2020 Watermain disinfection procedure
This document outlines procedures for disinfecting water mains as part of an addition, modification, replacement, extension, planned maintenance, or emergency repair in a municipal residential drinking water system. The procedures are required to be followed in order to satisfy conditions imposed by the Director in a drinking water works permit.
Published in August 2020
Summary of changes
Ontario’s Watermain Disinfection Procedure (WDP), first published in 2015, replaced the American Water Works Association (AWWA) Standard C651 as a requirement in municipal approvals for the disinfection of watermains. The first version of the Watermain Disinfection Procedure aimed to create more consistency in watermain repairs in Ontario. After implementation of the procedure, Operating Authorities contacted the Ministry of the Environment, Conservation and Parks to express the need for better disinfection, commissioning, and documentation requirements for new watermains in Ontario. Revisions to the procedure were developed by the Ministry in consultation with municipal drinking water system owners, operating authorities, and the Ontario Water Works Association (OWWA). The updated procedure also includes changes to the watermain repair sections based on comments received on the first version.
What has been updated
- Additional requirements for new watermains were added to the Preface and Section 1 of the procedure.
- Minor changes were made to Section 2 of the procedure.
- Section 3.1 was added to define the requirements for documentation for new watermains.
- The Appendices were updated to reflect the changes to the procedure.
When the procedure will take effect
The revised procedure will take effect through conditions in the Drinking Water Works Permit. There are two scenarios that will apply depending on the timing of a system’s Municipal Drinking Water Licence renewal: permits specifying timelines for transition (scenario 1) and permits that do not specify timelines for transition (scenario 2). Drinking water systems must use the 2015 procedure until the date specified by the permit, unless the system receives approval from the Ministry to use the 2020 procedure earlier. Drinking water systems cannot partially implement the 2020 procedure.
Scenario 1: Permits specifying timelines for transition
If the Municipal Drinking Water Licence for the system was renewed in 2019 or 2020, the updated permit includes a condition (typically condition 2.3) requiring any new procedure to be used within six-months from the time the procedure is published by the Ministry. The publication date of the revised procedure is August 1, 2020, requiring these systems to use the new procedure by February 1, 2021.
Scenario 2: Permits that do not specify timelines for transition
If the system’s permit does not already include a condition (typically condition 2.3) that requires use of the updated Watermain Disinfection Procedure, this condition will be added when the Municipal Drinking Water Licence for the system is renewed. The November 2015 version of the procedure is to be used until the permit is updated with the new condition at licence renewal, unless the system receives approval from the Ministry to use the updated procedure earlier. The updated condition will require the drinking water system to use the updated version of the procedure six-months from the date the renewed licence is issued.
Early implementation of the 2020 Watermain Disinfection Procedure
The Ministry is encouraging early implementation of the updated procedure as this eliminates the need to apply for relief in certain situations when disinfecting watermains. To implement the August 1, 2020 procedure prior to the date required by conditions in the permit, systems are required to submit a request to MDWLP@Ontario.ca.
Preface
This watermain disinfection procedure is a supporting document for Ontario legislation and regulations related to Drinking Water. Schedule B, Condition 2.3 of the Drinking Water Works Permit adopts this procedure by reference. Where this procedure makes reference to ANSI/AWWA Standard C651 Disinfecting Water Mains and CSA Standards B64.10 and B64.10.1, the most current versions of these standards shall be used. The section numbers mentioned in this document are based on the 2014 version of C651 and the March 2017 version of B64.10 and B64.10.1. When updated versions of these standards are released however, the corresponding section(s) and amended wording of the updated version will supersede the requirements of the previous version. Definitions listed in Appendix H are capitalized and italicized throughout this procedure.
The requirements in this procedure apply to all watermains of any size, including temporary watermains. Service Pipes of 100 mm diameter and greater shall be considered as watermains for the purposes of this procedure.
Operating Authorities shall use Certified Operators for activities that must be performed by a Certified Operator or may use a Water Quality Analyst for sampling and testing if permitted through regulation. Watermains that form part of a Drinking Water System can only be Isolated and placed into service by Certified Operators. Activities performed on Isolated watermains are not required to be performed by Certified Operators.
Any water used for the purposes of, but not limited to, flushing, swabbing, disinfection, hydrostatic testing, and displacing water to obtain samples for testing, shall be Drinking Water. Any temporary water supply to a new watermain shall be Flushed prior to its use as a water source.
Chemicals used for disinfection shall meet the requirements of both the American Water Works Association ("AWWA") and the American National Standards Institute ("ANSI") safety criteria standards NSF/ANSI/CAN 60.
Operating Authorities may use best management practices that exceed the minimum requirements in this procedure.
Deviations from this procedure may be requested from the Ministry’s Approval and Licensing office on a case-by-case basis.
1. Addition, modification, replacement, extension and planned maintenance
1.1. New watermains
For watermains, including temporary watermains, that are added to, modified, re-aligned, replaced or extended within a Drinking Water System, Operating Authorities shall ensure that the requirements of ANSI/AWWA Standard C651 are followed as modified by this procedure.
1.1.1. Backflow Prevention requirements for new watermains
The Backflow Prevention provisions within Section 4.8.9 of ANSI/AWWA Standard C651 shall be mandatory for the installation of new watermains except for Connections (see section 1.1.4).
Where required, Backflow Prevention for new watermains shall be accomplished by:
- an air gap as defined in CSA Standard B64.10 Selection and Installation of Backflow Preventers; or
- A CSA-certified reduced pressure principle (RP) backflow preventer that has been selected and field tested in accordance with CSA Standards B64.10 and B64.10.1. Examples of RP backflow preventer installations are shown in Figures A-1 and A-2, while schematic representations are shown in Figures A-3 and A-4, respectively, of Appendix A.
Exception: If a backflow preventer is relocated within the same day, testing is only required for the first installation of the day provided that the backflow preventer is relocated by a Certified Operator who will guard against damage during transit and re-installation.
For the purposes of CSA Standard B64.10, a backflow prevention tester’s licence shall be an Ontario Water Works Association (OWWA) Certified Cross Connection Control Specialist Certificate or a Ministry-approved equivalent. In addition to the list of professionals in Table 1 of Figure E.1. of CSA Standard B64.10, a Certified Operator or a Water Quality Analyst with a backflow prevention tester’s licence shall also be authorized to test, install, relocate, repair or replace backflow preventers used in the installation and commissioning of new watermains.
1.1.2.Disinfection of new watermains
For preliminary flushing prior to disinfection referred to in Sections 4.4.2 and 4.5.2 of ANSI/AWWA Standard C651, if the requirements of ANSI/AWWA Standard C651 for a velocity of 3.0 ft/sec (0.91 m/sec) are not practical, alternative cleaning consisting of swabbing or flushing 2-3 pipe volumes can be used at the discretion of the Operating Authority.
Where a newly constructed watermain is disinfected using the tablet, continuous feed, slug, or spray chlorination method (not limited to large transmission mains) as per the procedures in ANSI/AWWA Standard C651, the minimum contact times, initial chlorine concentrations, and maximum allowable decreases in chlorine concentration as listed in Table 1 shall be used. The disinfection method used is at the discretion of the Operating Authority.
When using the Tablet or Continuous Feed Disinfection Method, if the Maximum Allowable Decrease in Chlorine Concentrations is exceeded at any of the sampling points, the disinfection procedure must be repeated.
When using the Slug Disinfection Method, the chlorine concentration shall be measured in the slug at the beginning of the disinfection process, as the slug moves through the watermain, and at the point of discharge. If the chlorine concentration decreases by more than 25 mg/L at any of the sampling points, the flow shall be stopped and additional chlorine shall be added to restore the chlorine concentration in the slug to not less than its original concentration.
Table 1: Chlorine concentrations* and contact times for disinfecting new watermains
Disinfection method | Minimum contact time | Initial chlorine concentration | Maximum allowable decrease in chlorine concentration |
---|---|---|---|
Tablet or Continuous Feed | 24 hours | ≥ 25 mg/L | 40% of the Initial Chlorine Concentration to a maximum of 50 mg/L** |
Slug | 3 hours | ≥ 100 mg/L | 25 mg/L |
Spray | 30 minutes | ≥ 200 mg/L | Measurement Not Required |
* At concentrations over 10 mg/L, measurements of total chlorine and free chlorine shall be deemed equivalent.
