round bales of hay or haylage
- bales may need 6-7 minutes of processing prior to addition of other ingredients or moisture may be needed from silages to initiate bale break-up
Mobile mixers
Mobile mixers can also serve a dual purpose by both mixing and delivering feed. They are useful if a silo is located at another farm, or if sheep will be fed at another farm. They may also be considered for fence-line feeding.
Design
- trailer or truck mounted weigh/mixer unit is also used for feed delivery
- mixer is available in vertical, auger, reel or tumble designs in various sizes
- truck-mounted unit ties up power unit at all times
- trailer unit requires tractor attending times
Loading and unloading
- offers maximum flexibility in choice of feed storage site and type
- can load with front-end loader and/or conveyor
- can unload by drive-through to conveyors, bunks, fence line feeders or other locations
Scales
Scales are required on a mixer to properly weigh and blend the ration. Electronic digital readout scales are accurate to 0.25% and use load cells that are incorporated into the mixer design to weigh ingredients in the mixer. Dust and moisture can cause malfunctions if the unit is not sealed properly. Use mail or food scales for small amounts of ingredients such as salt, vitamins and additives to weigh these materials before adding them to the batch.
Mixer sizing
When trying to decide what capacity of mixer to choose, sheep managers consider the following:
- How many ewes per group?
- How much time to feed?
- How much space for a mixer?
- What feeds will be used?
- How many feedings per day?
- How much money can be afforded?
- What are the plans for future expansion?
- What is the ration density?
Mixers are rated in terms of volume (cubic feet or bushels); it is important to realize that the gross capacity of the mixer and mix capacity are not the same. "Struck Capacity" is volume when filled to the top of sides. "Mixing Capacity" is volume at the top of augers, paddles, etc. All mixers need some space to provide a good mix.
For instance, the mix capacity for tumble mixers is about 60%-70% of their gross capacity, while the mix capacity of auger mixers may be as high as 95%. Check with individual manufacturers on specifications for their units. The secret of a quality mix is to not overfill or underfill the mixer. A good rule is to calculate the size of mix, adjust for mixing capacity, determine mixer size, then order the next largest one.
Tables 1-3 show sizing options for different rations.
Number of feedings per day | Mixer size for group size of 100 | Mixer size for group size of 200 | Mixer size for group size of 400 | Mixer size for group size of 600 | Mixer size for group size of 800 | Mixer size for group size of 900 |
---|---|---|---|---|---|---|
1 | 1.42 m3 (50 ft3) | 2.83 m3 (100 ft3) | 5.66 m3 (200 ft3) | 8.50 m3 (300 ft3) | 11.33 m3 (400 ft3) | 14.16 m3 (500 ft3) |
2 | 0.71 m3 (25 ft3) | 1.42 m3 (50 ft3) | 2.83 m3 (100 ft3) | 4.25 m3 (150 ft3) | 5.66 m3 (200 ft3) | 7.08 m3 (250 ft3) |
3 | 0.48 m3 (17 ft3) | 0.93 m3 (33 ft3) | 1.90 m3 (67 ft3) | 2.83 m3 (100 ft3) | 3.77 m3 (133 ft3) | 4.73 m3 (167 ft3) |
Assumes: 2.25 kg (5 lb) of dry matter/ewe/day. TMR weights 320.37 kg/m3 (20 lb/ft3) at 50% moisture (50% dry matter), approximately 0.014 m3 (0.5 ft3)/ewe/day fed. This volume should be adequate for most rations not adding dry hay
Number of Feedings per Day | Group size 100 | Group size 200 | Group size 400 | Group size 600 | Group size 800 | Group size 900 |
---|---|---|---|---|---|---|
1 | mixer size m3 (ft3) 1.98 (70) | mixer size m3 (ft3) 3.96 (140) | mixer size m3 (ft3) 8.18 (280) | mixer size m3 (ft3) 11.89 (420) | mixer size m3 (ft3) 15.86 (560) | mixer size m3 (ft3) 19.82 (700) |
2 | mixer size m3 (ft3) 0.99 (35) | mixer size m3 (ft3) 1.98 (70) | mixer size m3 (ft3) 3.96 (140) | mixer size m3 (ft3) 5.95 (210) | mixer size m3 (ft3) 7.93 (280) | mixer size m3 (ft3) 9.91 (350) |
3 | mixer size m3 (ft3) 0.68 (24) | mixer size m3 (ft3) 1.33 (47) | mixer size m3 (ft3) 2.66 (94) | mixer size m3 (ft3) 3.96 (140) | mixer size m3 (ft3) 5.30 (187) | mixer size m3 (ft3) 6.63 (234) |
Assumes: 2.25 kg (5 lb) of dry matter/ewe/day. TMR weighs 256.30 kg/m3 (16 lb/ft3) at 40% MC (60% dry matter), approximately 0.019 m3 (0.7 ft3)/ewe/day fed. This volume should be adequate for most rations that include up to 10%-15% (by weight) dry hayi.
