Building temporary stairs on construction projects
Use this compliance guidance to help meet requirements for temporary stairs at construction project sites.
Overview
Temporary stairs are often installed on construction projects before permanent stairs. If you don’t properly design or install temporary stairs, a worker can fall or the stairs can collapse.
This page provides employers with:
- information about temporary stairs requirements on a worksite
- design and installation guidance to help follow the law
- non-mandatory best practices which may be helpful to consider
The information on this page is not:
- an all-inclusive list of hazards and controls
- replacing the Occupational Health and Safety Act (OHSA) and its regulations
- meant to be used as or considered legal advice
Health and safety inspectors apply the law based on the facts in the workplace. You can find more information about the duties of employers and other persons in the guide to the OHSA.
If you need more information about safety requirements, please contact the Ministry of Labour, Training and Skills Development’s Health and Safety Contact Centre at:
Toll-free: 1-877-202-0008 , Monday to Friday, from 8:30 a.m. to 5 p.m.- webohs@ontario.ca
Why temporary stairs are important
Between 2009 and 2019, 147 people in Ontario died as a result of falls at work. Inappropriate use of ladders contributed to many falls on construction projects.
You can help prevent falls on temporary stairs with the proper:
- design and installation
- maintenance
- use
The law
The OHSA sets out the rights and duties of all parties in the workplace and procedures for dealing with workplace hazards. The employer has the greatest responsibilities with respect to health and safety in the workplace and must take every precaution reasonable in the circumstances for the protection of a worker.
Ontario Regulation 213/91, Construction Projects under the OHSA contains important laws about temporary stairs, including:
- the design, installation, and use of temporary stairs in sections 75 to 77
- requirements for access and emergency evacuation in sections 17, 70 and 71
- guardrail specification requirements in section 26.3
- supervisor’s responsibilities for inspection in section 14
The regulation provides minimum standards an employer must follow to keep everyone on a worksite safe.
You may also want to review the requirements under the Ontario Building Code and the Ontario Fire Code.
General installation principles
Exceptions
When you build a structure with more than one level, you must have temporary stairs between levels as construction progresses.
Temporary stairs are not required when:
- you are only building structural beams or columns
- you attach a permanent ladder to a structure before you raise the structure into position
- you erect formwork or falsework to a suspended slab
If there isn’t enough space to install temporary stairs when formwork or falsework is in place to support the new floor above, you can use a ladder until you remove the forms.
Start and end of stairs
Temporary stairs must start on the lowest level of a structure, including the basement. As the construction progresses, the stairs should go up to the highest work level, unless it interferes with the work there. In that case, you need temporary stairs up until two storeys or nine metres below the highest work level, whichever distance is shorter.
Materials
Compressed wood is not suitable to connect the stairs. Compressed wood, including Aspenite and oriented strand board (OSB), can crack under pressure. It is important to pick adequate lumber that does not crack when you drive nails into it.
How to install
Tailor the temporary stairs to the needs of your site because every worksite is different. The below illustrations show installation best practices, however, they will vary with the site of the stairs.
