Removing liquid manure from storage
Learn about the methods to remove liquid manure safely and effectively from storages for application on land or transfer to another storage facility. This technical information is for Ontario producers.
ISSN 1198-712X, Published June 2014
Introduction
This fact sheet describes methods to safely and effectively remove liquid manure from storages for application on the land or for transfer to another storage facility.
The Nutrient Management Act, 2002, (NMA) outlines rules and requirements for the handling and storage of manure and other nutrients on farms. The specific rules governing liquid manure management are found in the Nutrient Management Regulation O. Reg. 267/03. Some of these rules are discussed in this document.
Toxic gases
Agitation of liquid manure storages results in the release of deadly manure gases. Use extreme caution when gases can accumulate in an enclosed space such as during the removal or transfer of manure from a slatted floor barn.
When agitating manure in an under-barn storage, remember to keep manure turbulence to a minimum to avoid an excessive release of gases. Keep people and livestock as far away as possible from the area being agitated. Turn on the barn fans and open barn curtains to provide extra ventilation. Prevent people from entering the barn during agitation or transfer. See the OMAFRA fact sheet, Hazardous Gases on Agricultural Operations.
Manure removal equipment
There are many equipment options available for the types of storage and operating systems in use.
Vertical pumps
These pumps are designed to operate in the vertical position and are used to remove manure from storages under barns and from small transfer or surge storages (Figure 1).
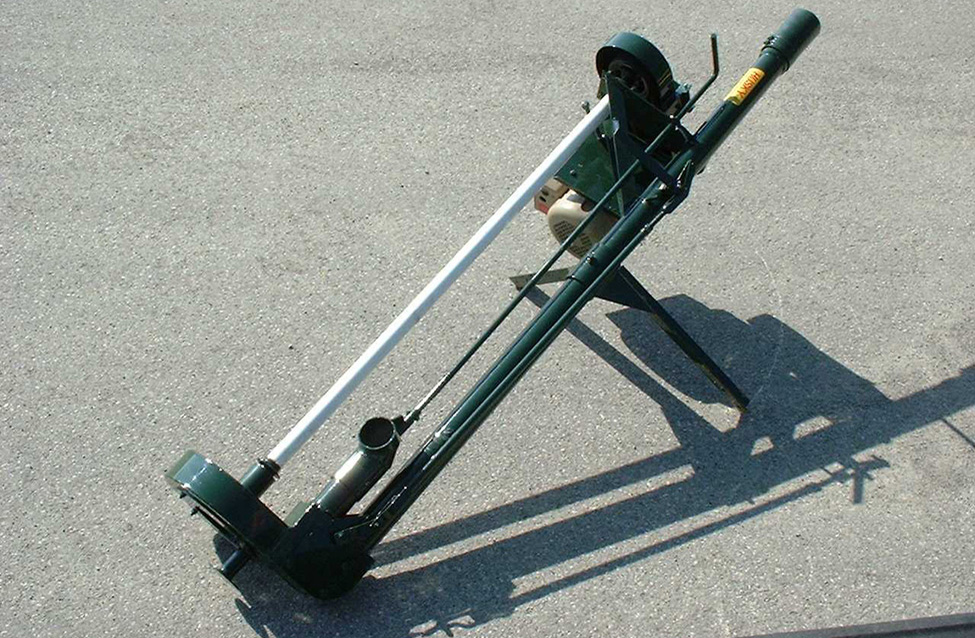
Usually, these pumps are driven with an electric motor and have limited capacity. Power take-off (P.T.O.)–driven vertical pumps are more powerful (Figure 2). These pumps are often mounted on a set of wheels for ease of transportation to different storages. Hydraulic cylinders tip the pump into the horizontal position for transport and raise and lower the pump into the storage.
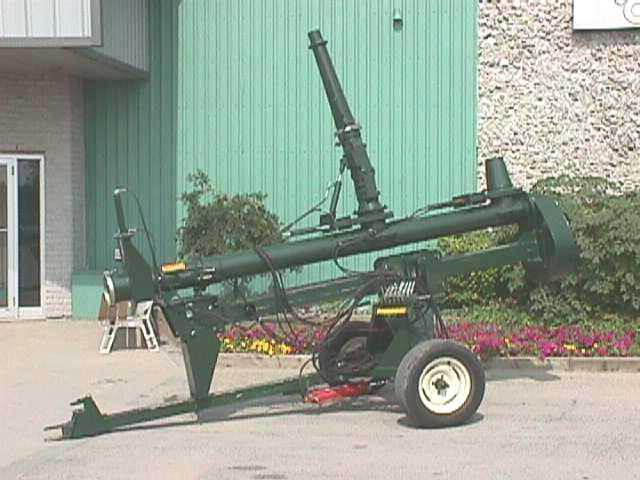
P.T.O.–powered pumps range in capacity from 14,000–23,000 L/min (3,600–6,000 U.S. gal/min). Power requirements range from 49–135 kW (65–180 hp).
