Achieve compliance on construction sites: fall prevention
Learn about fall prevention requirements in the construction regulation under the Occupational Health and Safety Act.
Overview
The following information is meant to help employers achieve compliance with the Occupational Health and Safety Act (OHSA) on construction sites.
This resource does not replace the Occupational Health and Safety Act (OHSA) and its regulations and should not be used as or considered legal advice. Health and safety inspectors apply and enforce these laws based on the facts they find in the workplace.
There are many ways for an employer to protect workers against falls on construction projects.
They fall under these categories from most effective to least:
- Elimination: remove the hazard
- Substitution: replace the hazard
- Engineering controls: isolate people from the hazard
- Administrative controls: change the way people work
- Personal protective equipment (PPE): protect the worker with PPE
When elimination or substitution is not possible, physical or engineered controls, such as guardrails, guards, etc., should be used to prevent workers from falling. These controls would also allow workers to move around more freely, while being protected from falling, and do not necessitate planning on what to do should a fall occur.
Installing the physical or engineered controls may require the installers to wear a personal fall protection system. In this case the wearer must be trained by the employer on the fall protection system, in addition to having a valid foundational working at heights training provided by a Working at Heights Training Provider approved by the Chief Prevention Officer (section 26.2 of O. Reg. 213/91 , and sections 6 and 7 of O. Reg. 297/13).
If a guardrail or physical barrier or engineered solution is not possible, the employer must use the highest ranked method of fall protection as per section 26.1(2) of O. Reg. 213/91, the highest being a travel restraint system that meets the requirements of section 26.4, and the lowest, a safety net that meets the requirements of section 26.8.
The employer must also develop fall rescue procedures for rescuing a worker after their fall has been arrested, before any use of a fall arrest system or a safety net by a worker at a project.
The following includes information about possible means to achieve compliance in various situations.
Application of fall protection
This section includes positions related to:
- the meaning of “fall”
- meaning of “falling into operating machinery”
- meaning of “fixed support”
- interpretation of "may be exposed to the hazard of falling”
- working at high angle
- falling into or onto a hazardous substance or object
- falling through an opening on a work surface
- height when there is an opening on a work surface
- interpretation of “practicable”
- fall protection at 2.4 m
- hierarchy of control
- fall protection and excavations
Most of the positions relate to sections 26 and 26.1 of the Construction Projects regulation (O. Reg. 213/91).
Meaning of “fall”
Issue:
What is the meaning of “fall”, how to calculate fall distance, and when to refer to O. Reg. 213/91, s.26 vs OHSA?
Position:
“Falling” in O. Reg. 213/91 section 26 is interpreted to mean the sudden act of rapidly descending in an uncontrolled manner because of gravity from a higher to a lower level. The total distance of a potential (or actual) fall is calculated from the lowest point the worker is occupying (or occupied) to the lowest point the worker could (or did) fall, to be measured as the total difference in vertical/plumb elevation.
For example, the following images illustrate the application of the program decision:
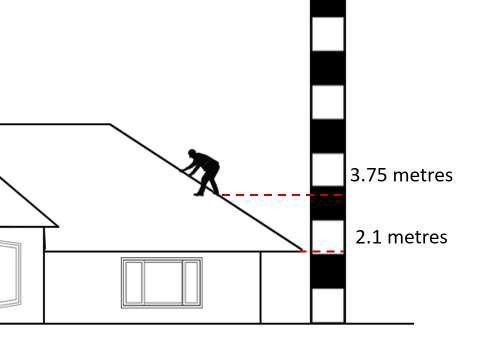
A worker on the roof of a house with a gradual incline at a vertical height of 3.75 metres. The eavestrough is at a height of 2.1 metres. The worker is standing on the inclined roof surface at a vertical distance of 1.65 metres from the eavestrough.
