
Important: This version of the e-Laws website will be upgraded to a new version in the coming weeks.
You can try the beta version of the new e-Laws at ontario.ca/laws-beta.
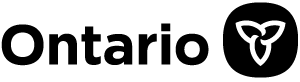
R.R.O. 1990, Reg. 1076: REFRIGERATION AND AIR-CONDITIONING MECHANIC
under Trades Qualification and Apprenticeship Act, R.S.O. 1990, c. T.17
Skip to contentrevoked or spent April 1, 2005 | |
March 4, 2005 – March 31, 2005 | |
April 1, 1999 – March 3, 2005 |
Trades Qualification and Apprenticeship Act
Loi sur la qualification professionnelle et l’apprentissage des gens de métier
R.R.O. 1990, REGULATION 1076
Amended to O. Reg. 141/99
REFRIGERATION AND AIR-CONDITIONING MECHANIC
Historical version for the period April 1, 1999 to March 3, 2005.
This Regulation is made in English only.
1. In this Regulation,
“certified trade” means the trade of refrigeration and air-conditioning mechanic;
“refrigeration and air-conditioning mechanic” means a person who,
(a) lays out, assembles, installs, maintains in the field any cooling or heating-cooling combination system for residential, commercial or industrial purposes within the limitation of the Energy Act,
(b) installs or connects piping for the purpose of conveying refrigerant of all types for either primary or secondary cooling,
(c) overhauls or repairs any equipment used in a refrigeration or air-conditioning system, and
(d) tests, adjusts, maintains all controls on refrigeration or air-conditioning systems including air-balancing,
but does not include a person who is engaged in the repair or installation of single-phase hermetically sealed domestic self-contained units with factory mass-produced systems precharged with refrigerant, or a person employed in production commonly known as mass production. R.R.O. 1990, Reg. 1076, s. 1.
2. The trade of refrigeration and air-conditioning mechanic is designated as a certified trade for the purposes of the Act. R.R.O. 1990, Reg. 1076, s. 2.
3. An apprentice training program is established for the certified trade and consists of five periods of related training and work experience training of 1,800 hours for each period,
(a) at full time educational day classes provided at a college of applied arts and technology or in courses that in the opinion of the Director are equivalent thereto in the subjects contained in Schedule 1; and
(b) in practical training and instruction provided by the employer of the apprentice in the subjects contained in Schedule 2. R.R.O. 1990, Reg. 1076, s. 3.
4. The subjects of examination for an apprentice in the certified trade are the subjects contained in Schedules 1 and 2. R.R.O. 1990, Reg. 1076, s. 4.
5. The rate of wages for an apprentice in the certified trade, whether for the apprentice’s regular daily hours of work or for hours of work in excess of the apprentice’s regular daily hours of work shall not be less than,
(a) 40 per cent during the first period;
(b) 50 per cent during the second period;
(c) 60 per cent during the third period;
(d) 70 per cent during the fourth period; and
(e) 80 per cent during the fifth period,
of the average hourly rate of wages or its equivalent for journeymen in that trade employed by the employer with whom the apprentice is working. R.R.O. 1990, Reg. 1076, s. 5.
6. The number of apprentices who may be employed by an employer in the certified trade shall not exceed,
(a) where the employer is a journeyman in the trade, one apprentice plus an additional apprentice for each three journeymen in the trade employed by that employer;
(b) where the employer is not a journeyman in the trade, one apprentice for the first journeyman in the trade employed by the employer plus an additional apprentice for each additional three journeymen in the trade employed by that employer. R.R.O. 1990, Reg. 1076, s. 6.
7. Any person who,
(a) applies in the prescribed form for apprenticeship in the certified trade; and
(b) works in that trade for three months or less,
is exempt from subsection 10 (2) of the Act. R.R.O. 1990, Reg. 1076, s. 7.
8. The Director shall issue a progress record book to each apprentice and the apprentice shall record therein the time that the apprentice spends in related training and work experience and the apprentice shall be responsible for the safekeeping of that progress record book. R.R.O. 1990, Reg. 1076, s. 8.