When these pumps are mounted in a tank, install safety fencing around the pumping zone.
When transferring manure from a lower elevation storage to a higher storage, make sure unintended backflow does not occur. There are several ways to do this, including having an outlet above the maximum liquid level in the higher storage. In most cases, do not rely on anti-backflow valves because debris in the manure could jam the valve open. The Nutrient Management Regulation requires that if there is an opportunity for backflow, the transfer system must have a primary and secondary shut-off valve.
Side-mounted pumps
Side-mounted pumps are used with storages that have vertical walls and are either above or partly above ground. They are mounted permanently on the outside of the storage and are P.T.O. driven (Figure 3). Manure flows out the bottom of the storage through a large diameter pipe and into the pump. From there, the manure is recycled back into the storage for agitation or out into a tanker for spreading.
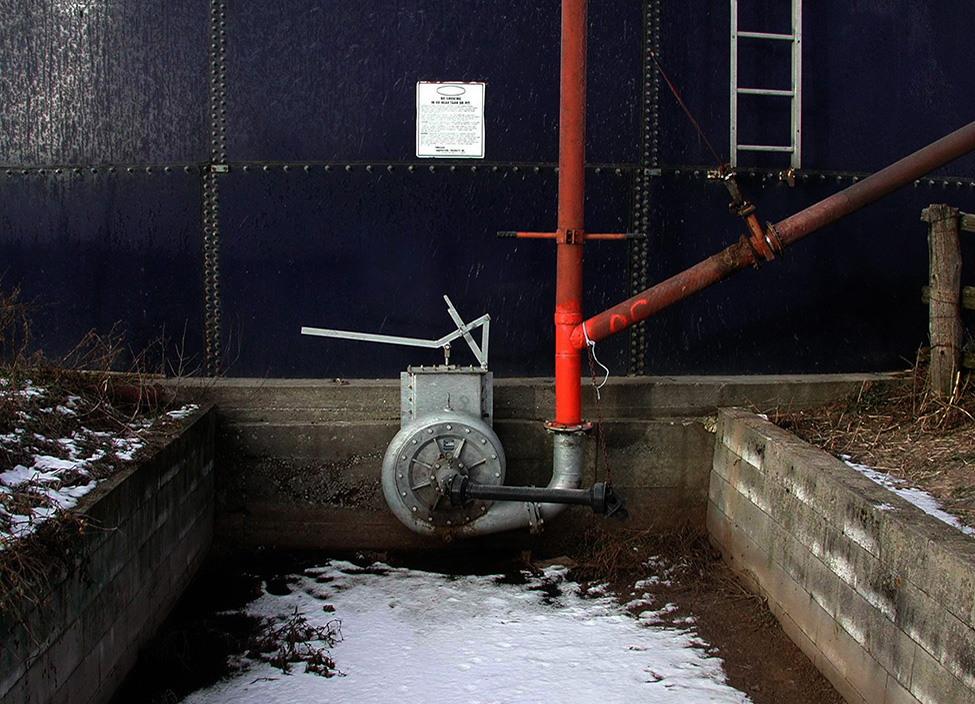
Shutoff valves are required between the pumping system and the storage tank to shut off flow to the pump. When the tank is empty, test these valves to ensure they are in working order.
Earthen manure storage pumps
Liquid manure storage pumps are available for storages with earth walls and/or sloped concrete ramps. They are also used in large below-ground storages where the pump is inserted into the storage on a slope.
These pumps are mounted on wheels for easy removal or transport. They have long power shafts that allow the impeller section of the pump to be backed down the side of the storage and into the manure. The pumps have various lengths of power shafts for storages of different sizes. Most pumps are manufactured with reaches varying from 6–12 m (20–40 ft).
