Milking centre design and construction for parlour milking
Learn about the design features recommended for the construction of milking parlour centres. This technical information is for Ontario livestock producers.
ISSN 1198-712X, Published July 2022
Introduction
This fact sheet discusses design features recommended for the construction of milking parlour centres.
A properly designed parlour supports increased milk production, cow comfort and cow health.
Milking centre design
Design your milking centre around the type and size of milking parlour you have selected (Figure 1).
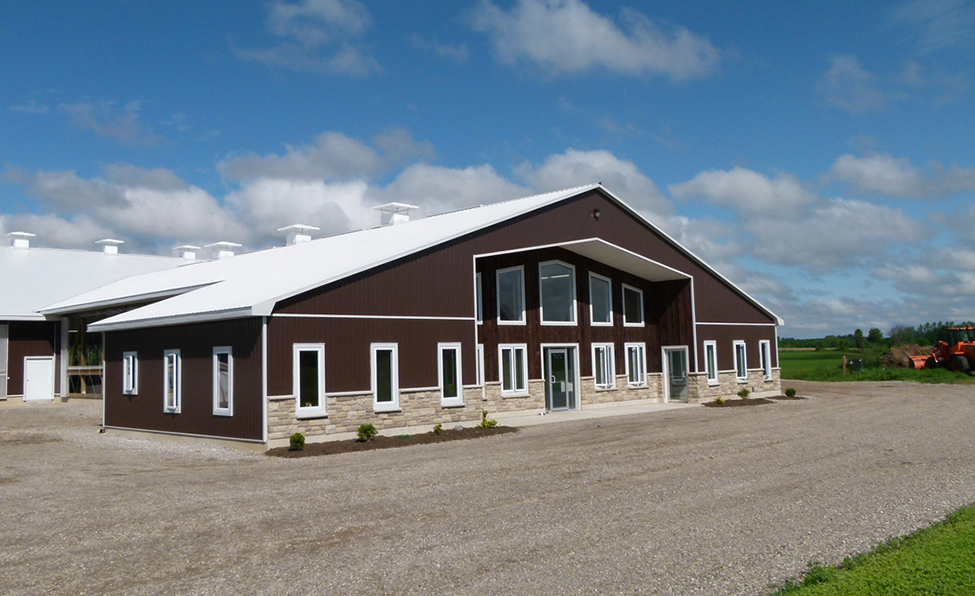
Planning — it is important to work closely with your milking equipment supplier to develop a plan but leave it up to the supplier to look after equipment placement and design details.
Coordination — ensure that the milking equipment supplier works closely with the general contractor to make sure elevations line up, especially when dealing with walk-in parlour pits and sloped holding areas.
Regulations — make sure that your milking equipment supplier and the general contractor are familiar with the regulations for cleanliness and sanitation of the milking centre.
Milking centre components
The milking centre consists of:
- a holding area
- the milking parlour
- a milk tank room
- a mechanical room
- optional areas, such as a storage room, supply room or employee area
Holding area
The holding area holds the cows before they enter the milking parlour. Groups of cows are moved from the free stall area to the holding area, where they wait to enter the milking parlour. A well-designed holding area orients the cows towards the parlour and allows for consistent, efficient loading of the parlour.
Sizing
Size the holding area to hold the largest single group of cows from the free stall area, allowing between 1.4–1.8 m2 (15–20 ft2) per cow.
It is a good practice to size the parlour so that cows are not in the parlour for more than an hour.
Sometimes the holding area is sized so that a single group of cows will fill the parlour and the holding area. Another approach is to size the holding area to contain the entire group. This allows a new group to fill the holding area, while the last cows from the previous group are being milked.
Slope
The holding area should be sloped between 2% to 4% away from the parlour. Steeper slopes cause stress on rear feet.
Return alleys sloped more than 5% will slow down the flow of cows exiting the parlour.
Floor finish
Install a grooved floor with a textured surface in the holding area, to provide good traction.
Rubber is often used in the holding area to make it more comfortable for the cows to stand on. Good traction on the rubber is a must.
Cow alleys used as holding area
Cow alleys can be used for holding areas to save costs, although some cows will try to “hide” in the stalls instead of moving up the alley, causing slowdowns and making it necessary to clean the stalls.
Crowd gates
Crowd gates can be used to reduce the size of the holding area as cows are being milked, to keep them entering the parlour (Figure 2).
Rigid gates are the preferred option, moving the cows more efficiently and separating the group of cows being milked from the next one coming up.
Cows often become conditioned to move on the sound of the crowd gate, so it becomes unnecessary to use the crowd gate aggressively to move the cows.
