Managing dust emissions from on-farm grain handling systems
Learn about the main sources of grain dust and the opportunities to reduce dust production and escape from on-farm grain handling systems. This technical information is for Ontario producers.
ISSN 1198-712X, Published June 2020
Introduction
Grain drying, handling and storage are essential to Ontario’s agricultural sector. On-farm grain handling systems continue to grow in number and size, giving farmers more ability to store and market grain themselves. However, grain-handling systems can create significant dust emissions.
Excessive dust creates nuisance issues, which can lead to complaints from nearby residents and businesses. Dust is also a safety risk and a fire hazard. In addition, since grain is sold by weight, excessive dust is like money floating away in the wind.
Every part of a grain-handling system can be modified to reduce or eliminate dust production and escape. Reducing dust will improve the safety and cleanliness of the facility, reduce the chance of complaints and improve profitability by keeping dust where it belongs — in the grain!
This factsheet identifies the main sources of grain dust and highlights opportunities to reduce dust production and escape from on-farm grain handling systems.
Sources of grain dust emissions
Unwanted dust emissions from grain systems is made up of:
- “red dog “or “bees wings”
- grain hulls
- field dust
“Red dog” is the light peeling material that breaks off from corn kernels (Figure 1). It is relatively large and light, making it very difficult to collect and clean. Dust emissions are sometimes called “fugitive dust,” which means the dust escapes from multiple sources, rather than being created at a single point. The amount of dust varies, depending on grain quality, moisture content, harvest conditions, handling practices and configuration of the dryer and handling systems.
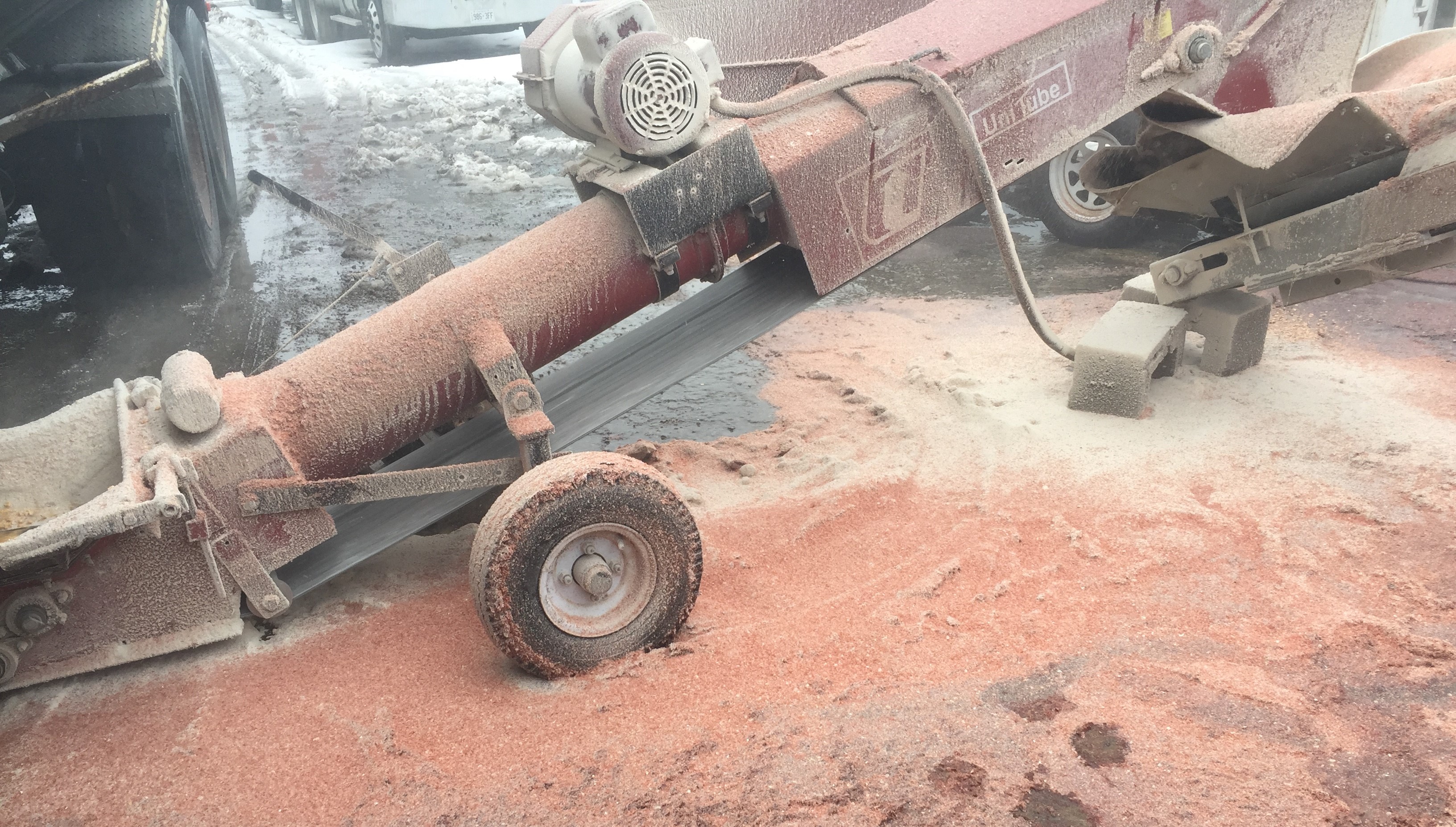
Most dust is generated during harvest season, when the majority of the drying and handling takes place. However, dust can escape any time grain is handled. Escaping dust reduces the weight and, since grain is sold by weight, lowers profits for the farmer. Figure 2 highlights the main sources of dust from on-farm grain-handling systems.
