Gérer les émissions de poussière produites par les systèmes de manutention du grain à la ferme
Renseignez-vous sur les principales sources de poussière de grain et les possibilités de réduire la production de poussière et la poussière en suspension produite par les systèmes de manutention du grain à la ferme. Ces renseignements techniques sont destinés aux producteurs de l’Ontario.
ISSN 1198-7138, Publié juin 2020
Introduction
Le séchage, la manutention et l’entreposage du grain sont indispensables au secteur agricole de l’Ontario. Le nombre et les dimensions des systèmes de manutention du grain à la ferme continuent d’augmenter, permettant ainsi aux agriculteurs d’entreposer et de commercialiser par eux-mêmes de plus grandes quantités de grain. Les systèmes de manutention du grain peuvent cependant produire d’importantes émissions de poussière.
Une présence excessive de poussière peut causer des problèmes de nuisance, susceptibles d’entraîner des plaintes de la part des résidents et des entreprises à proximité. La poussière constitue aussi un risque pour la sécurité ainsi qu’un danger d’incendie. De plus, étant donné que les grains sont vendus au poids, la présence excessive de poussière représente un véritable gaspillage d’argent.
Chaque composante d’un système de manutention du grain peut être modifiée en vue de réduire ou d’éliminer la production et les émissions de poussière. La réduction de poussière améliorera la sécurité et la propreté de l’installation, diminuera les risques de plaintes et haussera la rentabilité de l’exploitation en laissant la poussière où elle doit être, c’est-à-dire dans le grain!
La présente fiche technique porte sur les principales sources de poussière de grain et décrit les moyens existants de réduire la production et les émissions de poussière générées par les systèmes de manutention du grain à la ferme.
Sources des émissions de poussière de grain
Les émissions de poussière de grain indésirables sont faites de fines particules rougeâtres (appelées « red dog » ou « bee’s wings » en anglais), de glumes issues des grains et de poussières provenant des champs.
Les fines poussières rougeâtres se détachent des rafles de maïs sous forme de paillettes (figure 1) relativement grossières et légères, ce qui les rend très difficiles à ramasser et à nettoyer. Ces émissions de poussière sont parfois surnommées « émissions de poussière diffuses », ce qui signifie que la poussière provient de plusieurs sources plutôt que d’une seule. La quantité de poussière produite varie selon la qualité des grains, leur teneur en eau, les conditions à la récolte, les méthodes de manutention utilisées et la configuration du séchoir et du système de manutention.
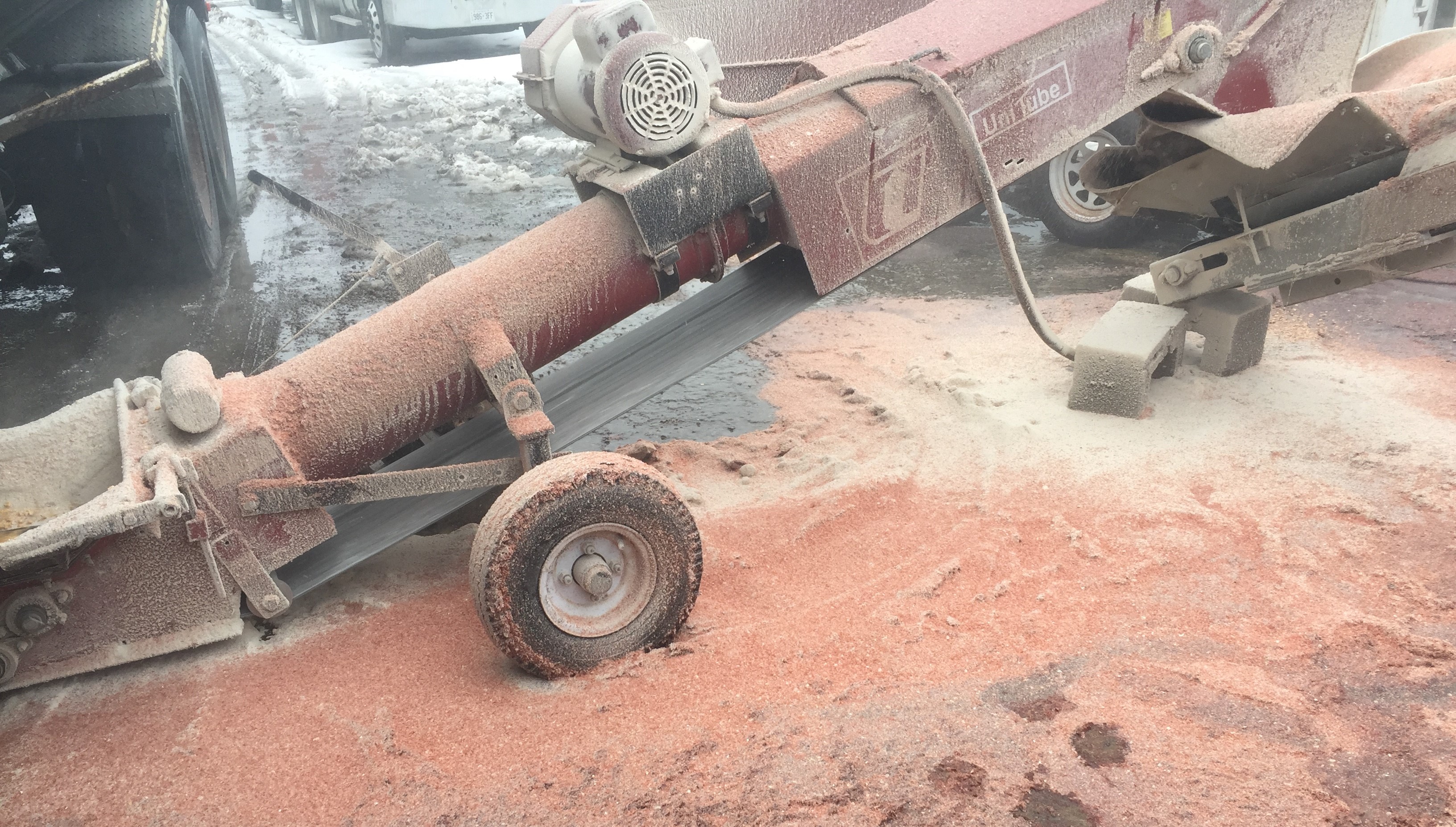
La plupart des émissions de poussière sont produites durant la saison de la récolte, au moment où la majorité des opérations de séchage et de manutention ont lieu. Toutefois, la poussière peut se dégager chaque fois qu’on déplace du grain. Les émissions de poussière réduisent le poids des grains et puisque ces derniers sont vendus au poids, elles réduisent donc les profits des agriculteurs. La figure 2 montre les principales sources d’émissions de poussière générées par les systèmes de manutention du grain à la ferme.