Number of feedings per day | Group size 100 | Group size 200 | Group size 400 | Group size 600 | Group size 800 | Group size 900 |
---|---|---|---|---|---|---|
1 | 2.27 (80) | 4.53 (160) | 9.06 (320) | 13.60 (480) | 18.12 (640) | 22.65 (800) |
2 | 1.13 (40) | 2.27 (80) | 5.53 (160) | 6.80 (240) | 9.06 (320) | 11.33 (400) |
3 | 0.76 (27) | 1.50 (53) | 3.03 (107) | 4.53 (160) | 6.03 (213) | 7.56 (267) |
Assumes: 2.25 kg (5 lb) of dry matter/ewe/day. TMR weighs 227.46 kg/m3 (14.2 lb/ft3) at 45% dry matter, approximately 0.22 m3 (0.8 ft3)/ewe/day fed. This volume should be adequate for most rations that include around 25% dry hay on a DM basis
Tumble or drum mixers
Related mixer capacity | Dimensions length x width x height | Discharge height | Loading height | Mixer weight | Power required |
---|---|---|---|---|---|
1.13 m3 (40 ft3) | 1.52 x 1.37 m x 1.52 m (5 ft x 4.5 ft x 5 ft) | 35 cm (14 in.) | 114 cm (45 in.) | 476 kg (1,050 lb) | 550 watts (0.75 hp) |
1.98 m3 (70 ft3) | 1.52 m x 1.98 m x 1.83 m (5 ft x 6.5 ft x 6 ft) | 50 cm (20 in.) | 129 cm (51 in.) | 657 kg (1,450 lb) | 750 watts (1 hp) |
2.83 m3 (100 ft3) | 3.05 m x 2.13 m x 2.13 m (10 ft x 7 ft x 7 ft) | 60 cm (24 in.) | 152 cm (60 in.) | 1,133 kg (2,500 lb) | 2,250 watts (3 hp) |
5.66 m3 (200 ft3) | 4.27 m x 2.44 m x 2.44 m (14 ft x 8 ft x 8 ft) | 91 cm (36 in.) | 182 cm (72 in.) | 1,406 kg (3,100 lb) | 3,750 watts (5 hp) |
8.50 m3 (300 ft3) | 4.88 m x 2.44 m x 2.74 m (16 ft x 8 ft x 9 ft) | 91 cm (36 in.) | 182 cm (72 in.) | 2,041 kg (4,500 lb) | 5,600 watts (7.5 hp) |
Chain mixers
Related mixer capacity | Dimensions length x width x height | Discharge height | Loading height | Mixer weight | Power required |
---|---|---|---|---|---|
1.70 m3 (60 ft3) | 2.13 m x 1.37 m x 1.83 m (7 ft x 4.5 ft x 6 ft) | 8 cm (3.5 in.) | Top | 816 kg (1,800 lb) | 1,500 watts (2 hp) |
2.83 m3 (100 ft3) | 2.44 m x 1.52 m x 2.13 m (8 ft x 5 ft x 7 ft) | 11 cm (4.5 in.) | Top | 1,133 kg (2,500 lb) | 2,250 watts (3 hp) |