** Exception: Where copper pipe is used as a watermain, disinfection shall be performed using the continuous feed method, with an initial chlorine concentration of ≥ 50 mg/L and a minimum 24-hour contact time. Due to the chlorine demand exerted by the copper, the maximum allowable decrease requirement in Table 1 does not apply, and the effectiveness of the disinfection process shall be demonstrated by the Microbiological Sampling referred to in Section 1.1.3.
The following examples are provided to demonstrate the proper use of Table 1.
Example 1
When using the Continuous Feed Disinfection Method with an initial chlorine concentration of 50 mg/L, the maximum allowable decrease in chlorine concentration is 40% of 50 mg/L, or 20 mg/L. Therefore, at least 30 mg/L of chlorine must be present after 24 hours.
Example 2
When using the Continuous Feed Disinfection Method with an initial chlorine concentration of 150 mg/L, the maximum allowable decrease in chlorine concentration is 50 mg/L, because 40% of 150 mg/L is greater than the maximum allowable decrease of 50 mg/L. Therefore, at least 100 mg/L of chlorine must be present after 24 hours.
Example 3
When using the Slug Disinfection Method, if the initial chlorine concentration in the slug is 150 mg/L, then the chlorine concentration must not decrease below 125 mg/L (a decrease of > 25 mg/L). If the chlorine concentration were to fall below 125 mg/L, the flow shall be stopped and chlorine added to restore the chlorine concentration to at least 150 mg/L.
1.1.3. Microbiological Samples for new watermains
The Operating Authority shall ensure that the Microbiological Samples taken in accordance with ANSI/AWWA Standard C651 include as a minimum Escherichia coli and Total Coliforms and are tested by a licensed and accredited laboratory. When Microbiological Samples are taken from new watermains that have not been placed into service, Operating Authorities shall ensure that additional samples are taken at the same time from the same location and are tested immediately for:
- free chlorine residual, if the system provides chlorination and does not provide chloramination; or
- combined chlorine residual, if the system provides chloramination.
These Microbiological Samples and disinfectant residual tests are not considered Drinking Water tests for the purpose of the Safe Drinking Water Act (SDWA), and are, therefore, not reportable. Any person authorized by the owner or Operating Authority can collect Microbiological Samples from watermains that have not been placed into service and perform the associated disinfectant residual tests.
For new watermains with limited sampling points available, an alternative method of taking Microbiological Samples is called staged sampling. Staged sampling shall be performed as follows:
- A flow meter shall be installed to measure flow through the new watermain;
- A sampling point shall be installed at the end of the new watermain (additional sampling points may also be installed along the length of the watermain); and
- Flow shall be established, and samples shall be taken from the sampling point(s) at intervals that are calculated to represent the lengths of the watermain as required by Sections 5.1.1.2 and 5.1.1.3 of ANSI/AWWA Standard C651, based on the pipe size and the measured flow rate.
Operating Authorities shall endeavour to maintain an Acceptable Disinfectant Concentration until the new watermain is placed into service. If a concentration of 0.05 mg/L of free chlorine residual in a chlorinated system (or 0.25 mg/L of combined chlorine residual in a chloraminated system) is not maintained prior to placing into service, the microbiological sampling shall be repeated.
1.1.4. Connecting new watermains to the existing system
The provisions outlined in Section 4.10 of ANSI/AWWA Standard C651 are mandatory, along with the additional requirements prescribed below. The Backflow Prevention provisions within Section 4.8.9 of ANSI/AWWA Standard C651 are not mandatory for Connections.
When Microbiological Samples are taken from Connections, Operating Authorities shall ensure that additional samples are taken at the same time from the same location and are tested immediately for:
- free chlorine residual, if the system provides chlorination and does not provide chloramination; or
- combined chlorine residual, if the system provides chloramination.
1.1.4.1. Connections equal to or less than one pipe length (Generally ≤ 6 m)
The Operating Authority shall ensure that Connections equal to or less than one pipe length (generally ≤ 6 m) are undertaken in accordance with Section 4.10.1 of ANSI/AWWA Standard C651 and that the Connection remain Isolated from the existing Drinking Water System, except while being flushed or sampled, until satisfactory results are received from one Microbiological Sample, taken by a Certified Operator or Water Quality Analyst, from water that has been directed through the Connection.
Exception: If a Certified Operator is present to witness the installation and disinfection of the Connection to ensure that the sanitary construction practices and disinfection requirements of Sections 4.10 and 4.10.1 of ANSI/AWWA Standard C651 were met, then the Connection can be placed into service with no Microbiological Sample required.
1.1.4.2. Connections greater than one pipe length (generally > 6 m)
Connections greater than one pipe length (generally > 6 m) shall be undertaken in accordance with Section 4.10.2 of ANSI/AWWA Standard C651.
Exception: The procedure described below may be used at the discretion of the Operating Authority for the installation and disinfection of Connections greater than one pipe length and up to a total length of 40 m if the Connection:
- Crosses a transportation corridor, the extended closure of which could result in significant community impacts (e.g., traffic congestion, loss of emergency vehicle access, safety concerns), or
- Cannot be constructed to within one pipe length of the existing watermain due to the potential for destabilizing an existing thrust block.
Procedure:
- The new watermain and Appurtenances forming the Connection shall be sprayed or hand swabbed with a minimum 1% sodium hypochlorite solution, aboveground or in the excavation, immediately prior to installation.
- A Certified Operator is required to witness the installation of the Connection to ensure that sanitary construction practices are followed, and proper disinfection is performed.
- The Connection shall remain Isolated from the existing Drinking Water System, except while being flushed or sampled, until satisfactory results are received from two Microbiological Samples taken by a Certified Operator or a Water Quality Analyst in accordance with Section 5.1.1.1 of ANSI/AWWA Standard C651.
- Where required by the Operating Authority, hydrostatic testing of the Connection shall not be undertaken against the isolating valve until satisfactory results from the Microbiological Samples referred to above are received. Drinking Water shall be used for hydrostatic testing.
Figure B-1 in Appendix B provides an example to help understand this exception.
1.1.4.3. Placing new watermains into service
Valves opened to place a new watermain into service shall, in all cases, be operated by a Certified Operator. As part of placing a watermain into service, Flushing through the Connection shall be performed until a Certified Operator or a Water Quality Analyst verifies that an Acceptable Disinfectant Concentration is present in the new watermain. If Microbiological Samples are taken and/or disinfectant residual tests are performed after a watermain is placed into service, they are considered as Drinking Water tests for the purpose of the SDWA and adverse test results are reportable.
1.2. Relining of watermains
For relining of existing watermains, the conditions of Sections 1.1.2, 1.1.3 and 1.1.4 of this procedure will apply.
Exception: The Operating Authority may allow return to service prior to receiving all satisfactory Microbiological Sample results if all the following conditions are met:
- The watermain is physically Isolated from the remainder of the Drinking Water System through Backflow Prevention;
- The local Medical Officer of Health is consulted prior to the commencement of the project and their advice is documented and followed; and
- Flushing of the watermain has been completed and an Acceptable Disinfectant Concentration has been restored.
1.3. Planned watermain inspection and cleaning
All equipment used for the inspection of watermains shall be dedicated for that purpose only, and shall be suitable for disinfection. Sanitary practices shall be followed to prevent the introduction of Contaminants into the watermain. All inspection equipment inserted into a watermain (e.g., electromagnetic, acoustic, or video inspection equipment) shall be cleaned and disinfected using a minimum 1% sodium hypochlorite solution immediately prior to insertion. Drinking Water shall be used for equipment cleaning and/or preparation of hypochlorite solutions. Disinfectant residual testing shall be performed upon removal of the inspection equipment. Flushing shall be performed if an Acceptable Disinfectant Concentration was not maintained.
For planned watermain cleaning by swabbing or Higher Velocity Flushing, the system can be returned to normal service, defined as having all valves returned to normal operating position, after an Acceptable Disinfectant Concentration is achieved at the point of flushing.
For all other types of cleaning (e.g. air scouring, ice pigging, etc.), the Operating Authority shall develop and implement a site-specific plan for cleaning, disinfection, and sampling in agreement with the local Ministry office in consultation with the local Medical Officer of Health.
1.4. Planned maintenance of Appurtenances and fittings
Section 2 of this procedure for Category 1 watermain breaks shall apply to the installation/replacement/repair of Appurtenances and/or fittings. If Contamination is evident or suspected, the procedures prescribed under Section 2 of this procedure for Category 2 watermain breaks shall apply.