Since earthen and some concrete storages can be quite large, special propeller-type agitators are available. These agitators are strictly for blending the manure before removing it from storage. They consist of a 3-point hitch frame, a long power shaft and a propeller. They can be lifted or lowered to enable the operator to break up heavy surface crusts or lift settled solids off the bottom of the storage. Pumps with hydraulically controlled nozzles are also used for this purpose, when the level of the liquid in the storage is lowered.
Some pumps have an auxiliary propeller mounted on them. This allows the one pump unit to either agitate and/or pump.
Take care when installing or removing a pump to not damage the liner of the storage. Operators may install a concrete pad over the liner at the pump entry point to prevent damage.
Sand-bedded systems
Most liquid manure systems use organic material such as straw, shavings or sawdust for bedding. However, in the dairy industry, sand is regularly used as bedding for livestock comfort. The properties of sand require specialized equipment and processes for removing sand-laden manure from storage. Sand is particularly rough on manure-handling equipment.
Since sand settles to the bottom of the storage, agitation must take place at the storage bottom to force the sand into suspension. It is more difficult to achieve this with coarse sand than with fine sand. Due to these difficulties, the liquid portion is generally removed first, then the sand and remaining manure are removed as a solid. Conduct nutrient sampling for both the liquid and solid portions to get accurate test results.
Hydraulic excavators are commonly used to reach into the smaller storages to remove the solid manure/sand blend. Larger storages have entrance ramps where the equipment enters the storage and loads the solids. Both types of material removal require a concrete base for satisfactory long-term operation.
A sand mixture in a tanker (especially if settled) has a much higher density, causing the tank to weigh more. Design the tank to be strong enough to handle this load. In addition, the increased loading may adversely affect the handling and braking characteristics of the tanker/tractor combination. Operators must be aware of this.
