Procedure for corrective action for systems not currently using chlorine
This document provides information on how to address adverse microbiological test results from drinking water samples taken from drinking water systems not currently using chlorine.
Introduction
This procedure document describes corrective actions that must be taken when there are adverse microbiological test results from drinking water samples taken from drinking water systems regulated under O. Reg. 170/03, Drinking Water Systems, made under the Safe Drinking Water Act, 2002 that are not currently using chlorine.
Corrective actions for drinking water systems are prescribed by Schedule 18 to O. Reg. 170/03. This procedure is adopted by reference in O. Reg. 170/03 and as such it is a regulatory document and must be used when prescribed. It may also be used as guidance in other scenarios.
Under O. Reg. 170/03, the installation and operation of treatment equipment including filtration and disinfection is required for all surface water systems, unless certain exemptions apply or regulatory relief is granted.
This procedure is intended for systems using groundwater or groundwater under the influence of surface water as a raw water source. It does not apply to surface water systems. It outlines several options for corrective action that owners of drinking water systems can take to ensure microbiological contamination is eliminated.
Adverse water quality incident
For the purpose of this procedure:
As defined in O. Reg. 170/03, “resample and test” means, with respect to corrective action that arises from the test of a water sample for a microbiological parameter,
- take a set of water samples, at approximately the same time, with,
- at least one sample from the same location as the sample that gave rise to the corrective action
- at least one sample from a location that is a significant distance upstream from the location described in (A), if that is reasonably possible, and
- at least one sample from a location that is a significant distance downstream from the location described in (A), if that is reasonably possible, and
- conduct, on the samples taken, the same test(s) that gave rise to the corrective action.
The owner of the drinking water system must ensure that the following corrective action is taken after a microbiological (i.e., Escherichia coli (E. coli), total coliforms, or other bacteria) adverse test result:
Escherichia coli
If the adverse test result is for the presence of E. coli, the drinking water system owner/operator must:
- immediately report the adverse test result to the medical officer of health and the Spills Action Centre of the Ministry of the Environment, Conservation and Parks
- immediately take all reasonable steps to notify all users of water from the system to use an alternate source of drinking water or, if no alternate source is available, to bring water to a rapid rolling boil for at least one minute before use
- resample and test as per paragraph 2 of section 18-5 of Schedule 18 to O. Reg. 170/03 and report any adverse resample test results as required
- immediately take the relevant corrective action steps described in the “Procedure” section of this document, as required by paragraph 5 of section 18-5 of Schedule 18 to O. Reg. 170/03
- after any step of the “Procedure” section below is followed, resample and test until E. coli is not detected in two consecutive sets of samples taken 24 to 48 hours apart
- take any other additional steps as directed by the medical officer of health
For more information on adverse water quality incidents, read the applicable guide for your system type:
Total coliforms and other bacteria
If the adverse test result indicates the presence of total coliforms or any of the bacteria listed in paragraph 2 of subsection 16-3(1), Aeromonas spp., Pseudomonas aeruginosa, Staphylococcus aureus, Clostridium spp. or fecal streptococci (Group D streptococci), in a resample (i.e. the set of samples collected after an initial adverse result), the drinking water system owner/operator must:
- immediately report the adverse test result to the medical officer of health and the Spills Action Centre of the Ministry of the Environment, Conservation and Parks
- follow the steps described in the “Procedure” section of this document
- after any step of the “Procedure” section below is followed, resample and test as soon as reasonably possible until the parameter is not detected in two consecutive sets of microbiological samples taken 24 to 48 hours apart
- take any other steps as are directed by the medical officer of health
For more information on adverse water quality incidents, read the applicable guide for your system type:
Procedure
After the initial corrective action steps have been taken for any of the above adverse test results, the owner should undertake the following steps:
Treatment
Check the system’s treatment equipment to ensure it is working properly and that untreated water is not bypassing the treatment system.
Confirm that regular maintenance is being performed. Regular maintenance can include filter and UV bulb replacement as per the manufacturer’s instructions. The system’s maintenance schedule must be listed in the engineering evaluation report for the system.