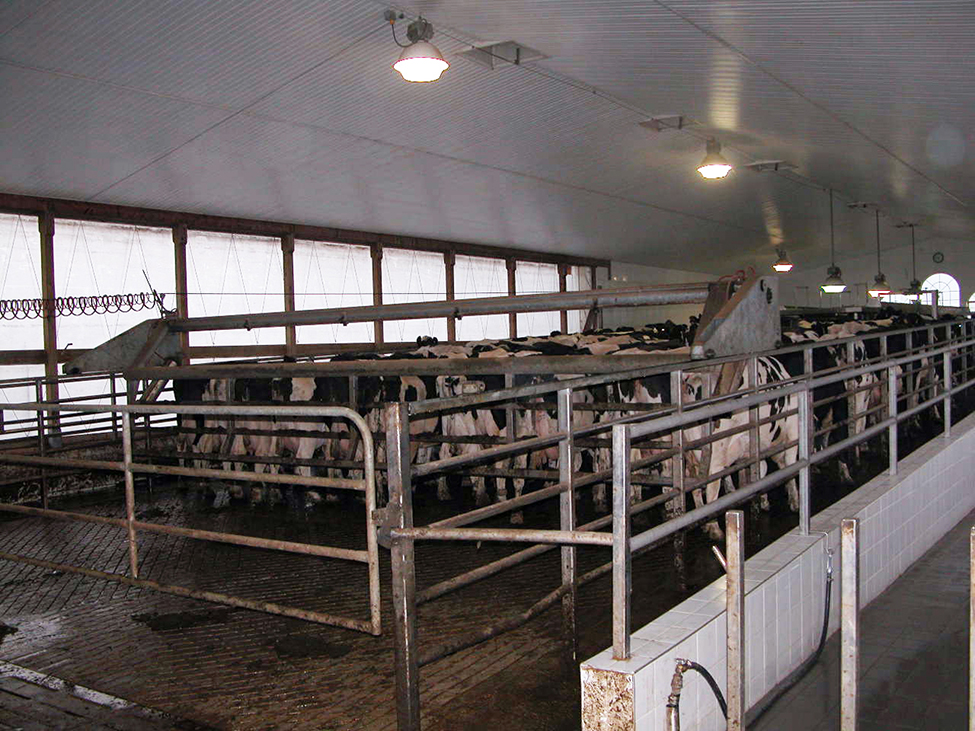
Cow movement
Cow movement from the holding area to the parlour should be as smooth as possible. Make sure the cows can see where they are going.
If curtains or doors separate the parlour from the holding area to keep it from freezing, make sure they are large enough to provide good visibility once they are open.
Set up the holding area so the cows enter the parlour directly. They should not have to turn. Design gates to funnel the cows towards the entrance without being so complex that they restrict entrance to the parlour. For wide parlours, avoid turning the cows more than 45° as they enter the parlour.
Parlour area
The type and number of stalls in the parlour is based on the operator’s milking speed and herd size.
Herringbone
Herringbone parlours range from double-4 to double-24, although some dairies use larger parlours. The walking distance between udders varies from 90–115 cm (36–45 in.), depending on the manufacturer.
Rigid automatic take-off arms make claw placement more positive.
Herringbone parlours are the preferred option for smaller herds due to the fewer number of stations.
Parallel
Parallel parlours range in size from double-6 to double-50. Cows stand parallel to each other at a 90° angle to the operator pit. Teat cups are attached from the rear by reaching through the hind legs. Walking distance between cows is 69–76 cm (27–30 in.).
Parallel parlours are the preferred option for mid- to large size herds.
Swing
Swing parlour designs are used to minimize parlour investment. Purchased herringbone, parallel or simple custom-built stalls are used for the cow platform. The milking unit is used on two stalls and is swung from one side of the parlour pit to the other. Rotating arms can be used to keep the hoses from hanging in the centre of the pit (Figure 3).