1.5. Tapping of watermains
Where existing watermains are tapped, the pipe surface at the location of the tap shall be cleaned and disinfected using a minimum 1% sodium hypochlorite solution. Where applicable, the drill/cutting/tapping bits and all surfaces of mainstops, service saddles, tapping sleeves and valves which will come into contact with Drinking Water shall likewise be cleaned and disinfected using a minimum 1% sodium hypochlorite solution immediately prior to installation. If any of the disinfected surfaces come into contact with the soil and/or water in the excavation prior to use, the cleaning and disinfection procedure shall be repeated.
The live tapping (i.e., wet tapping) of a watermain that is part of the Drinking Water System must be performed by a Certified Operator; however, a person or contractor who is not a Certified Operator may perform wet taps provided they are being Directly Supervised by a Certified Operator. The Operating Authority shall maintain records of the name of the Certified Operator present for the wet taps.
1.6. Service pipes
Service Pipes of 100mm diameter and greater shall be considered as watermains for the purposes of this procedure and shall be disinfected and tested in accordance with the requirements of ANSI/AWWA Standard C651 as modified by this procedure. For Service Pipes of diameter less than 100mm, Operating Authorities shall ensure that sanitary conditions are maintained during installation/repair, and that Flushing is conducted before they are placed into service.
1.7. Return to service of watermains Isolated from the distribution system
Where a section of watermain has been Isolated from a Drinking Water System and a concentration of 0.05 mg/L of free chlorine residual in a chlorinated system (or 0.25 mg/L of combined chlorine residual in a chloraminated system) was not maintained within the Isolated section (e.g., a valved-off stub), the Operating Authority shall develop and implement a re-commissioning plan that reflects the duration of isolation and the associated risks. The plan may include the implementation of Sections 1.1.2, 1.1.3, and/or 1.1.4 of this procedure. At a minimum, the plan must include:
- Flushing through the Isolated section of watermain; and
- Satisfactory test results to be received from at least one Microbiological Sample prior to the Isolated watermain being placed into service.
The Operating Authority shall keep a copy of the re-commissioning plan and maintain records showing that all items required by the re-commissioning plan were satisfactorily completed.
2. Watermain disinfection procedures for emergency repairs
This procedure uses a risk management approach to categorize watermain breaks based on the potential for Contamination. The objective of this procedure is to set minimum disinfection requirements to minimize the potential for Drinking Water Health Hazards during emergency/unplanned repairs resulting from the physical failure of a watermain and/or Appurtenance (a watermain break).
2.1. Categorization and public agency notification of watermain breaks
All watermain breaks shall be classified as Category 2 as per Section 2.1.2 of this procedure unless an Operator-in-Charge (OIC) conducts a visual inspection upon completion of the excavation to determine the nature of the watermain break and classifies it as a Category 1 as per Section 2.1.1. The OIC shall assess the evidence of Contamination or suspected Contamination of the watermain throughout the repair procedure and shall reclassify if required.
Refer to Appendices C (flowchart) and D (pictures) to better understand the criteria for categorizing watermain breaks.
2.1.1. Category 1
An OIC may classify watermain breaks with no evident or suspected Contamination as Category 1. The steps described in Sections 2.2 and 2.3 of this procedure shall be followed for Category 1 watermain break repairs.
Contamination is typically not suspected for circumferential breaks or small leaks where flow is maintained from the break until an Air Gap is established and where the Air Gap is maintained during the repair procedure. If, at any time, Contamination is evident or suspected, the watermain break shall be reclassified as Category 2.
2.1.2. Category 2
Watermain breaks with evident or suspected Contamination shall remain classified as Category 2. Watermain repairs involving more than one pipe length (generally ≥ 6 m) of replaced pipe are also classified as Category 2. The steps described in Sections 2.2 and 2.4 of this procedure shall be followed for Category 2 watermain break repairs.
2.1.3. Public agency notification
2.1.3.1. Category 1
Category 1 watermain breaks are not deemed to be observations of improper disinfection in accordance with Section 16-4 of Schedule 16 of O. Reg. 170/03, and are not reportable to the Spills Action Centre.
This procedure does not require that the local Medical Officer of Health be notified of Category 1 watermain break repairs; however, the local Medical Officer of Health may exercise their option to require such notification. Operating Authorities may choose to provide notification to, or seek advice from, the local Medical Officer of Health at any time.
2.1.3.2. Category 2
Category 2 watermain breaks are not reportable unless an Operating Authority believes that contaminated water was directed to users. If an Operating Authority believes that contaminated water was directed to users, this will constitute an observation of improper disinfection in accordance with Section 16-4 of Schedule 16 of O. Reg. 170/03, and the reporting and corrective actions of Schedule 16 and the applicable Schedule 17 or 18 of O. Reg. 170/03 shall apply.
This procedure does not require that the local Medical Officer of Health be notified of Category 2 watermain break repairs unless an observation of improper disinfection has been reported as noted above; however, the local Medical Officer of Health may exercise their option to require such notification. Operating Authorities may choose to provide notification to, or seek advice from, the local Medical Officer of Health at any time.
Notification to the Ministry is not required for Category 2 watermain breaks however if a Water Advisory is declared or a watermain break is assessed to be a Special Case as described in sections 2.4.4 and 2.4.5, the Operating Authority shall verbally notify the Ministry as soon as reasonably possible by speaking in person or on the telephone with a person. The notification shall be made to the Spills Action Centre during and after business hours.
2.2. Watermain break disinfection procedure common to Categories 1 and 2
The following steps must be performed for all emergency watermain repairs (Category 1 and Category 2). Examples of typical steps for Category 1, 2 and special cases are provided in Appendices E, F and G of this procedure, respectively.
2.2.1. Maintenance of flow
The Operating Authority shall determine if flow can be maintained to the watermain break site until the watermain is excavated. This determination shall be based on risks to worker and public safety, the possibility of property damage, and/or adverse impact to the natural environment.
The Operating Authority will attempt to maintain flow from the watermain break, where possible, until an Air Gap is established. Flow may be reduced by throttling valves while maintaining sufficient flow from the watermain break to minimize the potential for Contamination. Flow may be discontinued after an Air Gap has been created.
If flow from the watermain break is not maintained before an Air Gap is established, the watermain break shall remain Category 2.
2.2.2. Excavation dewatering
Excavation dewatering shall be continued for the duration of the repairs such that the Air Gap between the location of the watermain break and the water in the excavation is maintained. If the water level in the excavation rises such that the Air Gap is not maintained after flow from the watermain break has been discontinued, then the watermain break shall be classified as Category 2.
2.2.3. Disinfection of pipe and repair parts
All surfaces of pipe and repair parts which will come into contact with Drinking Water shall be disinfected using a minimum 1% sodium hypochlorite solution immediately prior to installation. If any of the disinfected surfaces come into contact with the water and/or soil in the excavation prior to installation, the surfaces shall be cleaned, and the disinfection procedure shall be repeated.
If cutting out a section of pipe, the interior surfaces of the cut ends of the existing watermain shall be disinfected using a minimum 1% sodium hypochlorite solution, swabbed or sprayed as far as can be practically reached.
2.2.4. Installation of repair parts
The repair parts shall be installed while ensuring that Contaminants do not enter the watermain.
2.2.5. Post-repair Flushing and return to normal service
Flushing shall be conducted following repairs by creating a temporary dead end downstream of the watermain break through valve operation, and Flushing through the location of the repair to a discharge point. Flushed water may be discharged from a hydrant, plumbing or Appurtenances. Where there is no discharge point to allow for Flushing, the Operating Authority shall tap the watermain on the downstream side of the watermain break and discharge from that point.
Flushing shall continue until the discharged water is visibly free from discoloration and particulates, and an Acceptable Disinfectant Concentration has been restored; whereupon the system can be returned to normal service, defined as having all valves returned to normal operating position.
Exception: Where the repair was performed using a repair sleeve and flow was maintained from the watermain break until an Air Gap was established, Flushing is not required.
Dechlorination is required for any water that is directly discharged into surface water or if the discharge into the natural environment is likely to cause an adverse effect, as per Condition 10.0 of Schedule B of the Municipal Drinking Water Licence. The discharged water is deemed to be a Class II spill for the purposes of O. Reg. 675/98 (Classification and Exemption of Spills and Reporting of Discharges) made under the Environmental Protection Act. Discharges of flushed water are also regulated under Condition 5.5 of Schedule C of the Municipal Drinking Water Licence.