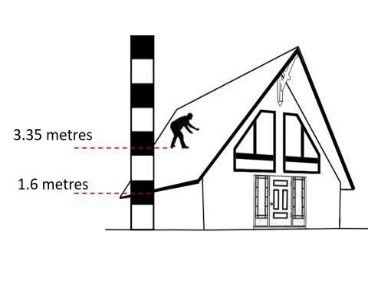
A worker on the roof of a house with a steep incline at a vertical height of 3.35 metres. The eavestrough is at a height of 1.6 metres. The worker is standing on the inclined roof surface at a vertical distance of 1.75 metres from the eavestrough.
The worker is exposed to the hazard of falling 3.75 metres in one instance and 3.35 m in the other.
The program position is that only the vertical fall distance will be considered for the purposes of interpreting and applying the fall protection requirements of sections 26 (O. Reg. 213/ 91) to 26.9. In all other cases where there is doubt about the applicability of the fall protection sections, and a worker may be exposed to the hazard of a high-angle slide or fall, or to a vertical fall not covered by s. 26, clauses 25(2)(a) and 25(2)(h) of the OHSA are applicable and the employer is required to comply with them.
Meaning of “falling into operating machinery”
Issue:
What is meant by “falling into operating machinery” in s.26 paragraph 3 of the regulation?
Position:
Falling into operating machinery means that a worker may be exposed to the hazard of falling from above into machinery that is running. Where a machine is functional but not running or “operating” during the time a worker is in the area, then the worker is not exposed to the risk of falling into operating machinery.
Meaning of “fixed support”
Issue:
Can heavy equipment and devices be considered a “structure” as contemplated in the definition of “fixed support” in s.1(1) of the construction projects regulation?
Position:
“Equipment and devices” are not “structures” and therefore do not fall under the scope of the definition for “fixed support” unless they are securely fastened to a structure or a component of such structure.
Interpretation of “may be exposed to the hazard of falling”
Issue:
How does the Construction Program interpret “may be exposed to the hazard of falling” in sections 26 and 26.3?
Position:
The ministry takes the position that workers on a sloped roof where there is an unguarded fall hazard described in sections 26 and 26.3 of the regulation, or workers on a flat roof within 2 metres of an unguarded fall hazard described in sections 26 and 26.3 of the regulation are exposed to the hazard of falling.
If a worker on a flat roof, through the course of the work, is likely to come within 2 metres of an unguarded fall hazard, then the threshold for “may be exposed” has been crossed.
For further clarification, a flat roof is a roof which is almost level in contrast to the many types of sloped roofs. The slope of a roof is properly known as its pitch and the pitch of a flat roof does not exceed 5° or a slope of 1(vertical) to 12 (horizontal).
Working at high angle
Issue:
How are falls from and exposure to high-angle non-vertical heights (which include the sloped portion of a roof or other surface or structure) regulated?
Position:
Only a vertical fall distance will be considered for the purposes of interpreting and applying the fall protection requirements in sections 26 to 26.9 of O. Reg. 213/91.
In all other cases where there is doubt about the applicability of sections 26 to 29, and a worker may be exposed to the hazard of a high-angle non-vertical slide and fall, or to a vertical fall not covered by those sections, clauses 25(2)(a) and 25(2)(h) of the OHSA apply.
Falling into or onto a hazardous substance or object
Issue:
Is a flat concrete floor or similar surface considered a hazardous substance or object? What is a hazardous substance or object?
Position:
No, a flat concrete floor in a building does not fall within the intent of a “hazardous substance or object”. The intent of this provision is to protect workers from falling into chemicals or such substances that could be in a vat, pit, etc., or on sharp or protruding objects which could penetrate human tissue or organs. A paved surface, a floor, garden soil, or other surface designed for pedestrians would not fall into this category.
Hazardous substances are substances that are toxic, corrosive or otherwise dangerous to life or health, such as acids, alkali, or other chemical or biological substances that could endanger health or safety.
Falling through an opening on a work surface
Issue:
How to interpret “falling through an opening on a work surface”.
Position:
Falling through an opening on a work surface means the worker’s body may fall totally through the opening.
Height when there is an opening on a work surface
Issue:
Does height matter when there are openings on a work surface?
Position:
No. Section 26 does not specify or restrict height for an opening on a work surface. This means that a guardrail or cover is required regardless of the depth of the opening.