4.25 m3 (150 ft3) | 2.74 m x 1.83 m x 2.44 m (9 ft x 6 ft x 8 ft) | 14 cm (5.5 in.) | Top | 1,632 kg (3,600 lb) | 3,750 watts (5 hp) |
7.08 m3 (250 ft3) | 3.05 m x 2.13 m x 2.90 m (10 ft x 7 ft x 9.5 ft) | 16 cm (6.5 in.) | Top | 1,905 kg (4,200 lb) | 5,600 watts (7.5 hp) |
Auger mixers
Related mixer capacity | Dimensions length x width x height | Discharge height | Loading height | Mixer weight | Power required |
---|---|---|---|---|---|
2.83 m3 (100 ft3) | 2.74 m x 1.83 m x 2.13 m (9 ft x 6 ft x 7 ft) | Bottom | Top | 1,451 kg (3,200 lb) | 3,750 watts (5 hp) |
5.66 m3 (200 ft3) | 30.48 m x 1.83 m x 2.13 m (12 ft x 6 ft x 7 ft) | Bottom | Top | 2,222 kg (4,900 lb) | 9,000 watts (12 hp) |
8.50 m3 (300 ft3) | 35.56 m x 2.44 m 2.13 m (14 ft x 8 ft x 7 ft) | Bottom | Top | 2,948 kg (6,500 lb) | 18,650 watts (25 hp) |
Note: Consult supplier for more exact information.
Mixing strategies
Mixing strategies and mixing times vary between types of mixers, so it is best to check with suppliers for specific information. Dry hay can be used in many mixers if it is chopped first, or by using vertical mixers, but hay rapidly uses up the capacity of the mixer. It is important to have a mix that is no more than 60%-65% DM to mix properly. If the mix is too dry, it may roll and not mix properly and it will not be as palatable. Use an accurate method of testing the moisture content of haylage, corn silage and high moisture grains. Check these feeds often, and adjust ration weights accordingly to maintain the same dry matter consumption.
The key is to know the limitations of your mixer and to work within them to obtain the best mix possible.
Feed room
The processing centre or feed room houses all the conveyors, mixing equipment and feed storage. Finding enough space for the extra equipment required to produce a total mixed ration may present the biggest problem on many farms. Room is required to store bags of supplements, minerals, etc., and to have pails and scales for measuring these ingredients. The mixer must be readily accessible and it may need 7-9 m2 (75-100 ft2) of floor space alone (see Table 4 for dimensions). Provide approximately 1 m (3 ft) of space around the mixer to allow easy access by a set of stairs or ladder for filling the mixer or for a feed cart to be loaded.