Resolve any treatment and maintenance issues before continuing with corrective action steps.
Distribution and source
Conduct an inspection of the distribution piping/plumbing system, wellhead, and surrounding property as described in Appendix A: Source and distribution checks to ensure that the system has been properly constructed and maintained to prevent entry of contaminants. Correct any distribution and source related problems identified before continuing with corrective action steps.
Temporary disinfection (this step only applies to groundwater systems)
Ensure that microbiological contamination is eliminated from the system through temporary disinfection as described in Appendix B: Procedure for temporary disinfection. If temporary system disinfection is successful (meaning microbiological parameters are not detected in two consecutive sets of microbiological samples taken 24 to 48 hours apart and in any additional samples required by the medical officer of health), then the issue is considered resolved and use of the existing groundwater source and treatment equipment can continue.
If adverse microbiological test results cannot be eliminated following temporary system disinfection, refer to Appendix C: Checklist to perform a final review to ensure all recommended steps were taken and then consult a licensed well technician. That consultation should include a site visit and consideration of the following factors:
- potential sources of contamination and source protection
- most effective means of delivering safe drinking water for the long-term
- health protection of the users who are served by the system
- raw water sampling at groundwater systems
Treatment or source modification
If adverse microbiological test results cannot be eliminated through the methods described in this procedure, then the owner of the drinking water system has the following options:
- Installation or addition and operation of treatment equipment in accordance with regulatory requirements, subject to confirmation in an engineering evaluation report prepared for the system by a licensed engineering practitioner.
- Disconnection from any existing source well that is suspected of being associated with the adverse results and connection to a new source well that has been constructed to meet the requirements of Regulation 903, the Wells regulation under the Ontario Water Resources Act. Note: this approach will also require an update to the system’s engineering evaluation report (per Schedule 21 to O. Reg. 170/03).
- Disconnection from all existing source wells and connection to a municipal residential drinking water system that is currently providing primary and secondary disinfection in accordance with sections 1-2 to 1-5 of Schedule 1 to O. Reg. 170/03, subject to approval by the Ministry of the Environment, Conservation and Parks; or