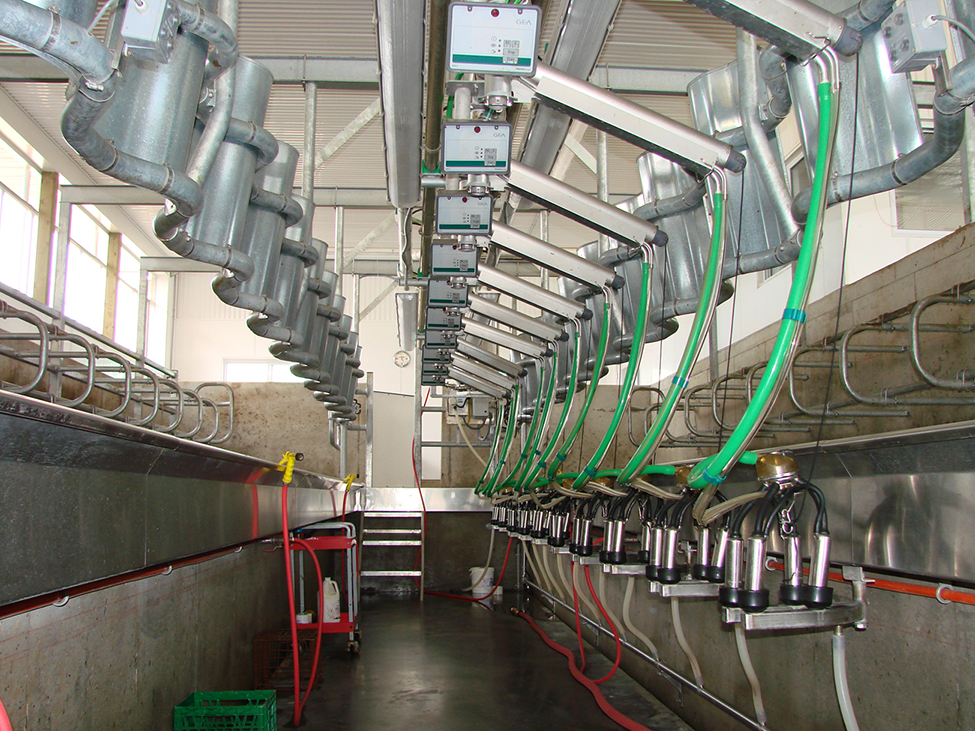
Rotary
Rotary parlours are available in either internal or external designs.
Rotary parlours have up to 80 stalls and are often used on very large dairies because of its ability to milk a higher number of cows per hour.
Rotary parlours promote a regimented, assembly-line-like work routine and operators must meet frequent deadlines in order to maintain the pace set by the rotating platform.
Operators access internal rotary parlours from a tunnel. Make sure the access has handrails and is kept as dry as possible for safety. Robotics are being adapted to internal rotary parlours.
Cow platform
The cow platform is another area where rubber is a benefit. Not only do the cows have to stand, but they are often required to make tight turns when they exit.
Where cows have to make turns, two 90° turns are better than one 180° turn. The platform should slope from the pit to the wall for cleaning and drainage.
Exit options
There are two main exit options from the milking stalls — a single-return lane or a double-return lane.
With the single-return lane, one row of cows must cross at the front of the parlour and exit with the second row. A single-return lane is easier for sorting cows as they exit the parlour but it eliminates the possibility of having a walk-in parlour.
With a double-return lane, each row of cows being milked has a separate lane to exit in and they do not cross in front of the operator’s pit. It is possible to build a pit where the operator walks in on the level or at least only has one step down.
Exit and return lanes
In standard-exit herringbone or parallel parlours, the exit lane should be 81–91 cm (32–36 in.) wide, where there are no turns. Where turns are necessary, use a clear opening 122–152 cm (48–60 in.) wide.
Rapid exit
Rapid-exit parlours make it possible for all the cows to exit at once, speeding up the exit process.
In rapid-exit herringbone parlours, the exit lane varies from 2.5–4.5 m (8–14 ft), depending on the number of parlour stalls.
Pit depth
The recommended pit depth varies with operator height and parlour design. Operators should not have to bend or stoop during milking. Deeper pits improve udder visibility and availability. The optimum working area lies between the elbow and the shoulder, an area of about 30.5 cm (12 in.) (Figure 4). The base of the udder should be located between these points when the operator is comfortably standing. The elbows of the operator should not contact the cow platform.
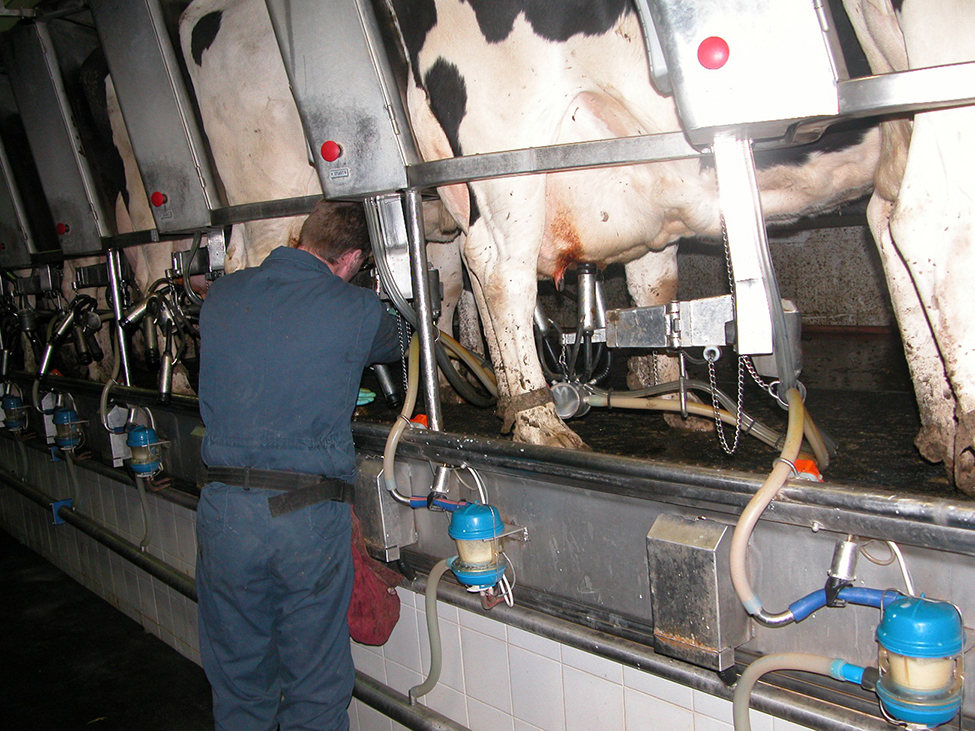
Common pit depths in herringbone parlours are 97 cm ±5 cm (38 in. ±2 in.). In parallel parlours, common pit depths are 102 cm ±5 cm (40 in. ±2 in.). It is better to have the pit too deep and be reaching up for the attachment, than too low and stooping. Adding floor mats will cushion the floor for the operator and raise the floor by about 2.5 cm (1 in.).