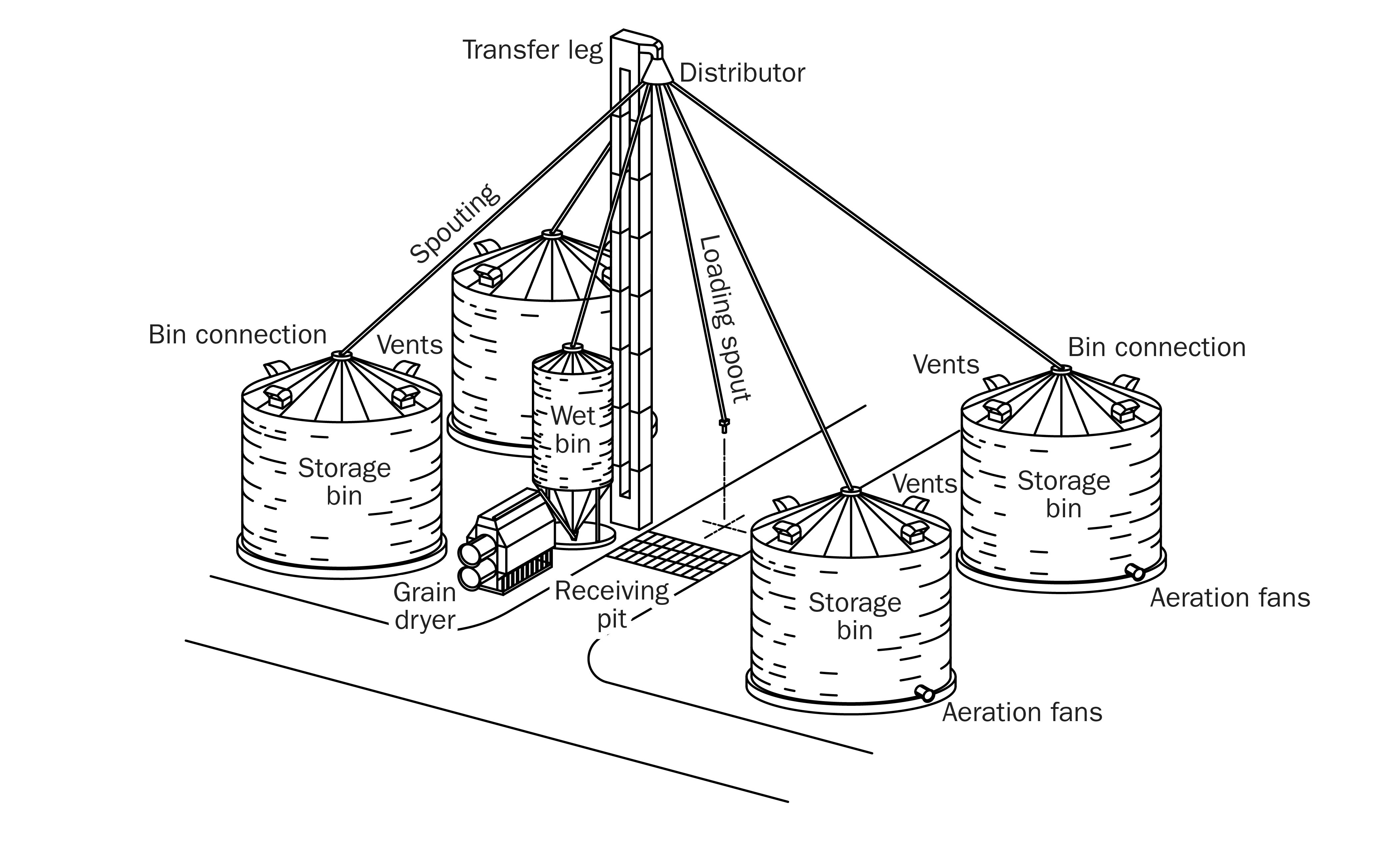
Grain receiving and shipping account for 80% to 90% of dust at a grain facility. Grain is normally unloaded from trucks into a receiving pit and loaded into trucks from above out of an auger or spout. During loading and unloading, air is displaced out of the pit or truck and carries dust with it. Dust is also produced while grain is falling from the spout or truck.
The transfer leg(s) and conveyor system move grain between receiving pits, storage bins and trucks through connected conveyors, elevator legs and augers. Small grain fragments and dust are produced as kernels rub against each other and against the conveyor/auger/pipe. Dust escapes at transfer points when the grain falls into or away from the conveyor system, and from unsealed joints along the system.