2.3. Additional information for Category 1 watermain break repairs
2.3.1. Microbiological Samples (Optional)
There is no requirement for Microbiological Samples to be taken following Category 1 watermain break repairs. Where the Operating Authority chooses to perform Microbiological Sampling, the samples shall be deemed Drinking Water samples within the meaning of O. Reg. 170/03, and the reporting/corrective actions of Schedule 16 and the applicable Schedule 17 or 18 of O. Reg. 170/03 shall apply.
2.4. Additional requirements for Category 2 watermain break repairs
In addition to the requirements described in Section 2.2 of this procedure, the following steps are required for Category 2 watermain break repairs.
2.4.1. Removal of Contaminants from watermain
Appropriate additional steps shall be undertaken to remove Contaminants from the watermain, such as:
- Physical removal of Contaminants;
- Flushing into the excavation;
- Higher Velocity Flushing after repairs where practical and feasible.
2.4.2. Additional disinfection procedures
In addition to the steps in Section 2.2.3 of this procedure, site-specific disinfection procedures may also be used depending on the severity or nature of the Contamination. The steps may include the disinfection procedures for new watermains as per ANSI/AWWA Standard C651.
2.4.3. Microbiological Samples (Mandatory)
After the completion of Flushing, at least one Microbiological Sample shall be taken and submitted as soon as reasonably possible, taking into consideration laboratory working hours and transportation timeframes.
The flow shall be directed to ensure that the sample represents water that has passed through the location of the repair. The sampling will typically occur at the point of Flushing, and may take place from sampling ports, hydrants, blow-offs, or premise plumbing. All samples shall be considered Drinking Water samples, taken and tested in accordance with O. Reg. 170/03 requirements. The reporting and corrective actions of Schedule 16 and the applicable Schedule 17 or 18 of O. Reg. 170/03 shall apply.
The watermain may be returned to normal service, defined as having all valves returned to normal operating position, prior to receipt of Microbiological Sample results.
2.4.4. Special case—Sewage Contamination
If there is evident or suspected sewage Contamination of a watermain, in addition to the steps in Sections 2.2 and 2.4 of this procedure, the Operating Authority shall develop and implement a plan with site-specific procedures for disinfection and sampling. The sampling plan shall include as a minimum taking two sets of Microbiological Samples at least 24 hours apart.
Return to normal service is contingent upon the corrective actions and sampling plan being completed to the satisfaction of the local Ministry office (in consultation with local Medical Officer of Health). The affected watermain(s) may not be placed into service before the corrective actions and sampling plan are completed unless a Water Advisory is declared.
The disinfection requirements for new watermains as per Section 1.1.2 of this procedure may be used based on agreement between the Operating Authority and the local Ministry office, in consultation with the local Medical Officer of Health.
2.4.5. Special case—Chemical Contamination
If there is evident or suspected chemical Contamination of a watermain, in addition to the steps in Sections 2.2 and 2.4 of this procedure, the Operating Authority shall develop and implement a plan with site-specific procedures for disinfection and/or decontamination and sampling. The Operating Authority shall finalize the plan in agreement with the local Ministry office, in consultation with the local Medical Officer of Health.
Return to normal service is contingent upon the corrective actions and sampling plan being completed to the satisfaction of the local Ministry office, in consultation with the local Medical Officer of Health. The affected watermain(s) may not be put back in service before the corrective actions and sampling plan are completed unless a Water Advisory is declared.
3. Documentation
3.1. Documentation for New Watermains
When installing new watermains as per Section 1.1 of this procedure, the Operating Authority shall maintain records of the following information as a minimum. The information shall be retained as per the record-keeping requirements of Section 27 of O. Reg. 128/04. This section does not require that all of the information be recorded on a single form:
- Backflow Prevention:
- Air gap (as defined in CSA Standard B64.10 Selection and Installation of Backflow Preventers) or Reduced Pressure Principle Backflow Preventer installed as per Section 4.8.9 of ANSI/AWWA Standard C651; and
- Backflow preventer tested as per Section 1.1.1 of this procedure.
- Pre-disinfection swabbing and/or flushing have been completed.
- Disinfection Process:
- Method of disinfection;
- Disinfection chemical meets the requirements of both the AWWA and NSF/ANSI/CAN 60 Standards.
- Date and time disinfection started and ended;
- Chlorine concentration at start and end of contact time at each sampling point; and
- Decrease in chlorine concentration in mg/L and/or percentage as applicable.
- Microbiological Sampling referred to in Section 1.1.3:
- Schematic or drawing showing approximate location where Microbiological Samples were taken;
- Microbiological and disinfectant residual sample results; and
- For staged sampling: flow rate, time each sample was taken and calculated length.
- Connections referred to in Section 1.1.4:
- Length of Connection;
- Confirmation whether sanitary construction practices were followed;
- Confirmation that proper disinfection was performed;
- Name of Certified Operator present for the installation of the Connection if required;
- Results of Microbiological and disinfectant residual samples if required;
- Reason for using the exception under s. 1.1.4.2 (if used);
- Disinfectant residual after watermain is flushed and put in service; and
- Date and time watermain was placed into service.
3.2. Documentation for Watermain Maintenance and Repair
When performing maintenance and repair activities as per Sections 1.4 and 2 of this procedure, the Operating Authority shall maintain records of the following information as a minimum. The information shall be retained as per the record-keeping requirements of Section 27 of O. Reg. 128/04. This section does not require that all of the information be recorded on a single form:
- Date.
- Location (e.g., a municipal address).
- Flow maintained at the site until Air Gap created.
- Watermain size and material (e.g., 150mm cast iron).
- No evident or suspected Contamination of the watermain was observed before or during the repair process.
- If watermain break, indicate type of watermain break (e.g., circumferential, longitudinal, split bell, spiral, rupture, blow-out, hole, leak at main stops/tapping valves, etc.).
- If planned maintenance, indicate type of planned maintenance (e.g., valve replacement)
- Air Gap maintained, once established, throughout the repair process.
- Name of Operator-in-Charge who classified the watermain break as Category 1 (if applicable).
- Type of repair (e.g., clamp, cut out, etc.).
- Pipe and repair parts disinfected.
- Post-repair Flushing undertaken (if applicable).
- For Category 2, where additional steps were required under 2.4.1 and 2.4.2, describe these steps.
- For Category 2 – Special Cases, include site-specific plan. If chlorine disinfection was used, indicate initial concentration, contact time, final concentration and final concentration as percentage of initial concentration.
- Disinfectant residual following final post-repair Flushing. If final disinfectant residual is less than 0.2 mg/L free chlorine in a chlorinated system or 1.0 mg/L combined chlorine in a chloraminated system, then provide the location and results of upstream disinfectant residual(s) or documented benchmarks for the area.
- Microbiological Samples taken (If applicable).
- Date and location(s) of sample(s) (e.g., Chain of custody).
- Date and time of return to normal service.
- Water Advisory declared (if applicable): Date and Time.
- Public Agency Notification (if applicable): local Ministry office (Date and Time).
- Public Agency Notification (if applicable): Spills Action Centre (Date and Time). Public Agency Notification/Direction (if applicable): local Medical Officer of Health (Date and Time).
Appendices
Appendix A: Examples of reduced pressure principle backflow preventer installations

Figure A-1: Temporary connection from a hydrant with Backflow Prevention using a CSA-certified reduced pressure principle backflow preventer.