- Disconnection from all existing source wells and connection to a regulated non-municipal drinking water system or municipal non-residential drinking water system that is currently providing primary and secondary disinfection in accordance with sections 2-2 to 2-5 of Schedule 2 to O. Reg. 170/03 and has the operational capacity to handle the additional demand, subject to confirmation in an engineering evaluation report prepared by a licensed engineering practitioner.
Procedure flowcharts for Escherichia coli and total coliforms/other bacteria
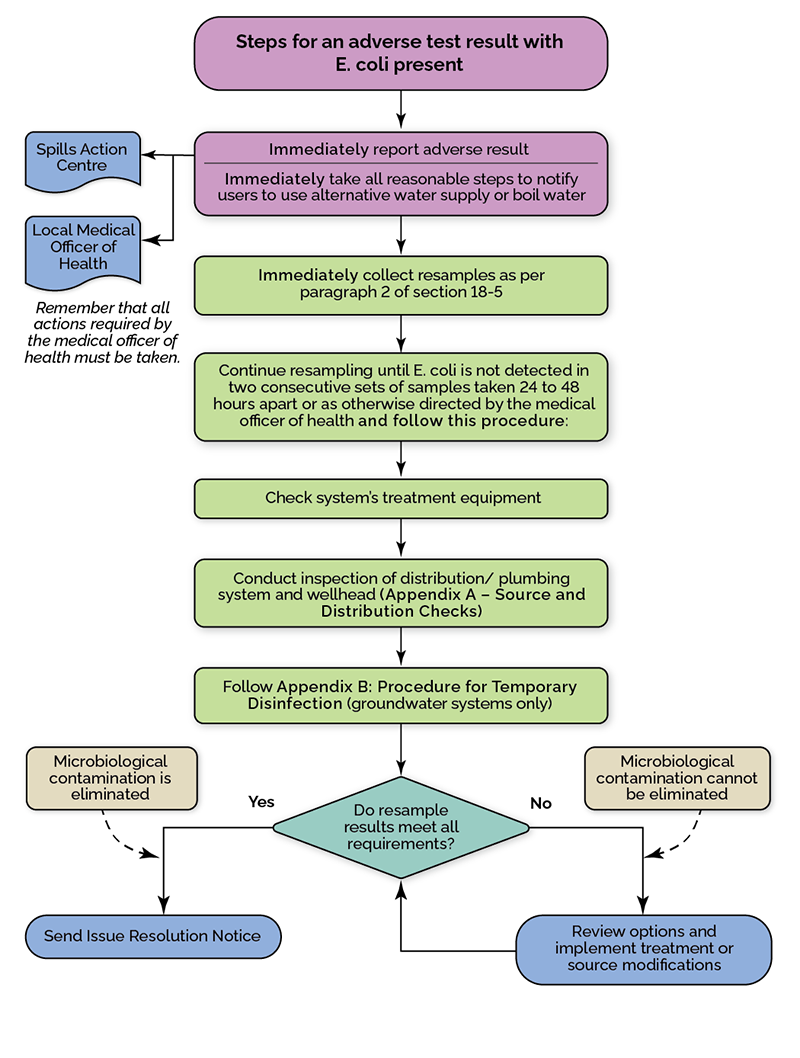
Steps for an adverse test result with E. coli present
- Immediately report adverse result to the local medical officer of health and the Spills Action Centre
- Immediately notify users to use alternative water supply or boil water
- Immediately collect resamples as per paragraph 2 of section 18-5
- Continue resampling until E. coli is not detected in two consecutives sets of samples taken 24 to 48 hours apart or as otherwise directed by the medical officer of health and follow this procedure:
- check system’s treatment equipment
- conduct inspection of distribution/plumbing system and wellhead (Appendix A: Source and distribution checks)
- follow Appendix B: Procedure for temporary disinfection (groundwater systems only)
- If the resample results meet all requirements:
- microbiological contamination is eliminated
- send Issue Resolution Notice
- If the resample results do not meet all requirements:
- microbiological contamination cannot be eliminated
- review options and implement treatment or source modifications
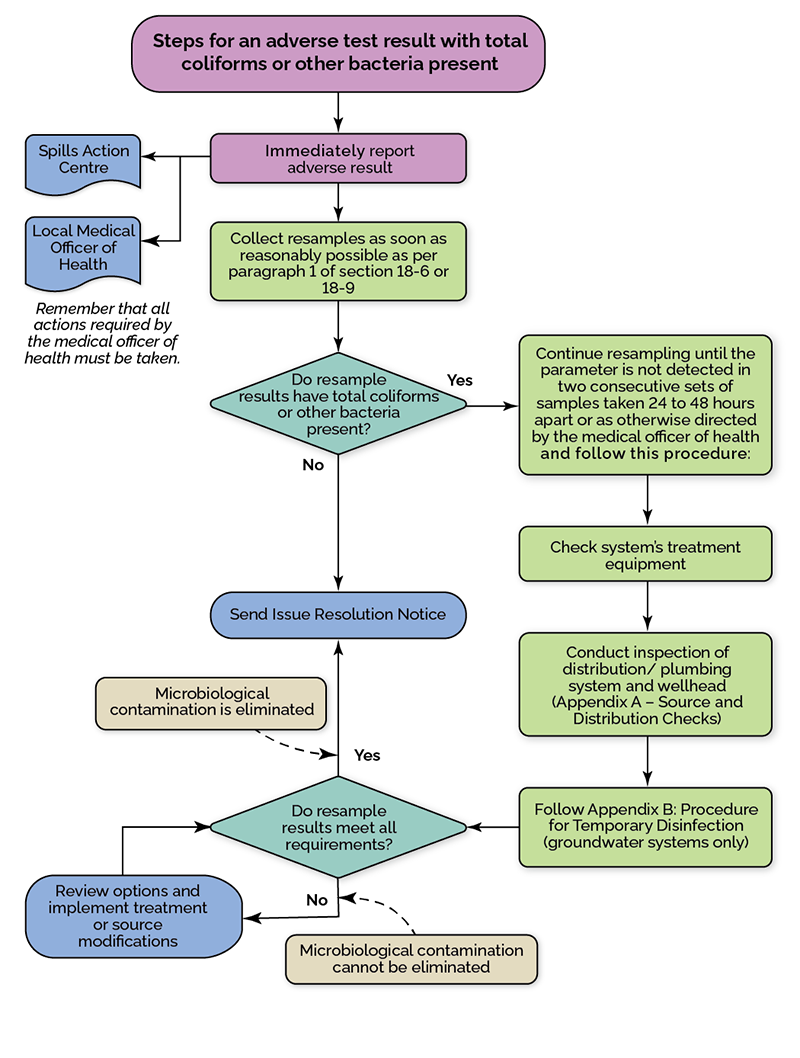
Steps for an adverse test result with total coliforms or other bacteria present
- Immediately report adverse result to the local medical officer of health and the Spills Action Centre
- Collect resamples as soon as reasonably possible as per paragraph 1 of section 18-6 or 18-9
- If the resample results do not have total coliforms or other bacteria present:
- send Issue Resolution Notice
- If the resample results have total coliforms or other bacteria present:
- continue resampling until the parameter is not detected in two consecutives sets of samples taken 24 to 48 hours apart or as otherwise directed by the medical officer of health and follow this procedure:
- check system’s treatment equipment
- conduct inspection of distribution/plumbing system and wellhead (Appendix A: Source and distribution checks)
- follow Appendix B: Procedure for temporary disinfection (groundwater systems only)