Grain dryers use large fans to move a lot of air and are responsible for up to 10% of dust at a grain facility. Different dryers have different air exhaust configurations (e.g., single exhaust, multiple exhausts, screened, open) that influence the amount of dust emitted.
Storage bins and silos must be ventilated (aerated) to keep grain dry and in good condition. However, aeration carries dust out through the bin vents. Dust-laden air is also displaced out the vents when the bin is filled. Dust emissions increase if grain is transferred more often. Silos and bins are responsible for up to 10% of dust emissions at a grain facility.
Reduce dust at the source
The most effective way to reduce dust is to prevent creating dust in the first place. Every operation on the farm elevator can be modified to reduce or eliminate dust production, and many dust control options cost nothing but operator time.
Siting
The location of a grain-handling system can have a big impact on dust production.
- Locate the elevator facility far from sensitive receptors (e.g., nearby residences or businesses) where prevailing wind directions and speeds will not aggravate a dust problem.
- Locate dryers, receiving and shipping areas on the windward side of storage silos or other buildings so they can act as buffers to prevent dust from escaping on the wind.
- Avoid placing dryers, receiving and shipping areas between rows of silos or bins. This could create a “wind tunnel” effect, making dust problems worse.
For existing facilities, relocation is not usually an option. When opportunities arise, reconfigure the layout to reduce dust, such as when purchasing a new storage bin or grain dryer.
General housekeeping
Follow good housekeeping practices around the elevator to prevent dust from accumulating. A buildup of dust is more likely to travel off site and create problems. Excessive dust is also a fire risk.
- Cover all open trucks and wagons.
- Drive slowly — post and enforce speed limits.
- Wet down driveways to limit dust generation.
- Pave driveways and yard wherever possible.
- Sweep and clean up any dust accumulation daily.
- Use sealed electrical equipment suitable for dusty environments to minimize fire risk.
- Wear approved particulate respirators and other personal protective equipment (PPE) in dusty areas to protect human health.
Grain receiving and shipping
Control dust during receiving and shipping by reducing the distance grain falls during transfer:
- Keep unloading chutes as low and close to the receiving pit as possible.
- Allow grain to form a cone around the receiving grate as it is being unloaded (also known as “choke flow” – Figure 3) to reduce dust by up to 90%.
