Decommissioning on-farm biogas systems
Learn about the process for decommissioning common on-farm biogas systems and operations.
ISSN 1198-712X, Published October 2022
Introduction
This fact sheet examines the special features for decommissioning common on-farm biogas systems and operations. Figure 1 shows an on-farm biogas process flow. Consult an engineer if your biogas system has features not discussed here.
This fact sheet, together with OMAFRA fact sheet Decommissioning and/or recommissioning existing nutrient storage facilities, describes important dismantling and demolishing methods for nutrient storage tanks and transfer systems, including:
- removing organic material while addressing environmental and safety risks
- reusing or demolishing storage systems and properly managing resulting demolition materials
- removing or properly disabling material transfer systems, including underground pipes for gas or liquids
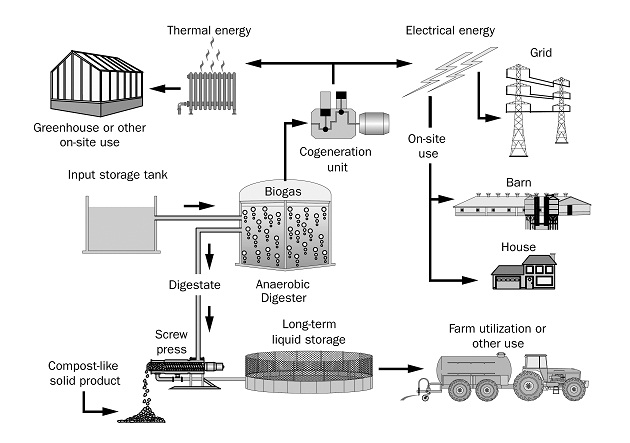
Steps to decommissioning an on-farm biogas system
The process of decommissioning a multi-part system, like a biogas system, is broken down into several steps:
- Identify and address potential safety risks
- Manage materials
- Dismantle and/or demolish structures and equipment
- Restore the site
1. Identify and address potential safety risks
Identify potential risks prior to decommissioning to help prevent potential impact on public health or the environment. When planning the decommissioning, consider the following:
- Is electrical power still connected to the system? Follow lockout procedures, ensure the power is fully shut off and that a licensed electrical contractor disconnects and handles all grid connection, high-voltage and 3-phase systems. The electrical contractor can help determine if other agencies such as the local distribution company (for example, Hydro One) or the Electrical Safety Authority (ESA) must be on-site for the decommissioning.
- Are there areas with hazardous/explosive gases? Are existing biogas-system safety alarms working and properly calibrated? If gas safety equipment is not working and gas pipes have not yet been properly decommissioned, some spaces could potentially be considered "confined spaces" that might contain a gas hazard. For more information on confined spaces, see the Ministry of Labour, Immigration, Training and Skills Development. For additional assistance with the Occupational Health and Safety Act, 1990 and worker safety, contact Workplace Safety and Prevention Services at
1-877-494-WSPS (9777) . - Are there sealed pipes or tanks, containing built-up biogas, that have not been vented? These pipes or tanks could be at very high pressure and/or contain hazardous/explosive gases. Risks occur when cutting pipes and opening valves. Licensed gas fitters, who are familiar with biogas systems, possess the equipment and knowledge to handle and dispose of these pipes. Ensure that decommissioning work conforms to Technical Standards and Safety Authority (TSSA) requirements.
- Is there a natural gas hook-up? If so, contact the natural gas distributor and work with a licensed gas fitter.
2. Manage materials
At the time of decommissioning, the biogas system may still contain a variety of input and digestate materials. An input is a material prior to any pre-treatment and digestion. Digestate is a material after pre-treatment (if necessary) and digestion. See Nutrient Management Regulation O. Reg. 267/03, as amended, for definitions of the input and digestate materials.
General precautions for pumping out liquids
Biogas systems are designed to produce and capture gas. Proceed with caution when emptying the digester vessels and other tanks to avoid encountering an explosive or toxic gas mixture.
- Agitating digester liquids could result in the release of hazardous gases such as hydrogen sulphide and create conditions that are dangerous to human health.
- Pumping out the digester contents can introduce air into the gas storage space, resulting in an oxygen/methane blend that is explosive if exposed to an ignition source. Use safe procedures around potential ignition sources such as electric motors and pumps.
- Use the biogas system's existing plumbing system to withdraw liquids.
- Ensure that all workers are aware of the precautions required for hazardous gases when working around digester vessels.
If uncertain about the risks, consult an engineer with biogas system experience to develop a safe plan for pump-out.
See the OMAFRA fact sheets, Hazardous gases on agricultural operations and Hydrogen sulphide in agricultural biogas systems for further information on managing hazardous gases.