- continue resampling until the parameter is not detected in two consecutives sets of samples taken 24 to 48 hours apart or as otherwise directed by the medical officer of health and follow this procedure:
- If the resample results meet all requirements:
- microbiological contamination is eliminated
- send Issue Resolution Notice
- If the resample results do not meet all requirements:
- microbiological contamination cannot be eliminated
- review options and implement treatment or source modifications
Contact the Ministry of the Environment, Conservation and Parks
To report an adverse water quality incident, contact the Spills Action Centre at:
If you have any questions, email drinking.water@ontario.ca.
Appendix A: Source and distribution checks
This list should be used to help determine if there are any issues with the source well for the drinking water system or within the distribution piping and plumbing associated with the system.
Reminder: Please ensure you have considered all potential health and safety hazards and have taken all necessary precautions before you begin any work. Please ensure that any work on the well is performed by someone with the proper qualifications. By law, only licensed well contractors and technicians may construct, alter, or extend a well or install equipment that is in or connected to a well.
Wellhead examination
- Ensure the well is accessible for cleaning, treatment, repair, testing, inspection, and visual examination.
- Inspect the area immediately surrounding the well.
- make sure this area is in a neat and sanitary condition
- look for settling of the ground around the outside of the well casing
- If there is no slope or if some of the area has settled, mound the earth around the outside of the casing so that it is tight, and so that water runs away from the well.
- maintain a permanent buffer of grass or other vegetation extending at least 150 cm from the well casing in all directions
- Check the surrounding area for sources of pollution.
- ensure all potential sources of contaminants, such as animals, fuel, and equipment, are located away from the well
- wells that are not drilled wells with watertight casings extending to a depth of more than 6metres below ground level should be located at least 30 metres from septic systems and other pollution sources
- wells that are drilled wells with watertight casings extending to a depth of more than 6 metres below ground level should be located at least 15 metres from septic systems and other pollution sources
- Inspect well cap for corrosion, cracks, holes and gaps. The well cap must be watertight and in good condition and a deteriorated cap must be replaced.
- Inspect the casing and all joints to ensure they are watertight and in good condition and all holes, cracks and joints are sealed.