Some pits are being installed with adjustable-height floors. This is useful where milkers of different heights will be using the parlour. Milkers using the adjustable floors report that adjusting the floor higher, part way through the milking, helps reduce fatigue.
Pit width
Pit width will depend on the type of parlour selected. It should be narrow enough to provide easy access from one side to the other, but wide enough to allow the operator easy movement throughout the pit and a clear line of sight to the udders and milking units. In double-sided parlours, 2–2.5 m (6–8 ft) is a common pit width. Recessing the pit wall under the cow platform will allow the operator to get closer to the udder as well as allow milk lines and equipment to be stored out of the way.
The floor should have slight slopes for drainage. Too much slope from the centre of the pit to the platform will result in an uncomfortable standing position.
Pit length
Some producers have found it useful to extend the operator pit 2–2.5 m (6–8 ft) beyond the last milker to make it easier to get behind balky cows to help move them into the parlour.
Parlour access
Having a ramp at the end of the pit makes it easier to enter the holding area; however, to the cow, operators appear to grow in size as they mount the ramp, which can frighten the cows.
Some producers also feel that it is not a good idea to enter the holding area too often, so they prefer a ladder or steps, as opposed to a ramp, to discourage milkers from entering the holding area. Cows will “train” milkers to come and get them.
Basement parlours
Building a basement under the parlour for the milking equipment has several advantages. The basement allows for efficient installation of the milk line. The parlour area is quieter (Figure 5) to work in since the pulsators are removed from the pit area. It is also easier to work on equipment in the basement.
These advantages need to be weighed against the extra costs of constructing the basements and subways. Another option is to just build a small basement for the receiver group. Some basements have been built large enough to house the vacuum pumps and other equipment.
Make sure the basement is well drained and kept dry.
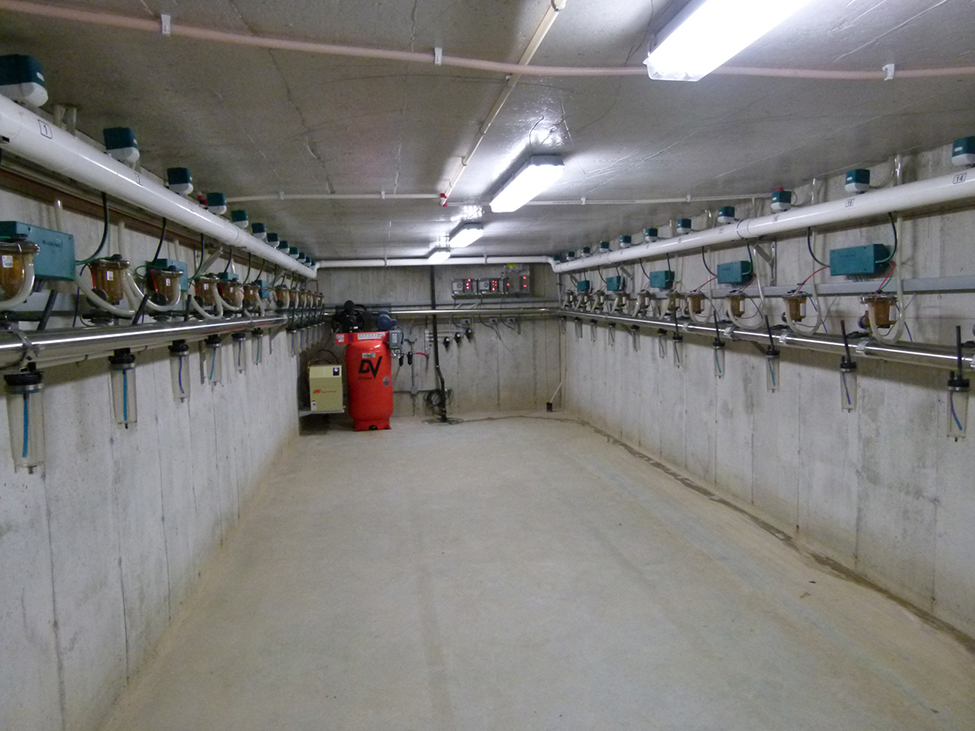
Milk tank room
The milk tank room is used to house the bulk milk tank and related equipment. Extend large tanks through the wall to reduce the area that has more rigid sanitation requirements. Milk tank rooms have a number of cleanings, sanitation and access requirements. Check with your regional Dairy Farmers of Ontario field service rep or your milking equipment dealer for these requirements.