9. An applicant for a certificate of qualification in the certified trade shall submit to the Director evidence satisfactory to the Director of,
(a) the applicant’s successful completion of the apprenticeship training program described in section 3; or
(b) the applicant’s engagement in the certified trade as a journeyman for a period at least equivalent to the total number of hours of which the apprenticeship training program consists. R.R.O. 1990, Reg. 1076, s. 9.
SCHEDULE 1
REFRIGERATION AND AIR-CONDITIONING MECHANIC
In-School Training
Item |
Column 1 |
Column 2 |
Column 3 |
Course |
Subject |
Instruction to be Given | |
1 |
Mathematics (Trade Related) |
Mathematics |
Whole numbers, fractions, mixed numbers, decimals. Linear, square and cubic measure. Area and volume calculations. Angles and degrees. Ratio and proportion. Weights and measures. Percentage and simple interest. Metric system and conversion methods. Algebra; fundamentals, linear equations, formulae, shop calculations. Slide rule use. Pipe capacities; cross sectional areas, ratio, fluid flow calculations. Estimating; units, trade unit, quantity calculations, costing principles. Inventory. Business operations; practices, payroll and wages calculations; insurance, taxes, Workers’ Compensation, wage earner’s lien. |
2 |
English Communications |
Printed, Written, and Oral Communication |
Vocabulary of the trade. Reading comprehension; use of trade publications, dictionary, library. Sentence structure, grammar, punctuation, composition. Trade related letter, memoranda writing, completion of forms, reports, job descriptions, estimates, orders. Oral communication. Good listening principles. |
3 |
Blueprint Reading |
Introduction and Interpretation |
Working drawings. Title block. Section views. Orthographic, isometric and multi-view projections. Auxiliary views. Aligned, revolved and auxiliary sections. Threads, fasteners. Dimensioning. Fits and tolerances. Surface finish. Standard architectural symbols. Schematics. Job Specifications, addendum. |
Elementary Drafting |
Tolerances. Reproduction process. Three—view drawing. Instrument use. Sections and material symbols. Dimensioning. Freehand sketching, schematics. Plan study of construction; materials, construction members, dimensioning methods, sections and details, schedules. Electrical drawings for commercial and industrial projects, electrical symbols. Schematic diagram for electric defrost system, single and multiple coil hook-up. Piping drawings; single line, double line, isometric. Pipe fabrication, piping and welding symbols. Preparation of elementary trade related working drawings, dimensioned sketches, piping systems, circuits, schematics, layouts, estimates. | ||
4 |
Safety |
General |
Safety rules and safe operating procedures. Protective clothing and equipment. First aid; refrigerant and electrical accidents, burns, artificial respiration. Ventilation. Fire prevention; types and use of extinguishers. The Occupational Health and Safety Act. The Workers’ Compensation Act. The Building Code Act. Electrical Safety Code under the Electricity Act, 1998. Handling and storage of refrigerants and oils. Safe use of lifting and hoisting equipment, electrical tools and equipment, welding equipment. Powder actuated tools. Good housekeeping. |
5 |
Trade Tools and Test Instruments |
Hand Tools |
Care and use of hammers and chisels, pliers, cutters and shears, drifts and punches. Files and reamers. Taps and dies, metal and wood saws, wrenches, drill bits (wood, metal, masonry), stud extractors, clamps and vises, pipe cutting, flaring and bending tools. |
Power Tools and Equipment |
Use, care and storage of portable electric drills and hammers. Pipe cutting and threading machines. Grinders. Powder actuated stud guns. Jacks and hoists, cranes, slings, pulleys. | ||
Test Instruments |
Use, care and storage of hydrometers, salometers, pressure and vacuum gauges, dry and wet bulb thermometers, electrical meters, stroboscope, stop watch. Fluid and gaseous flow meters. Leak detection devices; use of halide leak detectors, electronic leak detectors, soap test, litmus paper, sulphur stick. | ||
Measuring Tools |
Care and use of rules, squares and protractors. Calipers and feeler gauges. Levels. Micrometers. Plumb bobs. Chalk lines. | ||
6 |