- replace deteriorated casing to prevent the entry of surface water and foreign materials into the well
- Consider having a licensed well contractor extend the casing height to at least 40 cm above ground surface if the well casing is less than 40 cm above the ground.
- Check that air vents extend above the ground surface to a height that would prevent the entry of flood water from any anticipated flooding in the area.
- Check the air vent for cracks or holes.
- Check that the well vent is shielded and screened to prevent the entry of insects and other foreign materials into the well.
- Ensure the air vent is always free of obstructions and blockages.
If there are any issues identified with the well, retain a licensed well contractor to inspect and repair the well. A well contractor might:
- remove any debris floating in the well and prevent further debris from entering the well
- check the inside of the casing for stains or cracks
- check the seal around the plumbing inlets
Wells no longer in use or no longer being maintained for future use as a well must be properly Abandoned (plugged and sealed) by a licensed well contractor
- All minimum requirements prescribed by the Wells regulation must be adhered to, including the use of an abandonment barrier that prevents the movement of any water, natural gas, contaminants, or other material between a subsurface formation or between a subsurface formation and the top of the abandonment barrier.
- This abandonment must be done by a licensed well contractor, unless one of the exceptions in section 21(13) of the Wells regulation applies.
- The Ministry of the Environment, Conservation and Parks has resources available on the Wells on your property page, including:
- a link to the Water Supply Wells: Requirements and Best Practices Manual
- a series of technical bulletins that deal with well maintenance, disinfection procedures and well abandonment
Distribution piping and plumbing lines
- Monitor for leaks, corrosion and scaling in pipes, decreases in water pressure, and unexplained increases in water usage as they may lead to contamination.
- look for wet areas, greener vegetation, or melted snow at surface level along distribution lines to locate potential leaks
- Ensure that any leaks, dead-ends, or other mechanical difficulties and equipment failures have been fixed.
- Eliminate any cross-connections using gaps, breakers or other backflow prevention strategies or devices.
If any of these problems are identified, we recommend that you hire a licensed engineering practitioner to help resolve them.
Appendix B: Procedure for temporary disinfection
Temporary disinfection of a drinking water system not using chlorine is required when adverse microbiological test results occur. It is recommended when contamination is suspected (such as after a flood), and at the beginning of each operating season where the well has not been in continuous use throughout the year. Temporary disinfection is carried out by creating a concentration of between 50 mg/L to 200 mg/L free chlorine residual throughout the system from the well to the plumbing and maintaining it over a contact time of 12 to 24 hours. Manual disinfection may be necessary where systems do not have stand-by chlorine disinfection equipment installed.
Have the following functional stand-by chlorination equipment available for temporary system disinfection:
- pump
- solution tank
- a fresh supply of chemical disinfectant
- a means to detect chlorine residual at concentrations up to 200 mg/L
Temporary disinfection is achieved byundertaking the following steps:
- use a fresh supply of chemical disinfectant
- disinfect the system for a period of at least 12 hours to 24 hours such that a free chlorine residual between 50 mg/L to 200 mg/L is maintained at all points in the affected part(s) of the distribution piping and plumbing that is connected to the system
- flush the water lines with water to ensure the chlorine is removed from the system after the 12 to 24-hour period ends
- resample and test 24 to 48 hours after flushing
If necessary, temporary system disinfection can be effectively carried out without stand-by chlorination equipment.
Note: water should not be consumed during this temporary disinfection period due to the high amount of chlorine used. Water can be consumed once the highly chlorinated water has been discharged from the system, but any actions required by the local medical officer of health must still be followed.
Owners of small municipal residential drinking water systems must meet the requirements of their municipal drinking water licence and follow the applicable and current standards when performing disinfection (such as the AWWA (American Water Works Association) Standard for Disinfection of Wells (C654), the Ministry of the Environment, Conservation and Parks’ Watermain Disinfection Procedure). We recommend that the owners of all other types of drinking water systems also follow these procedures/standards. Note: The procedure for corrective action for systems not using chlorine does not apply to large municipal residential systems.