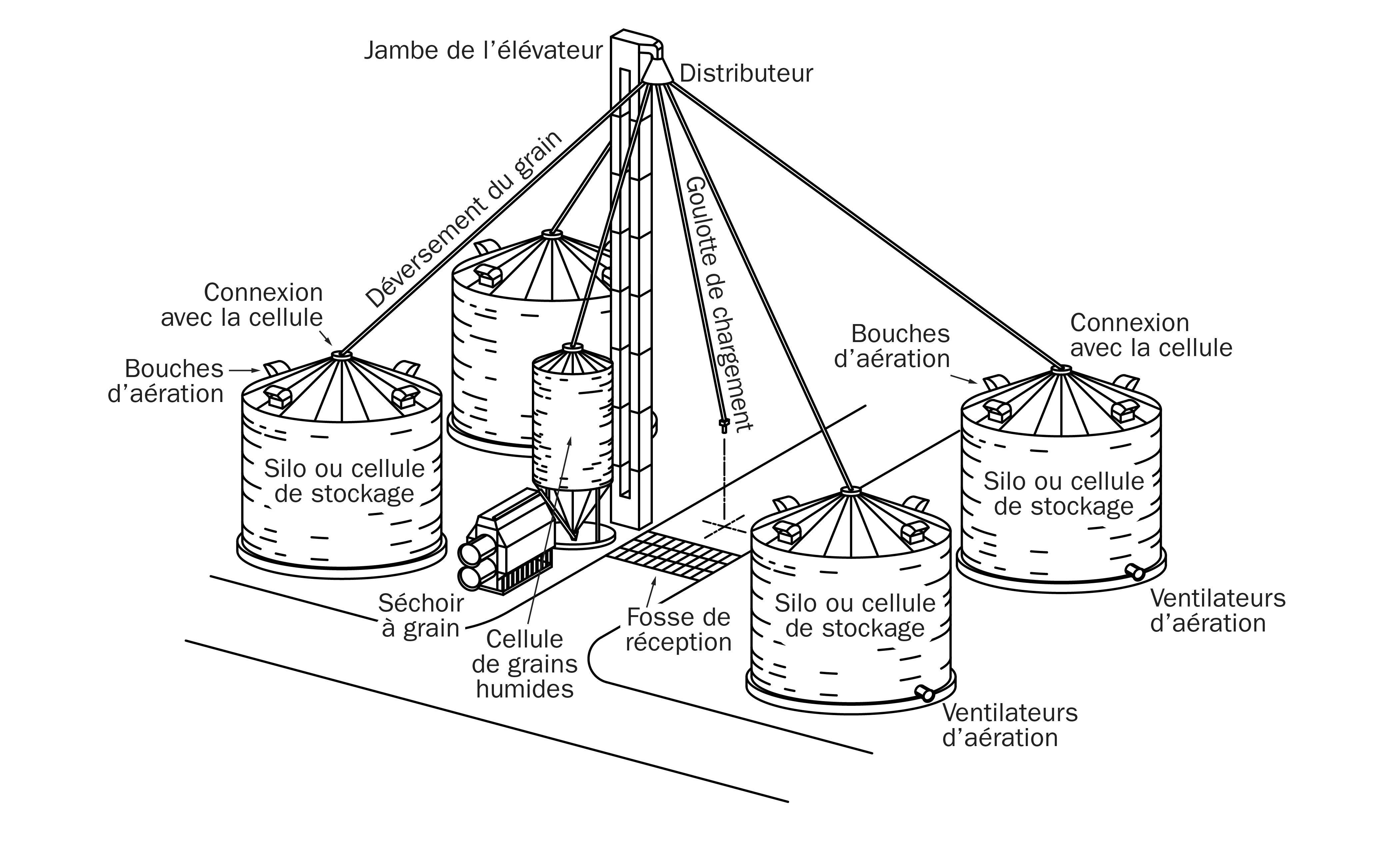
Les opérations de réception et d’expédition du grain sont à l’origine de 80 à 90 % des poussières produites par une installation de manutention du grain. Les grains sont normalement déchargés des camions dans une fosse de réception et chargés dans les camions du haut d’une vis à grain ou d’une goulotte (ou souffleuse). Durant le chargement et le déchargement, l’air se déplace vers l’extérieur de la fosse ou du camion et transporte la poussière. De la poussière est dégagée aussi lorsque le grain tombe de la goulotte ou du camion.
La jambe de l’élévateur et le système de convoyeurs permettent le déplacement des grains entre les fosses de réception, les cellules ou silos de stockage et les camions à l’aide de convoyeurs, de la jambe de l’élévateur et de vis à grains reliés entre eux. De petits fragments de grain et de poussière se dégagent des grains qui entrent en contact entre eux et contre le convoyeur ou la vis à grain ou les conduites. La poussière s’échappe à divers points de déversement quand les grains tombent dans le système de convoyeurs ou à l’extérieur de celui-ci, et à partir de joints non étanches le long du système.
Les séchoirs à grain sont pourvus de gros ventilateurs qui déplacent de grandes quantités d’air et génèrent jusqu’à 10 % de la poussière produite dans une installation de manutention du grain. La configuration des systèmes de sortie d’air diffère selon les séchoirs (p. ex. bouche d’air unique, bouches d’air multiples, avec ou sans grille), ce qui influe sur la quantité de poussière émise.