Managing materials during decommissioning of an on-farm biogas system
Fully remove and properly manage all materials (including water used for clean-up) from the digester system when decommissioning, as described:
Input – on-farm anaerobic digestion material
- Spread material as a nutrient following the Nutrient Management Strategy or Plan (NMS/P) as per O. Reg. 267/03, if applicable.
- Follow Best Management Practices (BMPs) for managing nutrients on the farm.
- Send material to another operating biogas system (satisfy any regulatory requirements for that system).
Input – off-farm anaerobic digestion material
- Spread as a nutrient following a Non-Agricultural Source Material (NASM) Plan as per O. Reg. 267/03, if applicable.
- Return to original source.
- Dispose of at a licensed waste disposal site.
- Send to another operating biogas system (satisfy any regulatory requirements for that system).
Note: While, in some circumstances, there are regulatory exemptions when bringing these materials to the biogas system, when sending them off-farm, they are considered to be waste and should be hauled by a licensed waste hauler.
Digestate – agricultural source material
- Spread as a nutrient following the NMS/P as per O. Reg. 267/03, if applicable.
- Follow BMPs for managing nutrients on the farm.
Note: If at least half the inputs to an on-farm biogas system are "on-farm anaerobic digestion materials," and they do not contain sewage biosolids or human body waste, the digestate can be considered an "agricultural source material" for the purpose of land application.
Digestate – NASM
- Spread following a NASM Plan as per O. Reg. 267/03, if applicable.
- Dispose of at a licensed waste disposal site.
Note: While, in some circumstances, there are regulatory exemptions when bringing NASM to the biogas system, when sending them off-farm they are considered to be waste and should be hauled by a licensed waste hauler.
3. Dismantle and/or demolish structures and equipment
Dismantle and demolish on-farm biogas system structures and equipment as described:
Above-ground pipes
- Remove and reuse, or dispose of according to applicable law.
Below-ground pipes
- Remove and reuse, or dispose of according to applicable law, or leave in place while ensuring pipes are empty and ends are not capped/plugged.
Condensation pit
- Remove and dispose of according to applicable law.
Storage tanks, digester
- Reuse for another purpose following applicable law.
- Remove above-ground portion.
- Remove below-ground portion to an extent consistent with the probable future use of the land.
Gas storage roof/dome
- Recycle or dispose of according to applicable law.
Components affected by desulphurization (build-up of crystallized sulphur)
- Handle components with crystallized sulphur residuals with care, having caution for flammability. Residual sulphur crystal material can be blended with the digestate as an agricultural nutrient.
Electrical equipment
- Select a licensed electrical contractor to determine the involvement of ESA and the local electrical distribution company during decommissioning.
- Salvage, recycle or dispose of according to applicable law.
Mixers, pumps and other mechanical equipment
- Lockout mixers and pumps to prevent unintentional activation while dismantling.
- Salvage, recycle or dispose of according to applicable law.
Emergency flare and over-under pressure relief valve
- Salvage, recycle or dispose of according to applicable law.
Note: Only remove these valves when there is no chance that gas pressure could still build up in the container protected by the valve.
4. Restore the site
In most cases, the biogas system site is restored as agricultural or farmstead land. The OMAFRA fact sheet, Decommissioning and or recommissioning existing nutrient storage facilities, provides recommendations for dealing with below-ground components and ground surface restoration, and for safely disposing of structural materials on or off the farm. Where the site is within the footprint of the farmstead or where equipment was mostly or all above ground, it may be satisfactory to remove the equipment, tanks or structures without any further site restoration. Also, some equipment or structures may be re-purposed for other farmstead needs once other biogas system components have been removed.
Conclusions
Throughout the entire process of dismantling and decommissioning on-farm biogas systems, take care that the work is done safely. Follow applicable law when handling materials both on and off the farm. Information in this fact sheet will not override other requirements.
For example, biogas systems that are approved under the Environmental Protection Act, 1990, as a renewable energy generation facility must follow the requirements of the Ontario Ministry of the Environment, Conservation and Parks document, Technical Guide to Renewable Energy Approvals, for guidance on preparing the Decommissioning Plan Report.
Resources
- American Society of Agricultural and Biological Engineers. Manure Storage Safety, ASABE EP470.1 OCT2011 (R2016). Manure storage safety EP470.
- German Agricultural Occupational Health and Safety Agency. 2008. Safety Rules of Biogas Systems.
- Ontario Ministry of Labour, Immigration, Training and Skills Development. Health and safety in farming operations. Section 7: Hazardous atmospheres and confined spaces. 2009. ISBN 1-4249-0803-5.
- Technical Standards and Safety Authority. Digester plants, landfill sites and bio gas facilities. Fuels Safety Edition Newsletter. Volume 5, Issue 2, Fall 2007, p. 7.