- Leave conveyors/augers off until the receiving pit is full to promote choke flow. Transfer grain more slowly when the pit or truck is empty or partially full.
- Avoid or limit operations during windy conditions, especially when wind is directed toward nearby sensitive areas.
- Install socks or drop-down spouts on unloading chutes and spouts, extending at least 15 cm (6 in.) below the sides of the receiving pit or truck if possible.
- Install cushion boxes or “dead heads” on unloading spouts to slow grain down.
- Use a grain cleaner to remove fines and dust from grain as it is received, and/or before shipping out.
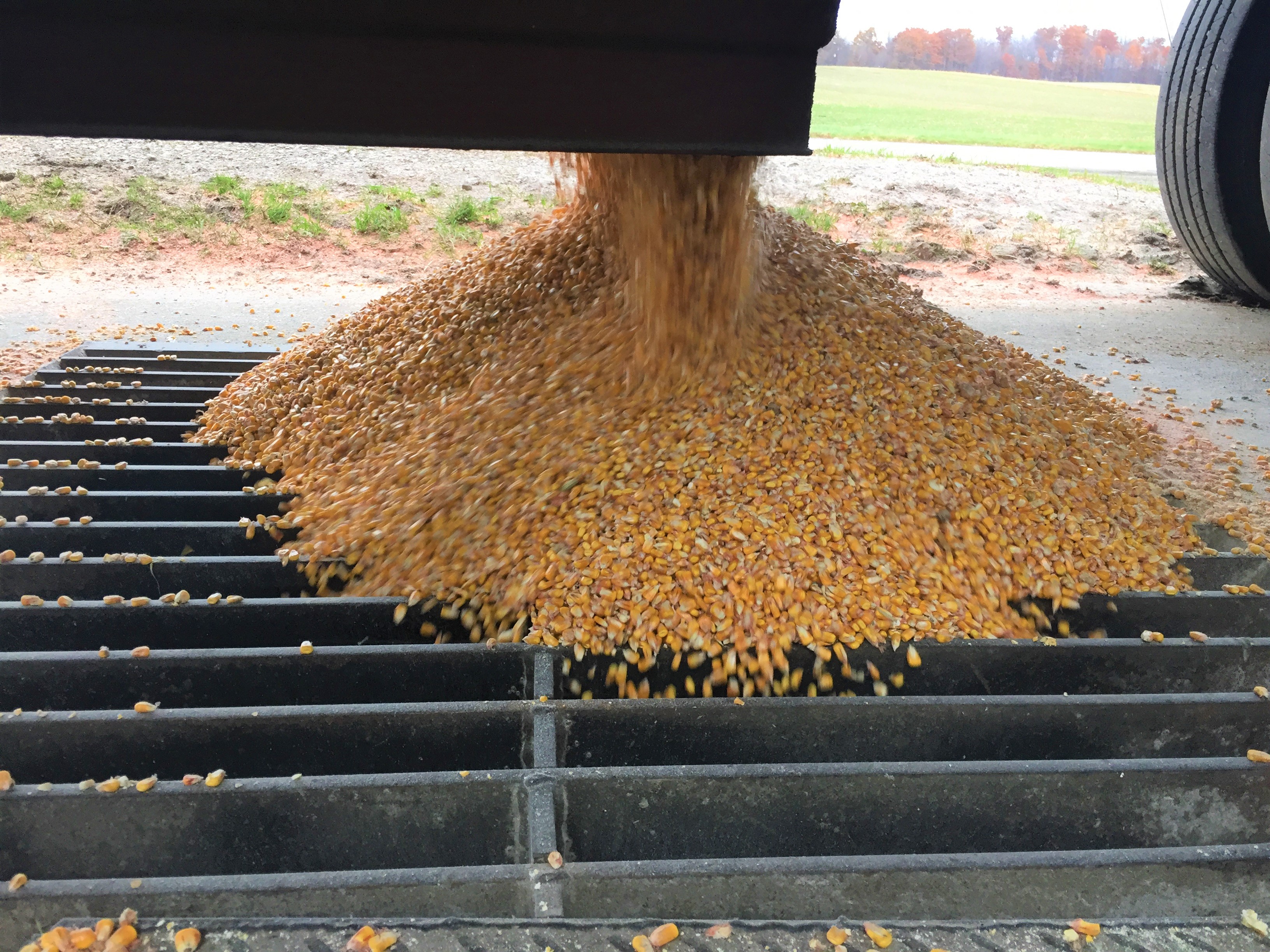
Transfer leg and conveyor system
A well-maintained grain-handling system should produce little dust:
- Ensure all grain-conveying equipment is fully enclosed.
- Keep all connections to spouts and other equipment sealed and dust-tight.
- Ensure no sharp edges are present in elevators, augers or piping, to minimize grain damage.
- Minimize open-air grain transfer.
- Operate all conveying equipment at the slowest speed necessary.
- Operate augers and conveyors fully loaded. Half-empty transfer systems create significantly more dust.
Grain travelling at high speeds is more likely to break, creating additional fines and dust. Install all spouting at proper angles to avoid high grain speeds. Install inline flow retarders (cushion boxes or “dead heads”) at regular intervals to reduce the speed of grain travel in steep spouting.
Use Figure 4 to decide whether flow retarders are needed. Measure the horizontal and vertical travel distance of the spouting and use these measurements to find the angle on the chart. Find where the angle line crosses the top of the “preferred area.” Use the curved lines on the chart to find the recommended spout length for installing flow retarders. For example, a spout with a horizontal distance of 15 m (49 ft) and a vertical distance of 18 m (60 ft) has a flow angle of about 50°. The 50° line leaves the “preferred area” at 10 m (33 ft) of spout length. In this spout, flow retarders should be installed every 10 m (33 ft).
In spouting steeper than 45°, install flow retarders every 10 m (33 ft) or less, to keep grain speeds low. In spouting steeper than 70°, install flow retarders every 5 m (16 ft) or less.
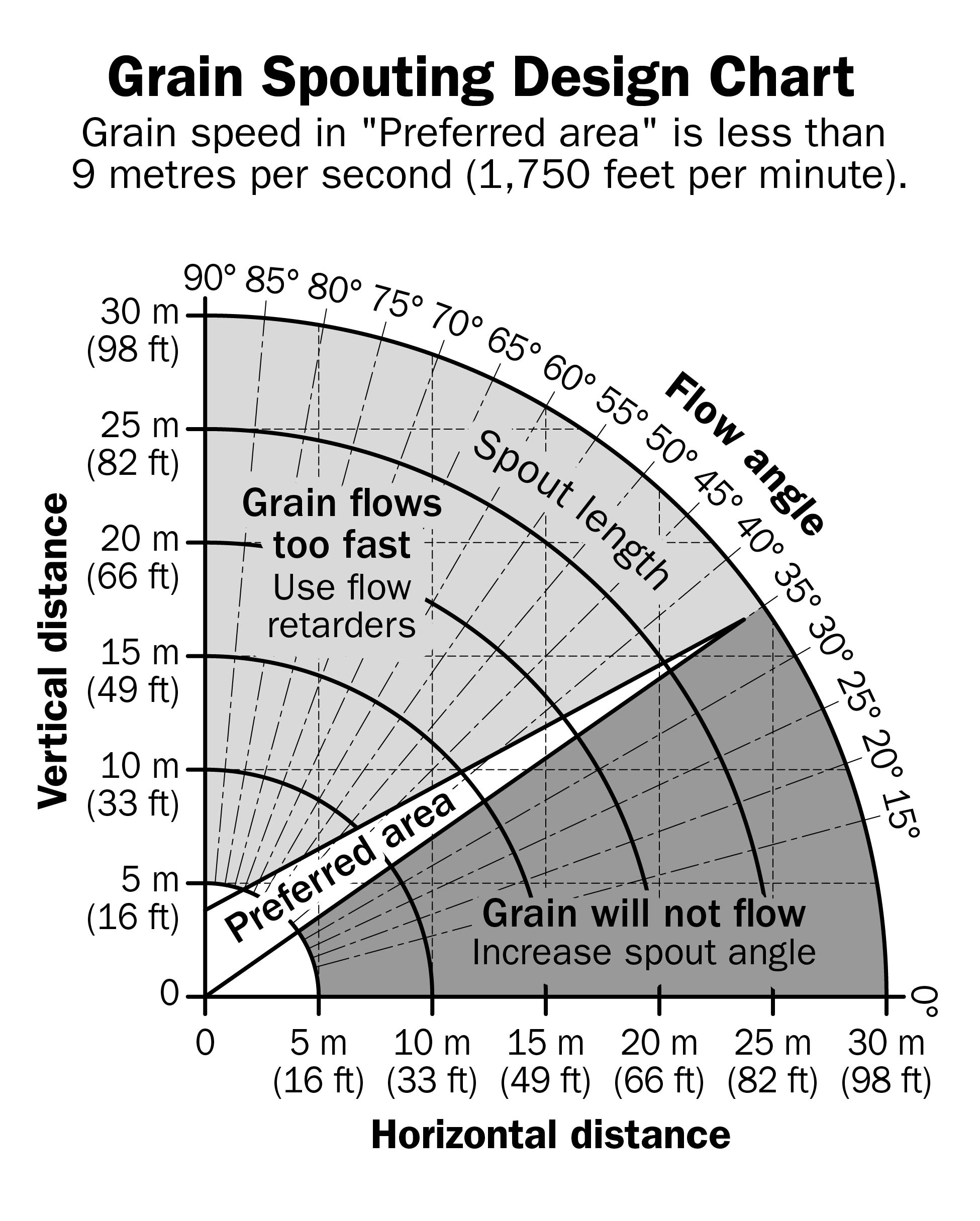
Grain dryers
Good management is critical to reducing dust from dryers:
- For screened dryers, use a screen size as small as possible to limit dust escape.
- Regular wash down, housekeeping and clean-up of the dryer and surrounding area is the most effective method to limit dust buildup.