Manual disinfection of a household-sized system
The following summary describes an alternative procedure for the manual disinfection of a household-sized system where all piping is contained within a single building that obtains water from a well.
The manual disinfection of a very small system is most commonly achieved using ordinary household bleach (read "Method for calculating amount of bleach needed" below). Use a new (unexpired) unscented liquid chlorine bleach product containing 5% to 5.25% sodium hypochlorite.
Bleach should be mixed with clean and potable water in a clean container before being placed into the well. When added to the well, the calculated amount of chlorine product should be able to create the desired concentration of free chlorine within the water volume of the well. When adding chlorine to the top of the well, it can be difficult to mix the chlorine throughout the water column because the pump and well screen are often both closer to the bottom of the well. Using a hose to run water back into the top of the well will help mix the chlorinated water down to the pump intake. For more information read the section on Well Disinfection.
Before disinfecting the water distribution piping and plumbing, remove or isolate any carbon filters from the system since carbon will tend to remove the chlorine. In addition, water heaters and storage tanks should be turned off, and completely drained. It is not necessary to drain and disinfect tanks and pipes that are connected to a furnace as part of a water or steam-based heating system.
Once the required amount of bleach has been added to the well, start feeding the chlorine solution through the distribution piping and plumbing. Open all the taps until you can smell chlorine, or use a residual chlorine detection method/instrument (such as pool test strips, colourimeter) to ensure that the chlorinated water is distributed throughout the piping, and then turn the taps off. This will thoroughly chlorinate the plumbing fixtures. If there are any taps on the system where chlorine smell cannot be detected, add more bleach into the well until a chlorine smell is present and then turn the taps off. Allow the high chlorine solution to sit in the system for about 12 to 24 hours. If you have a poor sense of smell, you can also engage someone else to check for the chlorine odour.
After 12 to 24 hours, discharge the water which has been sitting in the water lines. Flush all the taps in the system with new water until the smell of chlorine disappears. None of the water being flushed should be allowed to enter the septic tank or tile field (read the section on Handling heavily chlorinated water discharge). Entry of this water into the septic system may damage or cause the complete failure of the system. Although some chlorine may still be present in the system after flushing is completed, this will not be harmful.
After 24 to 48 hours, resample and test the plumbing for microbiological parameters. This procedure for manual disinfection should be repeated until adverse microbiological test results are no longer received from two consecutive sets of resamples taken 24 to 48 hours apart and from any additional samples required by the medical officer of health. Take such other steps as are directed by the medical officer of health.
Chlorination can effectively disinfect a well and water system. However, unless the source of the problem is found and corrected, the problem will likely continue to recur. In some cases, a new well may have to be constructed to correct the problem.
Method for calculating amount of bleach needed
To calculate the amount of bleach required, use the total depth of the well found on the well record.
The table below is an example of the volume of bleach required for each meter of well depth that is needed for varying well diameters. The volume of bleach is then multiplied by the total depth of the well, to get the final amount of bleach needed to obtain the required chlorine concentration (between 50 to 200 mg/L).
Table 1 is an example of the volume of bleach required to obtain the required chlorine concentration (50 mg/L). Column 1 shows the varying well diameters and Column 2 shows the volume of bleach that is then multiplied by the depth of the well.
To calculate the amount of bleach needed, find the diameter of the well in Column 1. Then find the corresponding volume (mL) in column 2 and multiply that by the depth of the well (which should be found on the well record).