Elements of Refrigeration |
Refrigeration |
Evolution. Definition and description. Applications for cooling, preserving. Trade terminology. |
Applied Physics |
Heat (cold); kinds of heat, sensible, latent, fusion, vaporization, sublimation, specific, super heat. Kinetic theory of heat; heat effects of bodies, change of state, volume. Vaporization, condensation, fusion, solidification, sublimation. Saturated and superheated vapour. Temperature and pressure relationship. Temperature; indicating instruments, scales, scale conversion, thermometer types and installation. Heat transfer; flow laws, conduction, convection, radiation. Units of measurement; British Thermal Unit, ton of refrigeration, specific heat. Pressure; atmospheric and absolute, indicating instruments, pressure and vacuum gauges. Fluid flow; friction, velocity, cause of flow, total pressure, units of measure. Properties of matter; gravity, density, saturation. Chemical and physical properties of air and water. Elements of energy; kinds, work and horsepower, heat, molecular energy. Gas laws; Dalton’s Law, Boyle’s Law, Charle’s Law. General Gas Law. Thermodynamic properties; pressure, temperature, volume, density, enthalpy, entropy. | ||
Basic Refrigeration Cycle |
Open cycle; water canteen, refrigerant drum. Closed cycle; basic essentials—compressor, evaporator, condenser, metering device. Compression cycle; operation and schematics, system components, refrigerant cycle. | ||
Basic Automatic Cycle Controls |
Control by thermostat (temperature), pressurestat (pressure), humidistat (moisture, humidity). Expansion in liquids, solids, vapours. Pressure drop across expansion valves, accessories. | ||
Multiple Systems |
Parallel evaporators. Control methods. Parallel compressors. Piping methods. | ||
Codes and Regulations |
Refrigeration systems and building occupancy classifications. Requirements for institutional, public, residential and commercial installations. Refrigerant piping and pressure vessels, pressure relief devices, valves, fittings, thread lubricants and sealers. | ||
7 |
Piping in Refrigeration Systems |
Piping Principles |
Identification and application of piping types; iron, plastic, copper, brass, steel and related fittings. |
Pipe Work |
Copper; cutting, flaring, swaging and bending procedures. Iron; cutting, threading, making of proper joints (coupled, flanged, welded). Plastic; cutting, joining. Steel; cutting, reaming, threading, bending, hanging. | ||
Hangers and Support |
Installation of pipe hangers. Cutting and threading rod hangers. Installing hangers in concrete, steel and wood. Hanging pipe and tubing, riser supports. Common problems; causes, elimination. Making up piping and fittings for commercial hook-ups. Applicable codes and regulations. | ||
Insulations |
Insulating materials; Types and methods of fitting. Insulating lines (liquid, suction). | ||
Piping Practices |
Allowable velocities. Pressure drop. Oil return. Compressor protection. Sizing of suction lines, liquid lines, hot gas risers. Use of refrigerant piping charts. System design. | ||
Piping |
Liquid, suction, hot gas discharge, condensate. Double risers, “P” traps. Multiple compressors, multiple evaporators, remote condensers. Primary and secondary systems. Refrigerant lines; high pressure, low pressure. | ||
8 |
Refrigerants and Oils |
Refrigerants |
Requirements. Thermodynamic properties. Physical properties. Classification and types; primary, secondary. Operational procedures. Leak detection methods for different types. Testing for contamination of refrigerant. Refrigerant cylinder filling methods. Toxicity, flammability and explosive hazards. Number designation of refrigerants. |
Oils and Lubricants |
Types. Characteristics. Properties and proper applications. | ||
9 |
Compression Cycle |
Vapour Compression Cycle |
Definition and description. Various systems. Dense air. Vapour compression. Absorption system. Control methods. |
Systems |
Low side and high side float systems. Capillary control. Direct expansion system; constant pressure, constant super heat. Principles of operation. Construction. Control and adjustment methods. Advantages and disadvantages. Applications. | ||
Condensing Units |
Types. Applications. General installation data. Cascade systems. | ||
Hermetically Sealed Units |