Les cellules de stockage et les silos doivent être ventilés (aérés) afin de garder le grain au sec et en bon état. Toutefois, l’aération déplace la poussière à travers les bouches d’aération de la cellule ou du silo. L’air chargé de poussière est aussi déplacé à l’extérieur des bouches d’aération au moment du remplissage du silo. Les émissions de poussière augmentent si le grain est transféré plus fréquemment. Les silos et les cellules de stockage génèrent jusqu’à 10 % des émissions de poussière d’une installation de manutention du grain.
Réduire la poussière à la source
Le moyen le plus efficace de réduire les émissions est d’empêcher au départ la production de poussière. Toute opération se déroulant dans un élévateur à grain à la ferme peut être modifiée en vue de réduire ou d’éliminer la production de poussière, et bon nombre de méthodes pour y parvenir ne coûtent que du temps à l’exploitant.
Choix de l’emplacement du système
L’emplacement d’un système de manutention du grain peut avoir un effet majeur sur la production de poussière.
- Installer l’élévateur à l’écart de lieux sensibles (comme la proximité de résidences ou d’entreprises), à un endroit où la direction et la vitesse des vents dominants ne risquent pas d’aggraver un problème dû à la poussière.
- Installer les séchoirs ainsi que les zones de chargement et de déchargement sur le côté face au vent des silos ou des autres bâtiments pour qu’ils agissent comme tampons et empêchent la poussière d’être transportée par le vent.
- Éviter de placer les séchoirs ainsi que les zones de chargement et de déchargement entre les rangées des silos ou des cellules de stockage. Cela pourrait créer un effet de soufflerie aggravant les problèmes de poussière.
Dans le cas des installations existantes, il n’est habituellement pas pratique de modifier l’emplacement du système. Si l’occasion se présente, on peut cependant reconfigurer le système avec l’objectif de réduire la poussière, comme dans le cadre de l’achat d’une nouvelle cellule de stockage ou d’un séchoir à grain.
Entretien général
Recourir à de bonnes pratiques d’entretien général autour de l’élévateur afin de prévenir les accumulations de poussière, lesquelles risquent davantage de se disperser à l’extérieur du site et de créer des problèmes. Les excès de poussière représentent également un risque d’incendie.
- Recouvrir tous les camions et les wagons ouverts.
- Conduire lentement; poser des affiches de limites de vitesse et faire respecter ces dernières.
- Humidifier les voies d’accès afin de limiter la production de poussière.
- Asphalter les voies d’accès et les cours, si possible.
- Balayer et nettoyer chaque jour toute accumulation de poussière.
- Utiliser du matériel électrique étanche approprié aux milieux poussiéreux afin de minimiser les risques d’incendie.
- Porter un masque filtrant approuvé et de l’équipement de protection individuelle dans les endroits poussiéreux afin de se protéger.
Réception et expédition du grain
Limiter les émissions de poussière au cours de la réception et de l’expédition du grain en réduisant la distance de chute des grains durant le déchargement :
- Placer les goulottes de déchargement au plus bas et le plus près possible de la fosse de réception.
- Laisser le grain former un cône autour de la grille de réception au moment du déchargement (formant une sorte de goulot d’étranglement, voir figure 3) afin de réduire jusqu’à 90 % de la production de poussière.
- Laisser les convoyeurs et les vis à grain fermés jusqu’à ce que la fosse de réception soit pleine pour favoriser la formation d’un goulot d’étranglement qui ralentit la chute du grain. Transférer les grains plus lentement quand la fosse ou le camion est partiellement ou complètement vide.