Example 1
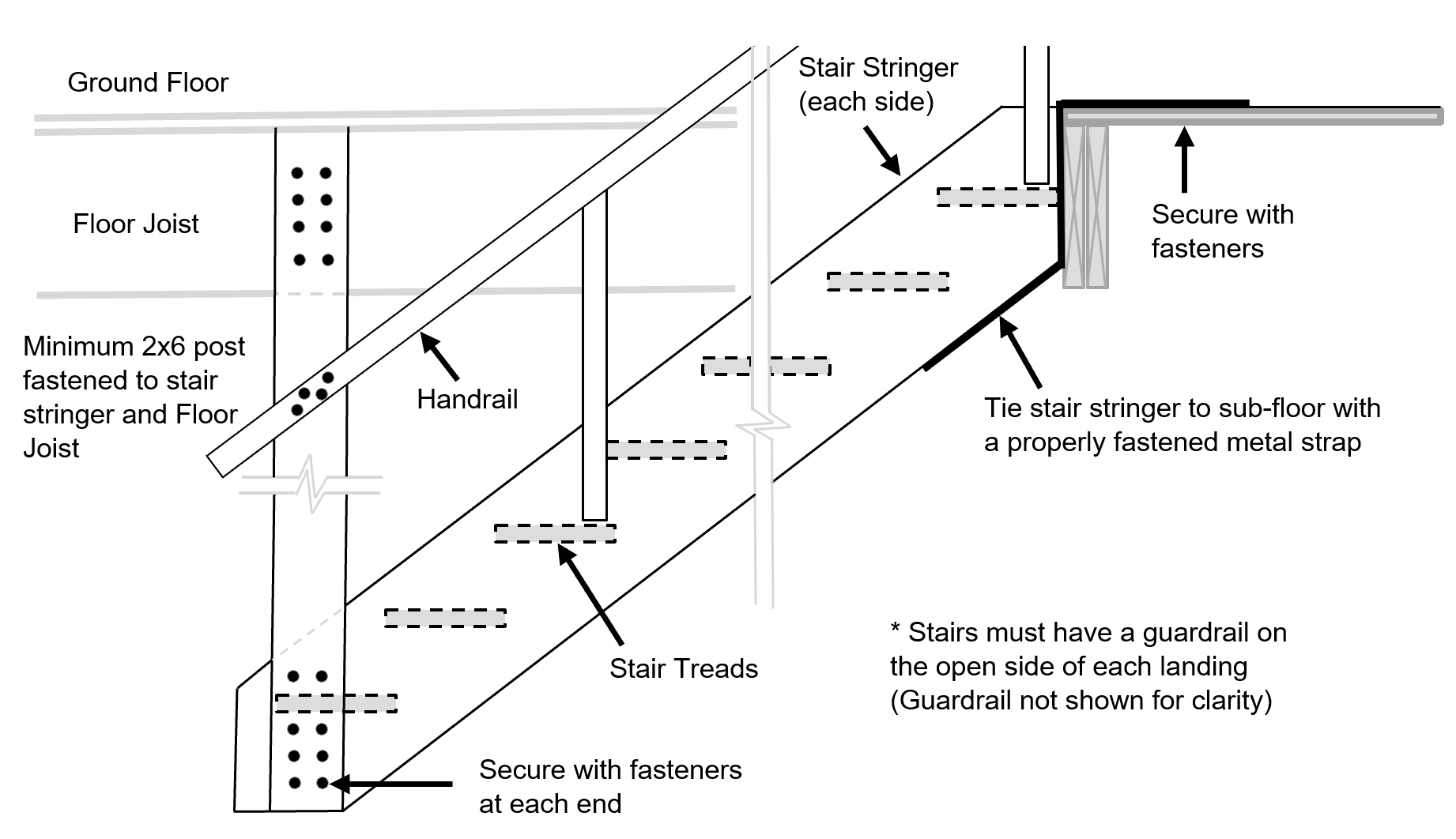
Diagram of temporary stairs connecting the basement to the ground floor. The top of the stair stringer is tied to the subfloor with a metal strap. The bottom of the stair stringer is fastened to a 2 by 6 post fastened to the floor joist beam. The stairs must have a handrail and guardrail on the open side of each landing.