Mechanical room
The mechanical room houses the equipment to run the milking system and equipment to cool the milk. It is a good idea to install this equipment on a slightly raised platform to allow for drainage, in case of leaks. The entire floor should slope towards a drain.
Provide a large overhead door directly to the outside. This will allow for easy access for equipment repair or replacements well as easier delivery of cleaning chemicals and other supplies.
Emergency power
Include emergency power generation in the planning process. If the power goes off, the cows still must be milked. The OMAFRA fact sheet On-Farm Generators for Emergency Use provides more information about on-farm generators for emergency use.
Storage and supply area
It is convenient to have a separate storage room for supplies and replacement parts. This could also be a storage area for herd health supplies. Space is also required for chemical cleaners and chemicals for foot baths. Store cleaning and sanitizing chemicals separately for safety reasons.
Staff and office area
As dairies become larger and more off-farm employees are hired, it is important to have a good staff area. An employee area may include a lunchroom, laundry facilities, lockers and separate washrooms for male and female employees.
Consider including an office as part of the milking centre complex. It can be used to store the herd health, management records and computer systems.
Milking centre environment
Each section of the milking area has different environmental needs.
Milking centre location
Locate the milking centre to make use of prevailing winds, but not block the prevailing winds from blowing through the main milking barn.
Design the milking centre to be well ventilated and restrict air blowing in from dirtier and wetter areas of the barn. Different ventilating rates may be required for different sections of the milking centre.
A mechanical (utility) room experiences heat build-up because of compressors and other equipment running. Warm air from the mechanical room can be used to warm up other areas during cold weather.
Holding area
The ventilation in the holding area must be adequate to remove the heat and moisture produced by the cows. If possible, ventilate this area naturally, similarly to the milking barn.
During hot weather it may be necessary to use large fans to keep the air circulating over the cows. Install panel fans 2.4–3.7 m (8–12 ft) apart and use 46–61-cm (18–24-in.) fans to blow across the width of the barn in the direction of the prevailing wind (Figure 6).
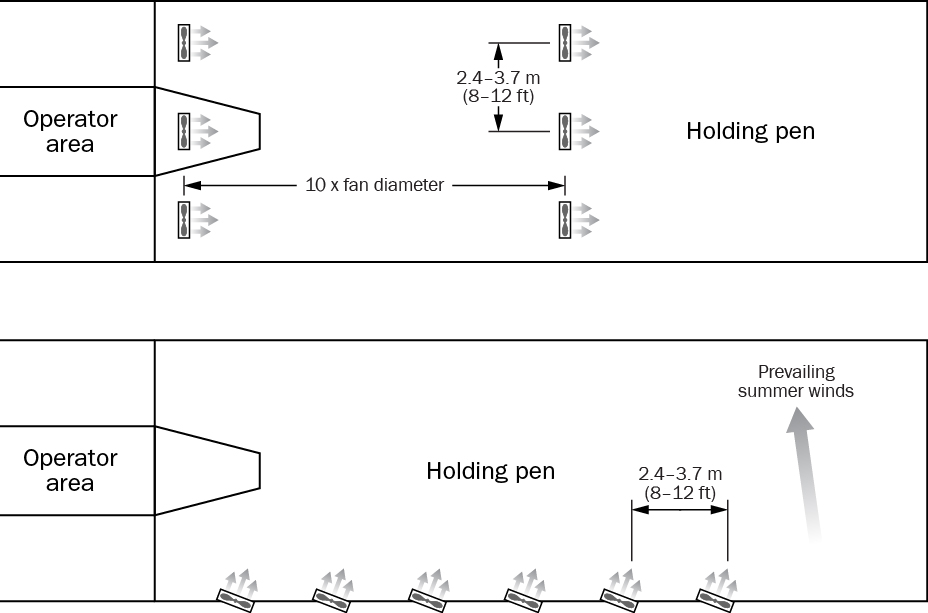
The same arrangement can also be used over the holding area to blow air away from the parlour. Another option is to install a high-volume low-speed (HVLS) fan over the holding area. Sprinklers can be added to provide extra cooling. A more recent innovation is to use positive-pressure ventilation tubes to provide fresh air in the holding area.