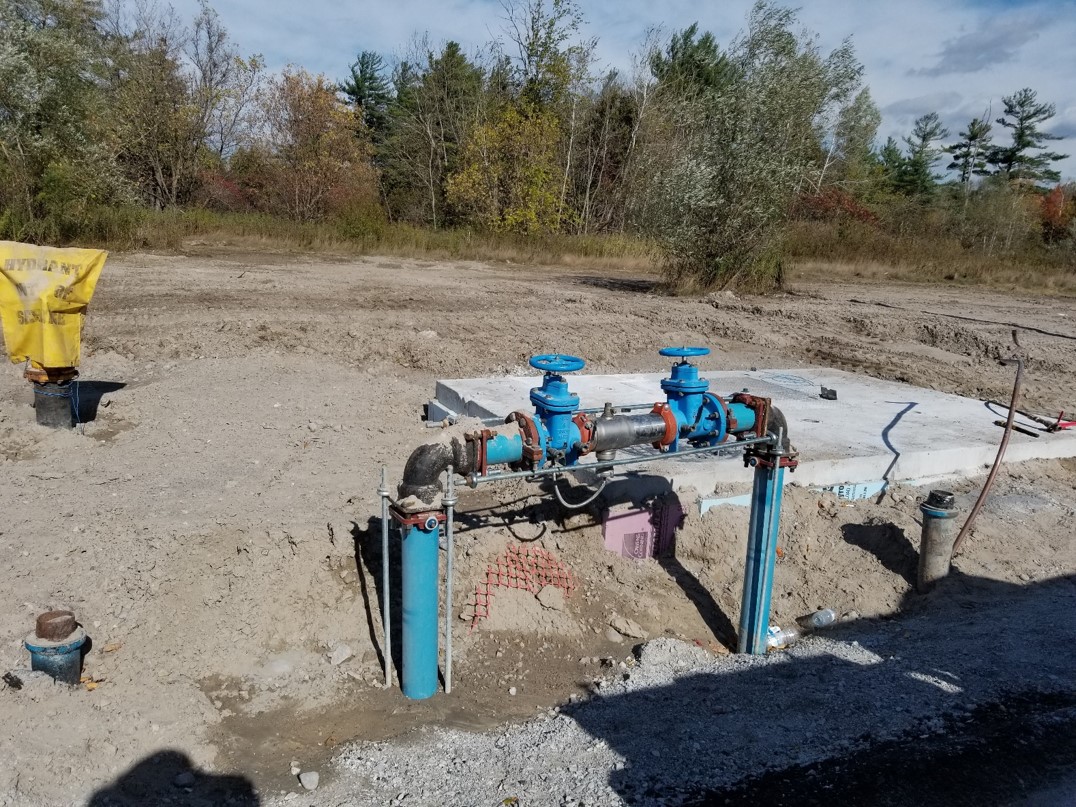
Figure A-2: Temporary connection from a watermain with Backflow Prevention using a CSA-certified reduced pressure principle backflow preventer.
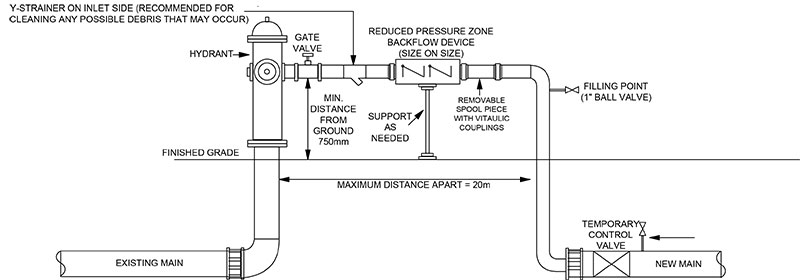
Figure A-3: Schematic of temporary connection from hydrant with Backflow Prevention using a CSA-certified reduced pressure principle backflow preventer.
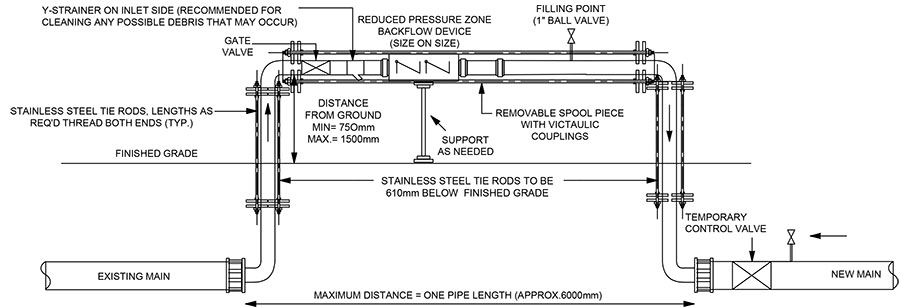
Figure A-4: Schematic of temporary connection from watermain with Backflow Prevention using a CSA-certified reduced pressure principle backflow preventer.
Appendix B: 1.1.4.2 Exception for Connections greater than one pipe length
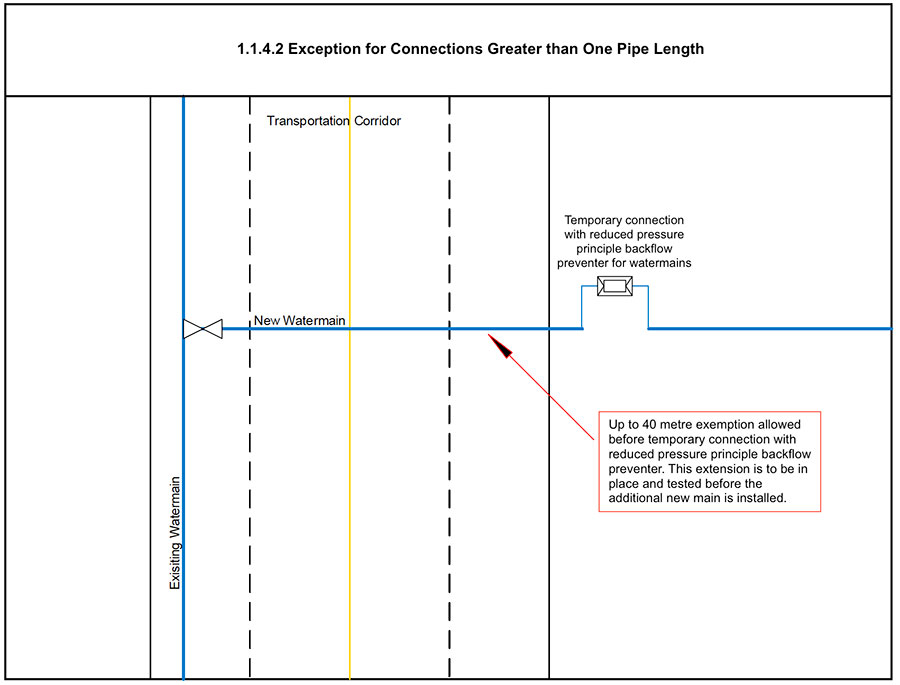
Figure B-1: Example of exception in Section 1.1.4.2. The figure shows an up to 40 metre exemption allowed before temporary connection with reduced pressure principle backflow preventer. This extension is to be in place and tested before the additional new main is installed.
Appendix C: Tools to help determine the category of watermain breaks—flowchart
The following flowchart will help determine the category of a watermain break.
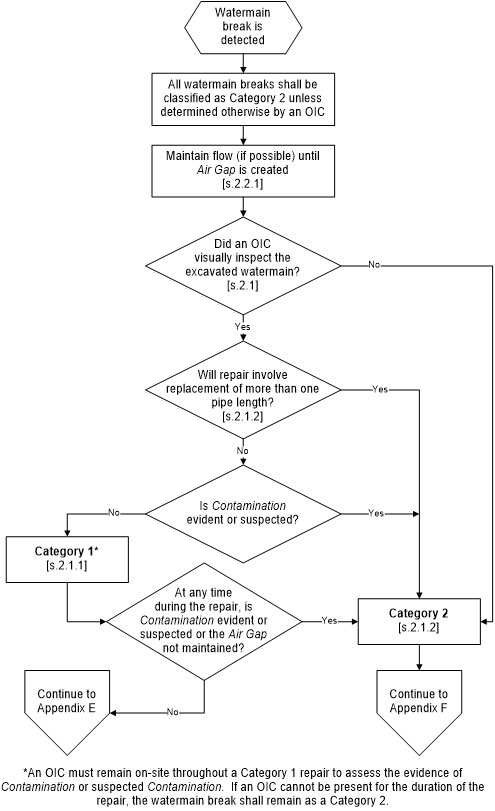
When a watermain break is detected:
Step 1: All watermain breaks shall be classified as Category 2 unless determined otherwise by an OIC.
Step 2: Maintain flow (if possible) until Air Gap is created. (Section 2.2.1)
Step 3: Did an OIC visually inspect the excavated watermain? (Section 2.1)
- If no, the break is Category 2 (Section 2.1.2). Continue to Appendix F.
- If yes, continue to Step 4.
Step 4: Will repair involve replacement of more than one pipe length? (Section 2.1.2)
- If yes, the break is Category 2 (Section 2.1.2). Continue to Appendix F.
- If no, continue to Step 5.
Step 5: Is Contamination evident or suspected?
- If yes, the break is Category 2 (Section 2.1.2). Continue to Appendix F.
- If no, the break is Category 1 (Section 2.1.1). Continue to Step 6. An OIC must remain on-site throughout a Category 1 repair to assess the evidence of Contamination or suspected Contamination. If an OIC cannot be present for the duration of the repair, the watermain break shall remain as a Category 2.