If an opening in a work surface is large enough for a worker’s body to fall completely through, the requirement for a guardrail or appropriate covering applies.
Interpretation of “practicable”
Issue:
Is the monetary impact factored into the deliberations of what is considered practicable?
Position:
Cost considerations do not supersede the health and safety of workers. There are instances in the regulation where “guardrails”, “handrail”, or “barrier” are specifically required, regardless of “practicability”. In the prescriptive areas of the regulations, practicability does not apply [namely sections 77 (handrail), 135, 137, 144, 153, 208, 209, and 233 (barrier)].
Fall protection at 2.4 m
Issue:
When installing or removing a guardrail system, or a protective cover, where there is a potential fall hazard of less than 3 metres, must a worker who may be exposed to the hazard of falling less than 3 metres be protected?
Position:
Yes, subsection 26.3 (1) of O. Reg. 213/91 establishes a threshold of 2.4 m in certain circumstances (instead of the 3.0 m outlined under paragraph 1 of section 26). There is no height threshold around openings in a work surface in subsection. 26.3 (2), where fall protection is required.
For the initial installation of a guardrail system or protective cover required by subsections 26.3 (1) and (2), the worker must be protected against falls. Also, the general provisions of clause 25 (2)(h) of the OHSA apply in instances where the worker is exposed to a fall, when such instances not covered by the regulation.
During a temporary removal of a guardrail or protective cover, subsection 26.3 (3) applies.
Hierarchy of controls in fall protection
Issue:
Do inspectors enforce the highest-ranking method of fall protection?
Position:
It is a contravention if a higher-ranking method is practicable as per subsection 26.1(2) and has not been used and an inspector may issue the corresponding order.
Fall protection and excavations
Issue:
There are two sections in O. Reg. 213/91 that apply to excavations and trenches (section 26.1 and subsection 233(4)). If a worker is exposed to a fall hazard greater than 3 metres which one is the most applicable?
Position:
Both sets of requirements are applicable. Due diligence would require the employer to apply the safest requirements in the circumstances.
Anchors and horizontal lifelines
This section includes positions related to:
- parapet clamps and moveable anchors
- whether a concrete block with a suitable anchor is an acceptable anchor point
- engineering requirements for manufactured horizontal lifelines
Most of the positions relate to sections 26.7 and 26.9 of the construction regulation (O. Reg. 213/91).
Parapet clamps and moveable anchors
Issue:
Can moveable anchor systems and parapet clamps be used as an anchor (fixed support) for a fall protection system?
Position:
Moveable anchors and parapet clamps are not “fixed supports” as defined in the construction regulation. However, if the supporting structure (e.g. roof or parapet) has adequate structural integrity and certain other conditions are met (including a site- specific engineer’s report and meeting the requirements of section 3 of O. Reg. 213/91), moveable anchors or parapet clamps may on a case-by-case basis be considered an acceptable fall protection anchor point for fall protection systems as a variation of the requirement for a fixed support.
In order to meet the requirements of section 3, the user of the moveable anchors or parapet clamps (employer, owner or constructor) must be able to prove that the moveable anchor or parapet clamp system in use affords protection for the health and safety of workers using it that is at least equal to the protection provided by a fixed support. Furthermore, the employer, owner, or constructor using the moveable anchor system or parapet clamps must give a written notice of such use to the joint health and safety committee or the health and safety representative on the project.
Concrete block anchor point
Issue:
Would a poured concrete block with a suitable anchor embedded in it be an acceptable anchor point for a fall arrest system? (section 26.7)
Position:
A poured concrete block (with a suitable anchor embedded in it) not attached to a building or structure would not constitute a fixed support.
However, using section 3, there are instances where this could be used as an anchor point. Such an application would need to be engineered, as it would be a variation of a fixed support. The weight of the poured concrete block would depend on:
- the specific application on the project
- where the anchor is located on the block
- the kind of fall protection system to be attached to it
- the configuration of the fall protection system
- the load capacity of the surface the poured concrete block is placed on, etc.