Description. Construction differences. Installation requirements. Applications. | ||
10 |
Compressors |
Basics |
Principles and general operation. Function in the system. Compressor seals. Capacity. Piston displacement, volumetric efficiency, compression ratio. Power sources. Lubrication. |
Compressor Types |
Common types and selection for type of refrigeration system application. | ||
Reciprocating; open, semi-hermetic, welded hermetic, vertical, V and W, for halocarbon or halogenated hydrocarbon and ammonia, double acting. 2 stage compressors and booster. Rotary; accessible, open and hermetic, domestic, ammonia. Centrifugal (halocarbon or halogenated hydrocarbon and ammonia). Screw type. | |||
Capacity Control |
Control methods. Cylinder unloading. Hot-gas bypass. Multiple compressors. Solenoid valve control (hot-gas and evaporator). Vane and speed controls. | ||
Installation |
Checking compressor and equipment received. Erection methods. Piping connections. Driver alignment and control connections. | ||
Absorption Machines |
Types of absorption systems, function of generators, absorbers, condensers, evaporators. Installation methods. Care in handling. | ||
Maintenance |
Procedures for replacing hermetic compressor. Replacing motor compressor system, valve plates, seals. Dis-assembly, inspection, overhaul and re-assembly of reciprocating and rotary compressors. Clean-up procedures (burn-out). | ||
11 |
Condensers and Receivers |
Condenser Types |
Description, purpose and function in system. Applications. Air cooled, water cooled, combination, evaporation. Auxiliary. Shell and tube condenser receivers. Construction materials. Controls and safety devices; pressure, temperature and humidity. Relevant codes. Freeze protection. |
Components and Operation |
Heat transfer. Piping and pumps. Cooling towers. | ||
Installation and Servicing |
Space requirements. Methods of mounting and installing condensers and cooling towers. Piping connections. Servicing procedures. Start-up. Closedown. Cleaning, water treatment, draining, flushing. Winter operation. | ||
12 |
Evaporators |
Principles |
Purpose and function in system. Air coolers (coils). Liquid coolers. Defrost systems. |
Design and Operation |
Circuiting. Direct expansion coils. Humidity. Defrost methods; electrical, thermo bank, reversing valves. Multiple coils. Capacities, coil temperature control. Air circulation effects on product, humidity, capacity. Applications for beer, soda, water coolers. | ||
Evaporation (temperature difference) |
Definition. Proper coil selection factors. Capacity and temperature difference relationship. | ||
Installation |
Evaporator selection and sizing factors. Valve selection. Space requirements. Mounting methods. Piping connections. Servicing procedures. | ||
13 |
Metering Devices |
Operating Principles and Types |
Definition and theory, Importance to system. Hand operated, thermostatic and automatic expansion valves. Capillary tube. Low side float. High side float. Applications. Selection factors. Operation; pressures, control. |
14 |
Evacuation |
Principles |
Reason for evacuation (air, moisture). Vacuum pump theory, inches of mercury, microns. |
Methods |
Evacuation by air; single by vacuum pump, double by vacuum pump, heat. Evacuation of moisture; dehydration by vacuum pump and by desiccants. | ||
15 |
Accessories |
Types and Function |
Characteristics and function in system. Dehydrators and desiccants. Liquid indicators. Suction line filters. Check, two-temperature and water regulating valves. Heat exchangers. Oil separators. Mufflers. Vibration eliminators. Accumulators. Head pressure control (low ambient conditions with roofmounted air cooled condensers.) |
16 |
Electrical Systems |
Basic Theory |
Current flow. Voltage. Resistance. Ohm’s Law. Measurement and use of test equipment; voltmeter, ammeter, ohmmeter, wattmeter, test fuses. Magnetism and solenoids. E.M.F. AC and DC. Generators and motors (single and poly-phase). Transformer principle. Batteries. Electrical safety practices. Relevant codes and standards. Safe operating procedures. |
Controls and Components |
Control circuitry; starter circuits, control circuits. Start and run capacitors, relays, magnetic starters, contactors. Circuit protective devices. Transformers. Low voltage control system. Control circuit testing. Motor types, testing and direction reversing procedures. Capacitor capacitance formula. Multiple capacitor connections. | ||