- Éviter ou limiter les opérations par temps venteux, surtout quand le vent souffle en direction d’emplacements adjacents vulnérables.
- Installer des jupes anti-poussière ou des goulottes rétractables sur les goulottes de déchargement, qui se prolongent d’au moins 15 cm (6 po) sous les côtés de la fosse de réception ou du camion, si possible.
- Poser des boîtes d’amortissement sur les goulottes de déchargement afin de ralentir la chute du grain.
- Utiliser un nettoyeur à grain afin de retirer les particules fines et la poussière des grains à la réception ou avant l’expédition.
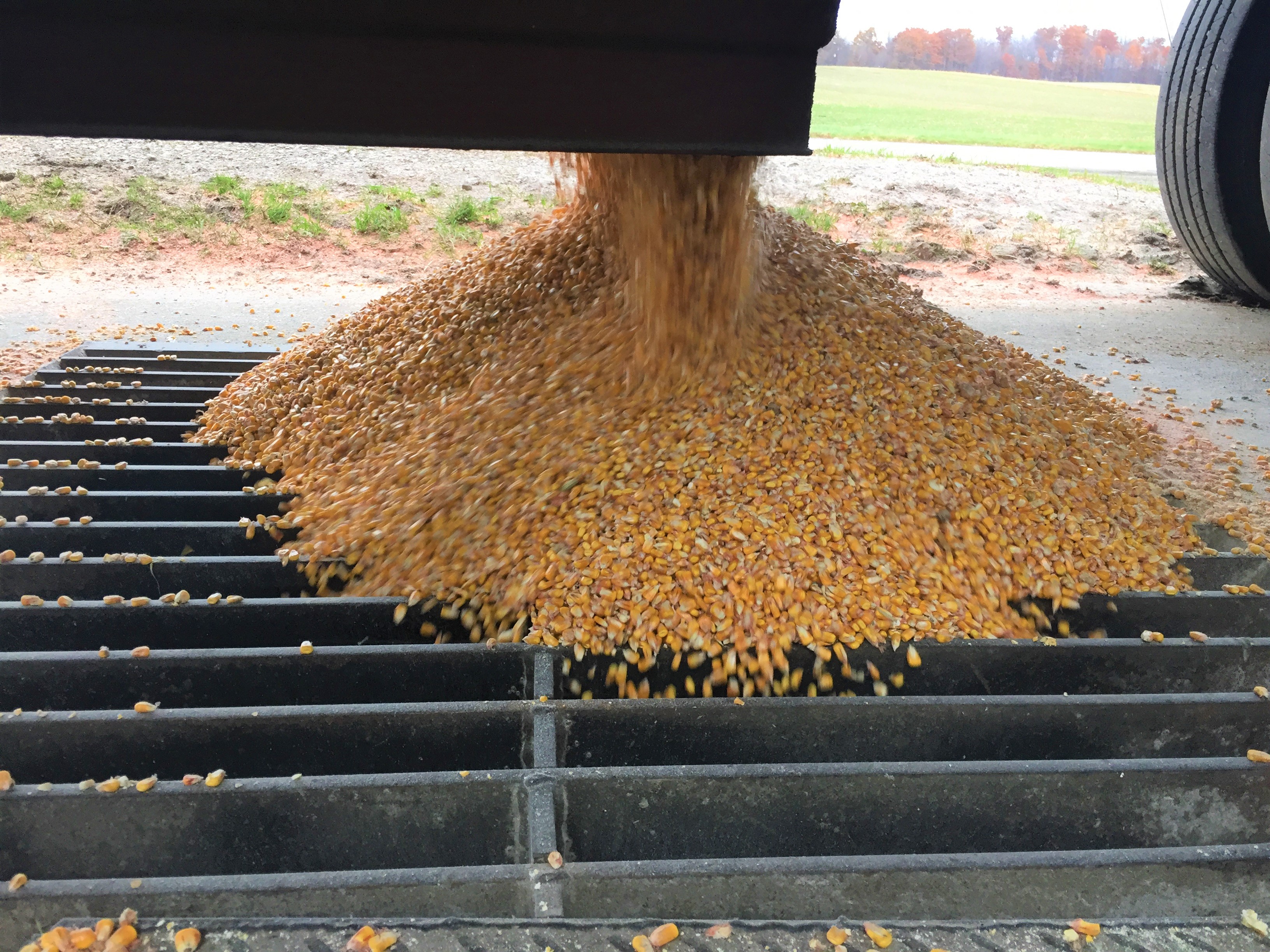
Jambe de l’élévateur et convoyeurs
Un système de manutention du grain bien entretenu ne devrait produire que peu de poussière :
- S’assurer que tout le matériel servant à déplacer le grain est entièrement étanche.
- Garder toutes les connexions aux goulottes et aux autres pièces d’équipement étanches et protégées contre la poussière.
- Garder les élévateurs, les vis ou les conduites à grains exempts d’extrémités pointues afin de réduire au minimum les dommages aux grains.
- Réduire au minimum le transfert de grain à l’air libre.
- Faire fonctionner tout le matériel servant au déplacement du grain le plus lentement possible.
- Faire fonctionner les vis à grain et le matériel de déplacement du grain lorsqu’ils sont tout à fait pleins. Les systèmes de transfert à moitié vides produisent beaucoup plus de poussière.
Le grain chargé ou déchargé à grande vitesse risque davantage de se rompre, ce qui produit une plus grande quantité de particules fines et de poussière. Placer toutes les goulottes à un angle approprié afin d’éviter que le grain se déverse trop rapidement. Installer le long du système des dispositifs spéciaux (boîtes d’amortissement) à intervalles réguliers qui permettent de réduire la vitesse de chute des grains dans les goulottes en pente abrupte.
Consulter la figure 4 pour vérifier s’il est nécessaire de mettre en place des dispositifs pour ralentir la chute des grains. Mesurer les distances de déversement horizontale et verticale parcourues durant la chute et utiliser ces mesures pour trouver l’angle approprié sur le graphique. Repérer l’endroit où la ligne correspondant à l’angle trouvé croise la « zone optimale ». Utiliser les lignes courbées sur le graphique pour trouver la longueur de la goulotte qui est recommandée pour l’installation des dispositifs servant à ralentir la vitesse de déversement des grains. Ainsi, une goulotte dont la distance horizontale est de 15 m (49 pi) et la distance verticale est de 18 m (60 pi) doit être installée à un angle d’environ 50°. La ligne correspondant à un angle de 50° traverse la « zone optimale » à 10 m (33 pi) de longueur de goulotte. Donc, pour cette goulotte, les dispositifs pour ralentir la chute des grains devraient être installés aux 10 m (33 pi).
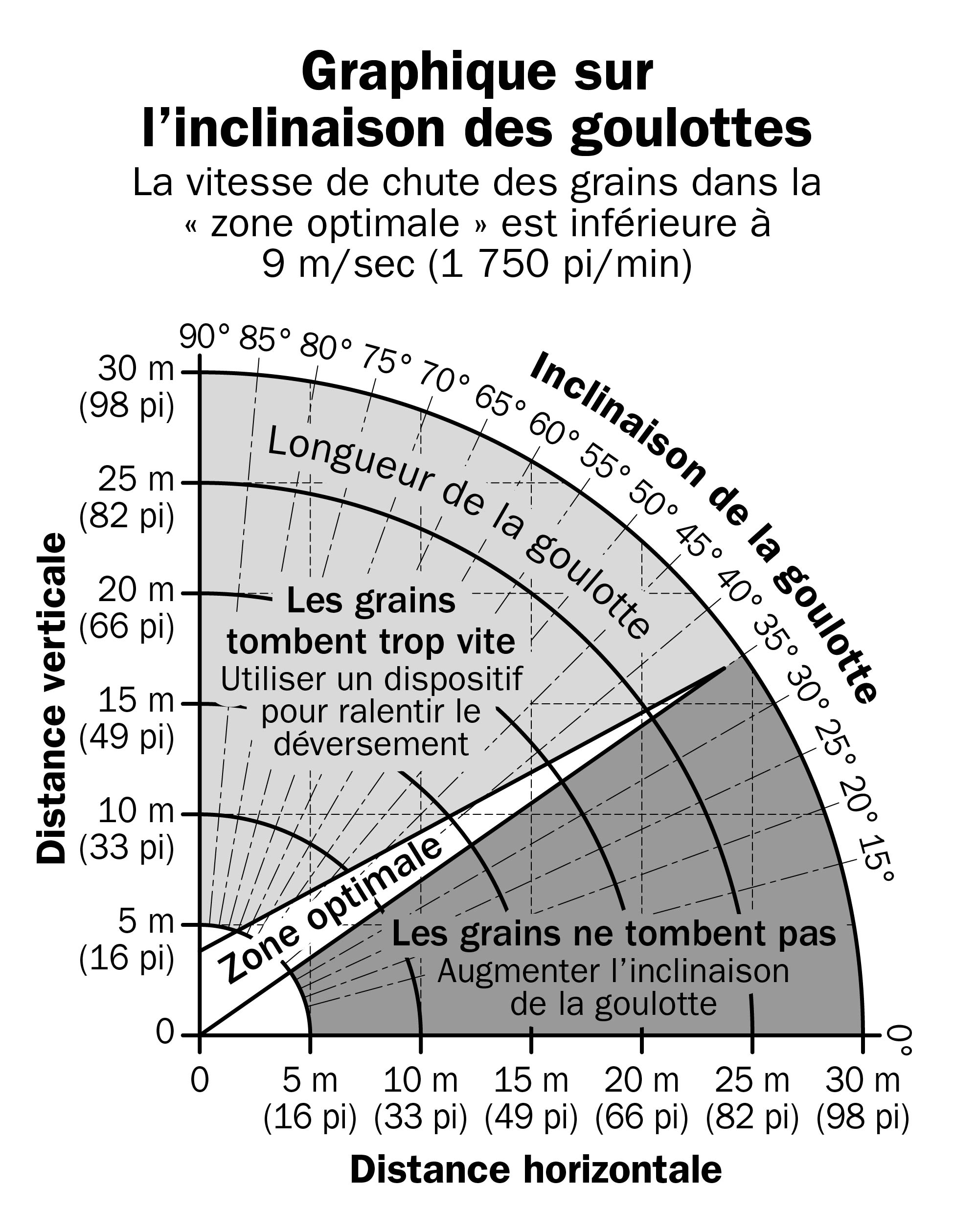
Dans une goulotte dont l’inclinaison est supérieure à 45°, placer des dispositifs aux 10 m (33 pi) ou moins pour ralentir la chute des grains, afin que les grains se déversent lentement. Dans le cas d’une goulotte dont l’inclinaison est supérieure à 70°, placer ces dispositifs aux 5 m (16 pi) ou moins.
Séchoirs à grain
Il est très important de gérer attentivement tout ce qui concerne les séchoirs à grain afin de parvenir à réduire les émissions de poussière qui leur sont associées :
- Dans le cas des séchoirs grillagés, utiliser le plus petit maillage possible afin de réduire les émissions de poussière.