Engineering requirements for manufactured horizontal lifelines
Issue:
Can manufactured horizontal lifelines (HLL) sold by suppliers of fall protection equipment be used on construction projects?
Position:
If the manufactured product complies with all the requirements outlined in subsection 26.9(8) and the engineer of record is authorized by Professional Engineers Ontario (PEO) to practice engineering in Ontario, then the manufactured product may be used as designed.
The system in question should have evidence of its engineering background. This should provide evidence that the engineer of record for the system is authorized by the PEO to practice engineering in Ontario. Systems not manufactured in Ontario or Canada may require separate, standalone engineering documentation in order to comply with subsection 26.9(8).
The anchoring for the manufactured system will always be treated as job specific. In addition to complying with the requirements outlined in section 26.7 for anchors, the user must ensure that they also comply with the requirements of the manufacturer’s instructions for the HLL. These may have more stringent demands on the anchorage, than those outlined in s. 26.7 (e.g. installation requirements exceeding those set out in the Building Code, or requirements to exceed the minimum static forces outlined in subsection 26.7(2) that the system is capable of withstanding). The user must comply with the most stringent requirements.
Additionally, users must be trained on the resulting fall protection system (from anchor point to harness donned by the worker) and given adequate written and oral instructions as per section 26.2, including the inspection of the anchors and system components prior to each use.
CSA standards considerations
This section includes positions related to:
- How to determine whether a component of a fall protection system meets the relevant CSA standard.
- Does the 30” limitation of lanyard length to a dorsal attachment apply to a travel restraint system?
Most of the positions relate to section 26.1 of the construction regulation (O. Reg. 213/91 ).
Determining if a component of a fall protection system meets the CSA standard
Issue:
How does an inspector determine if the components of a fall protection system meet the CSA standard referenced in the regulation? (section 26.1)
Position:
Equipment that meets the applicable CSA standard should have permanent labels, engravings, or stamps on it that reflect the standard to which it has been tested. Inspectors verify the label on the equipment in question.
For components that are not CSA certified or stated to “meet the requirements of the applicable standard”, the inspector may ask for engineering design documents and proof of testing to the appropriate CSA standard.
Application of the 30” limitation of lanyard length to a dorsal attachment to a travel restraint system?
Issue:
Does the 30” limitation of lanyard length to a dorsal attachment apply to a travel restraint system? (section 26.1)
Position:
Standard CSA Z 259.2.5-12 does not apply to components used in a travel restraint system.
Since a travel restraint system eliminates the exposure to a fall hazard, the standard does not apply. System components used in a method of fall arrest however, must meet all applicable requirements of CAN/CSA-Z 259.2.5-12.
If the manufacturer’s instructions specifically limit the length of the lanyard to be used in a travel restraint, then workplace parties must follow those instructions. (section.93(3) of O. Reg. 213/91)
Guardrails considerations
This section includes positions related to:
- the practicability of installing guardrails
- determining compliance of wooden guardrail systems
- stud wall guarding
- roofing platform for fall protection instead of PPE
- bump lines or other warning barriers used during construction
- fall protection requirements for elevators under construction
- guardrails and roofs
- guardrails at the perimeter of a balcony
Most of the positions relate to sections 26.1, 26.3, and 207 to 209 of the construction regulation (O. Reg. 213/91).
Practicability of installing guardrails
Issue:
When is it not practicable to install guardrails?
Position:
“Practicable" and "reasonably possible” are interpreted as having a similar meaning. Considering whether a thing is "practicable" or not requires analysis of all the relevant facts of the case, not only to determine the "possibility" of a thing, but also its "reasonableness" in context.
In relation to worker health and safety, this means that a risk and benefit analysis undertaken in good faith, which examines all relevant factors, is necessary in arriving at a sound conclusion as to a thing’s "practicability".
If it is determined that the installation of guardrails is not practicable as required by O. Reg. 213/91 subsection 26.1(1) then subsection 26.1(2) would apply.
Determining compliance of wooden guardrail systems
Issue:
How to determine if a wooden guardrail system has been constructed and installed as per the requirements of subsection 26.3(7.1).