Wiring Diagrams |
Interpretation of installation, label (or line) and schematic wiring diagrams and symbols. | ||
Installation |
Procedures for installation, connecting and testing of electrical circuits, controls and components for commercial refrigeration systems. Trouble shooting electrical faults. Use of electrical and mechanical test instruments. | ||
17 |
Controls and Control Circuitry |
Fundamentals of Control |
Purpose, function and types of control circuits and control devices in commercial refrigeration systems. Electric, pneumatic and electronic types. Primary and secondary categories. Control devices; controllers (thermostats, humidistats, pressure type switches). Controlled devices; automatic valves, valve operations, automatic dampers, damper operations, electrical heaters, meters, contactors, starters. Auxiliaries; transformers, relays, potentiometers, manual switches, clocks or timers. Components used in controls and circuits. Capacity and distribution control systems. |
Fundamentals of Measurement |
Temperature; primary elements, heating, cooling. Relative humidity; humidistats or hygrostats, sensing elements, controlled devices. | ||
18 |
Commercial Load Calculation |
Heat Transmission (Sensible) |
Conduction; walls, ceilings, floors. Time. Insulation type and thickness. External area. Temperature difference. Radiation; glass, other materials. Heat gains (“U” factor). Solar. Air change; inside volume, types of usage. Product. Miscellaneous factors; people, lights, motors, appliances (gas or electric). |
Load Estimation |
Estimating methods and forms used. Selection and locating factors for; coolers, compressors, condensers and receivers, piping, controls and accessories. Chart use. | ||
19 |
Installations and Start-up |
Main Components |
Installation procedures for self-contained units, compressors, condensers and receivers. Evaporators, tubing and piping, control devices and accessories. Fitting gauges and test instruments. |
Large Commercial Systems |
Design considerations and major factors. Low temperature food warehouses (long term storage). High temperature, short term food storage. Chain store applications. Packaged equipment. Industrial applications for dairies, breweries, meat packing plants. Skating and curling rinks. Test facilities and special equipment. Pumping systems. Water chillers (reciprocating, centrifugal, absorption). Cooling towers. Defrost methods. Self-contained air conditioners. Heat pumps. Air handling units. Direct and indirect coolers. | ||
Initial Start-up |
Evacuation, charging and purging procedures. Operational checks; leak test, charge, position valves, belts, oil, power source. Safe operating procedures, safety devices. Hazards and malfunctions. | ||
20 |
Service Problems |
Trouble Shooting |
Principles, procedures and techniques. Common component malfunctions and symptoms; condensers and receivers, evaporators, compressors, basic cycle controls, accessories, metering devices. Electrical systems; load and control circuits. Use of wiring diagrams, and design conditions. |
Inspection and Servicing |
Systematic detection of malfunctions, identification and corrective repairs or adjustments. Personal and equipment safety protection. Periodic preventive maintenance inspections. | ||
21 |
Welding (Oxyacetylene) |
General |
Welding terminology. Oxyacetylene equipment and processes. Hazards and safety precautions. Protective clothing and equipment. Welding and brazing rods, fluxes. Basic weld joints. Material cleaning and preparation. Weld and torch cutting faults. Weld testing procedures. |
Welding, Cutting, Brazing |
Equipment handling, set-up and operation; regulated pressures, tip sizes, flame types, purpose and adjustment. Flat and horizontal position fusion and braze welding. Manual torch cutting. Use of brazing, brazing alloys, silver solder, and soft solder for making joints. | ||
22 |
Air Conditioning |
General Principles |
Air and human comfort factors. Filters, fans, ducts, grilles, air balancing, types and layout of systems, noise levels. Effects of humidity, heating and cooling the air. Load analysis and calculation. |
Air Circulation |