It is possible to locate a feed room upstairs in the barn, but consider the strength of the barn and availability of hydro service before doing this.
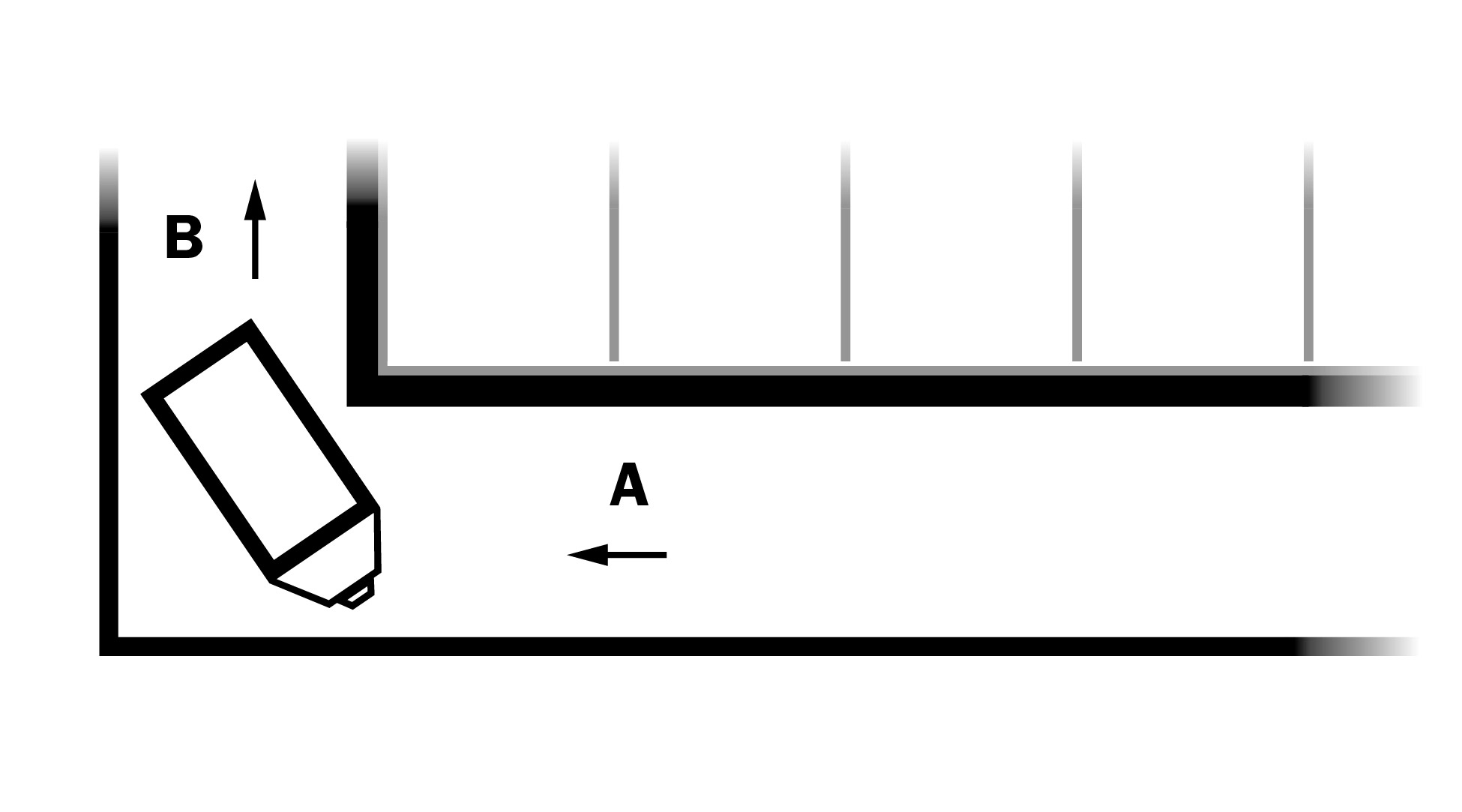
A new feed room may be necessary, possibly located next to the silos. Another option is to convey feed across the barn to a building. Locating a feed room separate from other buildings will allow for room to expand. Give some consideration to the environment of the room to provide comfortable working conditions.
Feed delivery
Plan equipment for moving ingredients to the mixer and conveying the final product away from it efficiently. Match equipment capacity to the other equipment in the system. Equipment for moving mixed feed towards the sheep must be capable of conveying feed faster than the unloading equipment or mixer can deliver it.
Feed carts and loader buckets
Powered feed carts are popular as an alternative to conveyors (Figure 2). The cost of transferring the ration can be reduced by using a feed cart to deliver the feed to remote sites where conveyors can't reach or would be too expensive to install. Choose a feed cart that can deliver the ration efficiently and will fit into the alley of the barn. Table 5 shows workable feed alley combinations for different feed cart sizes. Check with suppliers for more exact information. A loader bucket can be equipped with a "live" bottom to function much like a feed cart, while using existing tractors or skid-steer loaders.
Some producers are using TMR feed carts equipped with scales and mixing equipment. These carts serve a dual purpose, by mixing and delivering the ration. However, their capacity is relatively small and it is harder to get a high-quality of mix with these carts.