Storage silos and bins
Most dust is produced when grain is flowing into or out of storage:
- Transfer grain to and from silos as slowly as possible.
- Install cushion boxes in spouting at the top of bins, to reduce grain speed entering the silo.
- Do not run aeration fans during grain transfer, to minimize dust escape.
Reduce dust escape
No matter the effort or expense, some dust will escape during grain handling. Establish control measures around the elevator to capture and retain any dust produced, before it travels off site.
Windbreaks
Windbreaks can prevent dust from becoming airborne. Plant trees to create windbreaks, both on the windward side (to prevent wind from picking up dust) and the leeward side (to prevent dust-laden air from escaping the farm). Trees take time to grow, so plan ahead! See the OMAFRA publication Best Management Practices: Field Windbreaks (Order No. AF167) for more information.
Alternately, build new storage bins or other buildings to create windbreaks for an existing elevator.
Grain receiving and shipping areas
- Install gravity baffles on receiving pits, which open only when grain passes through.
- Cover and enclose the receiving and shipping area on at least three sides. A drive-through shed with doors closed at both ends prevents dust escape. A shed with no doors (or doors always open) could create a “wind tunnel” effect, making the problem worse.
- Use temporary curtains or barricades to provide shelter around receiving and shipping areas, if permanent coverings are not feasible.
- Wear respirators and other PPE in enclosed areas to protect human health.
- Clean enclosed areas regularly to minimize fire hazard from dust build-up.
- Install dust extraction systems on receiving pits, to draw dust down instead of allowing it to escape.
Transfer leg and conveyor system
- Reconfigure the transfer system to reduce dust if possible.
- Install spouting at shallow angles or install additional cushion boxes, where needed, to reduce grain speeds (Figure 4).
- Enclose all transfer points (e.g., elevator heads) and areas of significant dust production or escape.
Grain dryers
- Install dust collection piping and cyclone filters, to capture dust as grain enters the dryer (Figure 5).
- Some types of dryers can have filters added to outlet plenums to capture dust from the exhaust air.
- Some types of dryers can be enclosed. This can help to contain fines; however, this can also increase the risk of fire. Only enclose dryers if approved by the manufacturer and local authorities and follow all safety codes and regulations.