- Le moyen le plus efficace de limiter l’accumulation de poussière est de laver, entretenir et nettoyer régulièrement le séchoir et ses environs.
Silos et cellules de stockage
La majorité de la poussière est produite au moment où les grains sont chargés dans la structure d’entreposage ou en sont déchargés.
- Charger les grains dans les silos et les décharger hors de ceux-ci le plus lentement possible.
- Placer des boîtes d’amortissement dans les goulottes dans le haut du silo ou de la cellule, afin de réduire la vitesse de chute des grains qui y pénètrent.
- Ne pas faire fonctionner les ventilateurs d’aération durant le transfert du grain, afin de minimiser les émissions de poussière.
Réduire les émissions de poussière
Malgré toutes les mesures que l’on peut prendre et l’argent qu’on peut investir, il y aura toujours de la poussière qui se dégagera durant la manutention des grains. Mettre en place des mesures d’atténuation autour de l’élévateur afin de capter et de retenir la poussière produite avant qu’elle ne se dissémine à l’extérieur du site.
Brise-vents
Les brise-vents peuvent empêcher la poussière d’être transportée par l’air. Planter des arbres de manière à former des brise-vents, à la fois du côté d’où souffle le vent (afin d’empêcher que la poussière soit happée par le vent) et sous le vent (afin d’empêcher que l’air chargé de poussière s’échappe de la ferme). Les arbres prennent du temps à pousser, d’où l’importance d’une bonne planification! Pour plus d’information à ce sujet, consulter le fascicule du MAAARO, Brise-vents dans les champs, de la série intitulée Les pratiques de gestion optimales (no de commande AF168), à ontario.ca.
On peut aussi envisager de construire de nouvelles cellules de stockage/silos ou d’autres bâtiments qui agiront comme brise-vents autour d’un élévateur existant.
Aires de réception et d’expédition du grain
- Installer des déflecteurs agissant par gravité sur les fosses de réception, qui s’ouvrent uniquement au passage du grain.
- Recouvrir et délimiter les aires de réception et d’expédition du grain sur au moins trois côtés. Un hangar d’accès à sens unique dont les portes aux deux extrémités sont fermées empêche la poussière de s’échapper. Un hangar sans portes (ou dont les portes sont toujours ouvertes) pourrait provoquer un effet tunnel et aggraver le problème.
- Utiliser des rideaux ou des barrières temporaires afin de protéger les environs des aires de réception et d’expédition, s’il est impossible de les recouvrir de manière permanente.
- Porter des masques respirateurs et de l’équipement de protection individuelle dans les endroits confinés, à des fins de protection de la santé.
- Nettoyer les aires confinées afin de minimiser les risques d’incendie liés à l’accumulation de poussière.
- Installer des dispositifs de dépoussiérage sur les fosses de réception, qui permettent de pousser la poussière vers le bas au lieu de lui permettre de s’échapper.
Jambe de l’élévateur et système de convoyeurs
- Reconfigurer si possible le système de transfert du grain de manière à réduire les émissions de poussière.
- Installer les goulottes selon une inclinaison peu prononcée ou mettre en place des boîtes d’amortissement additionnelles, au besoin, afin de réduire la vitesse de chute du grain (figure 4).
- Délimiter tous les points de transfert (p. ex. le haut de l’élévateur) ainsi que les zones importantes de production ou d’échappement de poussière.
Séchoirs à grain
- Mettre en place des conduites de dépoussiérage ainsi que des filtres cycloniques, afin de capter la poussière au moment où elle pénètre dans le séchoir (figure 5).