Feed cart capacity | Feed cart dimensions | Alley width A | Alley width B |
---|---|---|---|
0.57 m3 (20 ft3) (25 bu) | 193 cm x 76 cm (76 in. x 30 in.) | 96 cm (38 in.) | 142 cm (56 in.) |
0.57 m3 (20 ft3) (25 bu) | 193 cm x 76 cm (76 in. x 30 in.) | 106 cm (42 in.) | 132 cm (52 in.) |
0.57 m3 (20 ft3) (25 bu) | 193 cm x 76 cm (76 in. x 30 in.) | 116 cm (46 in.) | 121 cm (48 in.) |
0.68 m3 (24 ft3) (30 bu) | 198 cm x 83 cm (78 in. x 33 in.) | 101 cm (40 in.) | 152 cm (60 in.) |
0.68 m3 (24 ft3) (30 bu) | 198 cm x 83 cm (78 in. x 33 in.) | 106 cm (42 in.) | 139 cm (55 in.) |
0.68 m3 (24 ft3) (30 bu) | 198 cm x 83 cm (78 in. x 33 in.) | 121 cm (48 in.) | 121 cm (48 in.) |
0.91 m3 (32 ft3) (40 bu) | 213 cm x 96 cm (84 in. x 38 in.) | 106 cm (42 in.) | 182 cm (72 in.) |
0.91 m3 (32 ft3) (40 bu) | 213 cm x 96 cm (84 in. x 38 in.) | 121 cm (48 in.) | 152 cm (60 in.) |
0.91 m3 (32 ft3) (40 bu) | 213 cm x 96 cm (84 in. x 38 in.) | 132 cm (52 in.) | 132 cm (52 in.) |
1.36 m3 (48 ft3) (60 bu) | 254 cm x 114 cm (100 in. x 45 in.) | 147 cm (58 in.) | 193 cm (76 in.) |
1.36 m3 (48 ft3) (60 bu) | 254 cm x 114 cm (100 in. x 45 in.) | 162 cm (64 in.) | 182 cm (72 in.) |
1.36 m3 (48 ft3) (60 bu) | 254 cm x 114 cm (100 in. x 45 in.) | 177 cm (70 in.) | 177 cm (70 in.) |
Conveyors
Belt conveyors have high capacity and are commonly used to transport silage from upright silos to the mixer; they can also be used for feed delivery. Texture belts can elevate feed at an incline, but their capacity is reduced, and feed may roll back off the conveyor. Chain and flight conveyors are generally lower capacity than the belt conveyors but can elevate feed over relatively short distances at a steeper incline.
Management changes
A well-managed TMR system means more production from your flock. Higher-producing ewes eat more feed, produce more manure and require better living space. So housing, ventilation, feeding, watering and manure handling systems must be capable of meeting these increased needs.
Key changes:
- ration balance points must be determined
- TMR means feeding ewes as a large management group, not as individuals or pens
- accurate mixing requires frequent moisture testing of forages
- ration formulation frequency may increase with TMR
A TMR system won't necessarily decrease labour hours. The increase or decrease in labour is very dependent on the previous feeding practices and the layout of the equipment in the feeding system. To obtain the maximum benefits from TMR feeding, grouping strategies and culling strategies may also have to change.
TMR feeding is not for everybody. You must carefully weigh the costs of the system against the benefits you expect to gain on your particular farm. There may be other changes that will produce quicker and more significant results. If you conclude that it is the way to go, plan your system carefully. Switching to a TMR feeding system will require major capital expenditures. Careful planning in the beginning will determine the degree of success in the long run.
Reference
House, H.K. 1991. Feeding Equipment for Total Mixed Rations. Ontario Ministry of Agriculture, Food and Rural Affairs, Clinton.
Wand, C. 2006. On farm calculations. Not published.
Wheeler, B. 1995. Total Mixed Rations and Computerized Concentrate Feeders. Ontario Ministry of Agriculture, Food and Rural Affairs, Kemptville.
This factsheet was written by Christoph Wand, Beef Cattle, Sheep and Goat Nutritionist, OMAFRA, Guelph
Footnotes
- footnote[i] Back to paragraph House, H.K. 1991. Feeding Equipment for Total Mixed Rations. Ontario Ministry of Agriculture, Food and Rural Affairs, Clinton.
- footnote[ii] Back to paragraph Wand, C. 2006. On farm calculations. Not published.