Position:
If the wooden guardrail system appears to meet spacing and dimensional requirements for the lumber and is in good condition to the point where it can resist all loads that it may be subjected to by a worker, it may be considered in compliance. See subsection 26.3(7) for additional requirements for wooden guardrails beyond those in 26.3(4)-(6).
Stud wall guarding
Issue:
Are stud walls deemed sufficient to substitute for guardrails in providing protection against falls?
Position:
Inspectors will issue an order for guardrails when an unguarded stud wall to which a worker has access is observed and a worker may be exposed to any of the hazards listed in section 26.
Roofing platform for fall protection instead of PPE
Issue:
Can workers on a roof rely on a temporary platform equipped with a guardrail system attached to the structure around the perimeter of the roof instead of using a personal fall protection system?
Position:
When such roofing safety platforms are installed and used per the instructions in the manufacturer’s operating manual workers on the roof may rely on them for fall protection and will not be required to use additional personal fall protection.
The guardrail system requirements in the regulation still apply. Sections 126 and 127 cover only scaffold platforms. This is not a scaffold but this work platform is covered by sections 134 and 135. This is not a suspended work platform as it is not suspended but is attached to the structure.
Any temporary platform equipped with a guardrail system must be installed, maintained, and used in accordance with any operating manuals issued by the manufacturer.
During the installation, repositioning, or removal of any temporary platform equipped with a guardrail system, fall protection requirements apply.
Bump lines or other warning barriers
Issue:
Can “bump lines” (or other warning barriers) be used on a construction project, other than for flat roof repairs and resurfacing? (sections 26 to 26.9, 207)
Position:
Section 207 type barriers (commonly known as “bump lines”) are required in the immediate work area at least two metres from the perimeter of the roof whenever a built-up roof is being constructed, repaired or resurfaced.
Barriers and signs may also be used on a flat roof surface if the workers are not required to be within 2.0 m of the edge.
Barriers and signs are also allowed and encouraged anywhere on a construction project as an additional protective measure to a guardrail system or fall protection system, where applicable (with required signage), but they are not a substitute for guardrails and fall protection systems, where these are required.
Fall protection requirements for elevators under construction
Issue:
Must an elevator under construction meet the requirements of suspended work platform systems or elevating work platforms?
Position:
An elevator is neither a suspended work platform system, nor an elevating work platform in the context of sections 136.1-142.06 and 143-149 of O. Reg. 213/91.
Where any of the hazards listed in section 26 exist to a worker on an elevator car, the fall protection sections (26.1 to 26.9) apply.
Where a guardrail system is installed on the skeleton platform, and the elevator car is in motion, a worker on the platform must make use of a travel restraint system that will adequately prevent ejection from the platform.
Guardrails and roofs
Issue:
Are guardrails needed on all roofs?
Position:
When workers are exposed to a fall hazard greater than 3 m, a guardrail is required if practicable. On flat roofing projects, the installation of guardrails would be expected. However, the practicability of installing a guardrail system on a sloped roof as required by subsection 26.1(1) must be considered.
It depends on the application, exposure to falls, and work being carried out.
For instance, both sections 208 and 209 require the use of a guardrail on a roof around a pipe that supplies hat tar or bitumen or a hoist. The worker must be protected by a guardrail on a flat roof if the worker would be exposed to a fall of more than 3 m, as it is practicable to install a guardrail system.
When it comes to sloped roofs, depending on the slope, configuration, type of work being done, a guardrail may be the most adequate method of fall protection. It could be substituted by personal fall protection equipment – the highest ranked method that is available – when installing the guardrail is not practicable.
Guardrails at the perimeter of a balcony
Issue:
When does a guardrail need to be at the perimeter of a balcony?
Position:
If a worker has access to the balcony perimeter or edge and may be exposed to a fall of 2.4 metres or more, then the worker shall be adequately protected by a guardrail system that meets the requirements of subsections 26.3 (2) to (8). However, despite the requirement for a guardrail system outlined in subsections 26.1(1) and 26.3(1), if it is not practicable to install a guardrail system, a worker shall be adequately protected by the highest ranked method of fall protection listed in subsection 26.1(2) that is practicable. Also, subsection 26.3(3) of the regulation allows the guardrail system to be removed temporarily to perform work in or around the opening if a worker is adequately protected and signs are posted in accordance with subsections 44 (1) and (2).