Milking parlour
The milking parlour is a more difficult area to ventilate because of the periods of use and non-use. It is also possible to ventilate this area naturally using large windows or roll-up doors that allow for lots of natural light.
Parlour heat
Heating the milking pit is usually not necessary, as the cows supply enough heat to keep the operator warm. It may be necessary to supply heat to keep the equipment from freezing and to keep it dry. Large, insulated curtains or insulated roll-up doors can separate the holding area from the parlour. Hot water floor heating and radiant tube heating are good alternatives as they both supply heat just in the pit area. If necessary, space heaters can keep the whole parlour area warm.
Parlour lighting
The holding and parlour areas can have lighting, similar to the rest of the barn.
The pit requires more lighting for observation at the udder level (recommended 200 Lux). Use separate lights hanging in the middle of the pit or mounted on the equipment panels so they shine on the udder.
The light level should be 500 Lux (50 footcandles) for the proper examination and cleaning of the cows’ udders.
Layouts
There are numerous possibilities for arranging the different components of the milking centre. Design layouts for natural ventilation and light and allow for future expansion.
Linear
Linear arrangements (Figure 7), where the milk tank room, equipment rooms and office area are located at the front of the parlour, allow for unobstructed ventilation to the holding area and parlour. However, parlour expansion is difficult with this arrangement, and natural sunlight is blocked at the front.
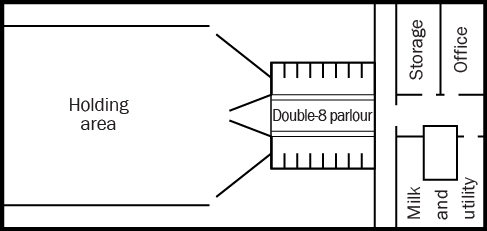
Side
With the milk tank room, equipment rooms and office area located on the side of the holding area and parlour (Figure 8), the parlour end is open for expansion, natural ventilation and light. Ventilation through the parlour area is blocked on one side.
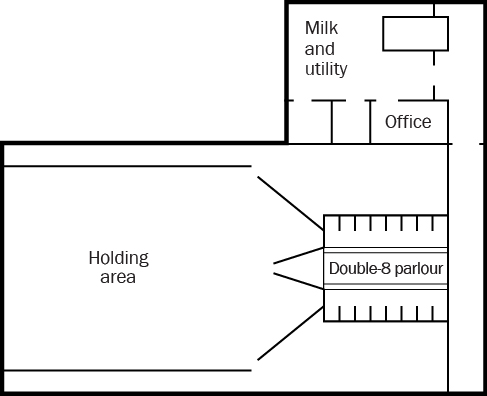
Combination
Many arrangements now locate some of the milk rooms on either side at the front (Figure 9), allowing for natural light and expansion possibilities. Natural ventilation is only partially blocked with this arrangement.
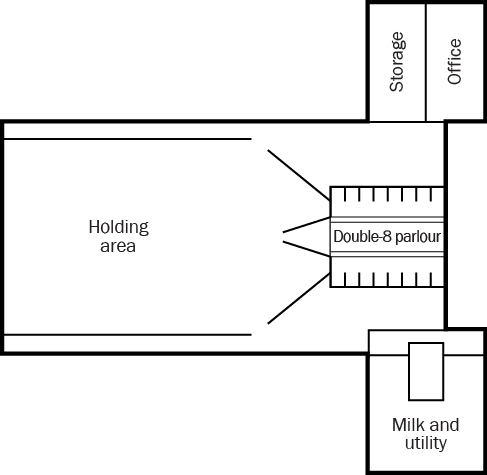
Cleaning and sanitizing floors and equipment
There are several ways of cleaning the holding and the parlour areas. Most producers use a combination of cleaning methods. Wall surfaces should be made of materials that are easily washed and sanitized. Recycle water as much as possible to reduce use and energy used.
Slats
If the barn has a slatted floor, the holding area can be slatted as well. Some producers will slat just the holding area separate from the rest of the barn.
Scrape
Scraping the holding area and parlour with a snow shovel is often the first step in cleaning.
Fire hose
High-volume low-pressure fire hoses are often used to wash the parlour area and holding area (Figure 10).