Step 6: At any time during the repair, is Contamination evident or suspected or the Air Gap not maintained?
- If yes, the break is Category 2 (Section 2.1.2). Continue to Appendix F.
If no, continue to Appendix E
Appendix D: Tools to help determine the category of watermain breaks—pictures
Examples of watermain breaks that are typical of Category 1 are included below for illustrative purposes only:
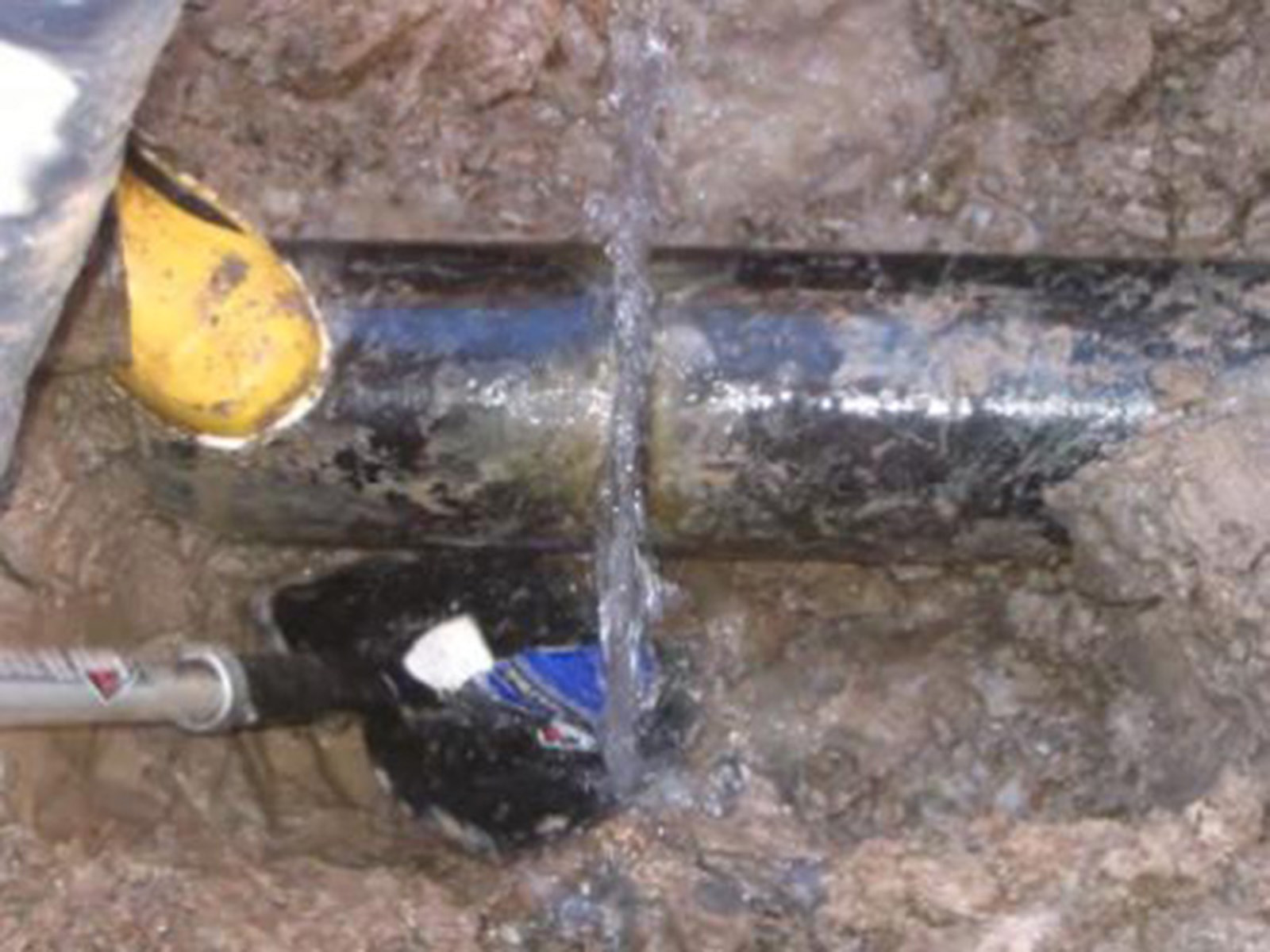
Figure D-1: Circumferential watermain break with flow maintained until after an Air Gap was established.
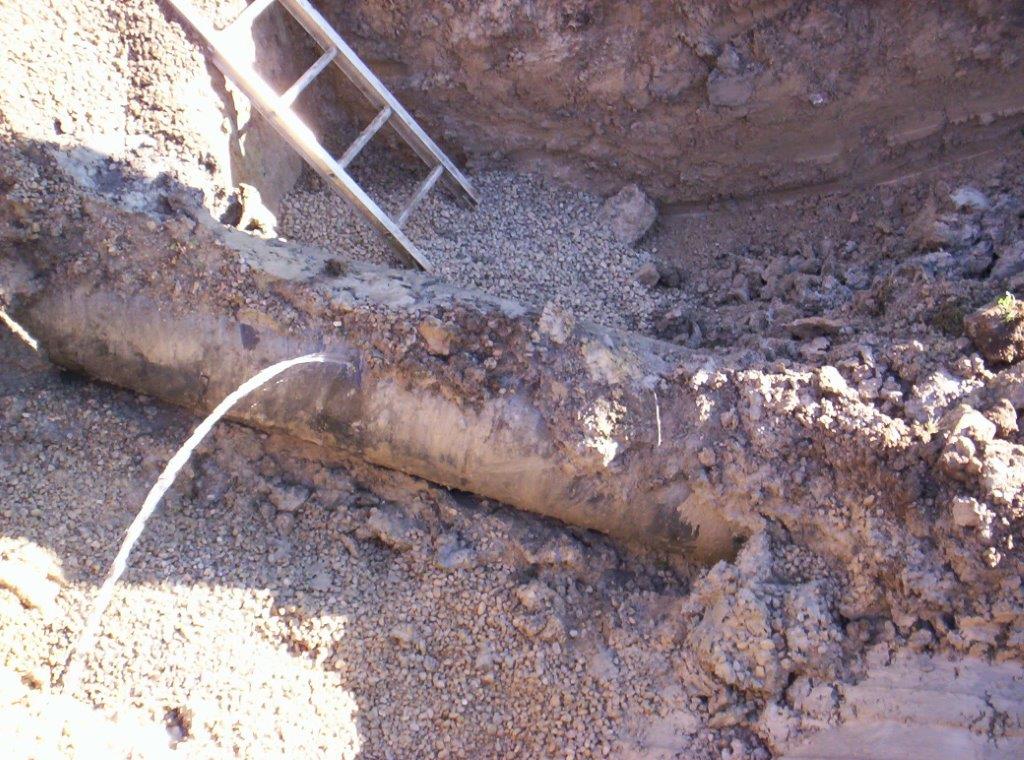
Figure D-2: Corrosion hole leak in a watermain with flow maintained until after an Air Gap was established.
Examples of watermain breaks that are typical of Category 2 are included below for illustrative purposes only:

Figure D-3: Longitudinal watermain break with evident Contamination.