If a worker does not have access to the balcony perimeter or edge, then the worker is not exposed to a fall hazard and a guardrail is not required. Preventing access to a balcony perimeter could be achieved by either:
- locking the door through controlled key access to the balcony
- installing a physical barrier at the balcony door
In addition to preventing access to the balcony, but not as a substitution, signage indicating that access is prohibited beyond this point unless the worker is protected by using adequate fall protection equipment (as required by section 44).
A snow fence would not be considered an adequate measure to prevent access to the balcony in this situation.
Flying forms or leading-edge work are situations where a guardrail may be useful located further back from the edge and not within 300 mm of the perimeter. In this situation a guardrail may be functioning as a barrier and not to prevent a fall. The highest ranked method of adequate fall protection is needed for workers going beyond the barrier.
If the time required to install a guardrail system, while being protected by a personal fall protection system, equals, or exceeds the time required to do the job, then it may not be practicable to install a guardrail system and may be justifiable for workers to use the personal fall protection system to complete the job.
Personal fall arrest issues
This section includes positions related to:
- travel restraint vs guardrails
- shock absorbing lanyard use to protect against ejection
- travel restraint and proximity to edge
- pole climbing for utility workers
- the use of polypropylene ropes in lifelines
- vertical lifelines splicing
- knots and hitches
- the use of self-retracting devices on a horizontal surface
- requirements for a leading edge self-retracting device
Most of the positions relate to sections 26.3 to 26.6 of the construction regulation (O. Reg. 213/91).
Travel restraint vs guardrails
Issue:
Is it acceptable to have travel restraint in lieu of guardrails when the length of time to install guardrails is the same or longer than it would take to do the work while using a travel restraint system?
Position:
If the time required to install a guardrail (while being protected by a personal fall protection system) equals or exceeds the time required to do the job, then it would be justifiable to use the personal fall protection system to just do the job.
Section 26.1 O. Reg. 213/91 requires the use of a guardrail under the listed conditions. However, section 26.1(2) indicates what methods of fall protection can be used if a guardrail installation is not practicable.
Shock absorbing lanyard use to protect against ejection
Issue:
Can a shock absorbing lanyard be used to protect workers from ejection from a mobile elevating work platform when it is being moved?
Position:
Yes, the ministry will accept the use of a shock absorbing lanyard to secure the worker’s harness or belt to the anchor point on the platform. The lanyard must be short enough to prevent the worker from being ejected from the platform.
A worker in a moving elevating work platform must be using a travel restraint system. The travel restraint system must physically prevent the worker from being able to travel past the guardrail system.
Travel restraint and proximity to edge
Issue:
How close to the edge of a surface can a worker approach for a system to still be considered travel restraint?
Position:
A travel restraint system must restrain the worker from reaching any edge and prevent the possibility of a fall from any edge or opening in the floor. While it is recommended to be at least 2 feet from the edge, if the system is configured to not allow the worker to fall from the edge, it is a travel restraint system.
A travel restraint system needs to be attached to an appropriate fixed support and all components need to be inspected by a competent worker before each use. The CSA standard applies to body belts or saddles used in a travel restraint system.
Pole climbing for utility workers
Issue:
Are utility workers allowed to use pole climbing to access and perform their work?
Position:
Pole climbing is an acceptable method if subsection 26.1(3) and subsection 26.5 (2) are complied with. While an elevated work platform may be preferable, pole climbing is an acceptable method.
The use of polypropylene ropes in lifelines
Issue:
Are polypropylene ropes allowed to be used as lifelines in a fall arrest system?
Position:
Polypropylene lifelines are banned by the CSA Z.259.2.5-12 and therefore not permitted in a fall arrest system.
While polypropylene polymers are allowed, polypropylene lifelines are not. It is to be noted also that the lifeline needs to comply with the provisions outlined by the standard, namely the labelling provisions.