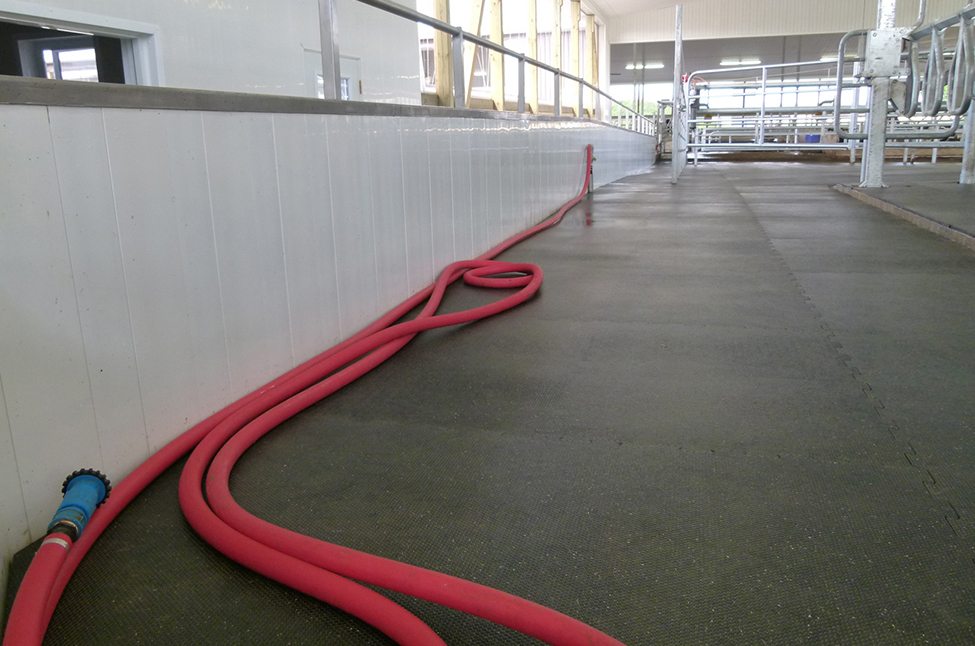
High-pressure sprayer
A high-pressure sprayer uses less water than a fire hose, but it is usually used for small areas because it takes longer.
Flush
Flush systems can be used to wash holding areas.
One method uses a flush tank at the top of the holding area with a valve system that releases a large volume of water to clean.
Another method uses a large outside storage tank that pipes water to valves mounted in the floor at the top end of the holding area.
Both systems require a large volume of “clean” water. The water supply is usually recycled water from the flush system, so some way of separating the solids is also required.
Recycling washwater
Washing milking equipment, parlour and holding area floors uses a significant amount of water.
Milking equipment can be washed using water recycled from the plate cooler. Water from the plate cooler can also be used for floor washing. Milking equipment washwater can also be used on the floors, provided the first rinse is removed. If recycled washwater from the first rinse is used, the milk in the water will make the parlour smell and can result in a bio-film build-up on the floor.
Energy Efficiency
On most dairy farms, about 20% of the electrical use is for milking and about 40% for cooling milk and hot-water heating for washing equipment. Adopt measures to minimize energy use by choosing energy-efficient equipment.
Vacuum pumps
The vacuum pump is a high‑energy user on all dairy farms. Variable frequency drive (VFD) controllers cause the vacuum pump motor to speed up or slow down in response to vacuum fluctuations caused by a unit falling off or other leaks in the line. This drastically reduces energy use. Studies have shown energy savings of 30%–80%, with typical savings around 60% when compared to single-speed vacuum pumps.
Milk pre-cooling
Milk cooling is another process that has potential for energy savings. Heat exchangers allow well water to be used to pre-cool the milk before it enters the bulk tank. By passing well water over a series of plates in a heat exchanger next to the warm milk, the milk can be cooled to 2°C–4°C above the water temperature. This process works best if the well water is less than 10°C. At this water temperature, the milk temperature decreases to a range of about 18°C–23°C, depending on the size of the unit. These calculations are based on a pre-cooling system with a design that uses a 2:1 flow rate that is 2 parts of water for each part of milk.
Milk pumps
Using a VFD milk pump to deliver a steady flow of milk dramatically improves the plate cooler efficiency. A VFD will reduce the energy use by the milk pump by about 50%.
Compressors
The compressor is at the heart of the refrigeration or milk cooling system. A scroll compressor uses about 30% less electricity than conventional reciprocation compressors. The scroll compressor has a simple design with dual spinning scrolls that compress and move refrigerant more efficiently and reliably than traditional compressors.
Water heating
Heating water for equipment washing is also a major energy user on dairy farms. Heat “reclaimers” or refrigeration heat recovery (RHR) systems (Figure 11) make a refrigeration system more efficient by water cooling the refrigerant instead of air cooling it. The heat transfer rate between the refrigerant and water is much higher than from the refrigerant to air. As the water used for cooling heats up, the system must then switch to air cooling.