Example 2
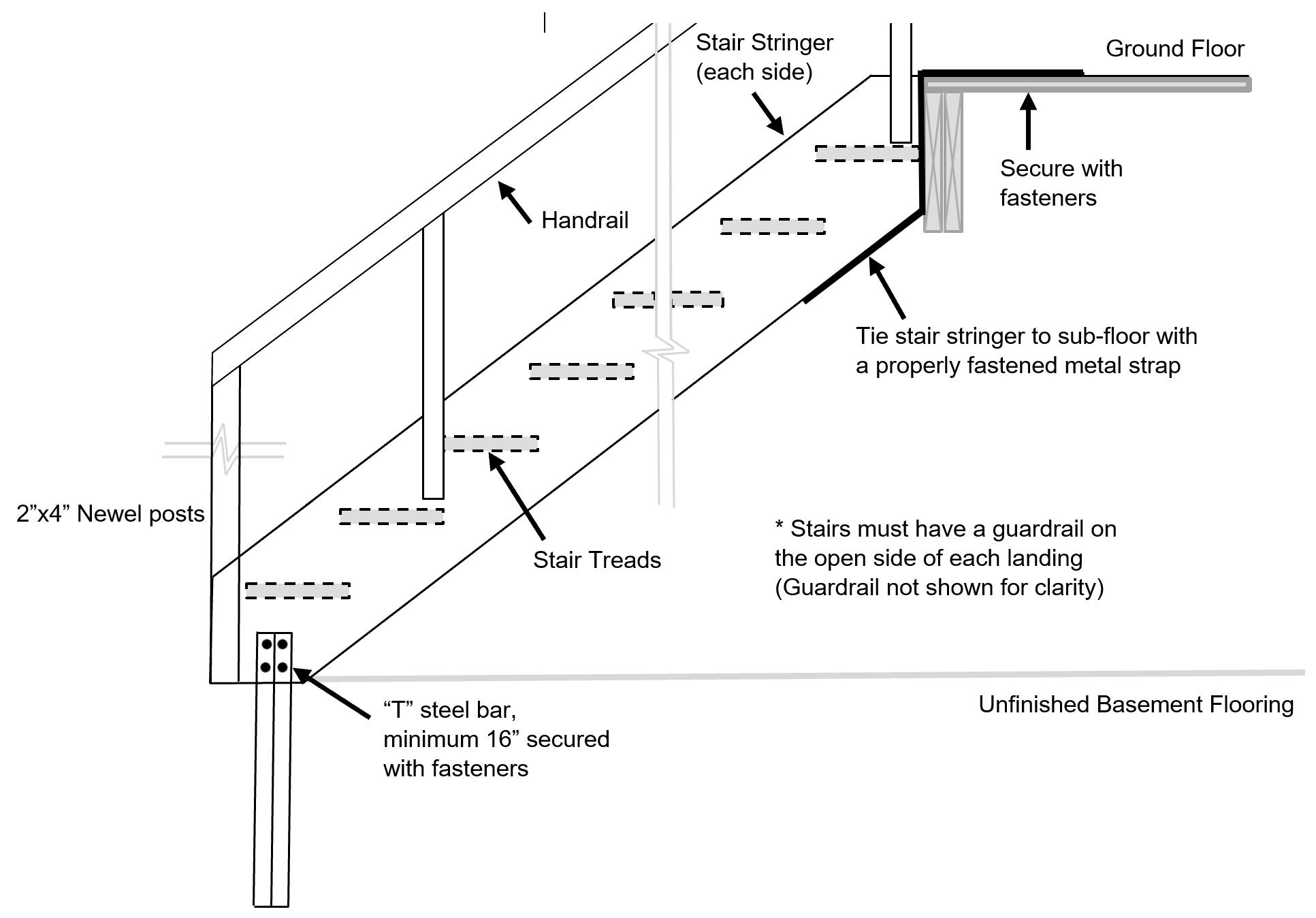
Diagram of temporary stairs connecting the unfinished basement flooring to the ground floor. The top of the stair stringer is tied to the subfloor with a metal strap. The bottom of the stair stringer is fastened to a T steel bar. The stairs must have a handrail and guardrail on the open side of each landing.
Emergency
When you lift the stairs, a ramp, runway or ladder must be available for emergency evacuation. There must be someone who can install the ramp or ladder at all times. Workers need to know where to find the ramp or ladder and how to secure it properly.