Well diameter (inside diameter of casing) | Volume of 5% bleach needed to disinfect each metre of well depth |
---|---|
5 cm (2") | 2 mL |
10 cm (4") | 8 mL |
12.5 ccm (5") | 12 mL |
15 cm (6") | 18 mL |
17.5 cm (7") | 24 mL |
20 cm (8") | 32 mL |
60 cm (2') | 300 mL |
75 cm (2.5') | 450 mL |
90 cm (3') | 650 mL |
Examples:
A drilled well with 15 cm diameter and 50 m depth:
18 mL (Column 2) x 50 m (depth found on well record) = 900 mL of bleach for manual disinfection
A dug well with diameter of 90 cm and 12 m depth:
650 mL (Column 2) × 12 m (depth found on well record) = 7800 mL or 7.8 L of bleach for manual disinfection
Instead of using Table 1, you can also use the following formula for estimating the approximate volume of household bleach to be added to well water to obtain a dose of 50 mg/L of available chlorine:
V = 0.08 × D2 × H
Where:
D = inside diameter of the well casing in centimetres
H = depth of water in metres
V = volume of bleach that must be added in millilitres
0.08 = constant factor
Knowing the diameter of the inside of the well casing and depth of water in the well, calculate the number of millilitres of bleach to be added to the well water.
Examples:
A drilled well with 15 cm diameter and water depth of 50 m would use 900 mL of bleach for manual disinfection.
(V = 0.08 × 152 × 50 = 900 mL)
A dug well with diameter of 90 cm and water depth of 12 m would use 7.8 L of bleach for manual disinfection.
(V = 0.08 × 902 × 12 = 7776 mL or 7.8 L).
Handling heavily chlorinated water discharge
To handle the discharge of heavily chlorinated water as per the Well Disinfection section in the Water Supply Wells: Requirements and Best Practices, a hose should be used to direct the water to a safe area or location on the property where the chlorinated water will not cause damage or contravene any applicable laws.
Highly chlorinated water should be neutralized (brought to a zero or near zero concentration) using dechlorination chemicals, which can be purchased at many pool supply stores or hardware stores. When using a neutralizer, the chlorinated water should be pumped into a large storage tank first. The neutralizer is to be added to the chlorinated water in the storage tank. Free chlorine test strips (Figure 8-4) should be used to verify that the chlorinated water has been neutralized.
When discharging chlorinated water, avoid:
- pumping strong chlorine solutions onto plants
- running the water into a lake, stream or other body of water
- running the water into any private sewage lines or a septic system, as this may overload the leaching bed or cause the septic system to malfunction by killing the active bacteria in the tank
Care should be taken to ensure that chlorinated well water is not pumped out in quantities, concentrations, or under conditions that may impair the quality of surface water or groundwater or that cause, or may cause, adverse effects, including but not limited to impairment of the natural environment or adverse impacts to neighboring property. Note: chlorinated water is toxic to fish.
For more information, read the Well Disinfection section in the Water Supply Wells: Requirements and Best Practices.
Appendix C: Checklist
Before proceeding to source or treatment modification, this list is a final check to ensure you have taken all the suggested steps. We recommend that you document the date and time each item is completed for future reference.
Treatment
Confirm that:
- there are no open bypasses to the treatment system
- the UV unit(s) auto shut-off mechanism is working properly
- treatment equipment maintenance was performed as required
Source
Confirm that:
- the ground is sloping away from the well in all directions
- the area around the well is neat and free from sources of contamination
- there is a proper setback distance from the well to septic tank(s)
- the well cap is watertight, and all holes, cracks and joints are sealed
- the well vent is screened and that there are no holes/cracks or obstructions/blockages
Note: You may wish to engage a Licensed Well Technician to determine if the well has problems that are not visible on the surface if you haven’t done so. They can also assist you with items listed above if you are unsure how to check them properly.
Distribution piping and plumbing lines
Confirm that:
- there are no leaks, corrosion or scaling in pipes
- there is/was no decrease in water pressure
- any cross-connection problems identified in Appendix A were addressed
Temporary disinfection
Confirm that:
- the correct amount of chlorine was used to conduct temporary disinfection
- all taps were opened and that a chlorine odour was detected at each one
- the high chlorine solution sat for 12-24 hours
Sampling
Confirm that:
- sampling is being conducted and transported (for example, refrigerated) in accordance with the instructions provided by the licensed laboratory
- screens or other attachments are removed from the tap when collecting a sample
- the tap used for sampling is disinfected prior to collecting the sample
- water is flushed from the tap for at least 2-3 minutes prior to sampling