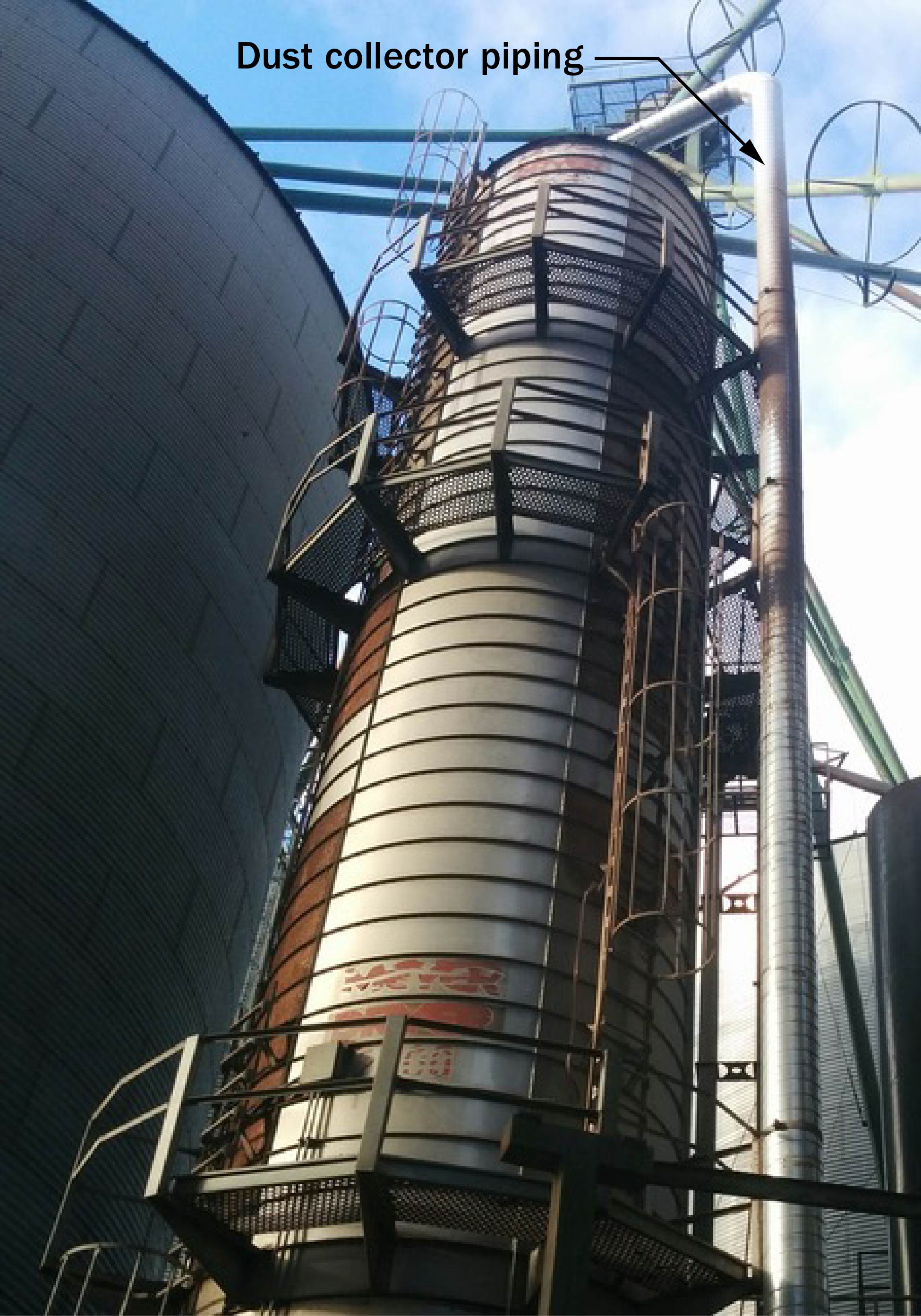
Storage silos and bins
- Use a grain cleaner to remove fines and dust before grain is put into storage.
- Install dust collection piping and cyclone filters to capture dust as grain enters the bin.
- Install an aeration fan to suck air down instead of force air up through the grain. Run this fan during grain transfer. The grain mass will act as a pre-filter to capture most of the large particulate. Exhaust the air through a filter or cyclone to collect any remaining smaller particles.
Filtration and removal
- Use exhaust fans with filters in semi-enclosed areas (e.g., receiving and shipping areas).
- Use dust-extraction systems with cyclone separation to capture dust from enclosed containers (e.g., storage silos, receiving pits, conveyor systems) (Figure 6).
- Plant crops such as switchgrass or miscanthus around the site to create a passive filtration system. These crops grow relatively quickly, creating a tall wall that slows air movement and helps keep dust in place.