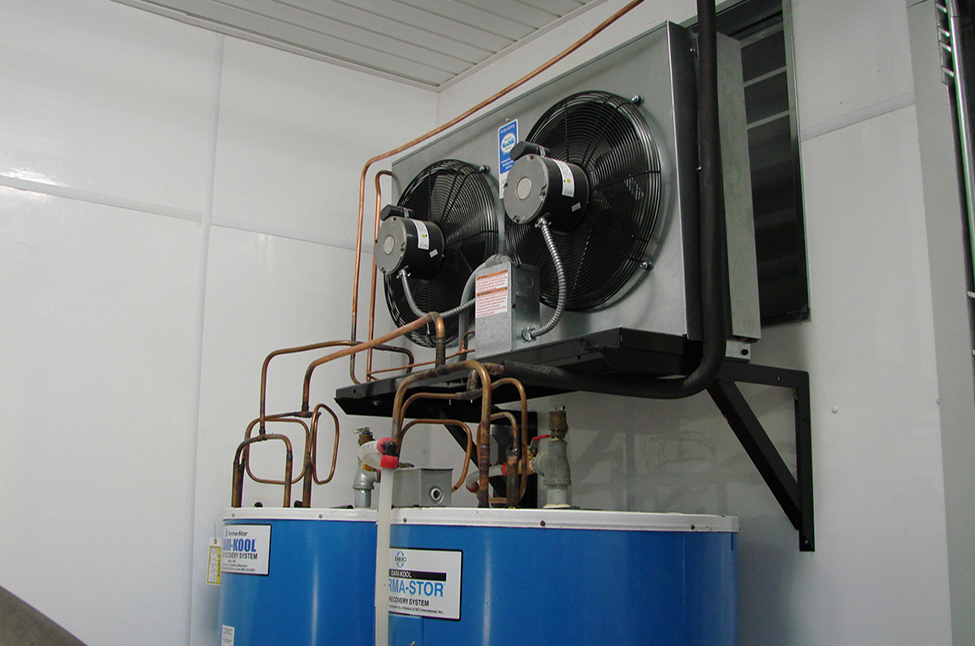
The heat recovered from the refrigeration lines can then be used for equipment washing. An electrical element may be part of the system to heat the water to a higher temperature if necessary. Up to 50% of the energy required for water heating can be recovered from the heat given off by the refrigeration system in this way.
Natural gas is a lower-cost energy source for hot water heating, compared to electricity.
Solar hot water heating
Solar energy is another option for heating hot water.
Co-ordinating plate coolers and refrigeration heat recovery systems
The energy conservation systems for milk cooling are interrelated.
Do not expect all the energy savings to be additive. In fact, unless the components are installed and adjusted to work together, the real energy savings may be disappointing.
For example, if a large plate cooler with a high water-flow rate and a VFD milk transfer pump cools milk very efficiently, the small amount of heat left in the milk may mean the bulk tank compressor does not run long enough to heat sufficient water for cleaning. This makes it necessary to use electricity to produce hot water for cleaning. Reducing the water flow rate through the plate cooler to supply more heat to the heat reclaimer would be more economical in this case.
Technology
More technology is becoming available in the area of precision dairy management. Although you may not be ready to incorporate this into your milking system at present, it is best to plan this into your system for the future.
Stray voltage
Stray voltage is a low-level electric shock that may result from the normal delivery or use of electricity. In dairy barns, both electricity transmission equipment and the farm electric equipment can contribute to levels of stray voltage. Consider eliminating the potential for a stray voltage problem at the design stage. Basic steps such as locating a transformer at a distance from the barn and using proper grounding and grades of wire could help minimize the problem.
Summary
The milking centre is at the heart of any dairy facility. Careful planning is required for efficient cow flow for milking and for operator comfort and efficiency. Milking and related cooling and washing activities use a lot of energy. With careful planning this can be reduced.
Resources
OMAFRA fact sheets:
- Building permit requirements to construct, expand or renovate farm buildings
- Dairy housing: developing the plan and procuring services and materials for constructing a new dairy barn
- Dairy housing: layout options
- Dairy housing: ventilation options for free stall barns
- Lighting options for free stall housing
- Using less energy on dairy farms
Bickert, W.G., et al. 2000. Dairy Freestall Housing and Equipment, 7th edition. MWPS-7. Midwest Plan Service. Iowa State University. Ames, IA.
Bickert, W.G. Milking Center Layout — Designing a Modern Milking Center. Proceedings from the Designing a Modern Milking Center, National Conference Rochester, NY, 1995.
This fact sheet was updated by Rajan Niraula, P. Eng., engineer, dairy and beef housing and equipment, OMAFRA.