Caution with raceway systems
Circulatory or raceway systems are often used in slatted floor barns and consist of a series of interconnected narrow channels. A propeller-type agitator is inserted into the storage in one location, agitating the manure by circulating it around the channels (Figure 4).
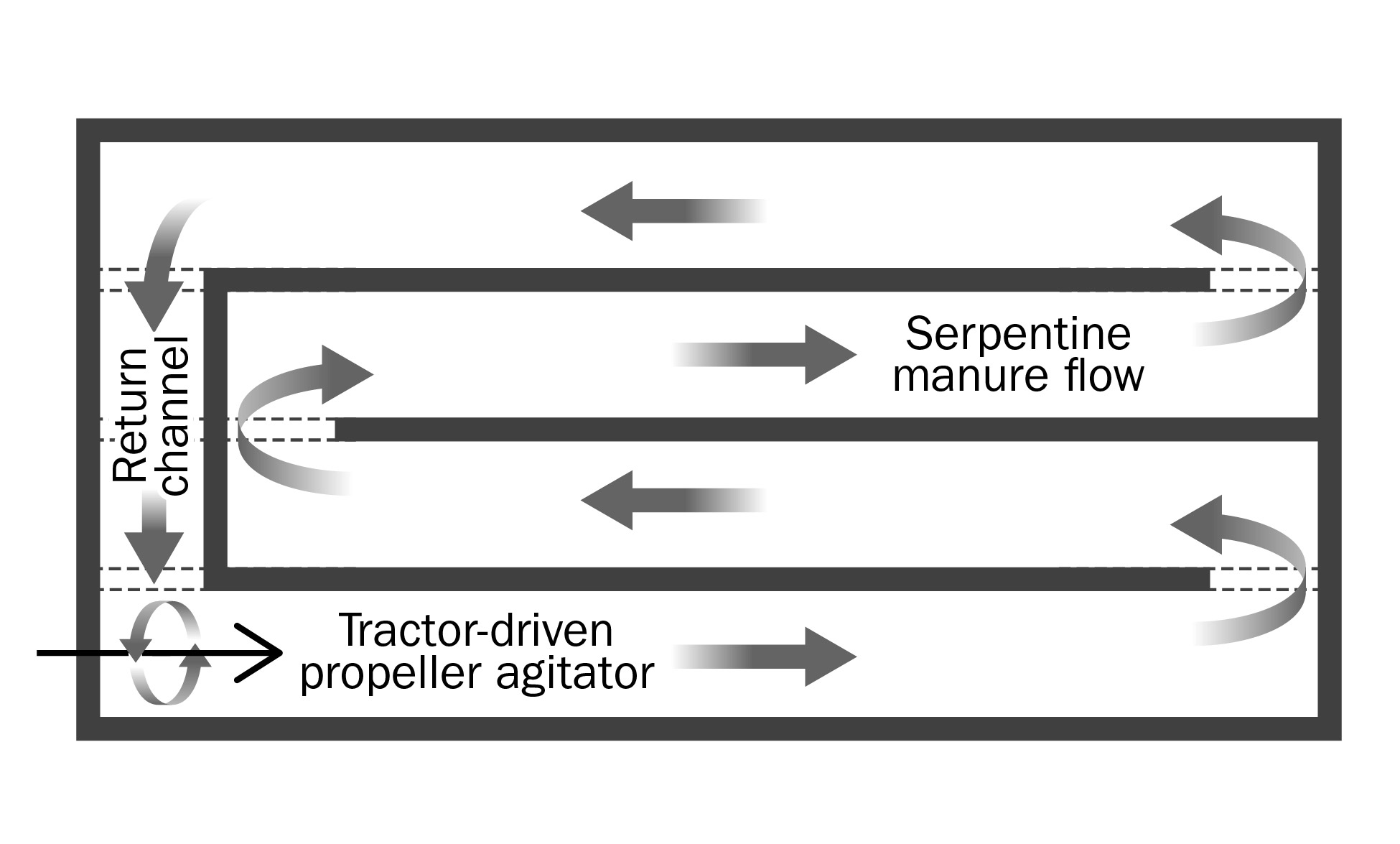
Problems arise if the manure does not start to circulate evenly and right away when the propeller agitator is started (Figure 5). If it doesn’t circulate properly, the manure level can rise sufficiently behind a section of thicker manure causing increased and uneven pressure on internal walls and slats. This causes the slats to be lifted off the channel walls. In some instances, especially when the weight of the slats is removed from the top of the wall, the walls will move from lack of lateral support. The slats and animals then fall into the manure storage, resulting in death and structural failure.
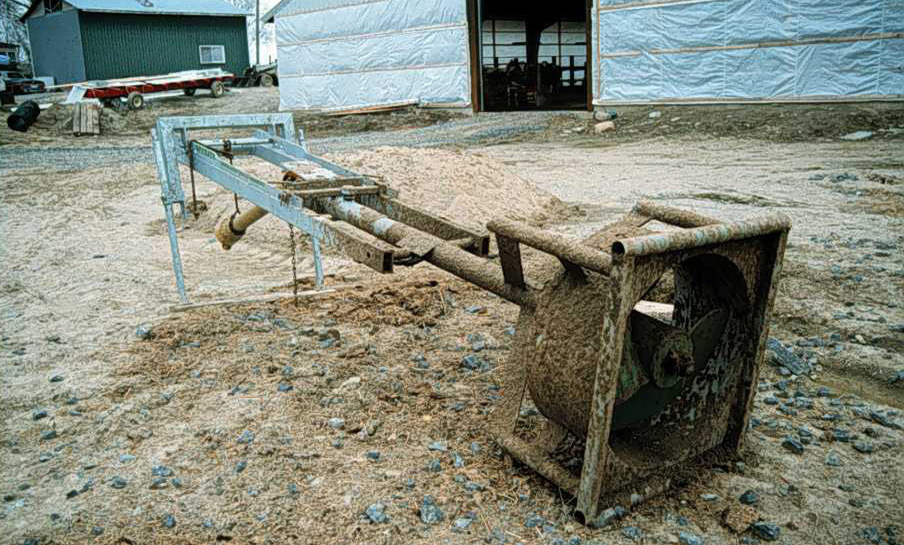
To avoid problems, agitate when the tank is half full to break up the surface crust and agitate again before emptying. In all cases, start the agitation very slowly and only increase the speed when the manure circulates completely and evenly.
If a manure system has not been agitated or removed for an extended period of time, it may be very difficult to achieve circulation. Even pumps at low flow could cause pressures that could initiate wall or slat failure. Consider an alternative means of agitation or dilution to correct this situation.
Removal and use of manure
The ability to agitate and pump liquid manure depends greatly on the moisture content of the manure. Pumping and agitation become more difficult as the moisture content of the manure is reduced. For this reason, thoroughly mix the manure to get the settled solids mixed in with the liquid portion before removing most of the liquid. This is especially true where the storage is particularly large and/or the agitating pump is slightly under-sized. Agitation time varies from 2–8 hours or longer, depending on the conditions.