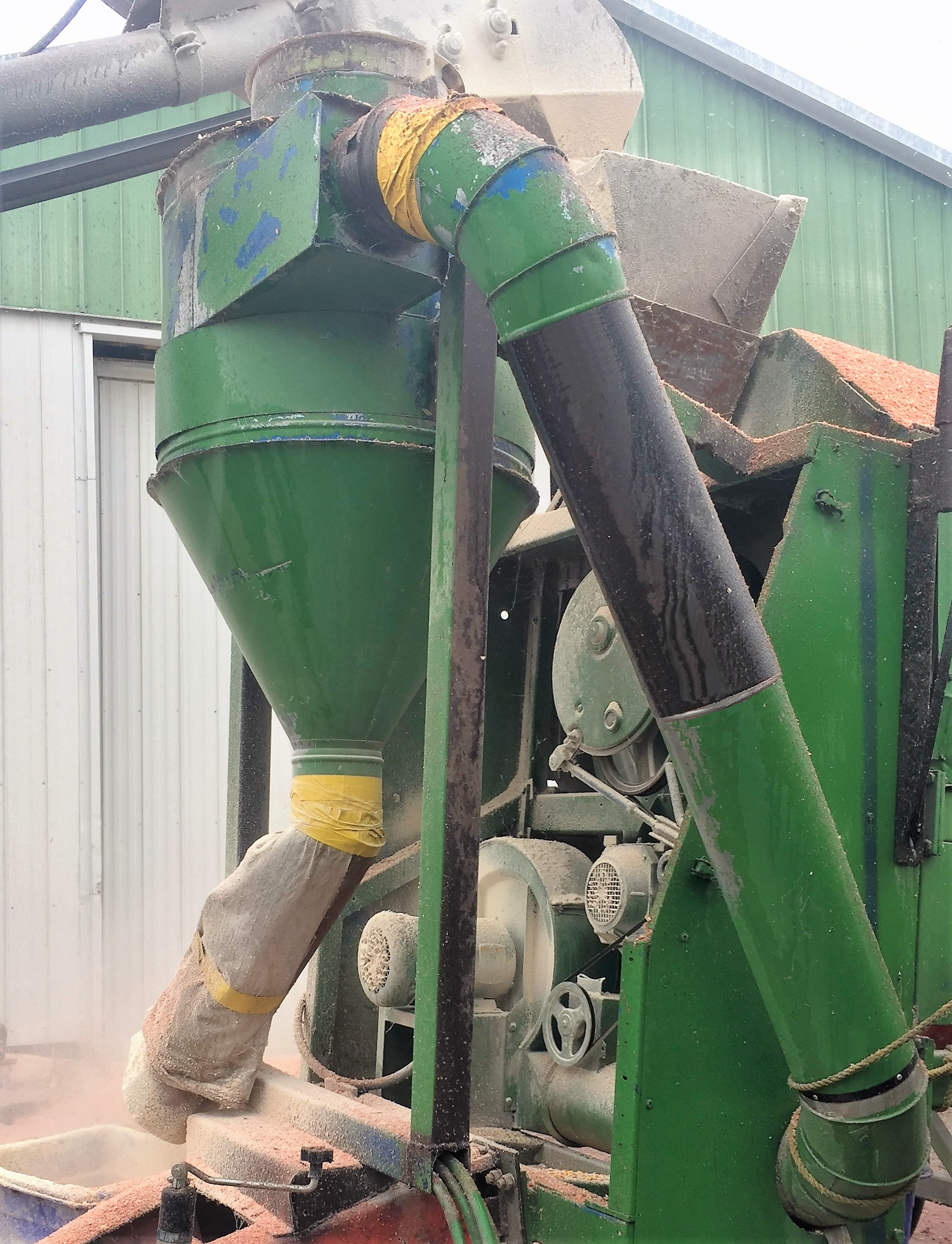
Dust suppression systems
Industrial dust suppression systems spray a fine mist of water into the air (Figure 7). The mist captures dust and prevents it from escaping. However, wet dust may stick to buildings, vehicles and roadways, creating more housekeeping work. These systems can be costly to purchase and require electrical power as well as a constant water supply to operate. However, they can be effective, especially when other methods of dust control are not practical. The option to rent may be possible for short-term needs.
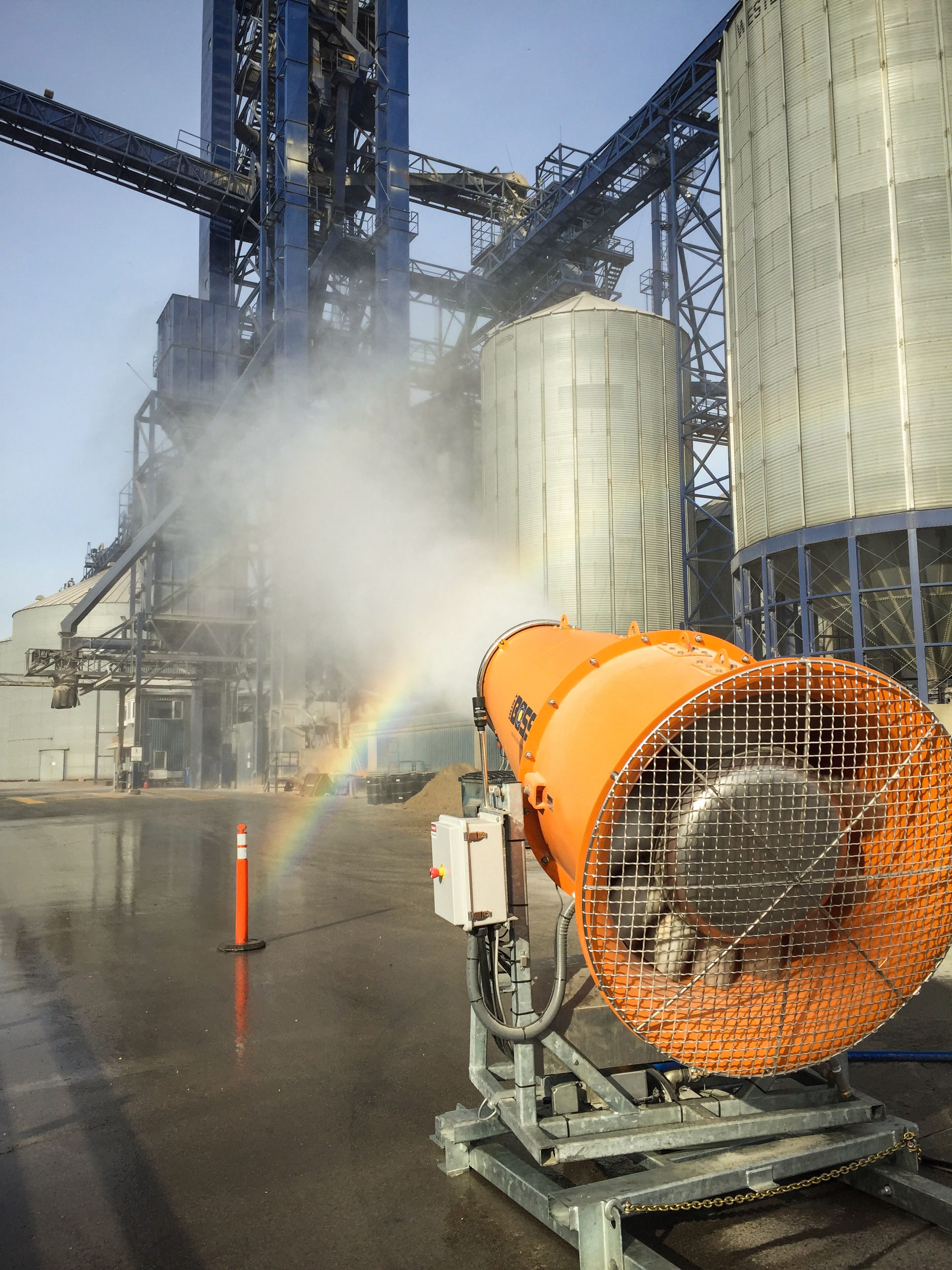
Develop a grain dust control plan
Develop a grain dust control plan for the grain-handling system, to highlight key actions to reduce dust emissions, minimize impact on neighbours and reduce profit loss from escaping dust. Consider all available options to reduce dust, including technologies and management practices. Write down the plan and update it regularly. Keep this written plan as a resource to help improve dust conditions and reduce the likelihood of receiving complaints from neighbours.
Include these three components in the grain dust control plan:
- Identify potential sources of unwanted dust emissions. List each process and operation in the grain-handling system and identify possible sources of dust emissions (e.g., shipping/receiving: receiving pit, transfer auger, overhead spout).
- Determine which dust sources are highest risk and have the biggest potential to cause nuisance to neighbours. Estimate the amount of dust escaping at each source, in relation to distance to neighbours, topography and weather patterns. (e.g., receiving pit: high potential for dust escape with nearby neighbours to the east).
- Identify control strategies to address dust emissions at each source. For each dust source, identify at least one or two control strategies to prevent the production of unwanted dust and/or decrease its release (e.g., avoid receiving grain in windy conditions, enclose receiving pit, establish a windbreak between elevator and nearby neighbours).