Return and outside air. Duct systems. Static pressure. Total pressure. Inches of water column. Ventilating systems; equipment required, location and applications. | ||
Air Cooling and Heating Systems |
Description. Equipment required. Location. Means of cooling and heating. Types of air distribution. Controls required. Year-round systems; function, mechanical operation, psychrometric charts. Equipment. Controls. Trouble shooting and servicing. | ||
Air Cleaning Equipment |
Filters; viscous and dry types. Filter bank installation, checking and cleaning procedures. Electrostatic air filters; component assembly, starting, operating, cleaning and maintenance procedures. | ||
Air Distribution |
Checking duct system. Setting and adjustment of registers, grilles, venting dampers, supply air diffusers. Adjustment of direct discharge (package free-blow units), induction units and high velocity mixing boxes. Adjustment and balancing of air volume. Setting open and closed exhaust hoods. Room C.F.M. Air movement F.P.M. Humidifying and de-humidifying equipment; spray and wetted surface types, evaporators. Service requirements. | ||
Design Factors |
Duct sizes for given total C.F.M. Duct system layout including fresh air. Register sizes and number per room. Air flow measurement. Dry expansion chillers; operation, selection, C.F.M., condenser water G.P.M., heat rejection factors. Window installations. Packaged equipment. Remote self-contained and central station equipment. | ||
Automatic Control Systems |
Pneumatic, electric, electronic, fluidic types. Installation procedures. | ||
23 |
Psychrometrics |
Properties of Air |
Relationship to air conditioning systems design and operation. Ventilation requirements. Evaporative cooling. Air mixture. Return air and outdoor air. Winter and summer air treatment passing through plenum. |
Calculations |
Air and humidity calculations. Use of psychrometric charts, sling and aspirating psychrometers. | ||
24 |
Air Handling and Distribution Equipment |
Components |
Fans and blowers. Filter devices. Humidification and de-humidification equipment. Diffusers, grilles, registers. Ductwork. Dampers. Fan coil units; types, features and limitations, controls. |
System Variations |
Single and multi-zone units; all-air and air-water induction systems, central station apparatus, piping. | ||
Air System Balancing |
Air flow balancing methods. Use of air measuring instruments. System adjustments and control. | ||
Maintenance |
Maintenance cycles and procedures. | ||
25 |
Air Conditioning Equipment |
Selection Factors |
Equipment types, domestic and commercial applications. Use of manufacturers charts. Packaged equipment. Heat pumps. Water chillers. Absorption equipment. Pumps; water, glycol, brines and ammonia types. |
R.R.O. 1990, Reg. 1076, Sched. 1; O. Reg. 141/99, s. 1.
SCHEDULE 2
REFRIGERATION AND AIR-CONDITIONING MECHANIC
Work Experience Training
Item |
Column 1 |
Column 2 |
Column 3 |
Course |
Subject |
Work Experience Training | |
1 |
Trade Practices (As Detailed in Schedule 1) |
General |
Safety rules and removal of all hazards. The Occupational Health and Safety Act. The Workers’ Compensation Act. The Building Code Act. Electrical Safety Code under the Electricity Act, 1998. Care and use of hand and power tools and equipment, test instruments, measuring tools. Pipe work; cutting, reaming, threading, flaring, swaging and bending. Making and fitting joints. Welding, brazing, torch cutting and soldering. |
2 |
Refrigeration Systems |
General |
Familiarization with basic refrigeration cycle, automatic cycle controls, multiple systems. Requirements for institutional, public, residential and commercial installations. Applicable codes and regulations. |
Pipe Work |
Familiarization with piping types, practice and applications. Use of refrigerant piping charts. Sizing and installing piping and fittings for liquid, suction, hot gas discharge, condensate lines. Primary and secondary systems, high and low pressure refrigerant lines. Making up and installing pipe hangers, hanging pipe and tubing, insulating lines. | ||
Refrigerants, Oils and Lubricants |
Familiarization with properties, types, classification and usage. Leak detection. Refrigerant contamination tests. Filling refrigerant cylinders. Hazards and safety precautions. | ||
Compressors |