Vertical lifelines splicing
Issue:
Should a vertical lifeline be spliced at any point except at the termination points?
Position:
No. Splicing reduces the strength of the rope.
Knots and hitches
Issue:
Is a triple hitch generally considered an adequate fall arrester?
Position:
No.
The use of self-retracting devices on a horizontal surface
Issue:
Can a self-retracting device (SRD) also known as self-retracting lanyard or self-retracting lifeline (SRL) be used on a horizontal surface?
Position:
Self-retracting devices (or lifelines) may be used on a horizontal surface only if the manufacturer’s operating manual for the SRL or SRD allows such usage. This is considered leading edge work (LE).
The manufacturer’s operating manual for the specific make and model of SRL or SRD must be consulted to determine compliance. Most SRL or SRD devices designed for this type of work will have “LE” or “Leading Edge” language either on the device or in the operating manual. The CSA standard CSZ-Z259.2.2-98 (R2004) also applies.
Requirements for a leading edge self-retracting device
Issue:
What are the requirements for a leading edge self-retracting lanyard (SRL) or self-retracting device (SRD)?
Position:
For an SRL or SRD to be used in a leading-edge application, it must meet the following conditions:
- meet CSA Z259.2.2-98 (R2004) standard
- be classified as leading-edge device
It should also be tested to ANSI Z359.14 or CSA Z 259.2.2-17 requirements.
Meeting the CSA Z259.2.2-98 (R2004) standard is a requirement under subsection 26.1(3) of O. Reg. 213/91 for any SRL used on construction projects.
While there is currently no CSA standard referenced in O. Reg. 213/91 for SRLs used in leading-edge applications, there is an ANSI standard and a CSA standard (Z259.2.2-17) that have been developed to include testing for SRLs classified for leading edge applications.
It is the employer’s and the user’s duty to ensure that the SRL being used in a leading-edge scenario has been designed and tested for leading edge applications (for employer’s duty please refer to clauses 25(2)(a) and 25(2)(h) of the OHSA and subsection 93(3) of O. Reg. 213/91; this latter is also a user’s duty). When the equipment has been designed for a leading-edge application, its manufacturer’s operating manual must contain such information, which must be strictly adhered to.
As with any other fall arrest system, the user must have received adequate training on the system, in addition to adequate oral and written instructions by a competent person. The user must also have a valid Working at Heights (WAH) record of training. Also, before the use of this system or any fall arrest system by a worker, the worker’s employer must have developed written procedures for rescuing the worker after their fall has been arrested.
Fall protection - skylights, roof hatches and other similar types of non-structural coverings on roofs
Issue:
How to provide fall protection when installing skylights, roof hatches and other similar types of non-structural coverings on roofs.
Position:
Unless proven otherwise, skylights (and other similar non-structural covers) are assumed to be structurally inadequate to support the weight of a worker, and therefore must be treated as “openings in a work surface” – a potential fall hazard to workers.
Should a worker be working on or in proximity of a skylight, fall protection requirements apply. Either a guardrail must be in place or the worker must be attached to a fall protection system.
With respect to true “openings” in a roof where the skylight, HVAC unit, etc. is not in place, subsection 26.3 (2) applies: a guardrail system or a protective covering must be in place. The guardrail or protective covering may be removed temporarily to perform work in or around the opening, only if:
- the worker is adequately protected (e.g. by a fall protection system: travel restraint or fall arrest) and
- signs are posted in accordance with subsections 44(1) and 44(2) to warn the other workers of the hazard (subsection 26.3(3)).
Unless the workplace parties can produce engineering documentation to confirm that skylights or other non-structural covers are able to support loads they are likely to be subjected to (e.g. the weight of a worker who may fall or stumble on it), it is advised to proceed under the assumption that they are not adequate to support a worker.
An inspector may require (sub clause 54(1)(m)(ii) of the OHSA) a constructor or employer to provide documentation confirming that the skylight (or other suspect surface) has been designed and is capable of withstanding all loads it is likely to be subjected to (including the weight of a worker or workers). Pending the production of such a report, signed and sealed by an engineer, or from the manufacturer, a requirement under clause 54(1)(i) of the OHSA to not access the area may be issued.