To achieve adequate agitation, large storages may require more than one pump-out location. All pump-out locations require safety fencing, both when the pumps are installed and when they are removed (Figure 6).
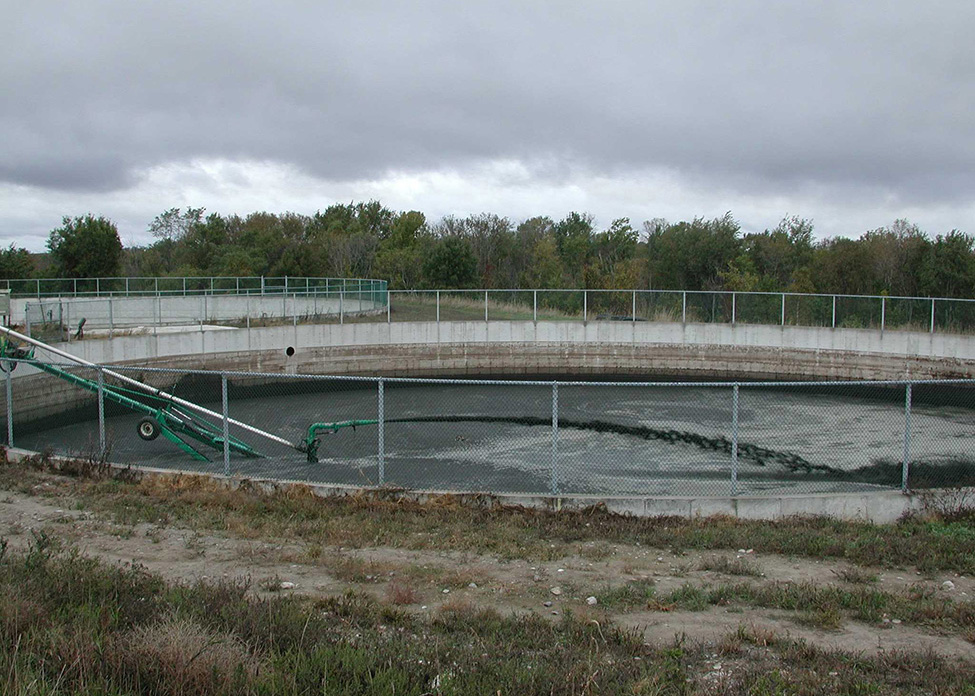
After the manure is thoroughly agitated, take manure samples when filling the tanker for nutrient and dry matter analysis to be used in the Nutrient Management Plan. Taking several samples throughout the pump-out period and mixing them for a composite sample will give a better estimate of the average manure content. Keep records from year to year to compare the data and see trends.
Many operators use their high-powered tractor to operate the agitator and then unhook it and use it to haul the heavy liquid tanker. Once agitation is complete, use a smaller tractor to pump manure into the tanker and keep the previously agitated manure in suspension. Ensure there is no chance of an agitation pump switching to transfer mode when the tanker is not in place.
Manure pumps usually have a high capacity in relation to the size of the liquid tanker. This means that a large tanker can be filled in minutes. It is important that the proper conditions exist, so the tanker is moved quickly into and out of position for loading (Figure 7).