Implement the actions identified in the dust control plan to reduce dust escape. For larger and/or longer-term actions (e.g., enclosing receiving pit, planting windbreak), write down a timeline to complete these actions. Review the plan annually and continue making improvements to reduce dust emissions.
Manage and address complaints
Dust from grain-handling systems can be a nuisance for nearby neighbours. If complaints are received, take them seriously and respond professionally. Listen to the complainant’s version of the story.
Identify the most likely source(s) of dust and review the dust control plan to look for solutions. Use the information in this factsheet to identify potential solutions. Make changes to reduce the impact of dust and follow up with the complainant to find out whether conditions have improved. Keep records of any complaints received and what steps were taken to reduce dust problems.
Open and honest communication helps avoid misunderstandings and demonstrates interest and willingness to find solutions. See the OMAFRA factsheet, Responding to Agricultural Nuisance Complaints for more information.
Summary
Every part of the grain-handling system can be improved to reduce dust emissions or prevent dust creation in the first place. Evaluate the entire system and look for opportunities to reduce dust production and dust escape. Fewer dust emissions reduce the chance of complaints and makes the grain handling system safer, cleaner and more profitable.
This factsheet was written by Amadou Thiam, P.Eng., engineering specialist, Air Quality, OMAFRA, Kemptville, and James Dyck, P.Eng., engineering specialist, Crop Systems and Environment, OMAFRA, Vineland, and reviewed by Steve Clarke, P.Eng., engineering specialist, Energy and Crop Systems, OMAFRA, Kemptville, and Steve Beadle, P.Eng., engineering specialist, Livestock Structures & Equipment – Swine and Sheep, OMAFRA, Ridgetown.