You can find other general emergency provisions in section 17, 70, and 71 of Ontario Regulation 213/91, Construction Projects.
Specific design guideline
Load bearing
Consider different stages of your project, and make sure the stairs can support the heaviest load that you anticipate. The regulation requires minimum live load of 4.8 kilonewtons per square metre, or 100 pounds per square foot.
We encourage you to seek advice from a professional engineer to meet minimum load bearing requirements.
Slope
Stairs that are too steep can be dangerous. The maximum slope of the stringers is 50 degrees and the ideal slope is between 30 and 35 degrees. There is an exception for prefabricated stairs built inside a tower formed by scaffold frame. These can have a maximum slope of 60 degrees.
Stair slope
- 20 degrees to 30 degrees is acceptable
- 30 degrees to 35 degrees is ideal
- 35 degrees to 50 degrees is acceptable
Width
Temporary stairs must be at least 500 millimetres (mm) wide. You may need wider stairs depending on the objects you need to move up and down the stairs. For example, you must ensure that large emergency equipment and emergency personnel can move along the stairs. Some constructors prefer a wider width to accommodate the movement of large equipment.
Uniformity and spacing
The treads and risers must have uniform width, length and height. Uneven steps can be a tripping hazard. The treads must also be level.
- run: between 235 mm (9.25”) and 355 mm (14”), between successive steps
- rise: between 125 mm (5”) and 200 mm (7-7/8”), between successive treads
- landing: less than 4.5 metres apart measured vertically
Handrail and guardrail
Stairs must have a wooden handrail on the open sides of the stairs and a guardrail on the open side of each landing. A wooden handrail must measure 38 mm by 89 mm and be free of:
- loose knots
- sharp edges
- splinters
- shakes
You must place the top of a guardrail between 0.9 metres and 1.1 metres above the thread and ensure this distance is consistent throughout the stairs. You must fasten and support handrails and guardrails.
You can find more guidance on how to follow guardrail requirements in chapter 18 of The Infrastructure Health and Safety Association’s Construction Health and Safety Manual on Guardrails.
Safety checklist
The law requires a supervisor, or a competent person appointed by the supervisor, to inspect the temporary stairs at least once a week to ensure they are safe. It is a good practice to inspect the stairs prior to use after installation and reinstallation. Here is a list of things to look out for:
General requirements
- a qualified person designed and installed the stairs
- the workers received site-specific safety instructions for using the stairs and maintenance
- If you plan to move the stairs at some point, for example, for pouring concrete in the basement, there is a plan for emergency access and egress and trained workers responsible for the move.
Design
- The slope of the stairs is within an acceptable range (50 degrees or less).
- The width of the stairs is at least 500 mm.
- The treads and risers are of uniform width, length and height and do not create any tripping or slipping hazard.
- There is a securely fastened and supported wooden handrail on the open sides of the stairs and a guardrail on the open side of each landing.
- The stairs have enough vertical clearance.
Installation
- The stairs start in the first level of the worksite, including the basement.
- There is enough space under the stairs for pouring concrete later, if applicable.
- You secured the stairs at the top and bottom and followed proper installation guidelines.
- You made the stairs with lumber that is not easily cracked and sheared – do not use compressed wood.
- If you use skeleton steel stairs, verify that they have temporary wooden treads that are securely fastened in place and made of suitable planking that extends the full width and breadth of the stairs and landings.
Maintenance
- The stairs appear to be in good condition. For example, there is no missing steps or stringers, no rotting wood, the guardrail and handrail are free of loose knots, sharp edges, splinters and shakes.
- You aren’t storing material on the stairs that would compromise their load bearing capacity or create any tripping or slipping hazard.
- You aren’t hanging any tools or other objects on the handrail or guardrails that may compromise the integrity of the stairs.
- The stairs are not slippery – including the top, bottom and landings.
- If the stairs are not in good order, put a barricade at the top and base of the stairs with a clear sign saying, “Unsafe Stairway.”