Familiarization with principles, types, general operation. Selection and installation of reciprocating, rotary, centrifugal, screw type compressors, 2 stage compressors and booster. Erection operations. Piping connections. Driver alignment and control connections. Installation of absorption equipment. | ||
(Maintenance) |
Replacing hermetic compressor. Clean-up after burnout. Replacing motor compressor system, valve plates, seals. Dis-assembly, inspection, overhaul and re-assembly of reciprocating and rotary compressors. Lubrication. | ||
Condensers and Receivers |
Familiarization with principles, types, function. Relevant codes. Mounting and installing condensers and cooling towers. Piping connections. Start-up and close-down operations. Servicing; cleaning, water treatment, draining, flushing. Winter operation. | ||
Evaporators |
Familiarization with principles, types, and function; air coolers (coils), liquid coolers, defrost systems. Installation; evaporator selection and sizing, valve selection, mounting operations. Piping connections. Servicing. | ||
Metering Devices |
Familiarization with operating principles and types. Selection and installation of hand operated, thermostatic and automatic expansion valves, capillary tubes, high and low side float. | ||
Accessories |
Function and installation of de-hydrators and desiccants. Liquid indicators. Suction line filters. Check, two-temperature and water regulating valves. Mufflers. Heat exchangers, oil separators. Vibration eliminators. Accumulators. | ||
Electrical Systems |
Familiarization with basic electrical theory. Safety practices and operating procedures. Relevant codes and standards. Installation, connecting and testing of electrical circuits, controls and components for commercial refrigeration systems. Use of wiring diagrams. Trouble shooting electrical faults. | ||
Controls and Circuitry |
Familiarization with control fundamentals and measurement. Installation of control circuits, fluidic, electric, pneumatic and electronic, primary and secondary control and controlled devices. Capacity and distribution control systems. Trouble shooting controls and circuitry. | ||
Commercial Refrigeration Systems |
Familiarization with heat transmission principles and factors. Commercial load calculations and estimates. Selection and location of coolers, compressors, condensers and receivers, piping, controls and accessories. | ||
(Installation) |
Large commercial systems; low temperature food warehouses (long term storage), high temperature, short term food storage. Chain store applications. Packaged equipment. Industrial applications for dairies, breweries, meat packing plants. Skating and curling rinks. Pumping systems. Water chillers. Cooling towers. Defrost systems. Self-contained air conditioners. Heat pumps. Air handling units. Direct and indirect coolers. Multiplex systems. | ||
(Initial Start-up) |
Safe operating procedures and safety devices. Fitting gauges and test instruments. Evacuation, charging and purging. Operational checks. | ||
(Trouble Shooting and Maintenance) |
Systematic detection of malfunctions, identification and corrective repairs or adjustments. Periodic maintenance inspections. | ||
3 |
Air Conditioning Systems |
General |
Familiarization with principles. Load analysis and calculation. Design factors for duct sizes, duct system layout, registers. Air flow measurement. Psychrometrics. Air and humidity calculations. |
Equipment Selection |
Equipment types for domestic and commercial applications. Use of manufacturers charts. Packaged equipment. Heat pumps. Water chillers. Absorption equipment. Pumps; water, glycol, brines and ammonia types. Free cooling. | ||
Installation |
Single and multi-zone units; all-air and air-water induction systems, piping. Window installations. Packaged equipment. Remote self-contained and central station equipment. Fans and blowers. Filter devices. Humidification and de-humidification equipment. Diffusers, grilles, registers. Ductwork. Dampers. Fan coil units. Pneumatic, electric and electronic, fluidic and automatic control systems. Air flow balancing. Use of air measuring instruments. System adjustments and control. | ||
Servicing |
Trouble shooting. Servicing, repairs. Periodic maintenance inspections. |
R.R.O. 1990, Reg. 1076, Sched. 2; O. Reg. 141/99, s. 2.