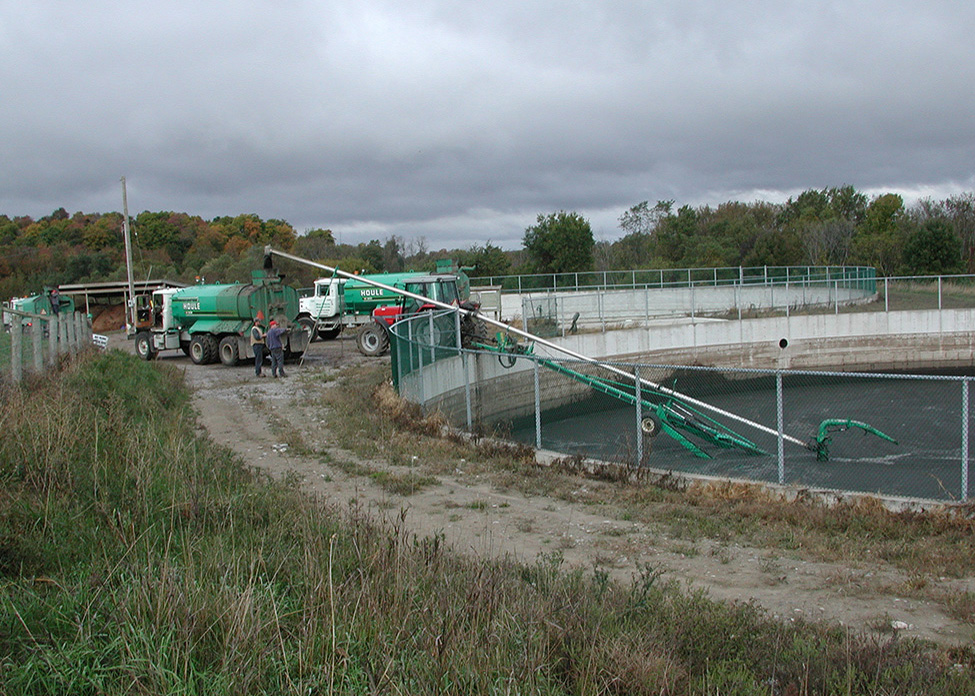
Having as large a tanker as practical reduces the number of trips to the field. This means more efficient use of equipment and labour. It is important to know that the tractor hauling the tanker has sufficient power and brakes to handle the large liquid load. Many larger tankers now come with brakes to minimize on-road risk. Skilled drivers are required to operate these heavy loads.
The risk of soil compaction increases with tanker size. Tankers should have adequate axles and tire size to minimize compaction.
In some cases, the manure is hauled to remote fields with semi-trailers. The tankers are then filled from the semi-trailer and used only for manure application. This option is becoming more popular as tankers are fitted with application equipment to inject the liquid manure. Manure injection equipment is designed to limit the exposure of manure to the air, thereby minimizing odours and nutrient loss.
Direct flow application systems
Direct flow systems move manure from the storage to the field for application through hoses. They may include tractor-pulled injection or broadcast systems, often called drag hoses. The Nutrient Management Regulation requires that safety devices are in place to stop the flow of material within 1 minute in the event of a leak in the piping system. The regulation sets out the staffing requirements for applying liquids by a direct flow application system. One or two operators are required, based on the ability of the operators to shut down the equipment within 1 minute, should a malfunction occur.
High trajectory application
The Nutrient Management Regulation prohibits using high trajectory application systems that spray liquid more than 10 m (30 ft) when applying manure or non-agricultural source materials, unless the material being applied is greater than 99% water by weight.
Gravity load-out from storage
A few gravity load-out systems have been installed in Ontario. These systems have storages installed at a higher elevation with an outlet pipe installed at a lower elevation. Operators of these systems must ensure that the storage’s earthen side walls are stable and the gravity shutoff system is secure. Operators should consider using a pump system to remove the manure instead of the gravity shutoff system. This avoids any issues with the shutoff system jamming open.
Safety fences and barriers
Maintain a safety fence at least 1.5 m (5 ft) high around open-top liquid manure storages. If a gate is opened for tractor access for agitating the manure, take steps to include the tractor within the safety fencing. This could include using temporary barriers and is especially important when operation of the agitation tractor is not fully supervised.
Install a safety fence barrier over any openings that are used to gain access to the pump. Open observation holes should have a safety fence or a lid that does not allow human access.
Avoiding spills
Removal of manure from storage needs to be completed carefully. Prevent spills from happening during tank filling by not overfilling the tanker. Many tankers have gauges that show when the tanks are almost full.
Take care to avoid inadvertently switching the agitation pump valve from agitation to transfer. This could cause a large spill!
If a spill occurs, immediately take steps to stop the source, contain the spill and notify the Ministry of the Environment Spills Action Centre at
Disclaimer
The information in this fact sheet is provided for informational purposes only and should not be relied upon to determine legal obligations. To determine your legal obligations, consult the relevant law. If legal advice is required, consult a lawyer. In the event of a conflict between the information in this fact sheet and any applicable law, the law prevails.
This fact sheet was revised by Don Hilborn (retired), P.Eng., engineer for by-products/manure, OMAFRA and reviewed by Jake DeBruyn, P.Eng., new technology integration, OMAFRA, Dan Ward, P.Eng., poultry and other livestock housing and equipment, OMAFRA and Dan McDonald, P.Eng., civil systems, OMAFRA.