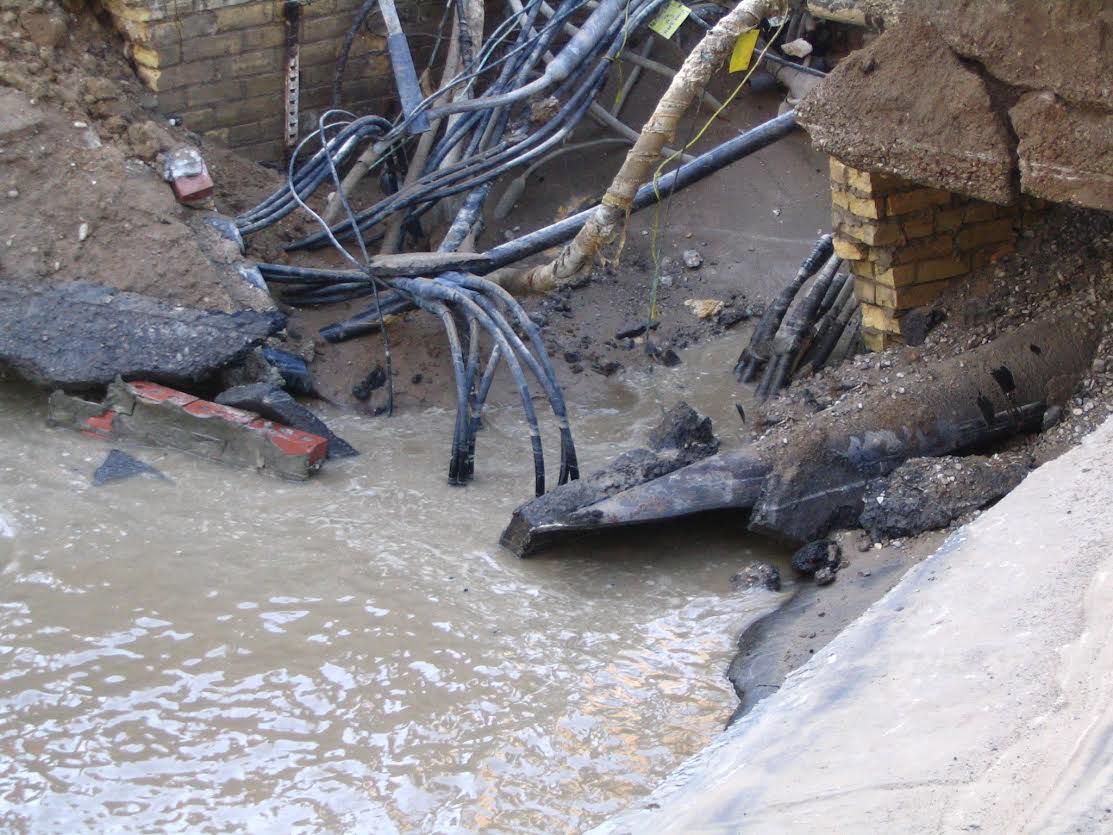
Figure D-4: Spiral watermain break with evident Contamination.
Appendix E: Category 1 flowchart
The following flowchart is an example of the typical steps required for Category 1 watermain breaks. Note: These steps also apply to the planned maintenance of watermain Appurtenances and fittings (refer to Section 1.4). Any additional directions given by the Ministry and/or the local Medical Officer of Health must be followed.
Category 1 (continued from Appendix C):
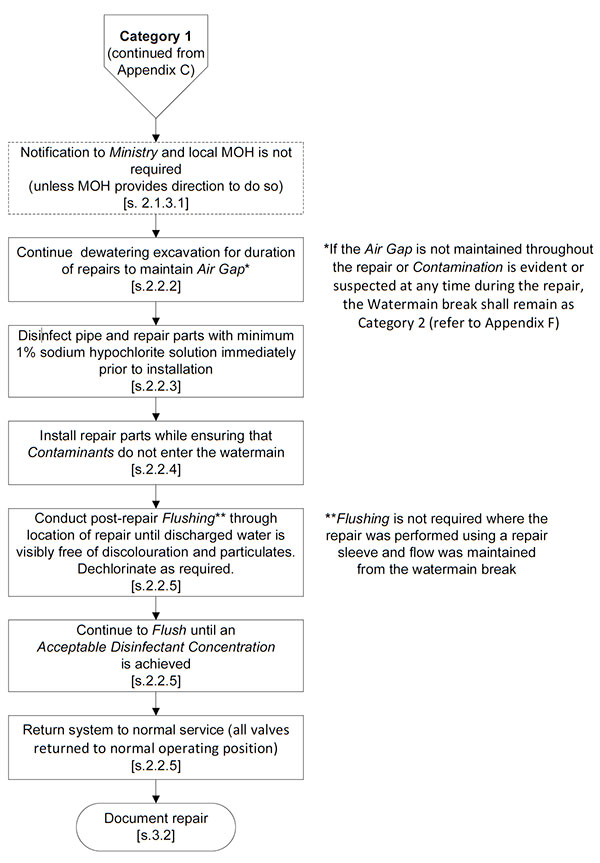
Steps required for Category 1 watermain breaks.
Step 1: Notification to Ministry and local MOH is not required (unless MOH provides direction to do so). (Section 2.1.3.1)
Step 2: Continue dewatering excavation for duration of repairs to maintain Air Gap (Section 2.2.2). If the Air Gap is not maintained throughout the repair or Contamination is evident or suspected at any time during the repair, the Watermain break shall remain as Category 2 (refer to Appendix F).
Step 3: Disinfect pipe and repair parts with minimum 1% sodium hypochlorite solution immediately prior to installation. (Section 2.2.3)
Step 4: Install repair parts while ensuring that Contaminants do not enter the watermain. (Section 2.2.4)
Step 5: Conduct post-repair Flushing through location of repair until discharged water is visibly free of discolouration and particulates. Dechlorinate is required. (Section 2.2.5). Flushing is not required where repair was performed using a repair sleeve and flow was maintained from the watermain break.
Step 6: Continue to Flush until an Acceptable Disinfectant Concentration is achieved. (Section 2.2.5)
Step 7: Return system to normal service (all valves returned to normal operating position). (Section 2.2.5)
Step 8: Document repair. (Section 3.2)
Appendix F: Category 2 flowchart
The following flowchart is an example of the typical steps required for Category 2 watermain breaks. Note: The sequence of actions may be varied as appropriate for the specific situation. Any additional directions given by the Ministry and/or the local Medical Officer of Health must be followed.
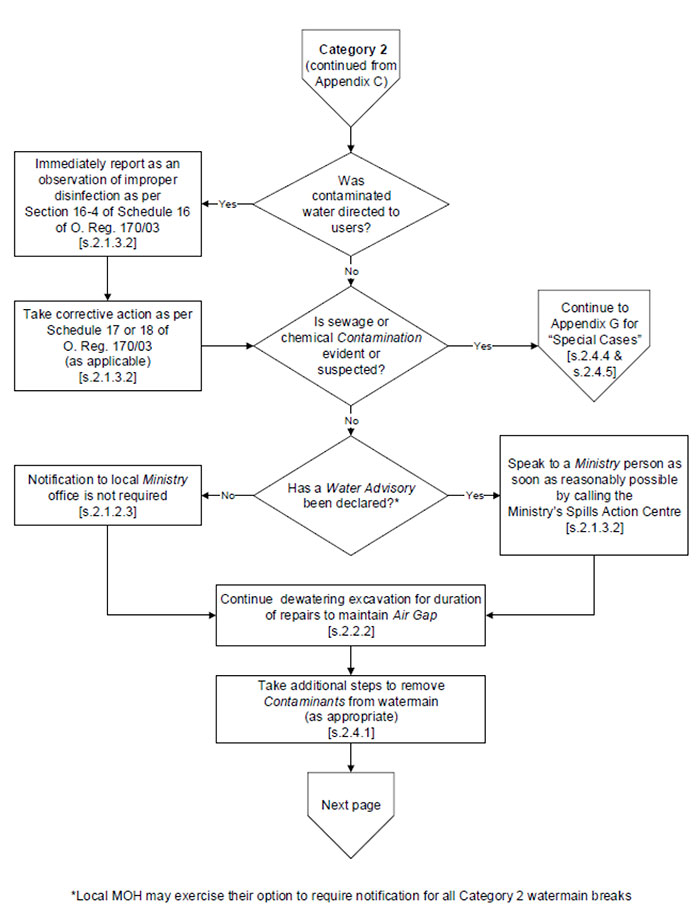
Steps required for Category 2 watermain breaks.
Category 2 (continued from Appendix C):
Step 1: Was contaminated water directed to users?
- If yes, immediately report as an observation of improper disinfection as per Section 16-4 of Schedule 16 of O. Reg. 170/03> (Section 2.1.3.2). Take corrective action as per Schedule 17 or 18 of O. Reg. 170/03 (as applicable). (Section 2.1.3.2). Continue to Step 2.
- If no, continue to Step 2.
Step 2: Is sewage or chemical Contamination evident or suspected?
- If yes, continue to Appendix G for Special Cases. (Section 2.4.4. and 2.4.5.)
- If no, continue to Step 3.
Step 3: Has a Water Advisory been declared? Local MOH may exercise their option to require notification for all Category 2 watermain breaks.
- If yes, speak to a Ministry person as soon as reasonably possible by calling the Ministry’s Spills Action Centre. (Section 2.1.3.2). Continue to Step 4.
- If no, notification to local Ministry office is not required. (Section 2.1.2.3). Continue to Step 4.