- On peut, dans certains types de séchoirs, ajouter des filtres dans les bouches d’air afin de capter la poussière qui s’échappe avec l’air sortant.
- Certains types de séchoirs peuvent être en milieu clos, ce qui peut faciliter la rétention des particules fines. Toutefois, cela peut aussi accroître les risques d’incendie. Les séchoirs peuvent être placés en milieu clos seulement si le fabricant et les autorités locales l’autorisent. Il est alors important de respecter tous les codes et règlements relatifs à la sécurité.
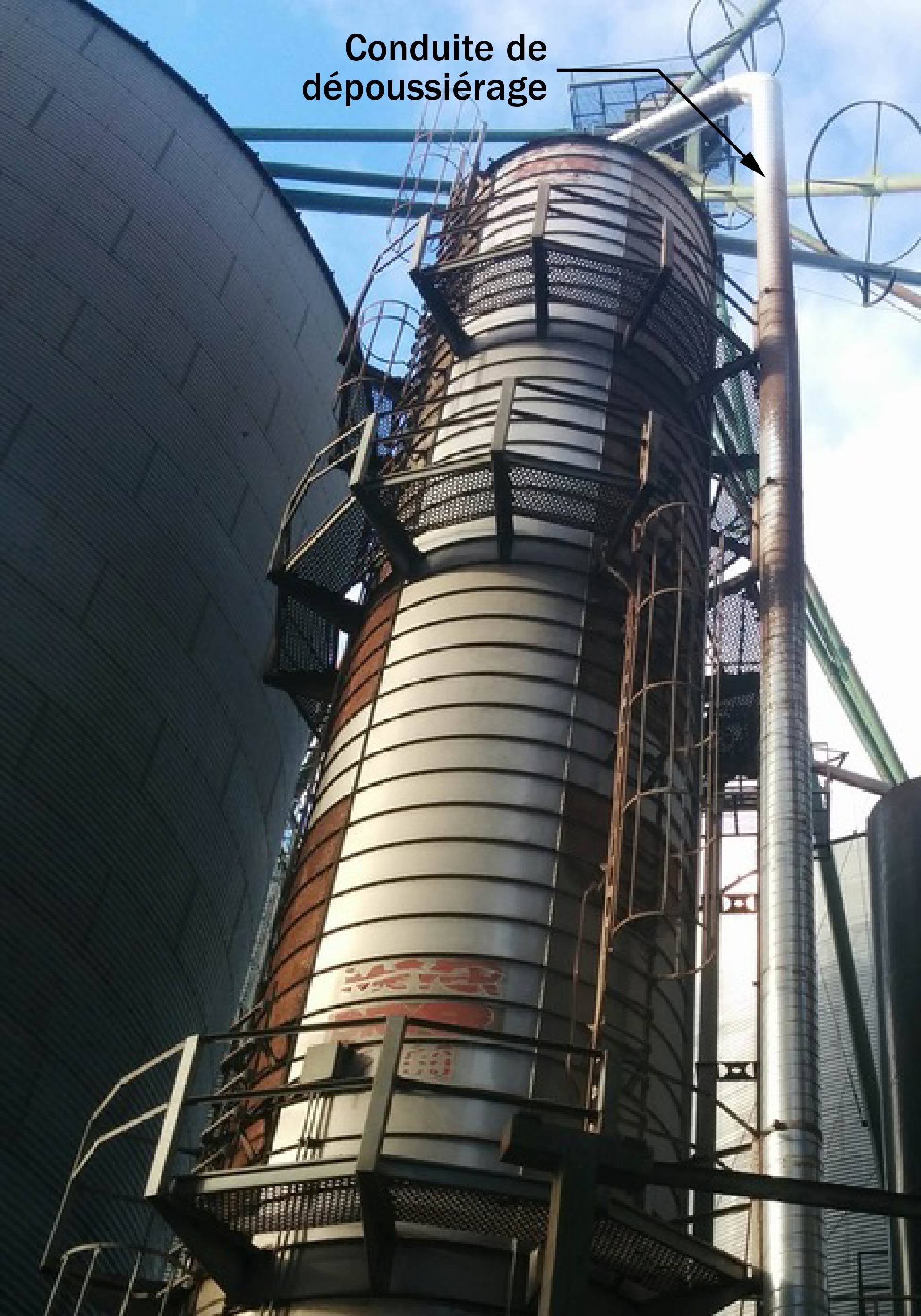
Silos et cellules de stockage
- Utiliser un nettoyeur à grain pour éliminer les particules fines et la poussière avant que le grain ne soit entreposé.
- Installer une conduite de dépoussiérage et des filtres cycloniques afin de capter la poussière au moment où le grain est introduit dans le silo ou la cellule de stockage.
- Installer un ventilateur d’aération pour aspirer l’air vers le bas plutôt que de le pousser vers le haut à travers les grains. Ouvrir le ventilateur durant le transfert du grain. La masse de grain agira comme un préfiltre et captera la plupart des grosses particules. Évacuer l’air par un filtre ou un cyclone afin de recueillir les particules plus petites qui restent.
Filtration et élimination
- Utiliser des ventilateurs d’extraction pourvus de filtres dans les milieux semi-clos (comme les aires de réception et d’expédition).
- Utiliser des systèmes de dépoussiérage pourvus d’un séparateur cyclonique afin de capter la poussière issue de structures closes (comme les silos de stockage, les fosses de réception, les systèmes de convoyeurs) (figure 6).
- Semer des cultures comme du panic érigé ou du miscanthus autour du site afin de créer un système de filtration passif. Ces espèces poussent relativement vite et créent une sorte de barrière en hauteur qui ralentit la circulation d’air et contribue à garder la poussière sur place.