The workplace party to whom the requirements have been issued may opt to comply by providing an adequate cover or guardrail system as outlined in section 26.3 instead of an engineering review.
Training
This section includes positions related to:
- fall protection training accreditation by the MLITSD
- fall protection training records
- online training for fall protection
Most of the positions relate to sections 26.2 of the construction regulation (O. Reg. 213/91) and sections 6, 7 and 10 of O. Reg. 297/13.
Fall protection training accreditation by the Ministry of Labour, Immigration, Training and Skills Development
Issue:
Will the ministry be accrediting agencies to do the fall protection training required by subsection 26.2 (1)?
Position:
No, there is no accreditation for fall protection training. It must be given in oral and written form, by a competent person. The Chief Prevention Officer only approves working at heights training providers and programs.
The adequate written and oral training required to be given to workers who may use a fall protection system is to be given by a competent person. Records of this training are to be provided by employers, upon request by inspectors. These records must include the signature of the competent person who provided the training.
Fall protection training records
Issue:
Who needs to provide the training record (or proof of training) to an inspector?
Position:
It is the employer’s responsibility to provide and keep copies of the fall protection training records for each worker. Subsection 26.2(4) is quite clear: “The employer shall make the training and instruction record for each worker available to an inspector on request”.
As far as working at heights training is concerned, the employer is required to keep a record of training with the information outlined in subsection 10(2) of O. Reg. 297/13 (Occupational Health and Safety Awareness and Training). The training record for the working at heights training must provide the:
- name of the worker
- name of the approved training provider
- date on which the approved training was successfully completed
- name of the approved training program that was successfully completed
Find a list of Chief Prevention Officer approved working at heights training providers.
Online training for fall protection
Issue:
Is online training for fall protection acceptable?
Position:
Online training for fall protection cannot be accepted as complete training. It can be accepted as part of the training.
Section 26.2 of O. Reg. 213/91 requires the employer of a worker who may use a fall protection system to have two specific sets of training. The employer is required to provide proof of training:
- In a Chief Prevention Officer (CPO) approved working at heights program (WAH) in compliance with the CPO approved standard and delivered by a CPO approved training provider: the worker must have a valid WAH training (valid for 3 years from the date of its successful completion, after which a refresher training will be required to confirm its validation).
- On the specific fall protection system in use on the project, provided by a competent person with both oral and written instructions.
While the theoretical portion of the WAH training may be delivered online, this would not cover the entirety of the training. Furthermore, it is the CPO approved training provider that delivers the proof of training. The employer needs to keep a record of such training, along with the date when it was delivered and by which CPO approved training provider.
The training specific to the fall protection system in use at the project must be carried out in person as well. The training referred to in section 26.2 of the regulation are two separate types of training.
Written rescue procedures developed by employer for rescuing a worker whose fall has been arrested
Issue:
What is required in written rescue procedures for fall arrest?
Position:
Most recent information has revealed that the window of opportunity for the successful rescue of a worker is within six minutes of the fall. To be able to implement such a quick response, workers nearby need to be well trained and the equipment necessary for the rescue must be readily available.
The employer of the worker using a fall arrest system or safety net must develop “written procedures for rescuing the worker after their fall has been arrested” (section 26.1(4)). This written procedure should reflect the above information.
Working alone while using a personal fall arrest system
Issue:
Does subsection 26.1 (4) prevent a worker from working alone when using a fall arrest system?
Position:
The written rescue procedures developed by the employer to rescue a worker whose fall has been arrested would outline the equipment used to affect such a rescue and the personnel needed as well. In most instances this would limit the possibility of working alone when using a fall arrest system – unless of course such a system incorporates a self-rescue mechanism (means to reach the next floor surface) and the nature and location of the work would allow the use of such a system.
Reliance on a cell phone is not an acceptable procedure for rescuing a worker whose fall has been arrested by a fall protection system.