Step 4: Continue dewatering excavation for duration of repairs to maintain Air Gap. (Section 2.2.2)
Step 5: Take additional steps to remove Contaminants from watermain (as appropriate). (Section 2.4.1)
Step 6: Disinfect pipe and repair parts with minimum 1% sodium hypochlorite solution immediately prior to installation. (Section 2.2.3)
Step 7: Use additional disinfection procedures as appropriate. (Section 2.4.2)
Step 8: Install repair parts while ensuring that Contaminants do not enter the watermain. (Section 3.2.4)
Step 9: Conduct post-repair Flushing through location of repair until discharged water is visibly free of discolouration and particulates. Dechlorinate as required. (Section 2.2.5). Flushing is not required where the repair was performed using a repair sleeve and flow was maintained from the watermain break.
Step 10: Continue to Flush until an Acceptable Disinfectant Concentration is achieved. (Section 2.2.5)
Step 11: Take at least one Microbiological Sample of water that passed through location of repair. (Section 2.4.3)
Step 12: Prior to receipt of sample results, system may be returned to normal service (all valves returned to normal operating position). (Section 2.4.3)
Step 13: Document repair. (Section 3.2)
Appendix G: Special case flowchart
The following flowchart depicts the requirements for special case Contamination (sewage or chemical) as a result of a watermain break.
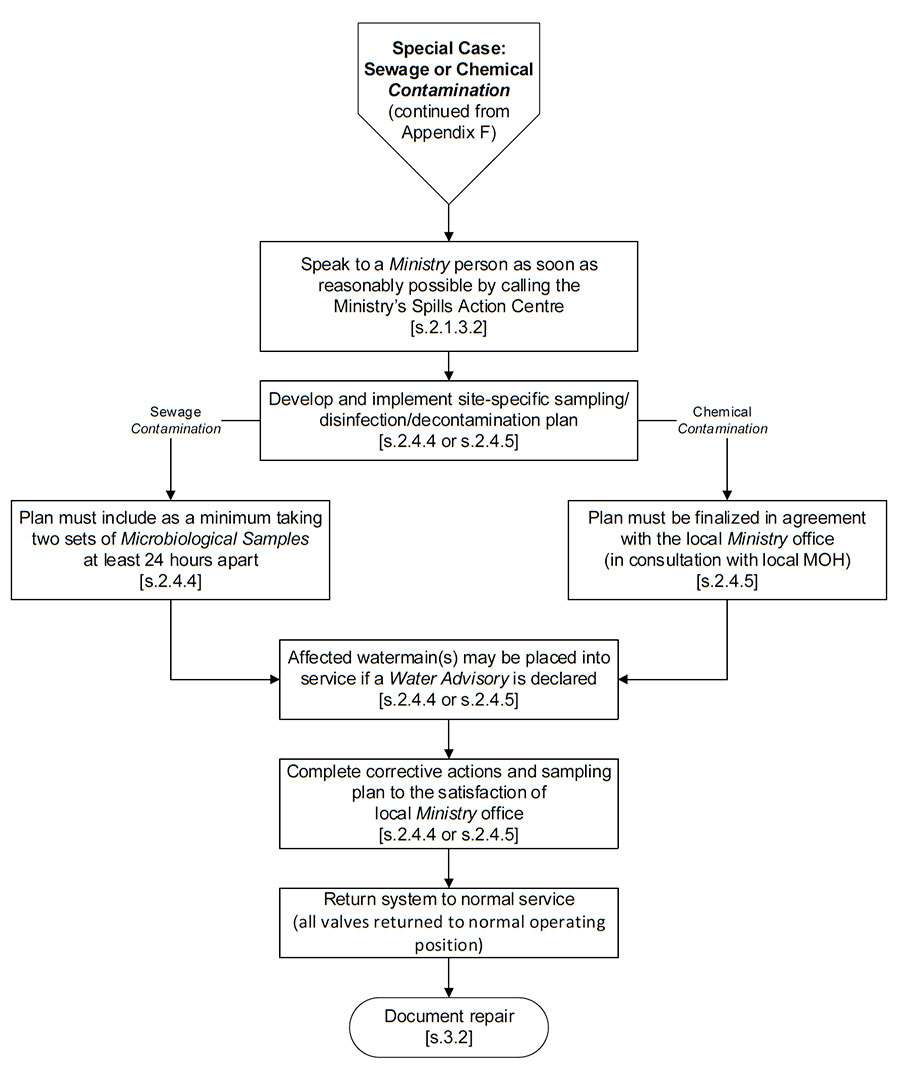
Special case: sewage or chemical Contamination (continued from Appendix F):
Step 1: Speak to a Ministry person as soon as reasonably possible by calling the Ministry’s Spills Action Centre. (Section 2.1.3.2)
Step 2: Develop and implement site-specific sampling/disinfection/decontamination plan. (Section 2.4.4 or section 2.4.5)
Step 3: Sewage Contamination or Chemical Contamination?
- If sewage Contamination, plan must include as a minimum taking two sets of Microbiological Samples at least 24 hours apart. (Section 2.4.4)
- If chemical Contamination, plan must be finalized in agreement with local Ministry office (in consultation with local MOH). (Section 2.4.5)
Step 4: Affected watermain(s) may be placed into service if a Water Advisory is declared. (Section 2.4.4 or section 2.4.5)
Step 5: Complete corrective actions and sampling plan to the satisfaction of local Ministry office. (Section 2.4.4 or section 2.4.5)
Step 6: Return system to normal service (all valves returned to normal operating position).
Step 7: Document repair. (Section 3.2)
Appendix H: Definitions
In this procedure,
- Acceptable Disinfectant Concentration
- means:
- a disinfectant concentration of at least 0.2 mg/L free chlorine residual in a chlorinated system or 1.0 mg/L combined chlorine residual in a chloraminated system; or, if these disinfectant concentrations cannot be achieved,
- a disinfectant concentration that is representative of the residual in the area, determined by testing upstream and downstream from the testing location or by using documented benchmarks for the area, as long as free chlorine concentrations are at least 0.05 mg/L in a chlorinated system and combined chlorine concentrations are at least 0.25 mg/L in a chloraminated system.
- Air Gap
- means a space at the location of the maintenance/repair between the exterior surface of the watermain and the interior surfaces of the excavation, including the water in the excavation, sufficient to prevent water, soil or any other Contaminant in the excavation from contacting the watermain, fittings, or Appurtenances throughout the maintenance/repair process.
- Appurtenance
- means an appurtenance, within the meaning of O. Reg. 170/03, which is in contact with the Drinking Water.
- Backflow Prevention
- means the prevention of a reversal of normal flow that could introduce Contamination to the Drinking Water System.
- Certified Operator
- means certified operator within the meaning of O. Reg. 170/03.
- Connection
- means all watermain and Appurtenances installed between an existing watermain and a new or future watermain/Appurtenance.
- Contaminant
- means foreign matter that is not intended to enter a watermain.
- Contamination
- means the introduction of a Contaminant into a watermain.
- Directly Supervised
- means directly supervised within the meaning of Section 5.1.1 of the Certification Guide for Operators and Water Quality Analysts of Drinking Water Systems, as amended, but it does not expressly refer to the definition of supervisor under the Occupational Health and Safety Act.
- Drinking Water
- means drinking water within the meaning of the Safe Drinking Water Act.
- Drinking Water Health Hazard
- means drinking water health hazard within the meaning of the Safe Drinking Water Act.
- Drinking Water System
- means drinking water system within the meaning of the Safe Drinking Water Act.
- Flushing
- means flowing water through a section of watermain/appurtenances and out of the system until the water appears visibly free from discoloration and particulates with an Acceptable Disinfectant Concentration. This definition does not include recharging a watermain.
- Higher Velocity Flushing
- means flushing of a watermain with sufficient velocity to discharge settled materials.
- Isolate
- means operate valves to ensure that there is no flow of water to or from a specific section of watermain.
- Microbiological Samples
- means water samples taken and tested for Escherichia coli and Total Coliforms by a licensed and accredited laboratory.
- Ministry
- means the Ministry of the Environment, Conservation and Parks.
- Operator-in-Charge
- means an operator-in-charge within the meaning of O. Reg. 128/04.
- Service Pipe
- means a service pipe within the meaning of O. Reg. 170/03.
- Water Advisory
- means a boil or drinking water advisory for the area being serviced by the affected watermains declared by the local Medical Officer of Health.
- Water Quality Analyst
- means a water quality analyst within the meaning of O. Reg. 128/04.