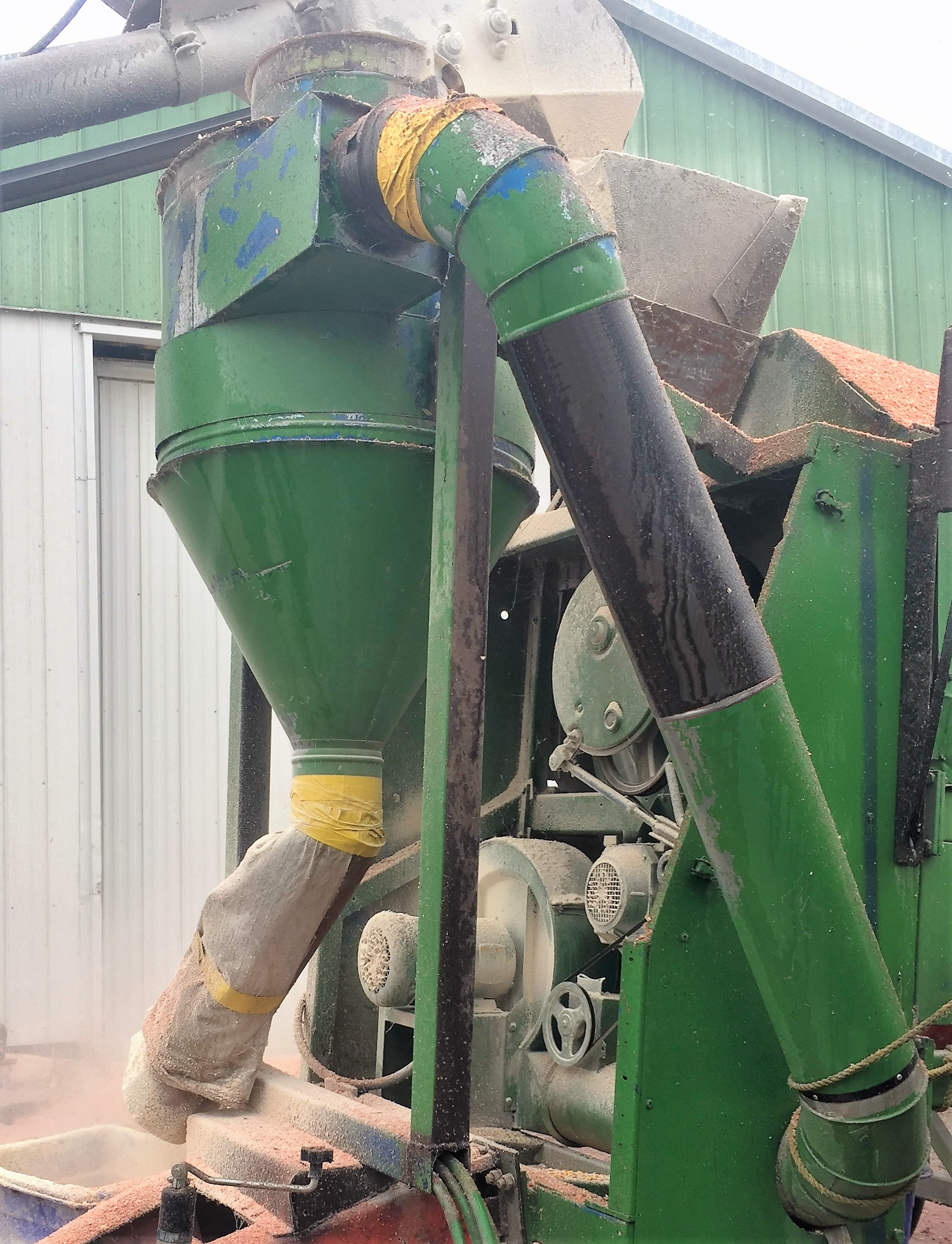
Systèmes de dépoussiérage
Les systèmes de dépoussiérage industriels pulvérisent un fin brouillard d’eau dans l’air (figure 7). Le brouillard capte la poussière et l’empêche ainsi de s’échapper. La poussière humide risque cependant d’adhérer aux bâtiments, aux véhicules et aux surfaces routières, ce qui accroît les travaux d’entretien. Ces systèmes peuvent être coûteux à l’achat, fonctionnent à l’électricité et exigent un approvisionnement d’eau constant. Ils peuvent cependant être efficaces, surtout quand il est difficile d’avoir recours à d’autres méthodes de dépoussiérage. Il est également possible de louer ces appareils à court terme.
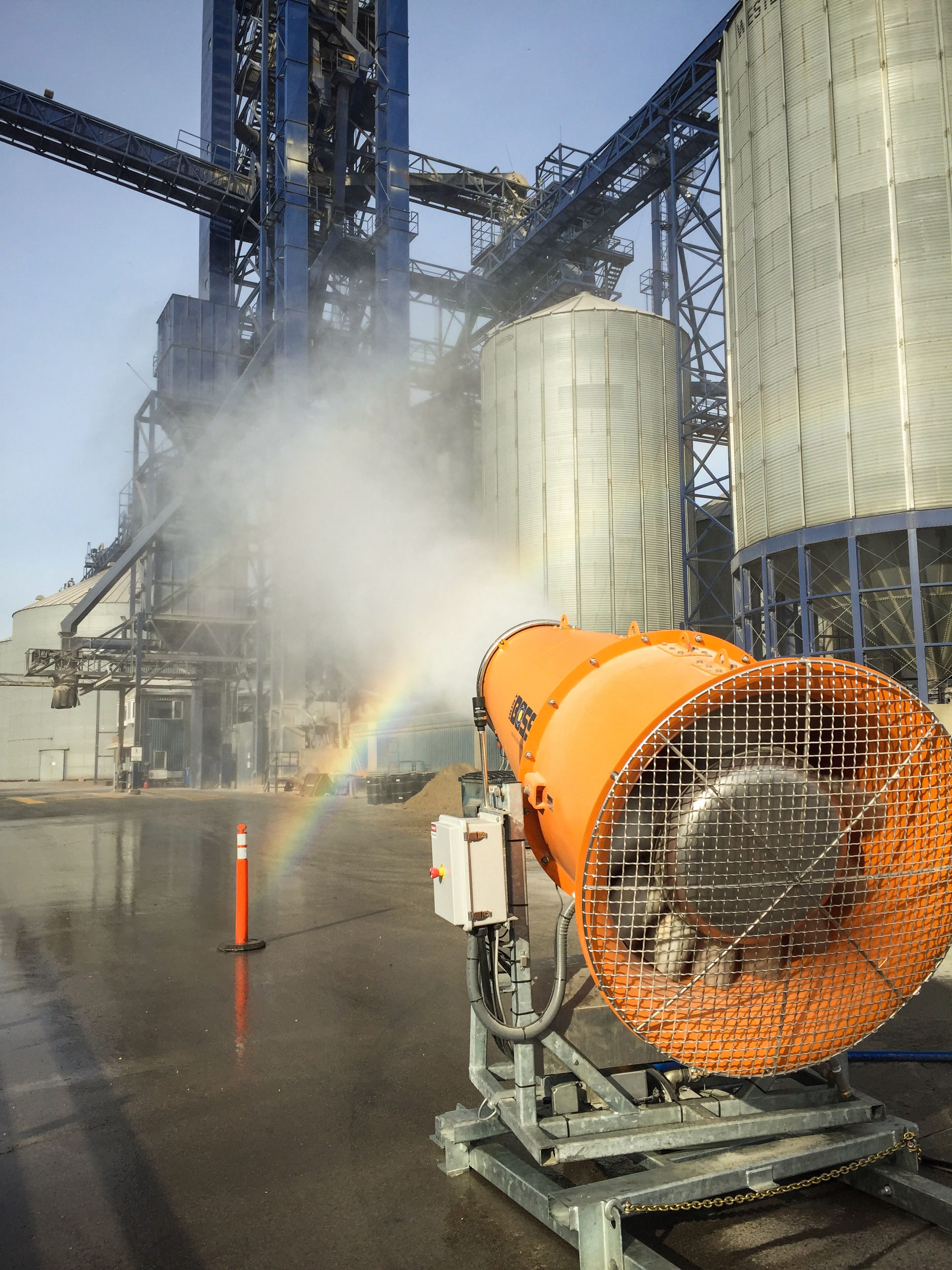
Plan de réduction des émissions de poussière de grain
Établir un plan de réduction des émissions de poussière produites par le système de manutention du grain, dans lequel on décrit les principales mesures visant à réduire les émissions de poussière, à minimiser leur effet sur le voisinage et à diminuer les pertes de profit associées à ces émissions. Envisager toutes les possibilités offertes de réduire les quantités de poussière émises, y compris diverses technologies et pratiques de gestion. Rédiger le plan et le mettre à jour régulièrement. Conserver le document à titre de ressource permettant de faciliter l’amélioration des conditions en matière d’émissions de poussière et de réduire la probabilité de faire l’objet de plaintes de la part des voisins.
Inclure ces trois volets dans le plan de réduction de la poussière de grain :
- Repérer les sources potentielles des émissions de poussière indésirables. Dresser une liste de chaque processus et opération propre au système de manutention du grain et repérer les sources potentielles d’émissions de poussière (p. ex. à l’aire de réception et d’expédition : la fosse de réception, la vis de transfert, la goulotte du haut).
- Trouver les sources de poussière qui présentent le plus de risque et qui ont le plus de chance de devenir une nuisance pour les voisins. Évaluer la quantité de poussière qui s’échappe de chaque source, par rapport à la distance qui la sépare des voisins, à la topographie et aux conditions de température (p. ex. la fosse de réception présente un risque élevé d’émission de poussière pour les voisins situés à l’est).
- Trouver des stratégies de dépoussiérage visant l’atténuation des émissions de poussière à chacune des sources. Pour chaque source d’émissions, trouver au moins une ou deux stratégies visant à prévenir la production de poussière indésirable ou à en diminuer les émissions (comme en évitant de recevoir du grain par temps venteux, en enfermant les abords de la fosse de réception, en aménageant un brise-vent entre l’élévateur et les proches voisins).
Appliquer les mesures décrites dans le plan pour réduire les émissions de poussière. Pour des interventions de plus grande envergure ou à plus long terme (comme l’aménagement d’une fosse de réception en milieu clos, la plantation de brise‑vents), prévoir un échéancier pour leur réalisation. Réviser le plan chaque année et continuer à apporter des améliorations visant à réduire les émissions de poussière.
Gestion et résolution des plaintes
La poussière produite par les systèmes de manutention du grain peut être une nuisance pour les voisins. Il est important de prendre les plaintes au sérieux et d’y répondre de manière professionnelle. Écouter la version de la partie plaignante.
Trouver la source la plus probable des émissions de poussière, et réviser le plan de réduction des émissions pour trouver des solutions. Utiliser l’information fournie dans cette fiche pour trouver des solutions potentielles. Apporter les changements requis pour réduire l’effet de la poussière et assurer un suivi auprès de la partie plaignante afin de vérifier si les conditions se sont améliorées. Garder les dossiers sur toutes les plaintes reçues et sur les mesures prises pour réduire le problème.
Une communication ouverte et honnête aide à éviter les malentendus et démontre l’intérêt et la volonté de l’agriculteur à trouver des solutions. Pour plus d’information, consulter la fiche technique du MAAARO intitulée Donner suite aux plaintes pour nuisance agricole, à ontario.ca.
Résumé
Toutes les composantes d’un système de manutention du grain peuvent être améliorées en vue de réduire les émissions de poussière ou de prévenir leur production au départ. Évaluer la totalité du système et tenter de repérer les possibilités de diminuer la production de poussière et les émissions qui s’en suivent. Une baisse de ces émissions réduit les chances de faire l’objet de plaintes et améliore la sécurité, la propreté et la rentabilité du système de manutention du grain.
Cette fiche technique a été rédigée par Amadou Thiam, ing., ingénieriste, qualité de l’air, MAAARO, Kemptville, et par James Dyck, ing., ingénieriste, systèmes de production des cultures et questions environnementales, MAAARO, Vineland. La fiche a été revue par Steve Clarke, ing., ingénieriste, énergie et systèmes de récolte, MAAARO, Kemptville, et par Steve Beadle, ing., ingénieriste, équipement et structures pour porcs et moutons, MAAARO, Ridgetown.